What is Package Substrate?
Package Substrate Producer. High speed and high frequency material packaging substrate manufacturing. Advanced production process with Msap and Sap technology.
Package Substrate is a crucial element in the realm of electronic materials, especially in the context of Integrated Circuit (IC) packaging. It serves as the fundamental layer that supports and connects various components within an IC package. The choice and design of this substrate material are paramount, as they significantly influence the overall performance, reliability, and thermal characteristics of electronic devices.
The substrate acts as a platform for mounting and interconnecting the semiconductor die, which is the heart of the IC, with the external environment. It provides electrical connections, thermal management, and mechanical support for the integrated circuit. Common substrate materials include ceramics, organic laminates, and metal-core materials, each offering different properties and advantages based on the specific requirements of the application.
The design of the package substrate involves considerations such as electrical connectivity, thermal dissipation, signal integrity, and mechanical stability. Advances in package substrate technology contribute to the miniaturization, increased performance, and enhanced reliability of electronic devices. As electronic devices continue to evolve and demand higher performance, the role of package substrate remains crucial in enabling these advancements in the field of semiconductor packaging.
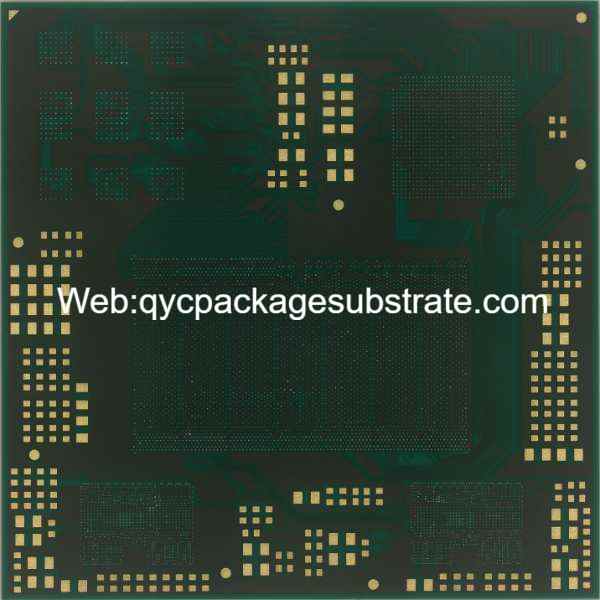
What Functions Does FCBGA Substrate Serve?
Absolutely, FCBGA Substrate plays a pivotal role in electronic devices by serving multiple key functions. Let’s delve into these functions:
Electrical Connections:
FCBGA Substrate excels in providing essential electrical connections within electronic devices. Through its advanced design, it ensures efficient and reliable connectivity between the integrated circuits, enabling seamless communication and data transfer.
Heat Dissipation Support:
One crucial function of FCBGA Substrate is its capability to support heat dissipation. Electronic components generate heat during operation, and FCBGA Substrate is engineered to efficiently transfer and dissipate this heat, preventing overheating and ensuring optimal performance and longevity of the device.
Accommodating More Connection Points:
FCBGA Substrate stands out for its ability to accommodate a higher number of connection points in a smaller space. This feature is particularly valuable in modern electronic devices where miniaturization is a key trend. By efficiently utilizing space, FCBGA Substrate contributes to the compact design of devices without compromising on functionality.
Compact and Efficient Devices:
By providing a platform for effective electrical connections, supporting heat dissipation, and maximizing connection points in a confined space, FCBGA Substrate significantly contributes to making electronic devices more compact and efficient. This is especially crucial in applications where space constraints and energy efficiency are paramount considerations.
In summary, the functions of FCBGA Substrate go beyond mere connectivity. Its role in facilitating heat dissipation and optimizing space utilization contributes to the overall efficiency and performance of electronic devices, making it a key player in modern electronic design.
How Many Types of Package Substrate Exist?
The world of Package Substrate encompasses various types, each tailored to meet specific requirements and applications. Let’s explore the diversity of Package Substrate types:
Diverse Variants:
Yes, there are indeed multiple types of Package Substrate. These variants are designed to cater to a range of applications and specifications, offering flexibility and versatility in electronic design.
Distinct Characteristics:
Each type of Package Substrate comes with its own set of distinct characteristics. These features are carefully crafted to address specific needs within the electronics industry. Examples of characteristics include varying thermal conductivity, signal integrity, and impedance control.
Suitability for Various Applications:
The various FCBGA Substrate types are highly versatile and find suitability across a broad spectrum of applications. Whether applied in high-performance computing, telecommunications, or other electronic devices, these substrates can be tailored to meet the specific requirements of diverse industries.
Different Materials and Manufacturing Processes:
Variability in materials and manufacturing processes is a key factor in the differentiation of FCBGA Substrate types. Some substrates may utilize advanced materials to enhance heat dissipation, while others may focus on optimizing signal transmission. The manufacturing processes can vary to accommodate specific design requirements.
Addressing High Frequency and High Density:
Certainly, certain types of FCBGA Substrate are specifically engineered to address the demands of high-frequency applications. Additionally, high-density variants are designed to accommodate a large number of connections in a confined space. This adaptability makes FCBGA Substrate a suitable choice for applications requiring both high frequency and high density.
In conclusion, the existence of multiple types of FCBGA Substrate demonstrates the adaptability and versatility of this advanced packaging technology. The variations in characteristics, materials, and manufacturing processes allow designers to choose the most suitable substrate for their specific electronic design needs.
Is FCBGA Substrate Different from IC Packaging?
FCBGA Substrate differs from IC packaging, and understanding this difference involves exploring their relationship, particularly in the context of chip packaging technology classifications. Let’s delve into this to comprehend the position of FCBGA Substrate within the integrated circuit ecosystem.
FCBGA Substrate vs. IC Packaging:
FCBGA Substrate:
Nature: FCBGA Substrate is a specific type of packaging technology that involves a Flip-Chip arrangement with a Ball Grid Array (BGA) for external connections.
Chip Orientation: In FCBGA Substrate, the chip is flipped to the bottom, allowing for more compact and efficient connectivity.
IC Packaging:
Diversity: IC packaging is a broader term encompassing various techniques to encapsulate integrated circuits for protection and connectivity.
Types: IC packaging includes a range of methods such as Dual In-line Package (DIP), Quad Flat Package (QFP), and many others, each with its characteristics.
Exploring their Relationship:
Classification of Chip Packaging Technology:
IC packaging includes diverse technologies, each classified based on how the chip is mounted and connected.
FCBGA Substrate falls under the category of Flip-Chip packaging, emphasizing its distinctive chip orientation.
Connection Methods:
In FCBGA Substrate, the external connections are achieved through a Ball Grid Array (BGA), offering advantages in terms of density and reliability.
Other IC packaging methods may use different connection approaches, such as through-hole connections in DIP or surface-mount connections in QFP.
Position of FCBGA Substrate:
Within the Integrated Circuit Ecosystem:
FCBGA Substrate holds a significant position within the integrated circuit ecosystem, especially in applications where its specific advantages, like compact design and enhanced connectivity, are crucial.
Advantages and Applications:
FCBGA Substrate is particularly advantageous in scenarios where space efficiency, high-density connections, and efficient heat dissipation are paramount.
Its application is prominent in modern electronics, contributing to the development of smaller, more powerful devices.
In conclusion, while FCBGA Substrate is a specific type of chip packaging technology, IC packaging encompasses a broader range of methods. Understanding their relationship and the distinct advantages of FCBGA Substrate positions it as a valuable and specialized component within the integrated circuit ecosystem.
How Does FCBGA Substrate Differ from Conventional PCBs?
let’s explore how FCBGA Substrate differs from conventional PCBs and highlight its unique features, especially in comparison to aspects like Motherboard, Substrate-like PCB (SLP), and HDI Substrate.
FCBGA Substrate vs. Conventional PCBs:
Unique Features of FCBGA Substrate:
FCBGA Substrate is a specialized packaging technology designed for Flip-Chip arrangements with a Ball Grid Array (BGA) for external connections.
Its unique feature lies in the flipped orientation of the chip, allowing for more efficient and compact connectivity.
Differences in Connectivity:
FCBGA Substrate excels in high-density connectivity due to its BGA connections, providing a large number of connection points in a confined space.
Conventional PCBs may use different connection methods, such as through-hole vias, which may limit their density.
Comparing Aspects with Other PCB Technologies:
Motherboard:
FCBGA Substrate may be integrated into a motherboard design for specific applications, offering advantages in terms of space efficiency and enhanced connectivity.
Traditional motherboards often utilize a combination of various packaging technologies based on the requirements of different components.
Substrate-like PCB (SLP):
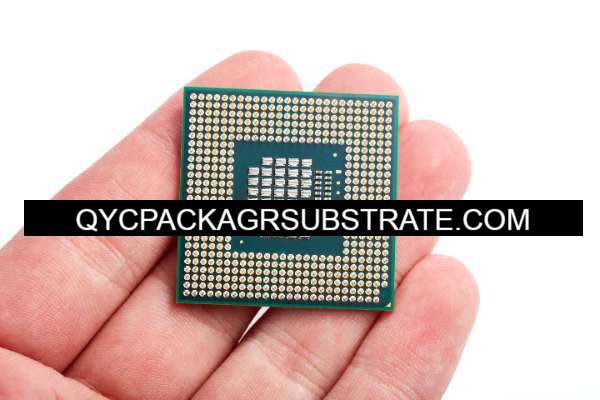
SLP is a type of PCB that mimics the characteristics of a semiconductor substrate. FCBGA Substrate, while sharing some similarities, specifically emphasizes the Flip-Chip arrangement and BGA connections for unique advantages.
HDI Substrate:
HDI (High-Density Interconnect) Substrate focuses on maximizing interconnection density. FCBGA Substrate aligns with this objective through its BGA connections, offering comparable or enhanced density.
Advantages of FCBGA Substrate in Circuit Design:
Compact Design:
FCBGA Substrate’s flipped chip design contributes to a more compact overall circuit layout, crucial in applications where space is limited.
Enhanced Connectivity:
The BGA connections of FCBGA Substrate provide a high-density array of connection points, ensuring efficient electrical connections.
Efficient Heat Dissipation:
FCBGA Substrate is designed to support effective heat dissipation, which is vital for maintaining optimal performance in electronic devices.
Applications in High-Performance Devices:
FCBGA Substrate finds its niche in applications where high performance, miniaturization, and efficient heat management are essential.
In summary, FCBGA Substrate stands out from conventional PCBs due to its specific design features, especially the Flip-Chip arrangement and BGA connections. When compared to Motherboards, SLP, and HDI Substrate, FCBGA Substrate demonstrates advantages in terms of compact design, enhanced connectivity, and efficient heat dissipation, making it a valuable choice in modern circuit design.
What Are the Primary Structures and Manufacturing Technologies of Package Substrate?
let’s delve into the primary structures and manufacturing technologies of Package Substrate to gain a comprehensive understanding:
Primary Structures of Package Substrate:
Flip-Chip Arrangement:
FCBGA Substrate is characterized by a Flip-Chip arrangement, where the semiconductor chip is inverted and mounted on the substrate. This allows for a more direct and efficient connection between the chip and the substrate.
Ball Grid Array (BGA) Connections:
FCBGA Substrate employs BGA connections for external connections. These solder balls provide a dense array of connection points, contributing to high-density interconnectivity.
Dielectric Layers:
Dielectric layers are integrated into the structure to insulate and separate conductive layers. They play a crucial role in maintaining electrical isolation and preventing signal interference.
Manufacturing Technologies of FCBGA Substrate:
Advanced HDI Manufacturing Technology:
FCBGA Substrate often incorporates High-Density Interconnect (HDI) manufacturing technology. This involves using advanced techniques to achieve higher wiring density, finer lines, and smaller vias, enhancing the overall performance of the substrate.
Improved HDI Fabrication Technology:
The manufacturing processes include improved HDI fabrication technology, emphasizing finer features and increased layer density. This contributes to the substrate’s ability to accommodate a greater number of connection points.
Semi-Additive Method:
FCBGA Substrate manufacturing may involve the semi-additive method, a technique that selectively adds conductive material to build up circuitry. This allows for precise control over the placement of conductive traces.
New Manufacturing Methods:
Ongoing advancements in manufacturing methods continue to shape FCBGA Substrate production. Innovations may include new materials, processes, and technologies that enhance the substrate’s overall performance.
Contributions to Advanced Package Substrate Technology:
Enhanced Connectivity:
The use of BGA connections and advanced HDI manufacturing technology contributes to enhanced connectivity, ensuring a robust and reliable electrical interface.
Miniaturization and Compact Design:
Improved HDI fabrication technology and new manufacturing methods support miniaturization, allowing for the creation of more compact and space-efficient FCBGA Substrates.
Optimized Signal Integrity:
The careful design of dielectric layers and the precise control over circuitry contribute to optimized signal integrity, reducing signal distortion and enhancing overall performance.
Efficient Heat Dissipation:
The manufacturing processes consider the incorporation of features to support efficient heat dissipation, crucial for maintaining the temperature within acceptable limits for high-performance electronic devices.
In conclusion, the primary structures and manufacturing technologies of FCBGA Substrate encompass a Flip-Chip arrangement, BGA connections, dielectric layers, and advanced manufacturing techniques such as improved HDI fabrication and semi-additive methods. These contribute to the substrate’s advanced packaging technology, ensuring enhanced connectivity, miniaturization, optimized signal integrity, and efficient heat dissipation for high-performance applications.
What Are the Frequently Asked Questions (FAQs) About Package Substrate?
1. What is Package Substrate, and how does it differ from traditional PCBs?
Addressing this question provides a fundamental understanding of Package Substrate’s unique characteristics, setting the stage for further exploration.
2. What advantages does Package Substrate offer in electronic device design?
Explaining the benefits, such as enhanced connectivity, compact design, and efficient heat dissipation, helps readers appreciate the practical applications of Package Substrate.
3. How does FCBGA Substrate contribute to high-density interconnectivity?
Delving into the use of Ball Grid Array (BGA) connections and advanced HDI manufacturing technology clarifies how FCBGA Substrate achieves high-density interconnectivity.
4. Can FCBGA Substrate be integrated into motherboard designs?
Exploring the integration of FCBGA Substrate into motherboards sheds light on its role in larger electronic systems and the versatility of its applications.
5. What role does the Flip-Chip arrangement play in FCBGA Substrate?
Understanding the Flip-Chip arrangement elucidates how the chip’s orientation influences the efficiency of electrical connections and overall circuit design.
6. How does FCBGA Substrate address heat dissipation challenges in electronic devices?
Explaining the features and manufacturing considerations for efficient heat dissipation provides insight into FCBGA Substrate’s role in maintaining optimal device performance.
7. What is the significance of dielectric layers in FCBGA Substrate?
Discussing dielectric layers helps readers grasp their importance in maintaining electrical isolation and preventing interference between conductive layers.
8. How does FCBGA Substrate align with advancements in HDI manufacturing technology?
Addressing this question highlights the incorporation of High-Density Interconnect (HDI) manufacturing technology, showcasing FCBGA Substrate’s alignment with industry advancements.
9. Are there specific applications where FCBGA Substrate excels?
Providing examples of applications where FCBGA Substrate is particularly advantageous helps readers understand its practical implications in various industries.
10. What ongoing developments can we expect in FCBGA Substrate manufacturing?
Discussing ongoing innovations in materials, processes, and technologies keeps readers informed about the dynamic nature of FCBGA Substrate manufacturing.
Is Package Substrate Paving the Way for the Future?
Recapping Crucial Points:
As we revisit the key insights discussed in the article regarding Package Substrate, it becomes evident that this advanced packaging technology is significantly shaping the present landscape of electronics design. Its unique features, such as the Flip-Chip arrangement, Ball Grid Array (BGA) connections, and integration with High-Density Interconnect (HDI) manufacturing technology, position FCBGA Substrate as a crucial component in achieving high-density interconnectivity, compact design, efficient heat dissipation, and optimized signal integrity.
Anticipating Future Development Trends:
Looking ahead, several potential development trends for FCBGA Substrate in the future electronics industry can be anticipated:
1. Miniaturization and Compact Devices:
- FCBGA Substrate is likely to play a key role in the ongoing trend towards miniaturization. As electronic devices become smaller and more compact, the demand for advanced packaging technologies that offer high-density connections in limited space will continue to rise.
2. Integration with Emerging Technologies:
- FCBGA Substrate may integrate with emerging technologies, such as 5G, Internet of Things (IoT), and artificial intelligence. The demand for compact, high-performance devices in these domains can drive further innovation in FCBGA Substrate design and manufacturing.
3. Enhanced Manufacturing Techniques:
- The future may see advancements in manufacturing techniques for FCBGA Substrate, including the development of even more refined HDI manufacturing processes, new materials, and improved semi-additive methods. These enhancements would contribute to increased performance and efficiency.
4. Application Expansion:
- FCBGA Substrate is likely to find new applications across various industries. Its capability to achieve high-density interconnectivity, compact design, and effective heat dissipation makes it suitable for a wide range of electronic devices. This applicability extends beyond consumer electronics to encompass medical devices and various other industry applications.
5. Collaboration with Semiconductor Technologies:
- Collaborations between FCBGA Substrate manufacturers and semiconductor technology developers may lead to innovations that further optimize the integration of chips with the substrate, pushing the boundaries of what is achievable in electronic design.
Insight into the Future Direction of Electronic Design:
FCBGA Substrate offers significant insights into the future trajectory of electronic design, underscoring the critical significance of high-density interconnectivity, streamlined form factors, and effective heat management. Positioned to lead in innovations, FCBGA Substrate is anticipated to play a pivotal role in shaping the design and functionality of forthcoming electronic devices as the electronics industry advances.
In conclusion, FCBGA Substrate is indeed paving the way for the future in electronics design by addressing current challenges and aligning with emerging trends. Its role in achieving smaller, more efficient, and high-performance electronic devices positions it as a key player in shaping the electronic landscape of tomorrow.