What is Cavity package substrate?
We are a professional Cavity package substrate manufacturer, we mainly produce ultra-small bump pitch Cavity substrate, ultra-small trace and spacing cavity packaging substrate and HDI cavity PCBs.
Cavity Package Substrate refers to a specialized form of package substrate used in electronic packaging. What sets it apart is its distinctive structure, which includes cavities or voids within the substrate material. These cavities play a crucial role in enhancing the performance and thermal management of electronic components.
The design of Cavity Package Substrate allows for more efficient heat dissipation, making it particularly valuable in applications where effective thermal control is essential. This technology is often employed in the packaging of integrated circuits (ICs) and other electronic devices, contributing to improved overall system reliability and functionality.
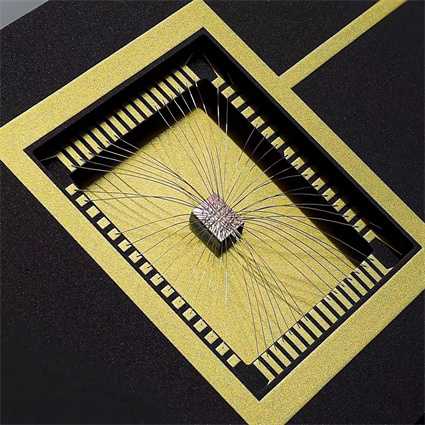
What Defines Cavity Package Substrate?
A cavity package substrate refers to a type of substrate used in semiconductor packaging that incorporates cavities or recessed areas within the substrate itself. These cavities are designed to house specific components or elements of the semiconductor package. The design and incorporation of cavities in the package substrate serve several purposes and set it apart from non-cavity package substrates:
Component Embedding:Cavities within the substrate facilitate the integration of diverse components directly into the packaging. This may encompass the inclusion of integrated circuits (ICs), passive components, and even Micro-Electro-Mechanical Systems (MEMS) devices. Embedding components in the substrate can contribute to a more compact and integrated package design.
Thermal Management: Cavities can be strategically positioned to facilitate enhanced thermal management within the semiconductor package. By incorporating recessed areas, the cavity package substrate allows heat-generating components to be positioned in closer proximity to the substrate. This strategic design enhances thermal conductivity and promotes more efficient heat dissipation. This becomes particularly crucial in high-performance applications where effective thermal management is paramount for ensuring device reliability.
Reduced Form Factor:By integrating cavities, semiconductor packages achieve a more space-efficient design, leading to a decreased form factor. This is particularly valuable in applications with stringent space constraints, such as mobile devices, wearables, and other compact electronic systems.
Improved Electrical Performance: Cavities can be designed to provide specific electrical properties, such as controlled impedance or reduced signal propagation delays. This customization of electrical characteristics can enhance the overall performance of the semiconductor package, especially in high-frequency applications.
Increased Integration and Functionality: The integration of cavities within the substrate facilitates a higher level of integration, accommodating multiple components within the package. This results in enhanced functionality and performance without a substantial increase in the overall package size.
Enhanced Signal Integrity: Cavity package substrates can be designed to improve signal integrity by minimizing signal crosstalk and electromagnetic interference (EMI). The controlled environment provided by the cavities helps in maintaining signal quality and reducing the impact of external influences.
In summary, a cavity package substrate distinguishes itself by incorporating recessed areas or cavities within the substrate, enabling various advantages such as component embedding, improved thermal management, reduced form factor, enhanced electrical performance, increased integration, and improved signal integrity. These features make it a specialized and versatile solution for semiconductor packaging, especially in applications where space, performance, and reliability are critical considerations.
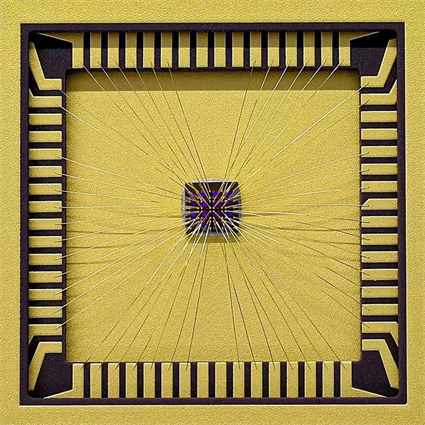
What Functions Does Cavity Package Substrate Serve?
Cavity package substrates serve several functions beyond traditional roles, offering unique advantages, particularly in the areas of heat dissipation and system performance enhancement. Here are some key functions:
Component Embedding: Cavity package substrates allow for the embedding of various components directly into the substrate. This enables a more compact and integrated design, contributing to increased functionality and reduced form factors.
Enhanced Thermal Management: The incorporation of cavities in the substrate facilitates improved thermal management. By strategically placing heat-generating components within these recessed areas, the substrate can efficiently dissipate heat. This is crucial for preventing overheating and maintaining the reliability of electronic devices, especially in high-performance applications.
Reduced Thermal Resistance: Cavities can be designed to minimize thermal resistance, enabling more effective heat transfer from critical components to the substrate. This contributes to a lower overall operating temperature, enhancing the lifespan and performance of semiconductor devices.
Customized Electrical Characteristics: Cavity package substrates can be engineered to provide specific electrical properties, such as controlled impedance and reduced signal propagation delays. This customization enhances the electrical performance of the package, making it well-suited for high-frequency applications.
Space-Efficient Integration: The use of cavities allows for the integration of multiple components within the substrate without significantly increasing the overall size of the package. This space-efficient integration is particularly valuable in applications where size constraints are critical, such as in portable electronics and miniaturized devices.
Improved Signal Integrity: The controlled environment provided by cavities helps in maintaining signal integrity. By minimizing signal crosstalk and electromagnetic interference (EMI), cavity package substrates contribute to improved signal quality, which is vital in high-speed and high-frequency applications.
Facilitates 3D Packaging: Cavities enable a three-dimensional (3D) packaging approach by allowing components to be stacked within the substrate. This enhances the overall system density and performance, especially in applications where space optimization is paramount.
Advanced Packaging Solutions: Cavity package substrates offer advanced packaging solutions, enabling the integration of diverse technologies, such as MEMS devices and sensors. This versatility broadens the range of applications for semiconductor packages.
In summary, beyond traditional functions, cavity package substrates play a crucial role in heat dissipation and system performance enhancement. Their ability to embed components, manage heat effectively, provide customized electrical characteristics, and facilitate space-efficient integration makes them valuable in a variety of advanced electronic applications.
What Types of Cavity Package Substrate Exist?
Various types of cavity package substrates exist, and their differences can be attributed to factors such as package shape, materials used, and targeted application domains. Here are some common types of cavity package substrates:
-
BGA (Ball Grid Array) with Cavity:
-
- Package Shape: BGA cavity packages typically have a ball grid array configuration with a cavity integrated into the substrate.
- Materials: The substrate materials can include organic laminates, ceramics, or even advanced materials like silicon.
- Applications: Commonly used in applications where high integration and efficient heat dissipation are essential, such as in microprocessors and high-performance integrated circuits.
-
LGA (Land Grid Array) with Cavity:
-
- Package Shape: Similar to BGA, LGA cavity packages feature a land grid array design with an embedded cavity.
- Materials: Substrate materials may include organic laminates, ceramics, or other materials suitable for the intended application.
- Applications: Used in applications requiring a flat package profile, such as in some types of memory modules and mobile devices.
-
Cavity Package on Package (C-PoP):
-
- Package Shape: C-PoP configurations involve stacking two or more packages, with at least one of them having a cavity.
- Materials: The materials can vary, and may include organic substrates, ceramics, or a combination of materials for optimized electrical and thermal performance.
- Applications: Commonly used in mobile devices for space-efficient integration of memory and logic components.
-
3D IC (Three-Dimensional Integrated Circuit) with Cavity:
-
- Package Shape: 3D ICs involve stacking multiple layers of integrated circuits with cavities for component embedding.
- Materials: Materials used can include silicon interposers, organic substrates, or other advanced materials suitable for 3D integration.
- Applications: Applied in high-performance computing, data centers, and other applications where compact and efficient integration is crucial.
-
MEMS (Micro-Electro-Mechanical Systems) Cavity Packages:
-
- Package Shape: MEMS cavity packages are designed to accommodate MEMS devices within the substrate.
- Materials: Materials utilized could encompass silicon, glass, or other materials harmonious with MEMS technology.
- Applications: Applied in devices such as sensors, accelerometers, gyroscopes, and other equipment utilizing MEMS (Micro-Electro-Mechanical Systems) technology.
-
Customized Application-Specific Packages:
- Package Shape: Customized packages with unique shapes and cavity configurations based on specific application requirements.
- Materials: Selection of materials is based on the particular electrical, thermal, and mechanical properties needed for the designated application.
- Applications: Designed to specifically cater to the unique demands of specific industries and applications, these configurations are meticulously crafted with an emphasis on fulfilling the distinct requirements of sectors like automotive, aerospace, and medical devices.
To summarize, the diversity of cavity package substrates arises from differences in package shape, materials employed, and targeted applications. Each variant of cavity package substrate is tailored to meet specific requirements, including the attainment of high integration, efficient heat dissipation, and suitability for a wide array of electronic devices and systems. The selection of a specific type hinges on the precise requirements and limitations within the application domain.
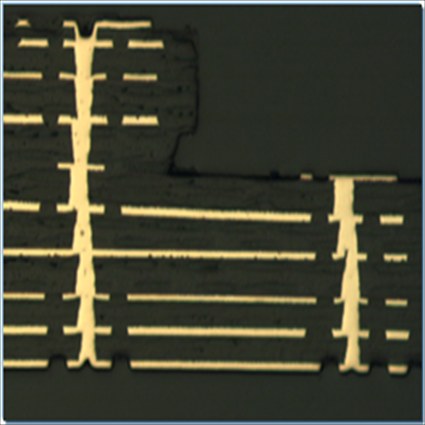
How is Cavity Package Substrate Linked to IC Packaging?
The Cavity Package Substrate is closely linked to IC (Integrated Circuit) packaging, playing a crucial role in enhancing chip density and overall performance. The integration of Cavity Package Substrate brings several improvements to IC packaging:
High Integration of Components: Cavity Package Substrate allows for the embedding of various components directly into the substrate. This enables a high level of integration, as multiple components, such as integrated circuits (ICs) and passive elements, can be housed within the substrate itself. This compact integration contributes to increased chip density.
Space-Efficient Design: By incorporating cavities to house components within the substrate, the overall package size can be significantly reduced. This space-efficient design is particularly valuable in applications where size constraints are critical, such as in mobile devices and other compact electronic systems.
Improved Thermal Management: The strategic placement of cavities allows for more efficient heat dissipation.Placing heat-generating components in close proximity to the substrate enhances thermal conductivity and minimizes thermal resistance. This optimized thermal management is crucial for preserving the reliability of integrated circuits, particularly in demanding high-performance applications.
Enhanced Electrical Performance: Cavity Package Substrate can be designed to provide specific electrical characteristics, such as controlled impedance and reduced signal propagation delays. These enhancements contribute to improved electrical performance, making it suitable for high-frequency applications.
3D Integration Capability: The design flexibility of Cavity Package Substrate facilitates three-dimensional (3D) integration. This allows for stacking multiple layers of components, leading to increased functionality and improved overall performance. 3D integration is particularly beneficial for applications where maximizing functionality in a limited space is crucial.
Customization for Specific Applications: Cavity Package Substrate designs can be tailored to meet the specific requirements of different industries and applications. For example, in automotive, aerospace, and medical devices, where reliability, compactness, and performance are critical, customized Cavity Package Substrate configurations can be developed to address these specific needs.
Reduced Signal Crosstalk and EMI: The controlled environment provided by cavities helps in minimizing signal crosstalk and electromagnetic interference (EMI). This contributes to improved signal integrity, ensuring that electronic signals are transmitted with minimal distortion or interference.
In summary, the integration of Cavity Package Substrate with IC packaging brings about improvements in chip density, space efficiency, thermal management, electrical performance, and overall functionality.These enhancements position Cavity Package Substrate as a valuable solution applicable across a diverse spectrum of industries, ranging from consumer electronics to vital sectors such as automotive, aerospace, and medical devices.
How Does Cavity Package Substrate Compare to Traditional PCBs?
Cavity Package Substrate differs from traditional Printed Circuit Boards (PCBs) in several aspects, offering advantages in terms of space utilization and system optimization. Here’s how Cavity Package Substrate compares and surpasses conventional PCBs:
-
Space Utilization:
- Cavity Package Substrate: The incorporation of cavities allows for the embedding of components within the substrate, leading to a more compact design. This results in superior space utilization, as critical components can be placed closer together without sacrificing performance.
- Traditional PCBs: Traditional PCBs rely on surface-mounted components, limiting the degree of integration and often requiring more surface area. This can result in larger overall system sizes.
-
Integration and Component Embedding:
- Cavity Package Substrate: Cavity designs enable the embedding of various components directly into the substrate, promoting a higher level of integration. This allows for a more streamlined and integrated system architecture.
- Traditional PCBs: Components on traditional PCBs are typically mounted on the surface, limiting the potential for integration and making it challenging to achieve the same level of compactness.
-
Thermal Management:
- Cavity Package Substrate: Cavities can be strategically positioned to enhance thermal management by bringing heat-generating components closer to the substrate. This contributes to better heat dissipation and overall system reliability.
- Traditional PCBs: Traditional PCBs may have limitations in managing heat efficiently, especially in densely packed designs where thermal issues can arise.
-
Customization for Specific Applications:
- Cavity Package Substrate: Cavity designs can be customized to meet the specific requirements of different applications and industries.This adaptability renders it well-suited for diverse applications, particularly those with exacting requirements related to size and performance.
- Traditional PCBs: Although traditional PCBs offer customization options, their degree of adaptability may be constrained when compared to cavity-based substrates. This is particularly evident in the context of accommodating unique form factors and meeting specific requirements of diverse applications.
-
Electrical Performance:
- Cavity Package Substrate: Cavity designs can be optimized for specific electrical characteristics, such as controlled impedance and reduced signal propagation delays. This can lead to improved electrical performance in high-frequency applications.
- Traditional PCBs: While traditional PCBs can achieve high-quality electrical performance, the customization options offered by cavity designs allow for more precise tailoring to application-specific requirements.
-
Signal Integrity and EMI:
- Cavity Package Substrate: The controlled environment provided by cavities helps minimize signal crosstalk and electromagnetic interference (EMI), contributing to improved signal integrity.
- Traditional PCBs: Traditional PCBs may be more susceptible to signal integrity issues and EMI in certain scenarios, especially in high-density designs.
In summary, Cavity Package Substrate surpasses traditional PCBs in terms of space utilization, integration capabilities, thermal management, customization for specific applications, electrical performance, and signal integrity. These advantages make Cavity Package Substrate a compelling choice, particularly in applications where compactness, high performance, and customization are critical considerations.
What Comprises the Structure and Production Technologies of Cavity Package Substrate?
The internal structure of a Cavity Package Substrate is designed to accommodate various components within its cavity while providing efficient interconnections. Several elements contribute to its structure, and advanced production technologies, including High-Density Interconnect (HDI) manufacturing, play a crucial role. Here’s an overview:
Internal Structure of Cavity Package Substrate:
-
Base Substrate Material:
-
- The base material forms the foundation of the substrate. Common materials include organic laminates, ceramics, or advanced materials like silicon, depending on the application requirements.
-
Cavities:
-
- Cavities are recessed areas within the substrate where components can be embedded. These are strategically designed to house specific elements such as integrated circuits (ICs), passive components, or MEMS devices.
-
Component Embedding:
-
- Components, such as ICs or sensors, are directly embedded within the cavities. This contributes to a more compact and integrated design.
-
Conductive Traces and Wiring:
-
- Conductive traces and wiring connect the embedded components, facilitating the flow of electrical signals. These traces are designed to provide the necessary electrical pathways within the substrate.
-
Dielectric Layers:
-
- Dielectric layers insulate conductive traces from each other to prevent short circuits. These layers are essential for maintaining the integrity of the electrical connections.
-
Solder Mask:
- A solder mask is applied to protect the conductive traces and prevent solder bridges during the assembly process. It also helps in identifying different functional areas on the substrate.
Production Technologies, including HDI Manufacturing:
-
High-Density Interconnect (HDI) Technology:
-
- HDI manufacturing is a key production technology for Cavity Package Substrates. It involves advanced techniques to achieve higher wiring density and finer feature sizes. This enables the creation of intricate and compact circuitry within the substrate.
-
Laser Drilling:
-
- Laser drilling is employed to create precise cavities within the substrate. This technology allows for the fabrication of small and intricate features, contributing to the miniaturization of the overall package.
-
Advanced Photolithography:
-
- Photolithography is used to create patterns on the substrate, defining the placement of conductive traces and other features. Advanced photolithography techniques enable the production of fine features with high precision.
-
Microvia Technology:
-
- Microvias are small, laser-drilled holes that connect different layers of the substrate. Microvia technology is essential for achieving high-density interconnections between layers in a compact form.
-
Thin-Film Deposition:
-
- Thin-film deposition techniques are utilized to create conductive and dielectric layers with precise thickness. This ensures the accuracy of the circuitry and insulation within the substrate.
-
Advanced Material Integration:
-
- Depending on the application, advanced materials such as liquid crystal polymers (LCP) or other high-performance substrates may be integrated using advanced manufacturing techniques.
-
3D Printing and Additive Manufacturing:
- For certain applications, precision 3D printing or additive manufacturing technologies may be employed to fabricate intricate structures, including precise cavities, with a high level of accuracy.
By integrating these components and leveraging advanced production technologies, Cavity Package Substrates can be crafted with intricate internal architectures, high-density interconnections, and tailored features to fulfill the specific demands of various applications. The ongoing advancements in manufacturing technologies contribute to further improvements in the performance and versatility of Cavity Package Substrates.
What Questions Arise Frequently about Cavity Package Substrate?
Common questions about Cavity Package Substrate often revolve around its applications, advantages, and specific features. Addressing these queries can provide a clearer understanding of how Cavity Package Substrate is utilized and its benefits. Below are several commonly asked questions (FAQs) about Cavity Package Substrate along with their significance:
What is Cavity Package Substrate, and how does it differ from traditional packaging?
Significance: Provides a fundamental introduction to Cavity Package Substrate, highlighting its distinguishing features compared to conventional packaging methods. Understanding these differences sets the stage for exploring its applications and advantages.
In which industries is Cavity Package Substrate commonly used?
Significance: Helps readers grasp the diverse range of applications, from consumer electronics to critical sectors like automotive, aerospace, and medical devices. Illustrates the versatility of Cavity Package Substrate across various industries.
How does Cavity Package Substrate contribute to thermal management in electronic devices?
Significance: Explains the role of cavities in improving thermal dissipation, a crucial aspect in electronic devices. Understanding this feature helps appreciate how Cavity Package Substrate enhances the reliability of semiconductor components.
What are the key advantages of using Cavity Package Substrate in electronic packaging?
Significance: Provides insights into the specific benefits, such as compact design, high integration, and improved electrical performance. Understanding these advantages highlights why Cavity Package Substrate is preferred in certain applications.
How does Cavity Package Substrate achieve high integration of components?
Significance: Clarifies how the design of cavities allows for the embedding of multiple components within the substrate, leading to increased integration. This knowledge is crucial for understanding the compactness and efficiency of Cavity Package Substrate.
What advanced production technologies are involved in manufacturing Cavity Package Substrate?
Significance: Sheds light on the manufacturing processes, including High-Density Interconnect (HDI) technology, laser drilling, and advanced material integration. Understanding these technologies provides insights into the precision and intricacy of Cavity Package Substrate fabrication.
Can Cavity Package Substrate be customized for specific applications?
Significance: Acknowledges the flexibility of Cavity Package Substrate in meeting the unique requirements of different industries. Understanding its customization capabilities emphasizes its adaptability to diverse application domains.
How does Cavity Package Substrate address challenges related to signal integrity and electromagnetic interference?
Significance: Explores the role of controlled cavities in minimizing signal crosstalk and electromagnetic interference (EMI), contributing to improved signal integrity. Understanding this aspect highlights the reliability of Cavity Package Substrate in high-frequency applications.
Is Cavity Package Substrate suitable for 3D integration?
Significance: Confirms the capability of Cavity Package Substrate in facilitating three-dimensional (3D) integration. Understanding this feature underscores its potential in achieving advanced system architectures and increased functionality.
What are the future trends and advancements in Cavity Package Substrate technology?
Significance: Provides a forward-looking perspective, helping readers anticipate potential developments in Cavity Package Substrate technology. Understanding future trends offers insights into its evolving role in the electronics industry.
Addressing these frequently asked questions contributes to a comprehensive understanding of Cavity Package Substrate, its applications, and the advantages it brings to electronic packaging. It enables readers to make informed decisions regarding its suitability for specific use cases and industries.
What Lies Ahead for Cavity Package Substrate?
In conclusion, Cavity Package Substrate is defined by its ability to accommodate embedded components within recessed cavities, contributing to high integration, improved thermal management, and customization for various applications. As we look ahead, several key features and future trends can be anticipated for Cavity Package Substrate within electronic packaging:
Key Features of Cavity Package Substrate:
-
Component Embedding:
-
- Cavity Package Substrate allows for the embedding of diverse components directly into the substrate, fostering a more compact and integrated design.
-
High Integration:
-
- The design of cavities enables a high level of integration, with multiple components housed within the substrate, contributing to increased chip density.
-
Thermal Management:
-
- Strategic placement of cavities aids in improved thermal management, allowing for efficient heat dissipation and enhancing the overall reliability of electronic devices.
-
Electrical Performance:
- Cavity Package Substrate can be optimized for specific electrical characteristics, such as controlled impedance, contributing to enhanced electrical performance.
Future Trends in Cavity Package Substrate:
Miniaturization and Size Reduction:
- Anticipate continued efforts in miniaturization, with a focus on further reducing the size of electronic packages. Cavity Package Substrate is poised to play a crucial role in achieving compact designs.
-
Enhanced 3D Integration:
-
- The movement towards the integration of three-dimensional (3D) structures is expected to persist. Cavity Package Substrate’s inherent capabilities make it well-suited for advanced 3D packaging architectures, enabling increased functionality.
-
Advanced Materials Integration:
-
- Anticipate progress in incorporating state-of-the-art materials like liquid crystal polymers (LCP) and other high-performance substrates. These advancements are poised to augment the electrical and thermal characteristics of Cavity Package Substrate, pushing the boundaries of its capabilities.
-
Optimized for High-Frequency Applications:
-
- With the increasing demand for high-frequency applications, Cavity Package Substrate is expected to be optimized for such environments, providing superior signal integrity and reduced electromagnetic interference.
-
Innovations in Manufacturing Technologies:
-
- Look for ongoing innovations in manufacturing technologies, including advancements in High-Density Interconnect (HDI) manufacturing, laser drilling techniques, and 3D printing, to further refine the fabrication process.
-
Expanded Application Domains:
-
- Cavity Package Substrate is likely to find new applications in emerging domains, driven by advancements in Internet of Things (IoT), wearable devices, and other innovative electronic systems.
-
Sustainability and Environmental Considerations:
- Future trends may include a focus on sustainability, with efforts to develop eco-friendly materials and manufacturing processes for Cavity Package Substrate, aligning with broader environmental initiatives.
In summary, the future of Cavity Package Substrate holds promise with a continued emphasis on miniaturization, enhanced integration, advanced materials, and optimized performance for evolving electronic applications. As technology evolves, Cavity Package Substrate is expected to play a pivotal role in shaping the landscape of electronic packaging.