What is IC&BGA Substrate?
BGA Substrate Provider. the Package Substrate will be made with Showa Denko and Ajinomoto High speed materials, BT base and Rogers Base or other types high speed materials and high frequency materials.
BGA (Ball Grid Array) substrate refers to the underlying structure or material that supports the ball grid array package in electronic devices. The ball grid array is a type of surface-mount packaging used for integrated circuits (ICs) and other electronic components. In a BGA package, the connection between the IC and the printed circuit board (PCB) is established through an array of solder balls.
The BGA substrate is a crucial component of this packaging technology. It is a thin, flat piece of material (often a laminate) that serves as the foundation for mounting the IC and provides electrical connections between the IC and the PCB. The substrate typically has a grid of metal traces and vias that connect the IC’s bonding pads to the solder balls on the bottom of the package.
BGA substrates come in various designs and materials, such as organic substrates (e.g., FR-4) or more advanced materials like ceramic. The choice of substrate material depends on factors like electrical performance, thermal characteristics, and cost. BGA packages with advanced substrates are often used in high-performance applications where thermal management and signal integrity are critical.
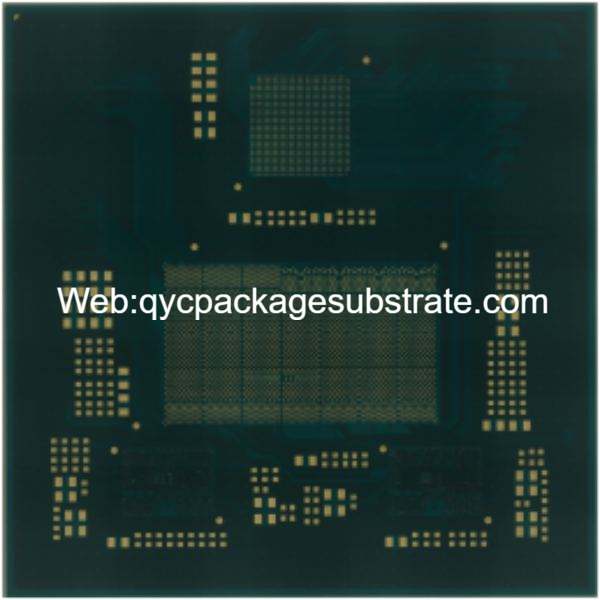
What Roles Do IC/BGA Substrates Play?
BGA substrates play several crucial roles in electronic devices, contributing to their overall functionality and performance. Some of the key roles include:
High-Density Interconnection:
BGA substrates enable the establishment of a high-density electrical interconnection between integrated circuits (ICs) and printed circuit boards (PCBs). Using an array of solder balls positioned on the BGA package’s underside, this technology allows for a compact and dense network of connections, accommodating a multitude of input and output connections within a confined space.
Thermal Management:
BGA substrates are pivotal for effective thermal management in electronic devices, establishing a crucial pathway for dissipating heat from the integrated circuit (IC) to the printed circuit board (PCB). The substrate’s material properties, combined with the configuration of thermal vias and conductive layers, significantly influence the efficiency of heat transfer. The overarching objective is to achieve optimal thermal management, preventing IC overheating and safeguarding overall performance and reliability.
Mechanical Support:
BGA substrates offer mechanical support to the IC. The substrate acts as a platform for mounting and securing the IC in place. This is particularly important in applications where the electronic device may be subjected to mechanical stress or vibration.
Electrical Performance:
The electrical performance of the BGA substrate is critical for signal integrity. The material’s dielectric properties, impedance control, and the design of the signal traces impact the transmission of high-frequency signals. Maintaining good signal integrity is essential for reliable data transfer and overall system performance.
Package Miniaturization:
BGA packages, with the support of the underlying substrate, allow for miniaturization of electronic devices. The compact design and high-density interconnection enable the creation of smaller and more space-efficient packages, contributing to the development of smaller and lighter electronic devices.
Reliability:
BGA substrates contribute to the overall reliability of electronic devices. The selection of materials and the design process for BGA substrates are carefully considered to address challenges such as thermal cycling, mechanical stress, and varying environmental conditions. This meticulous approach aims to guarantee the device’s enduring stability and sustained high performance over an extended period.
In essence, BGA substrates play a pivotal role in electronic devices by enabling high-density interconnection, facilitating effective thermal management, offering mechanical support to chips, and contributing significantly to overall reliability and performance. The careful selection of substrate material and thoughtful design considerations are essential to meet the specific requirements of each application.
How Do Different Types of IC Substrates Differ?
BGA substrates can be categorized based on their structure and application. Two common types of BGA substrates are rigid and flexible, each serving specific purposes in electronic design. Additionally, multilayer BGA substrates offer advantages in terms of performance and complexity.
Rigid BGA Substrates:
Structure: Rigid BGA substrates are typically made of rigid materials such as fiberglass-reinforced epoxy laminates (FR-4) or other rigid substrates. These materials provide a stable and robust platform for mounting the integrated circuit.
Application: Rigid BGA substrates are commonly used in applications where structural integrity and stability are essential. They are suitable for many standard electronic devices and applications.
Flexible BGA Substrates:
Structure: Multilayer BGA substrates find widespread use in high-performance applications, where their inherent advantages play a critical role in ensuring optimal functionality and reliability.
Application: Flexible BGA substrates are used in applications where the electronic device may undergo bending or flexing, such as in wearable devices, flexible displays, or other applications with form factor constraints.
Multilayer BGA Substrates:
Advantages: Multilayer BGA substrates are composed of numerous layers comprising both conductive traces and insulating materials. The incorporation of additional layers in multilayer BGA substrates offers a range of benefits, such as improved signal integrity, minimized electromagnetic interference (EMI), and enhanced thermal management capabilities.
Application:Widely utilized in high-performance applications, multilayer BGA substrates are instrumental in ensuring optimal functionality and reliability. Their inherent advantages make them well-suited for applications featuring complex circuitry, high-speed data transmission, and demanding thermal requirements.
In summary, the key differences lie in the material flexibility and the number of layers within the substrate. Rigid BGA substrates provide stability, flexible substrates offer bendability, and multilayer substrates enhance overall performance in terms of signal integrity and thermal management. The choice of BGA substrate type depends on the specific requirements of the electronic device and its intended application.
How Do IC AND BGA Substrates Differ from PCBs?
BGA substrates and traditional printed circuit boards (PCBs) are related components but serve distinct roles in electronic systems. Here are the similarities and differences between BGA substrates and PCBs:
Similarities:
Both Provide Electrical Connections:
Both BGA substrates and PCBs facilitate electrical connections between different components in electronic devices. They offer pathways for signals to travel between integrated circuits, connectors, and other electronic elements.
Use of Conductive Traces:
Both BGA substrates and PCBs use conductive traces (copper pathways) to transmit electrical signals. These traces are patterned on the substrate or PCB to establish the necessary connections.
Differences:
Role and Function:
A BGA substrate is specialized in establishing a connection interface specifically between the integrated circuit (IC) and the broader electronic system. In contrast, a PCB functions as the primary circuit board within an electronic device, providing a platform for a diverse array of components, such as ICs, resistors, capacitors, and connectors.
Mounting Components:
BGA substrates are specifically designed to mount and support ball grid array packages, while PCBs accommodate a broader range of components, including surface-mount and through-hole components. PCBs are more versatile in terms of component types and configurations.
Size and Form Factor:
BGA substrates are often smaller and more specialized, focusing on the footprint required for a specific BGA-packaged IC. PCBs, especially those in complex electronic devices like motherboards, can be larger and have a variety of form factors to accommodate multiple components.
Relationship with Motherboards:
In electronic devices, especially in the context of computers and other complex systems, BGA substrates are often part of the motherboard. Motherboards host various components, including CPUs and memory modules, which are mounted on BGA substrates. The relationship involves the integration of BGA substrates as specific components within the larger PCB structure of the motherboard.
In summary, while both BGA substrates and PCBs facilitate electrical connections in electronic devices, BGA substrates have a more specialized role in mounting specific types of integrated circuits, particularly those in BGA packages, whereas PCBs serve as the central circuit board hosting a diverse array of components in electronic systems.
What Comprises the Structure and Manufacturing Technologies of BGA Substrates?
The structure and manufacturing technologies of BGA substrates involve several key components and processes. Here’s an overview of the hierarchical structure and key manufacturing technologies:
Hierarchical Structure:
Base Material:
The foundation of a BGA substrate is a base material, commonly a laminate. Common materials include FR-4 (fiberglass-reinforced epoxy) for rigid substrates and polyimide for flexible substrates.
Conductive Layers:
BGA substrates have multiple conductive layers, usually made of copper. These layers form the intricate network of traces that connect the integrated circuit’s bonding pads to the solder balls.
Dielectric Layers:
Dielectric layers separate the conductive layers and provide insulation. The choice of dielectric material influences the electrical properties of the substrate.
Solder Mask:
Solder mask is applied to cover the conductive traces, leaving only the areas where solder joints will be formed exposed. This protective layer prevents unintended soldering and helps insulate the conductive paths.
Surface Finish:
The surface finish is applied to the exposed metal areas to enhance solderability and protect against oxidation. Common surface finishes include gold, tin, and solder.
Solder Balls:
On the bottom side of the BGA substrate, an array of solder balls is attached. These solder balls serve as the connection points between the BGA substrate and the PCB.
Manufacturing Technologies:
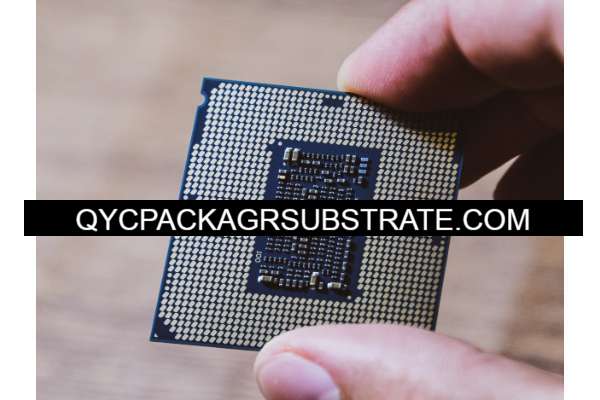
HDI (High-Density Interconnect) Fabrication Technology:
HDI technology allows for the creation of densely packed interconnections on the substrate. It involves using multiple layers of thin copper foils and insulating materials, enabling the design of complex circuits with fine features.
Laser Drilling:
Laser drilling is employed to create small-diameter vias for interconnecting different layers. This precision drilling method enhances the density of connections on the substrate.
Microvia Technology:
Microvias are tiny holes drilled into the substrate to create connections between layers. They contribute to the miniaturization and increased density of the substrate.
Improved Semi-Additive Method:
The semi-additive method involves selectively plating conductive material onto the substrate to create traces. The improved semi-additive method enhances the precision and efficiency of this process, allowing for finer trace features.
Advanced Lamination Techniques:
BGA substrates may undergo advanced lamination techniques to bond multiple layers of material together. This process ensures the structural integrity and reliability of the substrate.
These manufacturing technologies contribute to the production of BGA substrates with high-density interconnections, precise circuit features, and reliable performance. Advances in these techniques play a crucial role in meeting the demands of modern electronic devices for smaller form factors, improved functionality, and enhanced reliability.
What Common Questions Arise Regarding BGA Substrates?
What is a BGA substrate, and how does it differ from a traditional PCB?
Addressing this question helps establish a fundamental understanding of what BGA substrates are and how they play a specific role in electronic devices compared to standard printed circuit boards.
What are the key roles of BGA substrates in electronic devices?
Explaining the various roles of BGA substrates, such as high-density interconnection, thermal management, and mechanical support, provides insight into their importance in electronic systems.
How are BGA substrates manufactured, and what technologies are involved?
Describing the manufacturing processes, including HDI fabrication, laser drilling, and advanced lamination, helps readers grasp the complexity and precision involved in producing BGA substrates.
What types of materials are commonly used in BGA substrates, and how does material choice impact performance?
Understanding the materials used in BGA substrates, such as FR-4, polyimide, or advanced laminates, helps readers appreciate the importance of material selection in achieving specific performance characteristics.
Why are BGA substrates essential for thermal management in electronic devices?
Explaining the thermal management role of BGA substrates helps readers understand the significance of these substrates in preventing ICs from overheating and ensuring device reliability.
What are the differences between rigid and flexible BGA substrates, and when are they used?
Clarifying the distinctions between rigid and flexible BGA substrates and their respective applications provides readers with insights into the versatility of BGA technology.
How do BGA substrates contribute to high-speed data transmission and signal integrity?
Discussing the role of BGA substrates in supporting high-speed data transmission and maintaining signal integrity helps readers connect their importance to the performance of electronic devices.
What Can We Conclude About the Role of BGA Substrates?
In summary, BGA substrates play a critical role in the electronic field by serving as the foundation for integrated circuits (ICs) in modern electronic devices. Their key roles include:
High-Density Interconnection:
BGA substrates enable the creation of a dense network of electrical connections between ICs and printed circuit boards (PCBs), accommodating numerous input and output connections within a limited space.
Thermal Management:
BGA substrates contribute to effective thermal management by providing a pathway for dissipating heat from ICs to the PCB. This is crucial in preventing overheating and ensuring the reliability of electronic devices.
Mechanical Support:
BGA substrates offer mechanical support to ICs, serving as a stable platform for mounting and securing the components. This is particularly important in applications subjected to mechanical stress or vibration.
Electrical Performance:
BGA substrates play a vital role in maintaining good signal integrity and electrical performance. The material characteristics, design, and manufacturing technologies impact the transmission of high-frequency signals.
Miniaturization and Integration:
BGA substrates contribute to the ongoing trend of miniaturization in electronic devices, allowing for smaller and more space-efficient packages.
Looking ahead, future developments in BGA substrate technology are likely to impact electronic devices in several ways:
Advanced Materials and Manufacturing Techniques:
Continued advancements in materials and manufacturing technologies may lead to the development of BGA substrates with enhanced electrical performance, improved thermal characteristics, and increased reliability.
Integration with Emerging Technologies:
BGA substrates may play a crucial role in the integration of emerging technologies, such as 5G, Internet of Things (IoT), and artificial intelligence (AI), by providing the necessary connectivity and support for high-performance components.
Increased Complexity and Functionality:
Future BGA substrates may support increased complexity and functionality in electronic devices, allowing for the integration of more powerful and feature-rich components.
Adaptation to Evolving Device Form Factors:
As electronic devices evolve and adopt new form factors, BGA substrates may need to adapt to support innovative designs and configurations.
In conclusion, the role of BGA substrates in the electronic field is multifaceted, encompassing crucial functions such as interconnection, thermal management, and support for advanced electrical performance. Future developments in BGA substrate technology are poised to contribute to the ongoing evolution of electronic devices by enabling increased performance, miniaturization, and integration with emerging technologies.