FCBGA substrate manufacturer and package substrate manufacturer. We use advanced Msap and Sap technology, High multilayer interconnection substrates from 4 to 18 layers.
The FCBGA (Flip-Chip Ball Grid Array) substrate emerges as a pivotal element in the complex landscape of high-performance integrated circuits and microprocessors. It serves as a linchpin in the semiconductor industry, addressing the continual surge in demand for electronic devices that are not only smaller but also more powerful.
The distinctive feature of FCBGA lies in the “flip-chip” arrangement, where the semiconductor chip takes a topsy-turvy stance during assembly. Unlike the conventional method of showcasing the chip’s front side, flip-chip technology flips the chip, positioning its active side, adorned with solder bumps, toward the substrate. This maneuver brings forth a host of advantages, including reduced signal delays, minimized parasitic capacitance and inductance, and an uptick in thermal efficiency.
At the heart of this technology is the FCBGA substrate, a silent hero that provides a stable foundation for the flipped chip and establishes crucial electrical connections. Adorned with an array of solder balls in a grid pattern on its surface, the substrate forms a Ball Grid Array (BGA), facilitating a robust and effective connection between the chip and the circuit board.
The BGA configuration’s grid layout of solder balls offers a dense arrangement, enabling swift data transmission within a compact form factor. This attribute is especially valuable in applications that demand both high-performance capabilities and a space-efficient design.
A standout feature of FCBGA technology is its prowess in managing heat. The inverted chip configuration fosters direct contact between the chip and the substrate, enhancing thermal conductivity. This proves invaluable in applications where effective heat dissipation is critical for maintaining optimal functionality and safeguarding against thermal-induced damage.
In essence, the FCBGA substrate, alongside flip-chip technology, assumes a pivotal role in the creation of electronic devices that seamlessly blend compactness with high performance. Its contributions span from efficient electrical connections and minimized signal delays to superior thermal management, making it the preferred choice for cutting-edge microprocessors, graphics processing units (GPUs), and other semiconductor devices with stringent performance requirements.
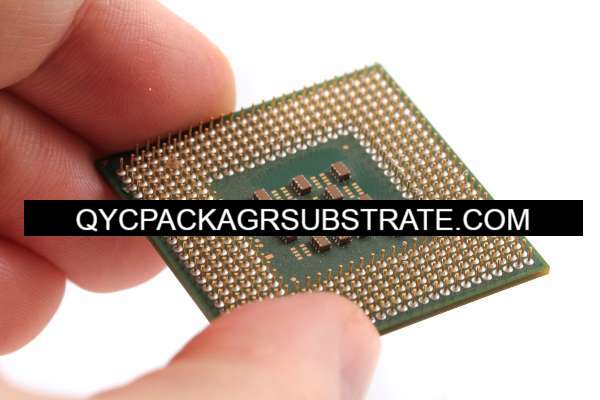
What Functions Does an FCBGA Substrate Serve?
The FCBGA substrate, often overlooked in the intricate world of integrated circuits, emerges as a silent architect of electronic device prowess. Its purpose extends far beyond the mundane task of cradling a chip; rather, it weaves a tapestry of functions crucial to the seamless operation and heightened performance of our electronic companions.
At its heart, the FCBGA substrate acts as a maestro orchestrating the electrical symphony within the chip. A network of conductive traces dances across its surface, facilitating a harmonious exchange of signals between the chip and the broader electronic ensemble. This isn’t a mere dance; it’s a precisely choreographed ballet that ensures signal integrity while adhering to the strictest standards of electromagnetic compatibility.
Yet, this substrate is not content with being just a conductor. It transforms into a stalwart defender, offering the chip a fortress of mechanical support. In a world where electronic devices endure physical stress and unpredictable vibrations, the substrate stands as a guardian, ensuring the chip’s resilience in the face of adversity.
The drama continues with a climactic twist – thermal regulation. Layers within the substrate emerge as unsung heroes, conducting heat away from the chip, thwarting the relentless threat of overheating. It’s a plot twist crucial for the chip’s longevity and reliability, akin to a well-crafted suspense novel where the protagonist escapes the clutches of a fiery demise.
In the grand theater of high-density packaging, the FCBGA substrate takes center stage. Here, it showcases its prowess in squeezing a multitude of connections and features into a confined space. Picture a masterful magician fitting an entire universe into a tiny box – that’s the magic of FCBGA substrates in the realm of compact electronics.
The substrate’s costume change, donning the distinctive Ball Grid Array (BGA) configuration, isn’t just for show. Those solder balls on the substrate’s underbelly aren’t mere embellishments; they simplify the assembly process, ensuring a secure embrace with the printed circuit board (PCB) and adding an extra layer of reliability to the chip’s performance.
In essence, the FCBGA substrate is the unsung hero in the grand narrative of electronic evolution. It’s not just a supporting character; it’s the driving force behind the scenes, crafting a tale of innovation, reliability, and high-performance electronics that captivate the modern technological stage.
What Key Factors Are Considered in FCBGA Substrate Manufacturing?
In the intricate process of crafting FCBGA (Flip-Chip Ball Grid Array) substrates, meticulous attention is given to various critical factors. These encompass material selection, the intricacies of hierarchical structure design, meeting stringent electrical performance requirements, and devising effective strategies for thermal management. Throughout the manufacturing journey, maintaining stringent control over each step remains paramount to ensure adherence to the highest quality standards.
Material Selection:
The decision on substrate materials is pivotal, ranging from organic options like FR-4 to high-temperature laminates and ceramic materials. Factors such as thermal conductivity, dielectric constant, and mechanical properties guide this selection.
Hierarchical Structure Design:
The substrate’s hierarchical structure is carefully planned to accommodate the complex arrangement of flip-chip and solder balls. Layer stacks, signal routing, and power distribution are intricately designed to meet the specific needs of the integrated circuit.
Electrical Performance Requirements:
Striving to meet stringent electrical performance specifications is imperative. The substrate design is fine-tuned to minimize signal distortion, crosstalk, and ensure reliable power delivery. Considerations include impedance matching, signal integrity, and other electrical characteristics.
Thermal Management Strategies:
Given the crucial role of FCBGA substrates in thermal management due to the flip-chip configuration, effective strategies are deployed to dissipate heat. This may involve incorporating thermal vias, metal heatsinks, or other cooling solutions to maintain an optimal operating temperature.
Process Control:
Maintaining precise control over manufacturing processes is non-negotiable to ensure consistency and reliability. Etching, drilling, plating, and other steps are vigilantly monitored, with stringent quality control measures in place to address any deviations.
Alignment and Precision:
Achieving accurate alignment during flip-chip assembly onto the substrate is paramount. Precision is upheld in solder ball attachment, ensuring each connection is established with utmost accuracy. The use of advanced equipment and techniques is fundamental for achieving the required precision.
Adherence to Quality Standards:
FCBGA substrate manufacturing strictly adheres to high-quality standards and industry specifications. This adherence guarantees that the final product aligns with expectations in terms of reliability, durability, and performance.
Testing and Inspection:
Rigorous testing and inspection procedures are enacted to identify and rectify defects or deviations. Checks for electrical continuity, impedance matching, and thermal performance are conducted, with advanced methods like X-ray inspection employed for a comprehensive assessment of solder connections.
In essence, the successful manufacturing of FCBGA substrates requires a comprehensive approach. By navigating through material considerations, hierarchical design intricacies, electrical performance tuning, thermal management strategies, precise processes, adherence to quality standards, and rigorous testing, manufacturers can produce substrates that meet the exacting demands of high-performance electronic devices.
How is FCBGA Substrate Related to FCBGA IC Packaging?
The intricate dance between FCBGA substrates and FCBGA IC packaging is a dynamic partnership, where the design and characteristics of the substrate intimately shape the performance and manufacturing intricacies of the integrated circuit (IC). This collaboration is not just about housing a flip-chip die; it’s a symphony of form meeting function in the realm of advanced chip technology.
Harmonizing Designs: FCBGA IC packaging encapsulates a flip-chip die within a protective layer, and the substrate is its design maestro. The FCBGA substrate must seamlessly align with the unique layout and electrical connectivity needs of the IC package. It’s not just about fitting in; it’s about orchestrating a design that harmonizes with the chip’s demands.
Electrical Choreography: The substrate takes center stage in FCBGA IC packaging as the conductor of electrical signals between the flip-chip die and the external circuitry. The intricacies of FCBGA IC packaging demand a nuanced dance of conductive traces on the substrate, ensuring a flawless performance of signal integrity. Different FCBGA IC packaging classifications bring their own dance styles, and the substrate design must be nimble enough to adapt.
Heat Dissipation Ballet: Thermal management is a key player, and the substrate is the prima ballerina in ensuring a graceful dissipation of heat. FCBGA IC packaging relies on the substrate to elegantly whisk away the thermal challenges posed by the flip-chip die. Different FCBGA IC packaging technologies may demand different thermal pirouettes, influencing the choice of substrate materials and the incorporation of cooling features.
Manufacturing Choreography: The manufacturing steps of FCBGA substrates must be in sync with the chosen dance of FCBGA IC packaging technology. Compatibility is not a choice; it’s a requirement for a seamless integration process. The substrate production must mirror the steps of the packaging technology ballet, ensuring a fluid and efficient performance.
Size and Density Pas de Deux: FCBGA IC packaging often demands a dance of high-density configurations and compact designs. The substrate is not just a supporting partner; it’s an active participant, allowing for the graceful integration of numerous connections in a confined space. The FCBGA substrate’s design sets the stage for the IC package’s size and density capabilities.
In essence, the relationship between FCBGA substrates and FCBGA IC packaging is an artful collaboration. The substrate is not just a backdrop; it’s an integral part of the performance. Its design intricacies, electrical connectivity finesse, thermal prowess, manufacturing compatibility, and support for high-density configurations are the choreography that influences the elegance and efficiency of the entire integrated circuit package. Understanding and perfecting this dance is essential for advancing the capabilities of electronic devices that rely on FCBGA IC technology.
What Sets FCBGA Substrate Apart from Traditional PCBs?
FCBGA (Flip-Chip Ball Grid Array) substrates exhibit distinct features that set them apart from traditional Printed Circuit Boards (PCBs), particularly showcasing advantages in addressing the requirements of high-performance electronic devices. The following highlights key differences and benefits associated with FCBGA substrates:
Innovative Flip-Chip Design:
FCBGA substrates stand out with their flip-chip configuration. Unlike conventional PCBs, where chips are conventionally front-side mounted, FCBGA involves flipping the chip and attaching it with the active side, featuring solder bumps, facing the substrate. This design minimizes signal delays, reducing parasitic capacitance and inductance.
Space-Efficient Form Factor:
Contributing to a more compact form factor, FCBGA substrates allow for higher packaging density. The flip-chip design facilitates the integration of more components within a limited space, proving advantageous for devices with stringent size constraints.
Enhanced Electrical Performance:
FCBGA substrates excel in electrical performance. The shortened interconnect lengths, direct chip-to-substrate contact, and optimized signal paths collectively result in improved signal integrity and reduced electrical losses. This is particularly beneficial for applications requiring high-frequency operation and rapid data transmission.
Effective Thermal Management:
Addressing the critical aspect of thermal management, the flip-chip configuration in FCBGA substrates enables efficient heat dissipation. Direct contact between the chip and substrate facilitates better thermal conductivity, aiding in managing and dissipating heat generated during device operation.
High-Density Interconnections:
FCBGA substrates adopt Ball Grid Array (BGA) configurations with a grid of solder balls, allowing for a higher density of interconnections. This grid layout supports faster data transmission and accommodates more connections in a confined space, making it suitable for applications with elevated pin counts.
Utilization of Advanced Materials and Processes:
FCBGA substrates often leverage advanced materials and manufacturing processes. The careful selection of materials with specific thermal and electrical properties, coupled with precise fabrication techniques, ensures that the substrate meets the exacting requirements of high-performance applications.
Precision in Manufacturing Processes:
Manufacturing FCBGA substrates demands precision in various processes, including flip-chip assembly, solder ball attachment, and substrate fabrication. The accurate alignment and attachment of flip-chips necessitate adherence to rigorous quality control measures to guarantee reliability in the final product.
Application in High-Performance Devices:
FCBGA substrates find extensive application in high-performance electronic devices, such as microprocessors, GPUs, and ASICs. Their ability to deliver superior electrical and thermal performance positions them favorably in applications where speed, compactness, and reliability are paramount.
In summary, FCBGA substrates distinguish themselves from traditional PCBs through their innovative flip-chip design, space-efficient form factor, enhanced electrical performance, effective thermal management, high-density interconnections, utilization of advanced materials and processes, precision in manufacturing, and suitability for high-performance electronic devices. Manufacturers must carefully consider these attributes to meet the evolving demands of modern electronic applications.
What is the Main Structure and Production Technology of FCBGA Substrates?
The intricate structure of FCBGA (Flip-Chip Ball Grid Array) substrates is a marvel of modern chip packaging, comprising multiple layers with specific functions. Typically constructed from a dielectric material like laminate, these substrates house the flip-chip die on the top layer, while the lower layer hosts a grid of solder balls for connection to the PCB. Intermediate layers weave a complex network of traces to facilitate electrical connectivity between the chip and external components.
In the realm of production technology, FCBGA substrates have witnessed significant advancements, notably in high-density interconnect (HDI) manufacturing and semi-additive manufacturing techniques. HDI technology employs laser drilling and sequential lamination to craft intricate circuit patterns in a confined space, addressing the high-density requirements of FCBGA substrates.
Semi-additive manufacturing takes precision to the next level. This process selectively deposits and plates conductive materials on dielectric layers, resulting in finer trace patterns and improved electrical performance. Beyond the technical finesse, the semi-additive approach minimizes material wastage, contributing to a more sustainable and cost-effective production process.
At the forefront of technological evolution, manufacturers are ceaselessly innovating, enhancing production techniques for FCBGA substrates. Their exploration extends to novel materials like ceramics with superior thermal conductivity and metal-coated dielectrics, driven by the escalating need for heightened thermal management in cutting-edge electronic devices. The ongoing pursuit also revolves around refining semi-additive manufacturing processes, placing a keen focus on optimizing deposition and plating methods to elevate precision and reliability to new heights. In essence, manufacturers are unwaveringly committed to pushing the boundaries, ensuring that FCBGA substrates not only meet but exceed the burgeoning demands of high-performance electronics.
The relentless pursuit of innovation highlights manufacturers’ dedication to not merely keeping up with but also spearheading the fulfillment of the ever-evolving needs in contemporary electronics through FCBGA substrates. In navigating the delicate equilibrium between miniaturization, high performance, and thermal efficiency, FCBGA substrates emerge as a testament to the dynamic and ever-evolving landscape of chip packaging technology. They are not just components; they embody the industry’s commitment to staying ahead of the curve and driving the next wave of advancements in electronic packaging.
What are Common Issues in FCBGA Substrate Manufacturing?
How Does Flip-Chip Assembly Impact Manufacturing?
Flip-chip assembly requires precise alignment and attachment of the chip with its active side facing the substrate. Challenges include achieving accurate alignment and solder ball attachment, demanding advanced equipment and techniques.
What Role Does Thermal Management Play in FCBGA Substrate Manufacturing?
Thermal management is critical due to the flipped-chip configuration. Efficient strategies, such as incorporating thermal vias and heatsinks, are employed to dissipate heat generated during device operation and maintain optimal operating temperatures.
What Quality Control Measures Are Implemented in FCBGA Substrate Manufacturing?
Rigorous quality control measures include testing for electrical continuity, impedance matching, and thermal performance. Advanced methods like X-ray inspection may be used to ensure the integrity of solder connections.
How Does FCBGA Substrate Manufacturing Address High-Density Interconnections?
FCBGA substrates employ Ball Grid Array (BGA) configurations with a grid of solder balls, enabling a higher density of interconnections. Challenges include ensuring precise placement and attachment of numerous solder balls in a limited space.
What are the Critical Stages in FCBGA Substrate Manufacturing?
Key stages include meticulous material selection, hierarchical structure design, precise flip-chip assembly, solder ball attachment, and various fabrication processes like etching and plating. Stringent control throughout these steps is imperative to meet rigorous quality standards.
What are the Conclusions Drawn?
In summary, the article highlights the crucial role of FCBGA (Flip-Chip Ball Grid Array) substrates in influencing the performance and reliability of electronic devices. These substrates, distinguished by their intricate design and the ongoing innovation in manufacturing technology, emerge as pivotal elements in advanced chip packaging. They serve as a foundational component, contributing significantly to the enhancement of electronic device capabilities.They facilitate improved electrical connectivity, provide essential mechanical support, and contribute to efficient thermal management.
The importance of FCBGA substrates becomes apparent as they skillfully address the requirements of high-density packaging, providing a streamlined solution that doesn’t sacrifice performance. Their crucial role in facilitating uninterrupted signal transmission and averting overheating highlights their essential contribution to the longevity and dependability of integrated circuits.
The unwavering dedication of manufacturers to innovation, emphasized in the article, highlights the dynamic evolution of FCBGA (Flip-Chip Ball Grid Array) substrate manufacturing technology. This commitment is evident in their exploration of novel materials, such as ceramics with improved thermal conductivity. Additionally, the continuous refinement of semi-additive manufacturing processes exemplifies a forward-thinking strategy aimed at meeting the ever-evolving demands of contemporary electronics. This proactive approach positions manufacturers at the forefront of technological advancements, ensuring that FCBGA substrates remain at the cutting edge of electronic packaging solutions.
Looking ahead, the future of FCBGA substrate manufacturing technology holds promising prospects. Potential developments may encompass further strides in materials science, leading to the discovery of even more efficient thermal management solutions. Additionally, the continuous optimization of manufacturing processes, driven by technological breakthroughs, may yield substrates that not only meet but exceed the escalating demands for miniaturization, high performance, and thermal efficiency in electronic devices.
In summary, FCBGA substrates are central to advancing electronic device capabilities, and the persistent innovation in their manufacturing technology signifies a commitment to spearheading technological progress. The dynamic nature of FCBGA substrates ensures their ongoing integral role in the future of chip packaging, contributing to the evolution of high-performance and reliable electronic devices.