Advance Semiconductor substrate manufacturer and package substrate manufacturer. We use advanced Msap and Sap technology, High multilayer interconnection substrates from 2 to 20 layers,
In the dynamic sphere of semiconductor advancements, intricate substrates assume a central role as foundational materials in the meticulous construction of semiconductor devices. Serving as the bedrock for integrating transistors, resistors, and capacitors, these substrates shape the intricate architecture of semiconductor components, particularly emphasizing the significance of integrated circuits (ICs).
Distinctive in their attributes, advanced semiconductor substrates feature heightened thermal conductivity, impeccable electrical insulation, minimal signal loss, and adaptability to the diminishing feature sizes inherent in semiconductor manufacturing processes. While silicon remains foundational, these substrates seamlessly integrate diverse materials or undergo specific modifications to optimize key properties.
Distinctive attributes of advanced semiconductor substrates include heightened thermal conductivity, impeccable electrical insulation, minimal signal loss, and adaptability to the diminishing feature sizes inherent in semiconductor manufacturing processes. While silicon maintains its prominence, advanced substrates seamlessly integrate diverse materials or undergo specific modifications to optimize key properties.
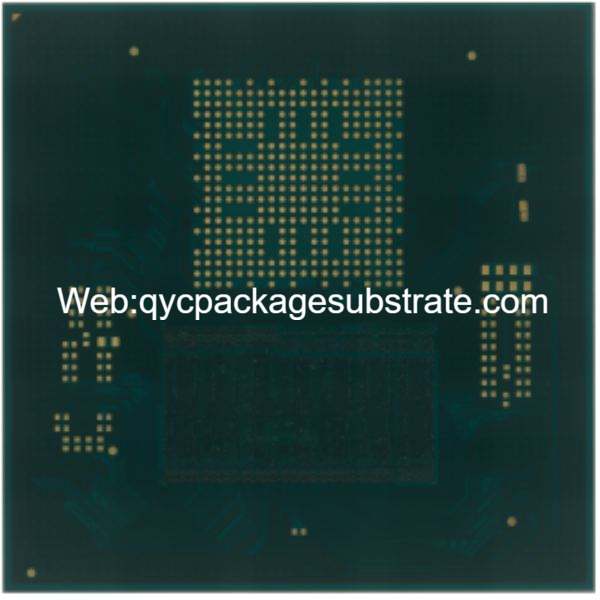
What Functions Does Advance Semiconductor Substrate Have?
Within the intricate tapestry of semiconductor device manufacturing, advanced semiconductor substrates play a dynamic and multifaceted role, embodying a multitude of essential functions:
Structural Foundation: Acting as the foundational cornerstone, these substrates offer robust support to the intricate components of semiconductor devices, guaranteeing sustained structural integrity.
Heat Dissipation Mastery: Harnessing high thermal conductivity, these substrates excel in efficiently dissipating the heat generated during device operation, adeptly mitigating potential overheating challenges.
Electrical Insulation Expertise: Precision-engineered for optimal electrical insulation, these substrates effectively prevent unintended electrical interactions between components, safeguarding the reliability and functionality of devices.
Signal Fidelity: Precision-crafted to mitigate signal loss, advanced substrates adeptly enable the smooth transmission of electrical signals between components, ensuring the unblemished purity and precision of conveyed data.
Catalysts for Miniaturization: Crafted to minimize signal degradation, advanced substrates effortlessly facilitate the smooth transmission of electrical signals between components, ensuring the preservation of data integrity and accuracy.
Harmonious Manufacturing Integration: Seamlessly aligned with precise manufacturing processes such as photolithography and etching, these substrates become integral components of semiconductor fabrication workflows, streamlining the overall production process.
Incorporation of Leading-edge Materials: Often integrating state-of-the-art materials or undergoing purposeful modifications, these substrates dynamically evolve to enhance specific properties, effectively meeting the dynamic requirements of the semiconductor industry.
Facilitators of Technological Fusion: Serving as catalysts, these substrates enable the smooth integration of semiconductor devices with a diverse array of technologies, fostering breakthroughs in wireless communication, artificial intelligence, and sensor technologies.
In essence, the functions of advanced semiconductor substrates are diverse and pivotal, playing an indispensable role in fortifying, streamlining, and propelling semiconductor devices within the ever-evolving landscape of technology.
What Are the Different Types of Advance Semiconductor Substrate?
In the dynamic realm of advanced semiconductor substrates, a diverse ensemble of materials takes the spotlight, each intricately designed to meet the nuanced demands of semiconductor technology. This captivating array includes:
Silicon Substrates: Silicon, the cornerstone material, undergoes refined enhancements to seamlessly align with the dynamic requisites of contemporary semiconductor manufacturing.
Silicon-on-Insulator (SOI): Showcasing a sleek silicon layer on an insulating canvas, SOI substrates delicately fine-tune power consumption, propelling the overall performance of devices to unprecedented levels.
Gallium Arsenide (GaAs) Substrates: Inherent to high-frequency applications, GaAs substrates play a pivotal role in sculpting the landscape of RF devices and high-speed electronic circuits.
Silicon Carbide (SiC) Substrates: Acknowledged for exceptional thermal conductivity, SiC substrates carve a niche in high-power and high-temperature devices, such as power electronics and automotive components.
Sapphire Substrates: Unveiling commendable thermal and electrical insulation properties, sapphire substrates take center stage in the craftsmanship of LED manufacturing.
Germanium (Ge) Substrates: Reserved for specialized applications, Ge substrates emerge as key players in the evolution of infrared and photodetector devices.
Gallium Nitride (GaN) Substrates: Imperative in the realm of high-power and high-frequency electronic devices, GaN substrates seamlessly integrate into the fabric of power amplifiers and LED technologies.
Organic Substrates: Pioneering the frontier of flexible electronics, organic substrates unfold opportunities for lightweight and flexible designs, particularly in applications like flexible displays and sensors.
Copper Substrates: Spearheading advanced packaging technologies, copper substrates actively contribute to orchestrating heightened thermal performance, introducing a layer of sophistication to semiconductor designs.
Glass Substrates: Deployed strategically in specific applications, glass substrates assume an instrumental role in crafting transparent and flexible electronic devices.
This assortment of substrates, ranging from the stalwart foundation of silicon to the avant-garde of innovative materials, dynamically responds to the unique and evolving requirements across the semiconductor industry. The selection process becomes an intricate dance, considering the nuances of the intended application, the pursuit of specific performance attributes, and the perpetual evolution driven by the forefront of materials science advancements.
What is the Relationship Between Advance Semiconductor Substrate and IC Packaging?
The intricate relationship between advanced semiconductor substrates and IC (Integrated Circuit) packaging is akin to a well-orchestrated performance, harmonizing efficiency, reliability, and overall functionality in semiconductor devices. Let’s delve into the nuanced interplay of their roles:
Cornerstone Foundation: Advanced semiconductor substrates serve as the bedrock, laying the essential foundation for the creation of integrated circuits. Their influence extends beyond mere support, shaping the very essence of stability and structural integrity in the IC.
Nerve Center of Connectivity: Acting as the central hub for interconnecting diverse IC components, the substrate intricately weaves the pathways for electrical signals to traverse between the intricate elements of transistors, resistors, and other vital components within the circuit.
Thermal Virtuoso: The substrate material, with its thermal conductivity and purposeful design, assumes the role of a virtuoso in managing the heat generated during the dynamic operation of the IC. The artistry lies in efficient heat dissipation, a prerequisite for the seamless performance of semiconductor devices.
Championing Miniaturization: Advanced substrates actively champion the ongoing wave of IC miniaturization. Their versatility enables the integration of myriad components within the confines of a limited space, aligning seamlessly with the demands of contemporary semiconductor packaging.
Synchronized Technological Ballet: The substrate material and technology engage in a synchronized ballet, gracefully adapting to the unique demands of the IC design and chosen packaging technology. This choreography is essential for unlocking the full potential of performance.
Package-on-Package Choreography: In configurations like Package-on-Package (PoP), where multiple ICs are elegantly stacked, the substrate takes on the role of a choreographer, orchestrating the graceful integration and interconnection of these stacked components.
Materials Alchemy: Innovations in substrate materials, incorporating advanced composites or engineered elements, represent a form of alchemy. This evolution promises to enhance electrical and thermal properties, contributing to the elevated performance and reliability of the IC.
Guardian of Signal Sanctity: The substrate serves as the guardian, zealously preserving the sanctity of signal integrity. Its role involves minimizing signal loss and fostering an environment conducive to reducing interference, ensuring the precision and reliability of data transmission within the IC.
Embracing Technological Crescendos: Emerging packaging technologies, epitomized by the dynamic landscape of 3D IC packaging, leverage advanced substrates. This allows for the vertical stacking of multiple semiconductor dies, ushering in a crescendo of advancements in performance and density.
EMC Ballet: The substrate’s material and design actively participate in an EMC ballet, ensuring that the IC operates harmoniously, free from disruptions caused by r succumbing to electromagnetic interference.
In essence, the collaboration between advanced semiconductor substrates and IC packaging is a masterpiece in motion. The substrate provides the canvas upon which the intricate components of the IC perform, shaping the narrative of heat dissipatioon, miniaturization, signal integrity, and compatibility with avant-garde packaging technologies. This orchestrated dance ultimately defines the symphony of performance and reliability in the integrated circuit.
How Does Advance Semiconductor Substrate Differ from Traditional PCBs?
The tale of advanced semiconductor substrates and traditional PCBs (Printed Circuit Boards) unfolds as a narrative of divergence, where unique elements—materials, designs, and functional trajectories—contribute to the distinctive dance between the two. Let’s traverse the nuances of their differences:
Layered Mosaic:
Advanced Semiconductor Substrates: Unveiling a multilayered mosaic adorned with intricate designs, these substrates become the canvas for high-performance integrated circuits. Each layer is a stroke of precision, meticulously optimized to fulfill specific electrical and thermal prerequisites.
Traditional PCBs: Embracing the concept of multiple layers, traditional PCBs paint a mosaic with less complexity compared to their advanced counterparts. Their design caters to applications with a simpler electronic landscape.
Semiconductor Manufacturing Stage:
Advanced Semiconductor Substrates: Stepping into the spotlight of semiconductor manufacturing processes, these substrates become conductors orchestrating the precise placement and interconnection of semiconductor components.
Traditional PCBs: Playing a versatile role across electronic devices, traditional PCBs function as stages for mounting and connecting electronic components. However, their repertoire lacks the specialized finesse demanded by semiconductor manufacturing processes.
Applications Spectrum:
Advanced Semiconductor Substrates: Commanding attention in high-performance and niche applications—microprocessors, memory chips, high-frequency devices. Their performance takes the lead, steering cutting-edge technological advancements.
Traditional PCBs: Embracing versatility, traditional PCBs find a home in diverse electronic devices, from computers to household gadgets. They cater to applications where the demand for performance is not as exacting as that of advanced semiconductor substrates.
Performance Sonata:
Advanced Semiconductor Substrates: Engaging in a sonata of performance metrics—electrical conductivity, thermal dissipation, signal integrity. Their role sets the stage for the seamless performance of state-of-the-art semiconductor devices.
Traditional PCBs: Partaking in a more standard sonata, traditional PCBs meet generic electronic requirements, offering a cost-effective solution for a myriad of electronic applications. However, their performance may not reach the crescendo attained by their advanced counterparts.
Manufacturing Choreography:
Advanced Semiconductor Substrates: Crafted with precision through specialized processes—epitaxy, thin-film deposition, photolithography. These manufacturing moves are choreographed with the intricate steps of semiconductor fabrication.
Traditional PCBs: Following a well-established routine of processes—etching, drilling, soldering—standard steps in the electronic industry. Traditional PCB manufacturing lacks the specialized intricacies demanded by semiconductor fabrication.
In essence, the narrative unfolds uniquely for advanced semiconductor substrates and traditional PCBs. The former takes a leading role in pushing the boundaries of semiconductor technology, while the latter provides a versatile canvas for a broader spectrum of electronic applications with less demanding performance prerequisites.
What is the Structure and Production Technology of Advance Semiconductor Substrate?
The intricate structure and production technology of advanced semiconductor substrates unfold through a series of sophisticated processes, each contributing to the creation of high-performance semiconductor devices. Here’s a nuanced overview:
Structured Brilliance of Advanced Semiconductor Substrates:
Foundation Material:
Silicon (Si), the cornerstone material, boasts exceptional semiconductor properties, setting the stage for the substrate’s functionality.
Tailored applications might explore alternatives like silicon carbide (SiC) or gallium arsenide (GaAs), each offering distinct electrical and thermal characteristics.
Layered Symphony:
Advanced semiconductor substrates often feature multiple layers, meticulously designed to fulfill specific functions.
Epitaxial layers, cultivated through epitaxy, enhance structural and electrical properties.
Insulating layers strategically isolate components, preventing electrical interference.
Metallization Choreography:
Metal layers, delicately deposited, weave intricate interconnections between different components.
Advanced lithography techniques precisely pattern these metal layers, crafting pathways for electrical signals with finesse.
Dielectric Ballet:
Dielectric layers, like performers on a stage, insulate metal layers and components, guarding against short circuits.
Introducing low-k dielectric materials minimizes signal delays, amplifying overall performance.
Materials Mastery:
Tailoring materials with specific attributes, such as high thermal conductivity or low signal loss, amplifies the substrate’s capabilities.
Artistry in Production Technology:
Crystal Crafting:
Commencing with the cultivation of a high-quality single crystal, methods like the Czochralski process or the Float Zone method shape the foundation.
Wafer Waltz:
Precision cutting techniques transform the crystal into thin wafers, serving as the canvas for semiconductor manufacturing.
Epitaxial Elegance:
Epitaxial layers gracefully emerge on the wafer surface, enhancing its electrical prowess through methods like chemical vapor deposition (CVD) or molecular beam epitaxy (MBE).
Lithography Poetry:
Photolithography, akin to an artist’s brushstroke, meticulously patterns various layers on the substrate. Photoresist material dances with light to create intricate designs.
Deposition Drama:
Deposition techniques, such as physical vapor deposition (PVD) or chemical vapor deposition (CVD), bring forth metal layers, dielectric materials, and other elements onto the stage.
Etching Choreography:
Etching processes delicately remove unwanted material, sculpting the final structure of the substrate with precision.
Annealing Symphony:
Annealing processes, like a harmonious tune, optimize the crystal structure and properties of the materials, elevating the substrate’s overall performance.
Testing Odyssey:
Rigorous testing becomes the climax, ensuring the substrate’s quality and functionality. Electrical testing, defect inspections, and quality control measures shape the grand finale.
The production technology of advanced semiconductor substrates emerges as a symphony of precision manufacturing, avant-garde materials, and cutting-edge processes, all harmonizing to craft substrates tailored for the demands of high-performance semiconductor devices.
Frequently Asked Questions (FAQs):
How does it differ from traditional PCBs?
Advanced semiconductor substrates, unlike traditional PCBs, are tailored for high-performance contexts, involving intricate materials and manufacturing processes to meet semiconductor device requirements.
What roles do advanced semiconductor substrates fulfill?
They play a crucial role in facilitating seamless electrical signal transmission between semiconductor components, minimizing signal loss for accurate data transmission.
What are the types of advanced semiconductor substrates?
Types include silicon, silicon carbide (SiC), and gallium arsenide (GaAs), selected based on the specific demands of semiconductor applications.
How is the manufacturing process executed?
The process involves crystal growth, wafer preparation, epitaxy, lithography, material deposition, etching, annealing, and thorough testing to ensure precise structure and quality.
What’s the connection with IC packaging?
Advanced semiconductor substrates are closely connected with IC packaging, serving as the foundation for mounting and interconnecting semiconductor components.
Conclusion
In summary, advanced semiconductor substrates stand out as pioneers reshaping the semiconductor landscape. These intricately engineered materials, including silicon, silicon carbide (SiC), and gallium arsenide (GaAs), take the spotlight in shaping high-performance semiconductor devices. The ongoing evolution in manufacturing processes, driven by innovative materials and design methodologies, showcases a proactive response to the escalating demands for faster, more compact, and energy-efficient electronic devices.
Departing from traditional norms associated with conventional PCBs, advanced semiconductor substrates carve a distinctive path in the domain of high-performance applications. Their crucial role in facilitating seamless electrical signal transmission between semiconductor components, minimizing signal loss, and ensuring precise data transmission distinguishes them in the dynamic electronic landscape. The close synergy with IC packaging underscores their significance, influencing the mounting and interconnection of semiconductor components and thereby impacting the overall performance and reliability of integrated circuits.
As these substrates find diverse applications across electronic devices, spanning microprocessors to smartphones, computers, automotive systems, and IoT devices, their adaptability becomes increasingly evident. The industry’s unwavering commitment to innovation not only propels technological boundaries but also signifies a proactive approach in navigating the ever-evolving electronic terrain.
In essence, the narrative of advanced semiconductor substrates unfolds as a symphony of innovation, seamlessly blending precision manufacturing, avant-garde materials, and cutting-edge processes. This symphony encapsulates a dedication to progress, adaptability, and the relentless pursuit of excellence in the dynamic realm of semiconductor technology.