What is QFP Package Substrate?
QFP Package Substrate Vender. the Package Substrate will be made with Metal base,BT base, Showa Denko and Ajinomoto High speed materials.or other types high speed materials and high frequency materials. Our company also offers the QFP Package service.
QFP (Quad Flat Package) is a type of surface-mount integrated circuit (IC) package used for electronic components. The QFP package has leads extending from all four sides of the component body, hence the name “quad flat.” These leads are soldered onto the surface of a printed circuit board (PCB).
The substrate in a QFP package refers to the material that provides mechanical support and electrical connections for the integrated circuit. It is typically made of a non-conductive material, such as fiberglass-reinforced epoxy resin (FR-4), ceramic, or other materials suitable for the application.
The substrate serves as the base for attaching the integrated circuit chip and provides the necessary wiring connections between the chip and the external leads of the package. It also helps dissipate heat generated by the chip during operation and provides physical protection for the delicate integrated circuit components.
In summary, the QFP package substrate is the foundation upon which the integrated circuit chip is mounted, providing mechanical support, electrical connections, and thermal management for the device.
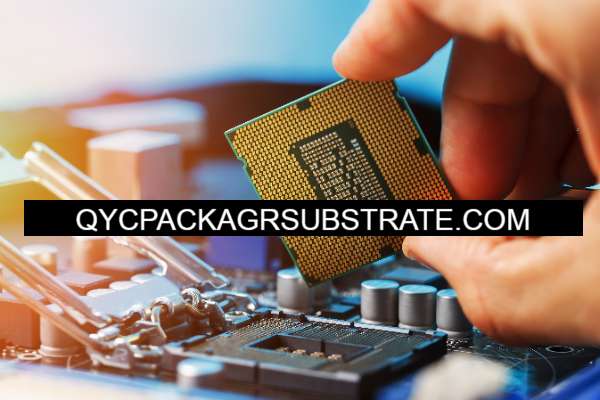
QFP Package Substrate
What are the functions of QFP Package Substrate?
The QFP (Quad Flat Package) package substrate serves several important functions in the overall operation and reliability of an integrated circuit (IC) device:
Mechanical Support: The substrate provides a sturdy base for mounting the IC chip and other components, ensuring structural integrity and stability for the package.
Electrical Connections: The substrate contains conductive traces that establish electrical connections between the IC chip and the external leads of the package. These connections facilitate the flow of signals and power between the IC and the rest of the circuit.
Signal Routing: The substrate routes signals between the IC chip and the external leads, ensuring proper transmission of data and control signals within the device and to external components.
Heat Dissipation: The substrate helps dissipate heat generated by the IC chip during operation. It may incorporate features such as thermal vias, metal layers, or heat spreaders to efficiently transfer heat away from the chip and distribute it across the package.
Electromagnetic Compatibility (EMC): The substrate may include features to mitigate electromagnetic interference (EMI) and ensure compliance with EMC requirements. This may involve shielding layers, ground planes, or other techniques to minimize electromagnetic emissions and susceptibility.
Environmental Protection: The substrate provides a protective enclosure for the IC chip, shielding it from environmental factors such as moisture, dust, and mechanical shock that could otherwise degrade performance or damage the device.
Overall, the QFP package substrate plays a crucial role in the functionality, reliability, and performance of integrated circuit devices by providing mechanical support, electrical connections, signal routing, thermal management, EMC compliance, and environmental protection.
What are the different types of QFP Package Substrate?
There are several different types of substrates used in QFP (Quad Flat Package) packages, each with its own characteristics and suitability for specific applications. Some common types of QFP package substrates include:
FR-4: FR-4 is a widely used substrate material for QFP packages. It is a type of epoxy resin composite reinforced with fiberglass. FR-4 substrates offer good electrical insulation, mechanical strength, and cost-effectiveness, making them suitable for a wide range of applications.
Ceramic: Ceramic substrates are made from materials such as alumina (Al2O3) or aluminum nitride (AlN). Ceramic substrates offer excellent thermal conductivity, high electrical insulation, and dimensional stability. They are often used in high-power or high-frequency applications where thermal management is critical.
Flexible: Flexible substrates, such as polyimide (PI) or polyester (PET), offer flexibility and conformability, making them suitable for applications where space constraints or bending requirements are present. Flexible substrates are commonly used in applications such as wearable electronics or flexible circuits.
Metal-Core: Metal-core substrates feature a metal layer, typically aluminum or copper, sandwiched between layers of insulating material such as FR-4 or ceramic. Metal-core substrates offer enhanced thermal conductivity and heat dissipation capabilities compared to traditional substrates, making them suitable for high-power LED applications or other thermal management-critical applications.
High-Temperature: High-temperature substrates are designed to withstand elevated temperatures during manufacturing processes such as reflow soldering. These substrates are often made from materials with high glass transition temperatures or thermally stable polymers.
Low-Cost Alternatives: In addition to traditional substrate materials, there are also low-cost alternatives such as laminate-based substrates or resin-coated copper (RCC) substrates. These alternatives offer cost savings but may have trade-offs in terms of electrical performance, thermal conductivity, or reliability.
The choice of substrate type depends on factors such as the specific application requirements, thermal management needs, electrical performance, cost considerations, and manufacturing processes. Each type of substrate offers unique advantages and trade-offs, and selecting the appropriate substrate is essential to achieve optimal performance and reliability in QFP package applications.
What is the relationship between QFP Package Substrate and IC packaging?
The relationship between QFP (Quad Flat Package) substrate and IC (Integrated Circuit) packaging is quite significant, as the substrate is an integral component within the overall IC packaging structure. Here’s how they relate to each other:
Physical Mounting: The IC chip is mounted onto the substrate within the QFP package. This substrate provides a stable platform for the chip to be securely attached, typically through wire bonding or flip-chip bonding techniques.
Electrical Connections: The substrate contains conductive traces that establish electrical connections between the IC chip and the external leads of the QFP package. These connections enable the transfer of signals, power, and data between the IC chip and the rest of the electronic system.
Thermal Management: The substrate plays a crucial role in dissipating heat generated by the IC chip during operation. It may incorporate features such as thermal vias, metal layers, or heat spreaders to efficiently transfer heat away from the chip and distribute it across the package, thus helping to maintain the chip’s temperature within safe operating limits.
Package Integrity: The substrate contributes to the mechanical integrity of the QFP package, providing structural support and protection for the IC chip. It helps to ensure that the chip remains securely mounted and protected from external environmental factors such as moisture, dust, and mechanical shock.
Manufacturing Process: The substrate is an essential component in the overall IC packaging manufacturing process. It undergoes various fabrication steps, including substrate material selection, layer formation, circuit patterning, and assembly, all of which are critical for producing a reliable and functional QFP package.
In summary, the QFP package substrate is closely intertwined with IC packaging, serving as a foundation for mounting the IC chip, establishing electrical connections, managing thermal properties, ensuring package integrity, and facilitating the manufacturing process. Together, these elements form a complete and functional IC package ready for integration into electronic systems.
How does QFP Package Substrate differ from PCB?
QFP (Quad Flat Package) package substrate and PCB (Printed Circuit Board) serve different roles within an electronic system, although they share some similarities. Here are the key differences between the two:
Function:
QFP Package Substrate: The substrate in a QFP package primarily serves as a mounting platform and electrical connection medium for the integrated circuit (IC) chip contained within the package. Its primary purpose is to facilitate the operation of the IC and ensure reliable electrical connections between the chip and the external leads of the package.
PCB: A PCB serves as a physical foundation for mounting various electronic components, including IC packages like QFPs. It provides electrical connections between these components through conductive traces, forming a complete circuit. PCBs can accommodate multiple components, including QFP packages, and serve as the backbone of electronic devices.
Integration Level:
QFP Package Substrate: The substrate is an integral part of the QFP package itself. It is specifically designed and manufactured to meet the requirements of the IC package, including considerations for electrical connectivity, thermal management, and mechanical support.
PCB: PCBs are standalone boards that can accommodate multiple components, including QFP packages, along with other electronic components such as resistors, capacitors, and connectors. They provide a platform for interconnecting these components to form complex electronic circuits.
Size and Complexity:
QFP Package Substrate: The substrate in a QFP package is typically smaller and less complex compared to a full-size PCB. It is designed to fit within the dimensions of the QFP package and may have fewer layers and features compared to a PCB.
PCB: PCBs come in various sizes and complexities depending on the specific application requirements. They can range from simple single-layer boards to complex multi-layer boards with intricate routing and features.
Manufacturing Process:
QFP Package Substrate: The substrate in a QFP package is typically manufactured using specialized processes tailored for IC packaging, such as thin-film deposition, photolithography, and etching. These processes are optimized for producing small, precise substrates suitable for mounting IC chips.
PCB: PCBs are manufactured using processes such as PCB fabrication, which involves layering and etching of copper-clad laminates, and PCB assembly, which involves soldering components onto the board. PCB manufacturing processes are tailored for producing larger boards with complex layouts and features.
In summary, while both QFP package substrates and PCBs are used in electronic systems, they serve different functions and have distinct characteristics tailored for their respective roles within the system. The QFP package substrate is specifically designed for mounting and connecting IC chips within QFP packages, while PCBs provide a platform for mounting various electronic components and forming complete electronic circuits.
What are the structure and production technology of QFP Package Substrate?
The structure and production technology of QFP (Quad Flat Package) package substrate involve several steps and considerations to ensure the substrate’s functionality, reliability, and compatibility with the integrated circuit (IC) chip and the overall package. Here’s an overview of the typical structure and production process:
Substrate Material Selection:
The substrate material is chosen based on factors such as electrical properties, thermal conductivity, mechanical strength, and cost.
Common substrate materials include fiberglass-reinforced epoxy resin (FR-4), ceramic, metal-core substrates (e.g., aluminum or copper), and flexible substrates (e.g., polyimide).
Substrate Fabrication:
The substrate fabrication process typically starts with a flat sheet or panel of the chosen substrate material.
For FR-4 substrates, the process involves laminating layers of fiberglass cloth with epoxy resin, curing the laminate, and then machining it to the desired dimensions.
For ceramic substrates, the process may involve sintering ceramic powder to form a solid substrate, followed by machining or laser cutting to achieve the desired shape and dimensions.
Layer Formation:
Depending on the substrate design, multiple layers may be added to the substrate to accommodate electrical traces, vias, and other features.
Layers may be added using processes such as thin-film deposition, photolithography, etching, and plating.
Circuit Patterning:
Conductive traces and pads are patterned onto the substrate layers using photolithography and etching processes.
These traces establish electrical connections between the IC chip and the external leads of the QFP package.
Via Formation:
Vias are drilled or laser-drilled through the substrate layers to establish vertical electrical connections between different layers.
Vias may be filled with conductive material (e.g., copper) to ensure reliable electrical connections.
Surface Finish:
The substrate surface is coated with a suitable finish to protect the traces and pads and facilitate soldering during assembly.
Common surface finishes include solder mask, immersion tin, immersion silver, and gold plating.
Quality Control:
Throughout the production process, various quality control measures are implemented to ensure the substrate’s dimensional accuracy, electrical integrity, and reliability.
This may involve visual inspection, electrical testing, and reliability testing to identify and rectify any defects or issues.
Assembly:
Once the substrate is fabricated and inspected, it is assembled with the IC chip and other components to form the complete QFP package.
Assembly processes may include wire bonding, flip-chip bonding, encapsulation, and lead forming.
Overall, the production technology of QFP package substrates involves a series of steps tailored to the specific substrate material and design requirements, with a focus on achieving high-quality, reliable substrates suitable for mounting IC chips within QFP packages.
Frequently Asked Questions (FAQs)
What is a QFP package substrate?
A QFP package substrate is a component of the QFP package that serves as a mounting platform and electrical connection medium for the integrated circuit (IC) chip contained within the package.
What materials are used to make QFP package substrates?
Common materials used for QFP package substrates include fiberglass-reinforced epoxy resin (FR-4), ceramic, metal-core substrates (e.g., aluminum or copper), and flexible substrates (e.g., polyimide).
What are the functions of a QFP package substrate?
The functions of a QFP package substrate include providing mechanical support for the IC chip, establishing electrical connections between the chip and the external leads of the package, managing thermal properties, ensuring package integrity, and facilitating the manufacturing process.
How is a QFP package substrate manufactured?
The manufacturing process of a QFP package substrate typically involves substrate material selection, substrate fabrication, layer formation, circuit patterning, via formation, surface finish, quality control, and assembly.
What are the different types of QFP package substrates?
Different types of QFP package substrates include FR-4, ceramic, metal-core, flexible, high-temperature, and low-cost alternatives. Each type offers unique advantages and trade-offs depending on the specific application requirements.
What factors should be considered when selecting a QFP package substrate?
Factors to consider when selecting a QFP package substrate include electrical properties, thermal conductivity, mechanical strength, dimensional stability, cost, and compatibility with the IC chip and the overall package design.
What are the advantages of using QFP package substrates?
Advantages of using QFP package substrates include their ability to provide reliable electrical connections, efficient thermal management, mechanical stability, and compatibility with various IC package designs.
What quality control measures are implemented during QFP package substrate production?
Quality control measures during QFP package substrate production may include visual inspection, electrical testing, and reliability testing to ensure dimensional accuracy, electrical integrity, and reliability.
Conclusion
In conclusion, QFP (Quad Flat Package) package substrates play a crucial role in the functionality, reliability, and performance of integrated circuit (IC) devices. These substrates serve as mounting platforms and electrical connection media for IC chips within QFP packages, offering mechanical support, establishing electrical connections, managing thermal properties, ensuring package integrity, and facilitating the manufacturing process.
QFP package substrates are manufactured using specialized processes tailored to the specific substrate material and design requirements. Common substrate materials include fiberglass-reinforced epoxy resin (FR-4), ceramic, metal-core substrates, and flexible substrates. The production process involves substrate fabrication, layer formation, circuit patterning, via formation, surface finish, quality control, and assembly.
When selecting a QFP package substrate, factors such as electrical properties, thermal conductivity, mechanical strength, dimensional stability, cost, and compatibility with the IC chip and the overall package design should be considered. Various types of QFP package substrates are available, each offering unique advantages and trade-offs depending on the specific application requirements.
Overall, QFP package substrates contribute significantly to the functionality, reliability, and performance of IC devices, ensuring optimal operation and longevity in various electronic applications