96AL2O3 Ceramic pcb
96AL2O3 Ceramic PCB Manufacturing, We offer Ceramic PCB and Ceramic package substrates with microtrace, and smallest spacing. Our company made the Ceramic substrates from 1 layer to 22 layers .
96% AL2O3 ceramic PCBs, also known as aluminum oxide ceramic PCBs, are substrates made from high-purity alumina (Al2O3) ceramics with a purity level of 96%. These PCBs offer exceptional thermal conductivity, electrical insulation, and mechanical strength, making them ideal for use in various electronic applications where reliability and performance are paramount.
The 96% AL2O3 ceramic PCBs feature a smooth surface finish and excellent dimensional stability, allowing for precise and reliable circuit patterning and component mounting. Their high thermal conductivity enables efficient heat dissipation, which is critical for electronic devices operating at high power levels or in demanding environments.
These ceramic PCBs are highly resistant to corrosion, moisture, and harsh chemicals, ensuring long-term reliability and durability even in challenging conditions. They are commonly used in power electronics, LED lighting, RF/microwave applications, and high-temperature environments where traditional PCB materials may not suffice.
Manufacturers can customize 96% AL2O3 ceramic PCBs to meet specific design requirements, including different thicknesses, sizes, and configurations. Whether for prototype development or mass production, these ceramic substrates offer excellent electrical performance and thermal management capabilities, contributing to the overall reliability and functionality of electronic systems.
What is a 96AL2O3 Ceramic PCB?
A 96AL2O3 Ceramic PCB refers to a printed circuit board (PCB) made from a ceramic material composed primarily of aluminum oxide (Al2O3) with a purity of 96%. This type of ceramic PCB offers several advantages over traditional PCB materials such as FR4 (a type of fiberglass-reinforced epoxy laminate):
- High thermal conductivity: Ceramic materials like aluminum oxide have excellent thermal conductivity compared to traditional PCB substrates. This property allows for efficient heat dissipation, which is crucial in electronic devices, especially those with high power densities.
- Excellent electrical insulation: Ceramic materials possess high electrical insulation properties, making them suitable for applications where electrical isolation is critical.
- High mechanical strength: Ceramic PCBs are mechanically robust, providing better resistance to mechanical stress, bending, and vibration compared to traditional PCB substrates.
- Chemical inertness: Ceramic materials are typically chemically inert, meaning they are resistant to corrosion and chemical reactions. This property enhances the durability and reliability of ceramic PCBs, especially in harsh environments.
- Dimensional stability: Ceramic materials exhibit minimal dimensional changes over a wide range of temperatures, ensuring the integrity and reliability of electronic assemblies.
Due to these properties, 96AL2O3 Ceramic PCBs are commonly used in high-performance electronic applications where thermal management, reliability, and longevity are paramount, such as in power electronics, high-frequency RF devices, LED lighting, and aerospace applications.
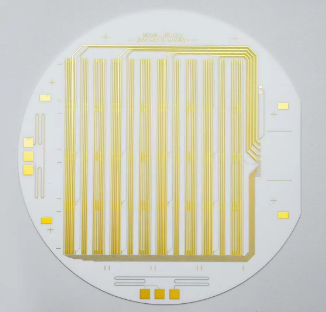
96AL2O3 Ceramic pcb
What are the 96AL2O3 Ceramic PCB Design Guidelines?
Designing with 96AL2O3 ceramic PCBs requires careful consideration of their unique properties and characteristics. Here are some general design guidelines:
- Thermal Management: Utilize the high thermal conductivity of ceramic materials to efficiently dissipate heat from high-power components. Place heat-generating components close to vias or thermal pads to facilitate heat transfer to the PCB substrate.
- Mechanical Considerations: Ceramic PCBs are more brittle than traditional FR4 boards, so avoid designs that may subject the board to excessive mechanical stress or bending. Ensure adequate support for the board within the enclosure to prevent flexing or cracking.
- Component Placement: Optimize component placement to minimize signal interference and maximize thermal performance. Place high-frequency components and signal traces away from high-power components to reduce electromagnetic interference (EMI). Arrange components to minimize signal loop area and impedance discontinuities.
- Via Design: Use vias strategically to provide electrical connections between different layers of the PCB. Implement thermal vias to enhance heat dissipation from heat-generating components to the PCB substrate. Ensure proper via placement and spacing to maintain signal integrity and thermal performance.
- Trace Width and Spacing: Design trace widths and spacing to accommodate the required electrical current and voltage levels. Consider the high dielectric strength of ceramic materials when determining trace spacing to prevent electrical breakdown.
- Dielectric Properties: Take into account the dielectric properties of the ceramic material when designing transmission lines and impedance-controlled traces. Adjust trace width and spacing to achieve the desired impedance characteristic.
- Soldering Considerations:Ceramic PCBs may require special soldering techniques due to their high thermal conductivity and low coefficient of thermal expansion (CTE). Use solder pastes and reflow profiles suitable for ceramic substrates to achieve reliable solder joints without damaging the board.
- Environmental Considerations: Ceramic PCBs offer excellent resistance to moisture, chemicals, and temperature extremes. However, consider environmental factors such as humidity, temperature cycling, and chemical exposure when selecting components and materials for the PCB assembly.
- Testing and Inspection: Perform thorough electrical testing and inspection to ensure the integrity and reliability of the ceramic PCB assembly. Use non-destructive testing techniques such as X-ray inspection to detect any defects or anomalies in the PCB and solder joints.
By following these guidelines and considering the unique properties of 96AL2O3 ceramic PCBs, designers can create robust and reliable electronic assemblies for a variety of high-performance applications.
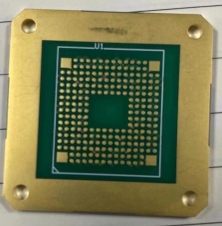
Ceramic package substrates
What is the 96AL2O3 Ceramic PCB Fabrication Process?
The fabrication process for 96AL2O3 ceramic PCBs involves several steps to create a high-quality substrate suitable for electronic applications. Here’s a general overview of the process:
- Material Selection: High-purity alumina powder, typically with a purity of 96%, is selected as the primary material for the ceramic substrate. The quality of the powder is crucial to ensure the desired properties of the final ceramic PCB.
- Mixing and Forming: The alumina powder is mixed with binders and additives to create a slurry with the desired consistency. This slurry is then formed into sheets or green tapes through processes such as tape casting or slip casting. These green sheets will serve as the base material for the ceramic PCB.
- Layering and Printing: Multiple green sheets are stacked together to achieve the desired thickness for the PCB substrate. If necessary, conductive traces and vias are printed onto the green sheets using screen printing or other appropriate techniques. These conductive elements will later facilitate electrical connections between components on the PCB.
- Laminating and Drying: The stacked green sheets undergo a lamination process to bond them together into a solid structure. Pressure and heat are applied during lamination to ensure proper bonding. After lamination, the structure is dried to remove any remaining moisture.
- Machining: The dried laminate undergoes machining processes such as milling, drilling, and routing to achieve the final dimensions and features of the ceramic PCB. This step is crucial for creating the necessary patterns for circuit traces, vias, and component mounting locations.
- Firing: The machined ceramic substrate is then fired in a high-temperature kiln to sinter the alumina particles and remove the organic binders. The firing process typically occurs at temperatures above 1500°C, allowing the alumina to densify and form a solid, highly durable ceramic material.
- Surface Finishing: After firing, the ceramic substrate may undergo additional surface treatment processes such as polishing or coating to improve its electrical properties, surface smoothness, or solderability.
- Quality Control and Testing: The finished ceramic PCBs undergo rigorous quality control and testing procedures to ensure they meet the required specifications for electrical performance, dimensional accuracy, and reliability.
By following these steps, manufacturers can produce high-quality 96AL2O3 ceramic PCBs suitable for a wide range of electronic applications, especially those requiring superior thermal management, electrical insulation, and mechanical strength.
How do you manufacture a 96AL2O3 Ceramic PCB?
Manufacturing a 96AL2O3 ceramic PCB involves a specialized process tailored to the unique properties of alumina ceramic material. Here’s a detailed outline of the typical manufacturing process:
- Material Preparation: High-purity alumina powder, with a purity of 96%, is selected as the primary raw material. The powder is carefully inspected for quality and consistency. Other additives and binders may also be included in the formulation to enhance specific properties or facilitate processing.
- Formulation and Mixing: The alumina powder is mixed with binders, solvents, and other additives to create a homogenous slurry. The mixing process is crucial to ensure an even distribution of particles and additives throughout the mixture.
- Green Sheet Formation: The slurry is then cast or tape-cast onto a substrate to form thin green sheets. These green sheets serve as the base material for the ceramic PCB. The thickness of the green sheets is typically controlled to achieve the desired final thickness of the ceramic substrate.
- Layering and Printing: Multiple green sheets are stacked together to build up the desired thickness of the ceramic substrate. During this process, conductive traces, vias, and other features may be printed onto the green sheets using techniques such as screen printing or inkjet printing. These features will later facilitate electrical connections between components on the PCB.
- Lamination: The stacked green sheets undergo a lamination process to bond them together into a solid structure. Pressure and heat are applied during lamination to ensure proper bonding between the layers. This step is essential for creating a mechanically stable substrate.
- Machining: The laminated ceramic substrate is then machined to achieve the final dimensions and features required for the PCB. Machining processes such as milling, drilling, and routing are used to create the necessary patterns for circuit traces, vias, and component mounting locations.
- Firing: The machined ceramic substrate undergoes a high-temperature firing process in a kiln. During firing, the organic binders in the green sheets are burned off, and the alumina particles sinter together to form a dense, solid ceramic material. The firing process typically occurs at temperatures above 1500°C and may involve multiple stages to achieve the desired properties.
- Surface Finishing: After firing, the ceramic PCB may undergo additional surface treatment processes such as polishing or coating to improve its electrical properties, surface smoothness, or solderability. These finishing steps help ensure the final PCB meets the required specifications for performance and reliability.
- Quality Control and Testing: The finished ceramic PCBs undergo rigorous quality control and testing procedures to verify their electrical performance, dimensional accuracy, and mechanical integrity. Various tests may be conducted, including electrical continuity testing, thermal cycling, and mechanical stress testing, to ensure the PCBs meet industry standards and customer requirements.
By following these manufacturing steps, manufacturers can produce high-quality 96AL2O3 ceramic PCBs tailored to the specific needs of electronic applications requiring superior thermal management, electrical insulation, and mechanical strength.
How much should a 96AL2O3 Ceramic PCB cost?
The cost of a 96AL2O3 ceramic PCB can vary widely depending on several factors including the size, complexity, quantity, and specific requirements of the PCB. Additionally, other factors such as the manufacturing process used, the level of customization, and the supplier or manufacturer’s pricing structure can also influence the final cost.
As a rough estimate, 96AL2O3 ceramic PCBs tend to be more expensive compared to traditional FR4 or other organic substrate PCBs due to the higher cost of raw materials, the specialized manufacturing processes involved, and the superior properties of alumina ceramic material. The cost can range from tens to hundreds of dollars per square inch, with larger or more complex boards typically costing more.
For a more accurate cost estimate, it’s recommended to contact PCB manufacturers or suppliers directly with your specific requirements and request a quotation. They can provide a detailed cost breakdown based on factors such as material costs, manufacturing processes, tooling costs, and any additional services or features required for your project.
Keep in mind that while 96AL2O3 ceramic PCBs may have a higher upfront cost compared to other types of PCBs, they offer significant benefits such as superior thermal conductivity, electrical insulation, mechanical strength, and reliability, making them suitable for demanding applications where performance and durability are critical.
What is the base material of a 96AL2O3 Ceramic PCB?
The base material of a 96AL2O3 Ceramic PCB is alumina oxide ceramic, specifically with a composition of 96% aluminum oxide (Al2O3). This material is renowned for its exceptional thermal conductivity, mechanical strength, and electrical insulation properties, making it an ideal substrate for demanding electronic applications.
Alumina oxide ceramic is derived from aluminum oxide, a naturally occurring compound that undergoes processing to create the desired material properties. The high purity level of 96% ensures optimal performance and reliability in electronic circuits operating under harsh conditions.
One of the key characteristics of alumina oxide ceramic is its excellent thermal conductivity, which allows for efficient dissipation of heat generated by electronic components. This property is crucial for applications where temperature management is critical, such as power electronics, LED lighting, and automotive systems.
In addition to thermal conductivity, alumina oxide ceramic exhibits high mechanical strength and rigidity, providing robust support for electronic components and ensuring the durability of the PCB. Its inherent electrical insulation properties make it suitable for applications requiring reliable isolation of electrical signals and components.
Moreover, alumina oxide ceramic offers excellent resistance to corrosion, chemicals, and wear, ensuring long-term reliability in challenging environments. This makes 96AL2O3 Ceramic PCBs suitable for aerospace, medical, and industrial applications where reliability is paramount.
Overall, the base material of a 96AL2O3 Ceramic PCB, alumina oxide ceramic, provides a solid foundation for high-performance electronic circuits, offering a combination of thermal conductivity, mechanical strength, electrical insulation, and chemical resistance essential for demanding applications.
Which company makes 96AL2O3 Ceramic PCBs?
One of the manufacturers of 96AL2O3 Ceramic PCBs is some specialized ceramic PCB manufacturing companies, such as Hitachi Chemical in Japan, Kyocera in the United States, Ferrotec in Germany, and so on. These companies have rich experience and technical expertise in the manufacturing and application of ceramic materials.
However, our company is also capable of producing 96AL2O3 Ceramic PCBs. As a professional electronic manufacturing company, we have advanced production equipment and a skilled technical team to meet the demand for high-quality ceramic PCBs from our customers. Our production process includes raw material procurement, design and engineering validation, manufacturing processing, quality control, and so on, ensuring reliable product quality.
Firstly, we choose high-quality 96AL2O3 ceramic material as the substrate to ensure its excellent thermal conductivity, insulation, and mechanical strength. Then, we use advanced processing techniques such as CNC machining, laser cutting, etc., to precisely process the ceramic substrate to meet the diverse needs of our customers. Throughout the production process, we strictly control every step to ensure stable and reliable product quality.
In addition to production processes, we also prioritize communication and collaboration with our customers. Our technical team can provide customized solutions based on customer requirements and maintain close communication with customers throughout the entire project process, promptly responding to customer needs and feedback.
In summary, our company, as a professional electronic manufacturing company, has rich experience and advanced technology to produce high-quality 96AL2O3 Ceramic PCBs and provide customized solutions to meet various customer needs.
Qualities of Good Customer Service
Good customer service is characterized by several key qualities:
- Responsiveness: This involves promptly addressing customer inquiries, concerns, and requests. Whether it’s through phone, email, or in-person interactions, responding quickly shows customers that their needs are valued and important.
- Empathy: Empathizing with customers means understanding their emotions, concerns, and perspectives. It involves actively listening to their issues, showing compassion, and demonstrating a genuine desire to help solve their problems.
- Clear Communication: Effective communication is essential in customer service. It means conveying information clearly and concisely, avoiding jargon, and ensuring that customers understand the solutions or actions being proposed.
- Professionalism: Maintaining professionalism in all interactions is crucial. This includes being polite, courteous, and respectful at all times, regardless of the situation. Professionalism also involves maintaining composure and staying calm, even in challenging or stressful situations.
- Knowledgeability: Customers expect service representatives to be knowledgeable about the products or services offered. Having a deep understanding of the company’s offerings allows representatives to provide accurate information, answer questions, and offer helpful recommendations.
- Problem-Solving Skills: Effective problem-solving is a key aspect of good customer service. It involves identifying issues, analyzing root causes, and finding practical solutions to resolve customer problems in a timely manner.
- Consistency: Consistency is important for building trust and loyalty with customers. Providing consistent service across all channels and interactions ensures that customers receive a reliable and predictable experience every time they engage with the company.
By embodying these qualities, businesses can create positive experiences for their customers and build long-lasting relationships that drive satisfaction and loyalty.
FAQs
What is a 96AL2O3 Ceramic PCB?
A 96AL2O3 Ceramic PCB is a type of printed circuit board made from 96% alumina oxide ceramic material. It offers exceptional thermal conductivity, high mechanical strength, and excellent electrical insulation properties.
What are the advantages of using 96AL2O3 Ceramic PCBs?
Some advantages include superior thermal management, resistance to high temperatures, excellent electrical insulation, and compatibility with high-frequency applications. They are also known for their reliability and durability in harsh environments.
What applications are 96AL2O3 Ceramic PCBs suitable for?
These PCBs are commonly used in industries such as power electronics, LED lighting, aerospace, automotive, medical devices, and telecommunications due to their ability to withstand high temperatures and harsh conditions.
How are 96AL2O3 Ceramic PCBs manufactured?
The manufacturing process typically involves forming the ceramic substrate, printing conductive traces and components, and firing or sintering the board at high temperatures. Additional processes such as metallization and coating may also be employed.
What are the design considerations for 96AL2O3 Ceramic PCBs?
Designers need to consider factors such as thermal management, mechanical stability, compatibility with components and assembly processes, electrical performance, and cost-effectiveness when designing with 96AL2O3 Ceramic PCBs.
Are 96AL2O3 Ceramic PCBs more expensive than traditional PCBs?
Yes, 96AL2O3 Ceramic PCBs tend to be more expensive due to the cost of ceramic materials and the specialized manufacturing processes involved. However, their unique properties often justify the investment in many high-performance applications.
Can 96AL2O3 Ceramic PCBs be customized for specific requirements?
Yes, manufacturers often offer customization services to tailor 96AL2O3 Ceramic PCBs to meet specific size, shape, and performance requirements. Customization may include substrate thickness, metallization patterns, and surface finishes.