ABF(Ajinomoto) FCBGA Substrate Manufacturer
ABF(Ajinomoto) FCBGA Substrate Manufacturer,ABF FCBGA Substrates are advanced packaging solutions for high-performance integrated circuits. Utilizing a build-up film process, these substrates feature multiple layers of insulating material and conductive traces, enabling dense interconnections and efficient signal transmission. With flip chip bonding technology, the IC die is directly attached to the substrate, enhancing electrical performance and thermal management. These substrates find extensive use in CPUs, GPUs, and networking equipment, where reliability, miniaturization, and high-speed data processing are paramount. Offering superior electrical characteristics and reliability, ABF FCBGA Substrates are integral components in today’s complex semiconductor devices.
What is ABF FCBGA Substrate?
ABF FCBGA (Ajinomoto Build-up Film Flip Chip Ball Grid Array) substrate is a type of packaging technology used in integrated circuits (ICs), particularly in high-performance applications like CPUs, GPUs, and other complex semiconductor devices. This substrate technology employs a build-up film process, where multiple layers of insulating material and conductive traces are deposited and patterned to create the necessary interconnections between the chip and the package’s external connections.
The “flip chip” aspect refers to the arrangement of the integrated circuit where the active surface (containing the circuitry) is flipped downward and connected directly to the substrate using solder bumps. This configuration offers several advantages over traditional wire bonding methods, including shorter interconnection lengths, reduced parasitic effects, and improved thermal performance.
The “Ball Grid Array” (BGA) indicates the arrangement of solder balls on the bottom side of the package, which serve as the interface between the IC and the circuit board it’s mounted on. BGA packages offer high-density interconnections and are well-suited for devices with a high pin count.
ABF FCBGA substrates are known for their reliability, high electrical performance, and suitability for advanced semiconductor devices requiring dense interconnections and efficient heat dissipation. They are commonly used in applications where performance, reliability, and miniaturization are critical, such as in high-end computing, networking equipment, and telecommunications infrastructure.
By extending this packaging technology to 300 words, we could delve into more details about its fabrication process, its advantages over competing technologies, its applications in various industries, and ongoing research and development efforts aimed at further enhancing its performance and capabilities. Additionally, we could discuss specific companies or products utilizing ABF FCBGA substrates and how this technology contributes to their competitiveness in the market.
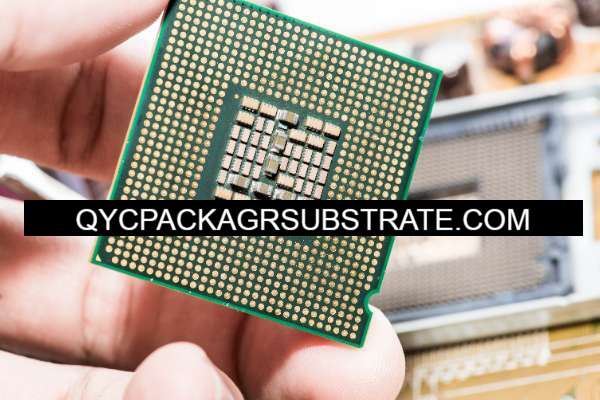
ABF(Ajinomoto) FCBGA Substrate Manufacturer
What are the ABF FCBGA Substrate Design Guidelines?
ABF FCBGA substrate design guidelines encompass a set of principles and recommendations for designing the layout and structure of the substrate to ensure optimal performance, reliability, and manufacturability of integrated circuits. These guidelines are crucial for achieving high electrical performance, minimizing signal interference, and ensuring proper thermal management. Here are some key aspects typically covered in ABF FCBGA substrate design guidelines:
- Signal Integrity: Ensuring signal integrity involves minimizing signal reflections, crosstalk, and other forms of interference that can degrade the quality of electrical signals transmitted through the substrate. Guidelines may include recommendations for controlled impedance routing, signal layer stackup, and minimizing signal discontinuities.
- Power Delivery: Proper power delivery is essential for stable operation and performance of integrated circuits. Design guidelines may specify requirements for power distribution network (PDN) design, including power plane capacitance, via placement for low impedance paths, and decoupling capacitor placement for noise reduction.
- Thermal Management: Effective thermal management is critical for preventing overheating of the integrated circuit, which can lead to performance degradation or even failure. Guidelines may include provisions for thermal vias, thermal pad placement, and heat spreader design to facilitate efficient heat dissipation from the chip to the substrate and ultimately to the surrounding environment.
- Manufacturability: Design guidelines also address manufacturability considerations to ensure that the substrate can be fabricated reliably and cost-effectively. This may include rules for minimum feature sizes, spacing requirements, alignment tolerances, and other factors relevant to the manufacturing process.
- Package Size and Layout: Guidelines may provide recommendations for the overall package size, pad pitch, and arrangement of solder balls to optimize assembly and compatibility with standard mounting processes.
- Material Selection: Guidelines may specify requirements for the selection of materials used in the substrate, including the type of build-up film, dielectric constants, and thermal properties to meet performance and reliability goals.
- Testing and Validation: Design guidelines may also include provisions for testing and validation of the substrate design to ensure compliance with performance specifications and reliability requirements.
These guidelines are typically developed based on industry standards, empirical data, and best practices established through research and experience. Adhering to these guidelines helps ensure that ABF FCBGA substrates meet the stringent requirements of high-performance semiconductor applications.
What is the ABF FCBGA Substrate Fabrication Process?
The fabrication process of ABF FCBGA (Ajinomoto Build-up Film Flip Chip Ball Grid Array) substrates involves several steps to create a sophisticated interconnection platform for integrated circuits (ICs). Here’s a general overview of the typical fabrication process:
- Substrate Preparation: The process begins with the preparation of a base substrate, which is typically a rigid material such as silicon or glass. This substrate serves as the foundation upon which subsequent layers will be deposited.
- Build-up Film Deposition:The build-up film deposition involves creating multiple layers of insulating material and conductive traces on the substrate. This is often achieved using a technique known as thin-film deposition, where successive layers of material are deposited onto the substrate surface using methods such as chemical vapor deposition (CVD) or physical vapor deposition (PVD).
- Laser Drilling: Laser drilling is used to create vias (vertical interconnect access) in the build-up film layers. These vias provide vertical connections between different layers of the substrate, allowing for the routing of signals and power throughout the structure.
- Circuit Patterning: After the vias are drilled, the conductive traces are patterned onto the build-up film layers using photolithography or other etching techniques. This process defines the electrical pathways that will connect the various components of the integrated circuit.
- Die Attach and Flip Chip Bonding: In the flip chip bonding process, the IC (integrated circuit) die is attached to the substrate with its active surface facing downward. Solder bumps are then formed on the bond pads of the IC, which will later be used to make electrical connections with the substrate.
- Underfill Encapsulation: Underfill encapsulation involves filling the gap between the IC die and the substrate with a specialized epoxy resin to provide mechanical support and protect the solder joints from mechanical stress and moisture.
- Solder Ball Attachment: Solder balls are attached to the bottom side of the substrate using a solder paste reflow process. These solder balls serve as the interface between the IC package and the printed circuit board (PCB) upon which it will be mounted.
- Testing and Inspection: The fabricated ABF FCBGA substrates undergo rigorous testing and inspection to ensure that they meet the required electrical and mechanical specifications. This may include electrical continuity tests, visual inspection, and thermal cycling tests to assess reliability.
- Packaging and Final Assembly: Once the substrates pass inspection, they are packaged into final IC packages, which may include additional components such as heat spreaders or lids for improved thermal performance. The packaged ICs are then ready for integration into electronic devices.
Overall, the fabrication process of ABF FCBGA substrates requires precision and attention to detail to ensure the reliable operation of the resulting integrated circuits in demanding applications.
How do you manufacture ABF FCBGA Substrates?
Manufacturing ABF FCBGA (Ajinomoto Build-up Film Flip Chip Ball Grid Array) substrates involves a series of intricate steps to create a sophisticated interconnection platform for integrated circuits (ICs). Here’s a detailed breakdown of the typical manufacturing process:
- Substrate Preparation: The process begins with the preparation of a base substrate, usually made of a rigid material such as silicon, glass, or laminate. This substrate serves as the foundation for subsequent layers.
- Build-up Film Deposition: Multiple layers of insulating material and conductive traces are deposited onto the substrate. This is typically achieved using a build-up film process, where successive layers of dielectric material and conductive traces are applied using techniques like chemical vapor deposition (CVD) or physical vapor deposition (PVD).
- Circuit Patterning: Photolithography or similar processes are used to pattern the conductive traces onto the build-up film layers. This step defines the electrical pathways that will connect the various components of the integrated circuit.
- Via Formation: Vias (vertical interconnect access) are created in the build-up film layers to provide vertical connections between different layers of the substrate. This is typically done using laser drilling or chemical etching processes.
- Metalization: After vias are formed, metal layers are deposited onto the substrate surface to provide electrical connectivity between different layers. These metal layers may also serve as redistribution layers to reroute signals as needed.
- Die Attachment and Flip Chip Bonding: The IC (integrated circuit) die is attached to the substrate with its active surface facing downward. Solder bumps are then formed on the bond pads of the IC, which will later be used to make electrical connections with the substrate.
- Underfill Encapsulation: An underfill material, often a specialized epoxy resin, is dispensed around the periphery of the IC die and flows into the gap between the die and the substrate. This provides mechanical support and protects the solder joints from mechanical stress and moisture.
- Solder Ball Attachment: Solder balls are attached to the bottom side of the substrate using a solder paste reflow process. These solder balls serve as the interface between the IC package and the printed circuit board (PCB) upon which it will be mounted.
- Testing and Inspection: The manufactured substrates undergo rigorous testing and inspection to ensure they meet the required electrical and mechanical specifications. This may include electrical continuity tests, visual inspection, and thermal cycling tests.
- Packaging and Final Assembly: Once the substrates pass inspection, they are packaged into final IC packages, which may include additional components such as heat spreaders or lids for improved thermal performance. The packaged ICs are then ready for integration into electronic devices.
Overall, manufacturing ABF FCBGA substrates demands precision, advanced fabrication techniques, and stringent quality control measures to ensure the reliable operation of the resulting integrated circuits in diverse applications.
How much should ABF FCBGA Substrates cost?
The cost of ABF FCBGA (Ajinomoto Build-up Film Flip Chip Ball Grid Array) substrates can vary significantly depending on various factors such as substrate size, complexity, materials used, manufacturing process, and volume production. However, to provide a general estimate, ABF FCBGA substrates typically cost several dollars to tens of dollars per unit in mass production.
Here are some factors that influence the cost of ABF FCBGA substrates:
- Substrate Size: Larger substrates require more materials and processing steps, leading to higher costs.
- Complexity: Substrates with more layers, finer features, and tighter tolerances are more complex to manufacture and often command higher prices.
- Materials Used: The type and quality of materials used in the substrate fabrication process can significantly impact the cost. High-performance materials may cost more but offer superior electrical and thermal properties.
- Manufacturing Process:The fabrication process used to manufacture ABF FCBGA substrates can vary, with some processes being more automated and efficient than others. Advanced manufacturing technologies may incur higher initial setup costs but could result in lower per-unit costs in high-volume production.
- Volume Production: Economies of scale play a significant role in substrate cost. Higher volume production typically leads to lower per-unit costs due to spreading fixed costs across a larger number of units.
- Customization and Special Features: Substrates with custom designs, special features, or additional testing requirements may incur extra costs.
- Supplier and Market Dynamics:The pricing of ABF FCBGA substrates can also be influenced by market demand, supplier competition, and fluctuations in raw material prices.
Overall, while ABF FCBGA substrates may represent a significant portion of the total cost of an integrated circuit package, they are essential for ensuring the performance, reliability, and manufacturability of high-performance semiconductor devices. Companies involved in the design and manufacturing of electronic products carefully consider the cost of substrates along with other factors to optimize the overall cost-effectiveness of their products.
What is ABF FCBGA Substrate Base Material?
The base material of ABF FCBGA (Ajinomoto Build-up Film Flip Chip Ball Grid Array) substrates primarily consists of a high-performance laminate made from glass-reinforced epoxy resins. This base material serves as the foundational layer upon which additional layers of dielectric and conductive materials are built up. The specific components of the base material include:
- Glass-Reinforced Epoxy Resin: This composite material combines glass fibers for mechanical strength and epoxy resin for electrical insulation. The glass fibers provide rigidity and dimensional stability, which are critical for maintaining the integrity of the substrate during the various stages of manufacturing and during operation.
- Ajinomoto Build-up Film (ABF): This is a proprietary dielectric film developed by Ajinomoto Fine-Techno Co., Inc. The ABF material is used for the build-up layers that are applied to the base substrate. It offers excellent insulation properties, fine patterning capabilities, and a low coefficient of thermal expansion, which matches well with the silicon die and the overall package, reducing the risk of mechanical stress and failure.
- Copper Foils: Copper is used extensively for creating conductive traces and interconnections in the substrate. Thin copper foils are laminated onto the dielectric layers and patterned using photolithography and etching processes to form the necessary electrical pathways.
The combination of these materials results in a substrate that offers high electrical performance, mechanical strength, and thermal stability, which are essential for supporting the dense interconnections and high-frequency signals typical of advanced semiconductor devices. The choice of materials and the specific layering and processing techniques are carefully optimized to ensure that the substrates meet the stringent requirements of modern electronic applications.
Which company manufactures ABF FCBGA Substrates?
Currently, there are many companies manufacturing ABF FCBGA (Ajinomoto Build-up Film Flip Chip Ball Grid Array) substrates, including well-known semiconductor materials and packaging suppliers, as well as companies specializing in high-performance substrate manufacturing. These companies offer various types of ABF FCBGA substrates globally to meet the needs of various application fields.
As a company focused on electronic component manufacturing, we can also produce ABF FCBGA substrates. We have advanced manufacturing equipment and technology, as well as an experienced engineering team capable of designing and manufacturing high-quality substrate products. Below is the general process of producing ABF FCBGA substrates in our company:
- Design and Engineering: Our engineering team conducts substrate design and engineering analysis according to customer requirements and specifications. This includes determining substrate size, layer stack-up, electrical characteristics, and thermal management solutions.
- Material Procurement and Preparation: We procure high-quality materials such as glass-reinforced epoxy resin base material, ABF film, and copper foils. These materials undergo strict quality control and inspection to ensure they meet our manufacturing requirements.
- Production Process: We use advanced production equipment and processes to stack ABF films and copper foil layers on the substrate. Through processes such as lithography, etching, and deposition, complex circuit patterns and vertical interconnects are formed.
- Chip Attachment and Packaging: We use flip chip bonding technology to attach integrated circuit chips to the substrate, followed by encapsulation and packaging with thermosetting resin. During this process, we ensure reliable electrical connections between the chip and the substrate and effective thermal management.
- Final Testing and Validation: Each production batch of substrates undergoes rigorous testing and validation to ensure they meet specifications and performance requirements. This includes electrical testing, thermal cycle testing, and reliability assessments.
We are committed to providing high-quality ABF FCBGA substrate products to meet customers’ requirements for high performance, reliability, and cost-effectiveness. Our manufacturing capabilities and technical expertise enable us to stand out in the competitive market environment and achieve success with our customers.
What are the 7 qualities of good customer service?
Good customer service is essential for building strong relationships with customers and ensuring their satisfaction. Seven qualities of good customer service include:
- Empathy: Customer service representatives should demonstrate empathy by understanding and acknowledging the customer’s feelings, concerns, and needs. This involves actively listening to customers, showing compassion, and providing personalized assistance.
- Patience: Patience is crucial when dealing with customers who may be frustrated, confused, or upset. Customer service representatives should remain calm and composed, even in challenging situations, and take the time to address each customer’s concerns thoroughly.
- Communication Skills: Effective communication is key to providing good customer service. Customer service representatives should communicate clearly, concisely, and courteously, both verbally and in writing. They should also be able to adapt their communication style to suit the preferences and needs of different customers.
- Product Knowledge: Customer service representatives should have a deep understanding of the products or services they are supporting. This enables them to answer customer questions accurately, provide helpful recommendations, and troubleshoot issues effectively.
- Problem-Solving Abilities:Good customer service involves quickly and efficiently resolving customer problems and complaints. Customer service representatives should be proactive in identifying solutions, taking ownership of issues, and following through until the customer is satisfied.
- Professionalism: Professionalism is essential in all customer interactions. Customer service representatives should maintain a positive attitude, remain respectful and courteous, and adhere to company policies and procedures at all times.
- Responsiveness:Customers expect timely responses to their inquiries and concerns. Good customer service involves being responsive and accessible to customers through various channels, such as phone, email, chat, or social media. Customer service representatives should strive to provide prompt assistance and follow-up to ensure customer needs are met.
By embodying these qualities, companies can deliver exceptional customer service experiences that foster loyalty, positive word-of-mouth, and long-term success.
FAQs
What is ABF FCBGA substrate?
ABF FCBGA (Ajinomoto Build-up Film Flip Chip Ball Grid Array) substrate is a type of packaging technology used in integrated circuits (ICs). It involves a build-up film process with multiple layers of insulating material and conductive traces, facilitating high-density interconnections.
What are the advantages of ABF FCBGA substrates?
ABF FCBGA substrates offer several advantages, including shorter interconnection lengths, reduced parasitic effects, improved thermal performance, and suitability for high pin-count devices. They also provide excellent electrical performance and reliability.
What applications are ABF FCBGA substrates used in?
ABF FCBGA substrates are commonly used in high-performance applications such as CPUs, GPUs, networking equipment, telecommunications infrastructure, and other complex semiconductor devices where miniaturization, performance, and reliability are critical.
How are ABF FCBGA substrates manufactured?
The manufacturing process involves substrate preparation, build-up film deposition, circuit patterning, via formation, die attachment and flip chip bonding, underfill encapsulation, solder ball attachment, testing, and final assembly. Advanced fabrication techniques and materials are utilized to ensure high quality and reliability.
What are the design guidelines for ABF FCBGA substrates?
Design guidelines include recommendations for signal integrity, power delivery, thermal management, manufacturability, package size and layout, material selection, and testing/validation. Adhering to these guidelines ensures optimal performance and reliability of the substrates.
Which companies manufacture ABF FCBGA substrates?
Several companies manufacture ABF FCBGA substrates, including semiconductor materials and packaging suppliers, as well as specialized substrate manufacturers. These companies provide a range of substrate products to meet diverse customer needs.
What are the cost considerations for ABF FCBGA substrates?
The cost of ABF FCBGA substrates varies depending on factors such as substrate size, complexity, materials used, manufacturing process, and volume production. Generally, they range from several dollars to tens of dollars per unit in mass production.