Ajimomoto Package Substrate Manufacturing. High speed material and Low CTE (Coefficient of Thermal Expansion). The Package Substrate CTE (Coefficient of Thermal Expansion) refers to the thermal expansion characteristics of the material used in the substrate of electronic packages. The substrate is a foundational component in electronic devices, providing a surface for mounting and interconnecting various electronic components, such as integrated circuits (ICs) and other microelectronic devices.
The CTE is a measure of how a material’s dimensions change with temperature variations. When electronic devices operate, they generate heat, leading to temperature fluctuations. If the materials in the package substrate have different CTE values, it can result in thermal stress, potentially causing mechanical failure or damage to the electronic components.
Ideally, the CTE of the package substrate material should be chosen to closely match the CTE of the other materials in the electronic device, such as the semiconductor chips and the packaging materials. This matching helps to minimize the thermal stresses and strains that can occur during temperature cycling. Common substrate materials include FR-4, BT, polyimide, ceramic, and others, each with its own CTE value.
In summary, the Package Substrate CTE is a critical consideration in electronic packaging design to ensure the reliability and longevity of electronic devices, especially in applications where temperature changes are frequent and significant.
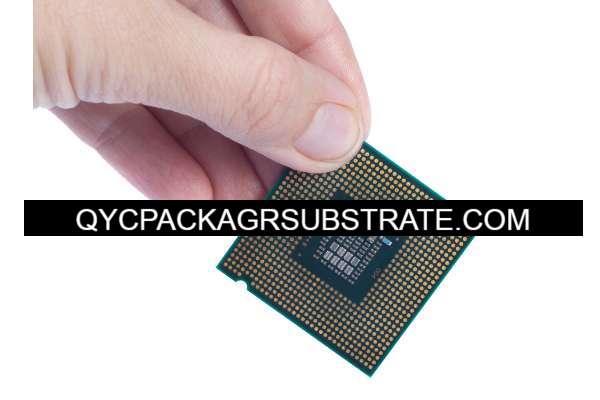
What are the Materials Used in a package substrate cte?
The coefficient of thermal expansion (CTE) is a crucial property in materials used for package substrates in electronic devices. Package substrates provide a foundation for mounting and interconnecting electronic components. The CTE is particularly important because electronic devices undergo temperature variations during operation, and materials with similar CTE values help prevent thermal stress and potential damage to the components.
Common materials used in package substrates and their approximate CTE values include:
- FR-4 (Flame Retardant-4):
-
- CTE: Around 13-18 ppm/°C
- Description: FR-4 is a type of epoxy-glass laminate widely used in printed circuit boards (PCBs). It’s a common substrate material due to its good electrical insulation properties and cost-effectiveness.
- BT (Bismaleimide Triazine):
-
- CTE: Typically around 2-4 ppm/°C
- Description: BT is a type of high-performance polymer often used in advanced package substrates. It has a lower CTE compared to FR-4, making it suitable for applications where precise dimensional stability is crucial.
- Polyimide:
-
- CTE: Varies, but typically in the range of 20-30 ppm/°C
- Description: Polyimide films are known for their high-temperature stability and flexibility. They are used in flexible circuits and as a substrate material for certain electronic packages.
- Ceramic Substrates:
-
- CTE: Varies depending on the specific ceramic material.
- Description: Ceramic materials, such as alumina (aluminum oxide) and aluminum nitride, are used in some advanced packaging applications. Ceramics generally have lower CTE values compared to organic materials.
- Copper (for Metal Core PCBs):
-
- CTE: Around 16-18 ppm/°C
- Description: Metal Core PCBs (MCPCBs) use a metal layer, often copper, as the substrate. The CTE of the metal layer is important for matching with the CTE of other materials in the system.
- Silicon (for Silicon Interposers):
- CTE: Similar to silicon, which is around 2.5 ppm/°C
- Description: Silicon interposers are used in advanced packaging technologies. Silicon’s low CTE helps in minimizing thermal stress.
What are the types of package substrate cte?
The types of package substrate materials, based on their coefficient of thermal expansion (CTE), can be broadly categorized into several groups. Here are some common types:
- Low CTE Materials:
-
- Description: These materials have low coefficients of thermal expansion, typically in the range of 2-4 ppm/°C. They are chosen for applications where precise dimensional stability is critical to avoid thermal stress. Examples include Bismaleimide Triazine (BT) and certain advanced polymers.
- Moderate CTE Materials:
-
- Description: Materials in this category have moderate coefficients of thermal expansion, typically ranging from 10-20 ppm/°C. FR-4 (Flame Retardant-4), a common epoxy-glass laminate, falls into this category. It offers a balance between dimensional stability and cost-effectiveness.
- High CTE Materials:
-
- Description: High CTE materials have coefficients of thermal expansion above 20 ppm/°C. Some polyimides and certain flexible substrates fall into this category. They may be chosen for specific applications where flexibility is a key requirement.
- Ceramic Substrates:
-
- Description: Ceramics, such as alumina (aluminum oxide) and aluminum nitride, have relatively low CTE values compared to organic materials. They are often used in advanced packaging where excellent thermal and mechanical properties are essential.
- Metal Core PCBs (MCPCBs):
-
- Description: MCPCBs use a metal layer, usually copper, as the substrate. Metals typically have higher CTE values (around 16-18 ppm/°C) compared to organic materials like FR-4. The choice of metal core is based on its specific thermal and electrical conductivity properties.
- Silicon and Semiconductor Materials:
- Description: Silicon, commonly used in semiconductor manufacturing, has a very low CTE (around 2.5 ppm/°C). Silicon is used in advanced packaging technologies, such as silicon interposers, where precise dimensional stability and compatibility with semiconductor materials are crucial.
The choice of package substrate material depends on the specific requirements of the electronic device, including thermal performance, cost considerations, and the need for dimensional stability. Engineers carefully select materials with CTE values that match well with other components in the system to minimize thermal stresses and enhance the overall reliability of the electronic package.
When is It Ideal to Use package substrate cte?
The Coefficient of Thermal Expansion (CTE) of a package substrate is a critical consideration in electronic packaging design, and its ideal use depends on specific application requirements. Here are scenarios where considering the Package Substrate CTE is particularly important:
- Temperature Fluctuations:
-
- Ideal Scenario: When electronic devices are exposed to significant temperature variations during operation. Matching the CTE of the package substrate with other materials, such as semiconductor chips and packaging materials, helps minimize thermal stress and potential damage.
- High-Performance Electronics:
-
- Ideal Scenario: In applications where precision and stability are crucial, such as high-performance computing, telecommunications, and aerospace. Maintaining dimensional stability under varying temperatures is essential for the reliable operation of sensitive electronic components.
- Thermal Cycling Environments:
-
- Ideal Scenario: When the electronic device is expected to experience frequent thermal cycling, such as in automotive applications or certain industrial settings. A well-matched CTE helps prevent mechanical failures caused by repeated thermal stress.
- Miniaturized Devices:
-
- Ideal Scenario: In miniaturized electronic devices where space is limited. Controlling thermal expansion becomes more critical in smaller devices, and selecting a substrate with an appropriate CTE is essential for maintaining the integrity of the device.
- High-Frequency Applications:
-
- Ideal Scenario: In high-frequency applications, such as RF (Radio Frequency) and microwave circuits. Maintaining stable electrical properties under varying temperatures is crucial for signal integrity, making CTE matching important.
- Reliability-Critical Applications:
-
- Ideal Scenario: In applications where reliability is paramount, such as medical devices, aerospace systems, and automotive electronics. Matching CTE helps ensure the long-term reliability and performance of electronic components.
- Flexible and Rigid-Flex PCBs:
- Ideal Scenario: In flexible and rigid-flex PCB designs where the substrate experiences bending or flexing. The CTE of the substrate should be chosen to accommodate the mechanical stresses associated with flexing without compromising electrical performance.
It’s important to note that the ideal use of package substrate CTE is highly application-dependent. Designers and engineers must carefully consider the specific thermal and mechanical requirements of the electronic system to choose a package substrate with a CTE that complements other materials in the assembly. This consideration contributes to the overall reliability and longevity of the electronic device.
How is a package substrate cte Manufactured?
The manufacturing process of a package substrate, with a focus on the Coefficient of Thermal Expansion (CTE), involves several key steps. Keep in mind that the specific details can vary based on the type of substrate material (organic or ceramic) and the technology used by the manufacturer. Here is a general overview:
- Material Selection:
-
- Organic Substrates: If using an organic substrate like FR-4, the material is typically pre-preg (pre-impregnated) fiberglass sheets with epoxy resin. For ceramic substrates, materials like alumina or aluminum nitride are chosen.
- Layer Formation:
-
- Organic Substrates: Layers are built up using pre-preg sheets. These layers are stacked and pressed together.
- Ceramic Substrates: Layers may be formed through processes like tape casting or screen printing, depending on the specific ceramic material.
- Curing:
-
- Organic Substrates: The layers are cured in an oven to harden the epoxy resin and create a solid substrate.
- Ceramic Substrates: For ceramics, the layers may undergo a sintering process at high temperatures to fuse the particles and create a solid structure.
- Drilling and Imaging:
-
- Via Formation: Holes (vias) are drilled through the substrate to connect different layers. Laser drilling is common for precise drilling.
- Imaging: A photosensitive material is applied, and a UV light is used to transfer the circuit pattern onto the substrate.
- Metallization:
-
- Thin Film Deposition: A thin layer of conductive metal (usually copper) is deposited onto the substrate through techniques like sputtering or electroplating.
- Pattern Formation: Photolithography or etching is used to define the circuit pattern on the metal layer.
- Surface Finish:
-
- Surface Treatment: The substrate may undergo surface treatments to enhance solderability, prevent oxidation, and improve overall reliability.
- Quality Control:
-
- Testing: Various tests, including electrical testing, thermal cycling, and visual inspections, are conducted to ensure the quality and reliability of the substrate.
- Assembly (if applicable):
-
- Component Attachment: In some cases, electronic components may be attached to the substrate. This can include soldering or other bonding techniques.
- Final Inspection and Packaging:
- Quality Assurance: The final substrates undergo thorough inspection to ensure they meet the specified requirements.
- Packaging: The substrates are packaged and prepared for shipment.
Where to Find package substrate cte?
To find information about package substrate CTE (Coefficient of Thermal Expansion) or to source package substrates with specific CTE requirements, you can explore the following avenues:
- Visit QYC CO., LTD Website:
-
- Start by visiting the official website of QYC CO., LTD. Company websites often provide detailed information about their products, services, and capabilities.
- Search on Industry Directories:
-
- Explore industry directories or online platforms that list electronics and PCB (Printed Circuit Board) manufacturers. QYC CO., LTD may be listed along with details about their specialization, including package substrate CTE.
- Contact QYC CO., LTD Directly:
-
- Use the contact information provided on their official website to reach out to QYC CO., LTD directly. This could include emailing their customer support or using any provided contact forms.
- Collaborate with Electronic Component Distributors:
-
- Electronic component distributors may have partnerships with PCB manufacturers like QYC CO., LTD. Check with distributors to see if they can provide information or facilitate communication.
- Explore Online PCB Marketplaces:
- Online marketplaces connecting buyers with PCB manufacturers may list QYC CO., LTD. Explore these platforms to learn more about their offerings and potentially connect with them.
Remember to verify the information obtained and consider factors such as the company’s reputation, customer reviews, and their ability to meet specific requirements related to package substrate CTE.