What is Flip-Chip Package Substrate?
Flip-Chip Package Substrate manufacturer. the Package Substrate will be made with Showa Denko and Ajinomoto High speed materials. Or other types high speed materials and high frequency materials.
Flip-chip packaging is an advanced packaging technology used in integrated circuits (ICs) to achieve a more compact and high-performance design. In a flip-chip package, the IC chip is “flipped” upside down and mounted directly onto the substrate or circuit board. The electrical connections are made through tiny solder bumps on the active side of the chip, which are then joined to corresponding pads on the substrate.
This is in contrast to traditional packaging methods where the IC is mounted upright and wire bonds are used for the connections. Flip-chip packaging offers several advantages, including:
Shorter Signal Paths: Flip-chip reduces the distance that signals need to travel, leading to shorter interconnect lengths and improved electrical performance.
Improved Thermal Performance: Because the heat-generating components of the IC are closer to the substrate, heat dissipation is often more efficient.
Higher I/O Density: The flip-chip design allows for a higher density of input/output (I/O) connections, making it suitable for high-pin-count applications.
Reduced Inductance: Flip-chip packaging generally has lower inductance compared to wire-bonded packages, contributing to better high-frequency performance.
Compact Size: Flip-chip packaging can result in smaller form factors, enabling more compact and lightweight electronic devices.
However, flip-chip packaging also comes with its own set of challenges, such as increased complexity in the manufacturing process and potential reliability issues. Despite these challenges, it is widely used in various applications, particularly in high-performance computing, mobile devices, and other electronics where space and performance are critical considerations.
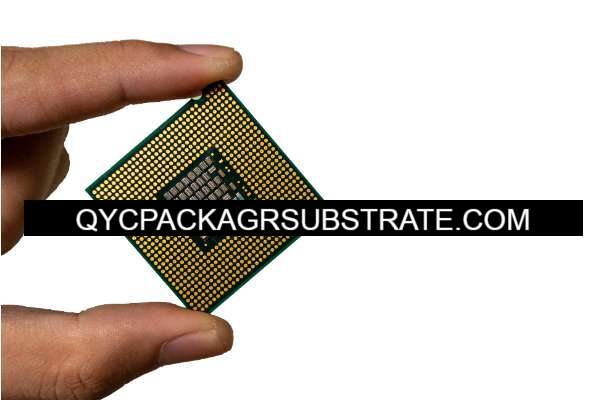
What are the Functions of Flip-Chip Package Substrate?
Flip-Chip Package Substrate (FCPS) serves multiple functions in both electrical and mechanical aspects, making it a crucial component in electronic devices. Some of its key functions include:
Electrical Interconnection: FCPS plays a crucial role in establishing electrical connections between the integrated circuit (IC) chip and the substrate or circuit board. These connections are formed by solder bumps on the chip, creating contact with corresponding pads on the substrate. This process facilitates the transmission of signals between the chip and the broader electronic system.
High I/O Density: FCPS enables a dense arrangement of input/output (I/O) connections, facilitating the transmission of a significant number of signals between the chip and the substrate.This is particularly advantageous in applications that require a high pin count and complex functionalities.
Improved Electrical Performance: The short interconnect lengths in FCPS contribute to improved electrical performance by reducing signal propagation delays and minimizing parasitic effects such as inductance. This is crucial for high-speed and high-frequency applications.
Thermal Management: FCPS plays a role in enhancing thermal conduction between the chip and the substrate. The inverted configuration facilitates more efficient dissipation of heat generated by the integrated circuit (IC), thereby enhancing thermal management. This is particularly crucial in high-performance applications where effective heat dissipation plays a pivotal role in ensuring reliability and optimal performance.
Mechanical Support and Protection:
The FCPS offers structural reinforcement to the chip and aids in shielding it from potential physical harm. The substrate acts as a stable platform for the flipped chip, ensuring proper alignment and structural integrity.
Size Reduction: The compact design of FCPS contributes to size reduction in electronic devices, making it suitable for applications where space is a limiting factor.
Reliability: FCPS is designed to offer highly reliable electrical connections, and the flip-chip configuration can reduce the risk of wire bond-related failures. This makes FCPS suitable for a wide range of complex applications, including those with stringent reliability requirements.
In summary, the Flip-Chip Package Substrate serves a crucial role in providing reliable electrical connections, supporting thermal management, and offering mechanical stability in electronic devices. These functions make it well-suited for various complex applications, especially those demanding high performance and miniaturization.
How Does Flip-Chip Package Substrate Differ from Traditional PCBs?
let’s compare Flip-Chip Package Substrate (FCPS) with traditional printed circuit boards (PCBs), printed wiring boards (PWBs), and modern motherboards to highlight their differences:
- Mounting Orientation:
-
- FCPS: Utilizes a flip-chip design where the IC chip is inverted and mounted upside down on the substrate.
- PCBs and PWBs: Typically involve mounting components upright, and wire bonds or solder joints connect them to the board.
- Modern Motherboards: May incorporate a mix of mounting methods depending on the specific components used.
- Interconnection Method:
-
- FCPS: Achieves electrical connections through solder bumps on the flipped chip, allowing for a high density of I/O connections.
- PCBs and PWBs: Utilize traces, vias, and solder joints for electrical connections, with wire bonding for semiconductor devices.
- Modern Motherboards: Can combine various interconnection methods, including through-hole and surface-mount technologies.
- Signal Path Length:
-
- FCPS: Features shorter signal paths due to the direct chip-to-substrate connection, contributing to improved electrical performance.
- PCBs and PWBs: Signal paths may be longer, especially in wire-bonded configurations, potentially leading to increased signal propagation delays.
- Modern Motherboards: Employ advanced design techniques to optimize signal paths for performance.
- Thermal Performance:
-
- FCPS: Enhances thermal conduction between the chip and substrate, aiding in efficient heat dissipation.
- PCBs and PWBs: Heat dissipation depends on the material properties and design; additional heat sinks or cooling solutions may be used.
- Modern Motherboards: Incorporate various thermal management solutions, including heat sinks, fans, and heat pipes.
- I/O Density:
-
- FCPS: Offers a high I/O density, making it suitable for applications with a large number of input/output connections.
- PCBs and PWBs: I/O density can vary, with limitations on the number of connections depending on the technology and design.
- Modern Motherboards: Strive for a balance between I/O density and component placement to meet diverse connectivity needs.
- Complexity and Size:
- FCPS: Can contribute to compact designs due to the flip-chip configuration, potentially reducing the overall size of electronic devices.
- PCBs and PWBs: Size and complexity depend on the specific application and requirements.
- Modern Motherboards: Integrate various components, connectors, and features, resulting in complex and often multi-layered designs.
In summary, Flip-Chip Package Substrate differs from traditional PCBs and PWBs in terms of mounting orientation, interconnection method, signal path length, thermal performance, I/O density, and overall complexity. While FCPS offers advantages in specific applications, the choice between these technologies depends on the specific needs of the electronic system being designed. Modern motherboards, as comprehensive electronic platforms, may incorporate a mix of these technologies to achieve optimal performance and functionality.
What is the Structure and Manufacturing Technology of Flip-Chip Package Substrate?
The structure of a Flip-Chip Package Substrate (FCPS) typically involves several key components:
- Substrate Material:
- The substrate serves as the foundation and support for the entire package.
- Common substrate materials include organic laminates, ceramics, or other advanced materials with suitable electrical and thermal properties.
- Solder Bumps:
- The active side of the IC chip features small solder bumps, often made of a lead-free solder alloy.
- These bumps facilitate electrical connections between the chip and the substrate.
- Dielectric Layers:
- Dielectric layers are used to insulate and separate different conductive layers on the substrate.
- These layers are crucial for preventing electrical interference and ensuring the reliability of the package.
- Metal Layers and Traces:
- Multiple metal layers are present on the substrate, forming a complex network of traces.
- These metal layers provide the necessary pathways for electrical signals to travel between the chip and other components.
- Through-Silicon Vias (TSVs):
- In some advanced FCPS designs, through-silicon vias may be incorporated, allowing vertical connections through the thickness of the chip.
- TSVs contribute to improved electrical performance and signal integrity.
Manufacturing Technology of Flip-Chip Package Substrate:
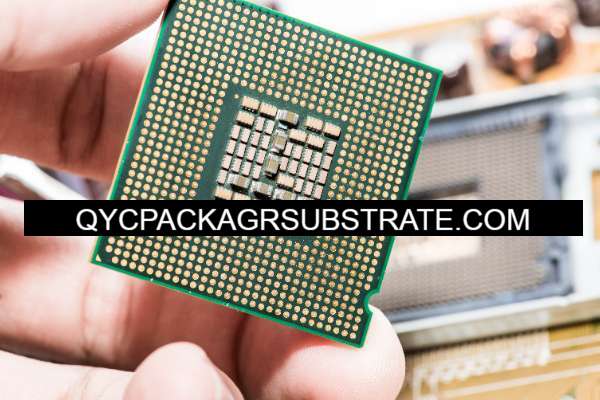
The manufacturing process of FCPS involves several steps:
- Substrate Fabrication:
-
- The substrate is manufactured using traditional printed circuit board (PCB) processes or other advanced techniques.
- Layers of dielectric material and metal traces are deposited and patterned on the substrate.
- Bump Formation:
-
- Solder bumps are deposited onto the active side of the IC chip using various methods, such as electroplating or solder paste printing.
- The bumps are precisely placed in a specific pattern to match the layout on the substrate.
- Flip-Chip Bonding:
-
- The flipped IC chip is aligned and bonded to the substrate, with the solder bumps making contact with corresponding pads on the substrate.
- The bonding process may involve controlled heating to reflow the solder and create secure electrical connections.
- Dielectric and Metal Layer Build-Up:
-
- Additional dielectric layers and metal traces are deposited on top of the substrate and interconnected to create a multilayer structure.
- These layers form the intricate wiring needed for high-density interconnectivity.
- TSV Implementation (Optional):
-
- If through-silicon vias (TSVs) are part of the design, they are created to establish vertical connections within the chip.
- Final Assembly:
- The completed FCPS undergoes final assembly, which may include additional processes such as underfilling, encapsulation, and testing.
Technological Focus and Emerging Techniques:
- High-Density Interconnect Technology:
-
- FCPS places a significant emphasis on achieving high-density interconnectivity to accommodate the increasing number of I/Os in modern semiconductor devices.
- Semi-Additive Methods:
-
- Semi-additive manufacturing techniques, where metal layers are selectively added, enable finer features and greater design flexibility in FCPS.
- Advanced Materials:
-
- The use of advanced substrate materials with enhanced thermal and electrical properties is crucial for improving the overall performance of FCPS.
- 3D Integration and TSVs:
- Incorporating through-silicon vias and exploring 3D integration techniques contribute to overcoming space limitations and enhancing electrical performance.
In summary, Flip-Chip Package Substrate involves a sophisticated structure with a focus on high-density interconnectivity. The manufacturing process incorporates traditional PCB methods, advanced materials, and emerging techniques such as semi-additive methods and 3D integration to meet the demands of modern semiconductor packaging.
What Are the Emerging Trends in Flip-Chip Package Substrate?
As of my last knowledge update in January 2022, I can provide insights into potential emerging trends in Flip-Chip Package Substrate (FCPS). Keep in mind that developments in technology may have occurred since then. Here are some trends that were gaining attention:
- Advanced Materials:
- Continued exploration and adoption of advanced substrate materials with enhanced thermal and electrical properties to further improve the overall performance of FCPS.
- Heterogeneous Integration:
- Integration of different technologies, functions, and materials on a single chip or package, allowing for more versatile and efficient systems. This includes integrating different types of components, such as sensors, logic, and memory.
- 3D Integration:
- Continued exploration and development of three-dimensional integration techniques, including Through-Silicon Vias (TSVs), to overcome space limitations and enhance overall performance.
- Advanced Packaging Technologies:
- Integration with other advanced packaging technologies, such as fan-out wafer-level packaging (FOWLP) and system-in-package (SiP), to create more compact and efficient electronic systems.
- Semi-Additive Manufacturing:
- Increased adoption of semi-additive manufacturing methods for creating finer features and achieving greater design flexibility in FCPS.
- Improved Thermal Management:
- Ongoing efforts to enhance thermal management capabilities, possibly through the integration of advanced cooling solutions, heat dissipation materials, or innovative designs to address the challenges of increased power densities.
- 5G and High-Frequency Applications:
- Tailoring FCPS designs to meet the specific requirements of high-frequency applications, especially in the context of 5G infrastructure and communication systems.
- AI Hardware Acceleration:
- Design optimization to support hardware acceleration for artificial intelligence and machine learning applications, taking advantage of the unique characteristics of FCPS for improved performance.
- Sustainability and Green Packaging:
- Consideration of environmentally friendly materials and manufacturing processes to align with the industry’s increasing focus on sustainability and green packaging practices.
Understanding these trends can indeed provide readers with insights into the potential future development of FCPS. It’s important to stay updated with the latest advancements and research in the field to grasp the evolving landscape of flip-chip packaging technology. Always refer to the latest sources for the most current information on technological trends and developments.
FAQs
Let’s address some frequently asked questions (FAQs) about Flip-Chip Package Substrate:
How does FCPS contribute to miniaturization in electronic devices?
FCPS achieves miniaturization by inverting the chip and directly mounting it onto the substrate. This configuration reduces the footprint of the package, allowing for more compact designs. The shorter interconnect lengths in FCPS also contribute to space savings in electronic devices.
What advantages does FCPS offer in terms of electrical performance?
FCPS provides shorter signal paths, reducing signal propagation delays and minimizing parasitic effects like inductance. This leads to improved electrical performance, making FCPS suitable for high-speed and high-frequency applications where signal integrity is crucial.
Is FCPS suitable for high-power applications?
FCPS can be adapted for high-power applications, but thermal management becomes a critical consideration. The design should incorporate effective heat dissipation methods, and materials with good thermal conductivity may be utilized to address the challenges associated with increased power densities.
How does FCPS contribute to improved reliability in electronic devices?
FCPS can enhance reliability by providing more secure electrical connections compared to traditional wire bonding. The flip-chip configuration reduces the risk of wire bond-related failures. Additionally, FCPS offers better thermal management, contributing to the overall reliability of electronic systems.
What is the outlook for FCPS in the semiconductor packaging industry?
The outlook for FCPS is positive, with continued growth expected in the semiconductor packaging industry. As electronic devices demand higher performance, compact designs, and efficient thermal management, FCPS is likely to play a crucial role in meeting these requirements. Ongoing advancements in materials and manufacturing technologies further contribute to its positive industry prospects.
Are there any challenges associated with FCPS implementation?
While FCPS offers numerous advantages, challenges include the complexity of the manufacturing process, potential reliability issues related to solder joints, and the need for careful thermal management. Addressing these challenges requires ongoing research and development efforts within the semiconductor packaging industry.
Conclusion
In the ever-evolving landscape of electronic packaging, Flip-Chip Package Substrate (FCPS) stands out as a transformative technology, playing a pivotal role in driving innovation and advancing the capabilities of electronic devices.Introducing a unique design that flips the conventional placement of chips onto the substrate, FCPS has sparked a revolutionary transformation in the fields of miniaturization, high-density interconnectivity, and thermal management. It has become a vital element, meeting the demands of modern applications ranging from high-performance computing to cutting-edge technologies like Artificial Intelligence (AI), 5G, and the Internet of Things (IoT).
The importance of FCPS is highlighted through its role in facilitating compact designs, improving electrical performance, and establishing dependable connections. These aspects are critical in the evolution of advanced electronic systems for the next generation. Its ability to address the challenges posed by increasing power densities and high-frequency applications makes FCPS a cornerstone in the technological advancements shaping the electronic industry.
As we navigate this technological journey, it is imperative for industry professionals, researchers, and technology enthusiasts to closely follow the developments in the field of Flip-Chip Package Substrate. The ongoing exploration of cutting-edge materials, innovative manufacturing techniques, and diverse applications is positioned to uncover fresh opportunities and expand the horizons of what electronic devices can accomplish.
In summary, Flip-Chip Package Substrate (FCPS) transcends its role as a mere component in electronic packaging; it serves as a catalyst for innovation, a crucial facilitator of advancement, and a propelling force steering the evolution of electronic technologies. As we embrace the future of electronics, staying informed and engaged with the ongoing advancements in FCPS will undoubtedly enrich our understanding of its profound impact on the electronic landscape. Let us embark on this technological journey together, exploring the essence of Flip-Chip Package Substrate and witnessing the transformative potential it holds for the future.