Ajinomoto Package Substrate Manufacturer. the Package Substrate will be made with Showa Denko and Ajinomoto High speed materials.or other types high speed materials and high frequency materials.
“Organic Package Substrates” are organic boards utilized in the packaging of integrated circuits (ICs). In the realm of electronic device manufacturing, ICs need to be enclosed for protection and interconnection purposes. These substrates are fashioned from organic polymers, such as epoxy resin or polyimide.
The significance of organic package substrates lies in their pivotal role during IC packaging, furnishing electrical connections, managing heat, and providing mechanical support. Typically, these substrates boast a multi-layered structure encompassing conductive layers, insulating layers, and through-holes facilitating the connection of IC chips with other components. By opting for organic materials, manufacturers can achieve cost-effectiveness and enhance production efficiency.
The design and material choices for organic package substrates are critical factors influencing the performance and reliability of electronic devices. These substrates may exhibit varying layer thicknesses, conductivity levels, and thermal properties to cater to diverse application needs. In high-performance scenarios, sophisticated techniques like multilayer film stacking and metal-filled through-holes may be employed to meet stringent performance and density requirements.
To sum up, organic package substrates assume a crucial role in the contemporary electronics industry, providing essential support and connectivity for ICs. They strike a balance by keeping costs relatively low while meeting the varied demands of different applications.
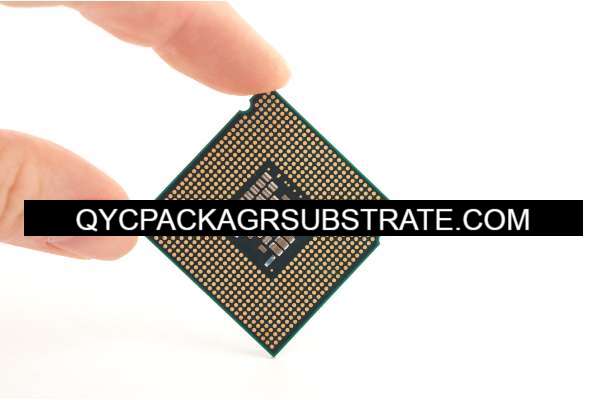
What is the function of Organic Package Substrates?
Organic Package Substrates function as the backbone in the intricate world of integrated circuit (IC) packaging, orchestrating a symphony of roles to enhance the performance and robustness of electronic devices. Here’s a glimpse into their diverse functionalities:
Conducting Electrical Symphony: Serving as vital pathways for electrical connectivity, Organic Package Substrates form the intricate network that facilitates seamless communication between the integrated circuit and other components in the electronic ensemble.
Architects of Structural Resilience: As stalwart architects of electronic assemblies, these substrates provide indispensable structural support. This support is akin to a silent guardian, shielding the system from the rigors of mechanical stresses and vibrations, ensuring a sustained and harmonious operation.
Masters of Thermal Choreography: Organic Package Substrates take on the role of choreographers in the thermal ballet, skillfully managing and dissipating the heat generated during the integrated circuit’s performance. This dance of thermal regulation prevents overheating, preserving the graceful rhythm of reliable electronic functionality.
Artisans of Interconnection Tapestry: With their intricate through-holes and vias, these substrates craft a rich tapestry of interconnections between different layers. This craftsmanship allows for the seamless integration and harmonious interplay of diverse elements within the IC package.
Guardians of Protective Enchantment: Contributing to the magic of encapsulation, Organic Package Substrates weave a protective enchantment around the integrated circuit. This shield wards off external elements, be they moisture, dust, or contaminants, preserving the mystical integrity and functionality of the IC.
Custodians of Signal Purity: The design and composition of these substrates act as custodians of signal purity. They provide a stable and reliable stage for electrical connections, ensuring the transmission of pristine signals and minimizing interference, thereby maintaining the clarity of communication within the electronic ensemble.
In essence, Organic Package Substrates emerge as the virtuosos of IC packaging, harmonizing a symphony of functions that collectively elevate the efficiency, reliability, and endurance of electronic devices.
What are the different types of Organic Package Substrates?
A spectrum of Organic Package Substrates caters to the nuanced needs within the domain of integrated circuit (IC) packaging. Let’s delve into the distinct varieties:
Printed Circuit Boards (PCBs): As the bedrock of electronic assemblies, PCBs meld copper traces onto an organic substrate, often fashioned from materials like FR-4 epoxy resin.
Flexible Printed Circuit (FPC): Embracing adaptability, FPCs bring flexibility to the forefront, serving applications where traditional rigid PCBs fall short. This type finds resonance in the world of flexible and bendable electronic devices, such as the ever-evolving landscape of wearables.
Chip-on-Board (COB): In a dance of efficiency, COB packaging directly mounts the IC onto the substrate, presenting a spatially economic solution. Organic materials like epoxy or polyimide often take center stage in the composition of COB configurations.
System-in-Package (SiP): Orchestrating a convergence of multiple ICs into a cohesive package, SiP employs a substrate, typically organic, infused with technologies like flip-chip bonding or wire bonding, weaving a tapestry of compact multi-IC solutions.
Organic Interposers: As mediators in the symphony of semiconductor components, organic interposers facilitate high-density interconnections. They play an instrumental role in advanced packaging technologies, including the three-dimensional realms of 2.5D and 3D IC integration.
High-Density Interconnect (HDI) PCBs: Engineered for prowess, HDI PCBs unveil intricate designs with multiple layers and high-density interconnection technologies, finding their stage in systems craving the marriage of compactness and superior electrical characteristics.
Rigid-Flex PCBs: Navigating the spectrum between rigidity and flexibility, Rigid-Flex PCBs masterfully blend the attributes of both substrates, opening the curtain to the creation of intricate three-dimensional electronic ensembles.
Ceramic-Organic Hybrids: In a harmonious fusion, these hybrids amalgamate ceramic and organic materials, elevating thermal performance and electrical characteristics to meet the nuanced demands of diverse electronic applications.
The selection of Organic Package Substrate becomes a meticulous orchestration, considering the application’s unique cadence, flexibility prerequisites, thermal dynamics, and the desired integration levels within the symphony of the electronic system. The dynamic evolution of technology continually introduces new players to the stage, expanding the repertoire of substrate types to harmonize with the ever-evolving demands of the electronics industry.
How are Organic Package Substrates related to IC packaging?
Organic Package Substrates are indispensable companions in the intricate dance of integrated circuit (IC) packaging. Their relationship with IC packaging is profound, encapsulating various key dimensions:
Architects of Structure: At the core, Organic Package Substrates serve as the architectural foundation for IC packaging. They provide the canvas upon which the integrated circuit components, from chips to additional elements, find their place in a coherent structure.
Electrically Charged Network: Embedded within these substrates are conductive pathways that form an electrically charged network. This network facilitates the seamless flow of electric currents between the IC and the array of components, establishing the vital electrical connections essential for device functionality.
Thermal Maestros: Acting as thermal maestros, Organic Package Substrates are instrumental in orchestrating the management of heat generated by the IC. Their design allows for the efficient dissipation of heat, preventing overheating and harmonizing the symphony of reliable and enduring IC performance.
Guardians of Encapsulation: Beyond their structural role, these substrates take on the role of guardians, encapsulating the IC within a protective cocoon. This shielding mechanism shields the delicate IC from the external elements, ensuring a resilient and enduring performance against the onslaught of moisture, dust, and contaminants.
Interconnectivity Artisans: Featuring through-holes, vias, and other interconnection technologies, Organic Package Substrates become artisans of interconnectivity. They enable the creation of intricate connections, forming the backbone of the interwoven electronic tapestry within the IC package.
Pioneers in Advanced Technologies: In the era of advanced packaging, such as System-in-Package (SiP), these substrates become pioneers. They facilitate the convergence of multiple ICs into a cohesive unit, unlocking the potential for compact and space-efficient solutions in the dynamic landscape of electronic devices.
Versatility Virtuosos: Depending on their type, whether Flexible Printed Circuit (FPC) or Rigid-Flex PCB, Organic Package Substrates showcase versatility. They adapt to the unique demands of applications, offering flexibility or a blend of rigidity and flexibility to accommodate diverse design requirements.
In essence, the synergy between Organic Package Substrates and IC packaging is profound. These substrates are not mere supporters; they are conductors, guardians, and architects, shaping the very essence of IC functionality, reliability, and longevity. The meticulous consideration of Organic Package Substrates becomes a linchpin in the intricate ballet of IC packaging.
How do Organic Package Substrates differ from traditional PCBs?
Organic Package Substrates and traditional Printed Circuit Boards (PCBs) traverse parallel paths in electronics, yet diverge in design intricacies, core functions, and application scopes. Let’s navigate the distinctions that set them apart:
Strategic Focus:
Organic Package Substrates: Take the spotlight in the artistry of integrated circuit (IC) packaging. Their focus lies in delivering structural prowess, refined interconnections, and cutting-edge features finely tuned for the demands of compact and high-performance electronic devices.
Traditional PCBs: Form the backbone of electronic systems with a broader canvas. They cater to a diverse range of electronic components, extending beyond ICs. Their mission is to weave a tapestry of electrical connections across various applications.
Adaptability and Integration:
Organic Package Substrates: Exhibit a spectrum of adaptability with multiple layers, intricate traces, and advanced interconnection technologies. Their design finesse aligns with the specific needs and nuances of modern ICs.
Traditional PCBs: Embrace versatility with complexity varying based on application needs. While some embrace sophistication, others maintain simplicity, serving a multitude of electronic applications.
Layering and Complexity Ballet:
Organic Package Substrates: Grace the stage of IC packaging with layers, fine traces, and intricate interconnections, orchestrating a ballet of complexity to meet the demands of contemporary electronic devices.
Traditional PCBs: Partake in a dance of complexity, with High-Density Interconnect (HDI) PCBs approaching the finesse of Organic Package Substrates, while standard PCBs may follow simpler choreography suited for less demanding applications.
Flexibility Flourish:
Organic Package Substrates: Showcase flexibility prowess through types like Flexible Printed Circuits (FPC) or Rigid-Flex PCBs. They embrace the dance of flexibility, catering to designs demanding bends and twists.
Traditional PCBs: Transition from rigidity to flexibility with variations like flexible and rigid-flex PCBs. While not specialized for extreme flexibility, they join the ensemble, offering adaptability when needed.
Packaging Technology Stance:
Organic Package Substrates: Often feature in the avant-garde of packaging technologies, embracing System-in-Package (SiP) and 3D IC integration. Their narrative revolves around the integration of multiple ICs into a single, compact masterpiece.
Traditional PCBs: Versatile in adopting advanced technologies, yet not specifically tailored for the intricate packaging demands associated with housing multiple ICs in confined spaces.
In essence, Organic Package Substrates take center stage as artisans of IC packaging, finely tuned for the demands of contemporary electronics. Traditional PCBs, with their versatile repertoire, contribute to the broader symphony of electronic applications, accommodating a spectrum of designs and functionalities.
What is the main structure and production technology of Organic Package Substrates?
The essence of Organic Package Substrates lies in a versatile structure meticulously crafted through a series of production techniques. Let’s embark on a journey through their main structural elements and the intricacies of the production process:
Structural Composition:
Foundation Material:
At its core, Organic Package Substrates rest upon an organic canvas. Materials like epoxy resins or polyimides form the foundational layer, providing stability and electrical insulation.
Conductive Tapestry:
Woven into the substrate are multiple layers of conductive brilliance. Thin films of copper or other conductive metals create a intricate tapestry, forming pathways for electrical connectivity within the substrate.
Insulating Harmony:
Interlaced with the conductive layers are dielectric elements, creating a harmonious balance. These layers act as insulators, safeguarding the conductive traces and ensuring the dependability of electrical connections.
Vertical Connectivity Threads:
Through-holes or vias are strategically positioned, creating vertical threads that pierce through multiple layers. These threads enable three-dimensional interconnections, contributing to the substrate’s depth and complexity.
Surface Finishing Touch:
The substrate’s surface undergoes a finishing touch, donning a solder mask for insulation and receiving surface finishes like tin or gold. This not only enhances solderability but also serves as a shield against oxidation.
Production Symphony:
Lamination Ballet:
The production dance commences with lamination, where layers of substrate material, conductive brilliance, and insulating harmony are gracefully pressed together under the embrace of heat and pressure. This symphony creates a unified, multilayered masterpiece.
Copper Choreography:
Thin layers of copper foil pirouette onto the substrate, ready to take center stage. Through an intricate dance of photolithography and etching, the copper layers are patterned to unveil the desired circuitry.
Drilling and Plating Rhythms:
Drills come alive, carving through the substrate to create through-holes or vias. These cavities are plated with conductive allure, orchestrating electrical connections that bridge different layers.
Solder Mask Elegance:
A layer of solder mask is applied with elegance, providing insulation and protection to the conductive traces. This not only shields the substrate but also imparts a distinctive hue, aiding in functional identification.
Surface Finale:
The grand finale features the application of a surface finish, a touch of tin, lead-free solder, or gold. This not only adds a final stroke to the aesthetic but also enhances the substrate’s solderability and guards against the passage of time.
Quality Sonata:
The production crescendo culminates in a quality sonata. Rigorous testing and inspection measures ensure that the completed substrate harmonizes with specifications for electrical connectivity, insulation, and overall reliability.
In essence, the symphony of Organic Package Substrates is composed of intricate layers and a production ballet that transforms raw materials into a masterpiece tailored for the nuanced demands of integrated circuit packaging.
Frequently Asked Questions (FAQs)
Unpacking Organic Package Substrates: What Are They Made Of?
Organic Package Substrates are composed of materials, often derived from organic compounds like epoxy resins or polyimides. These materials serve as the fundamental platform for mounting and interconnecting ICs, ensuring the reliability and functionality of electronic devices.
Can You Walk Us Through the Production Choreography of Organic Package Substrates?
The production journey involves a series of meticulous steps, from lamination and copper cladding to drilling, plating, solder mask application, and surface finishing. This symphony of processes results in the creation of multilayered substrates with the necessary features for IC integration.
What Should Guide the Selection of an Organic Package Manufacturer?
Critical considerations include the manufacturer’s industry experience, reputation, technological prowess, production capabilities, and commitment to quality standards. Compatibility with specific project requirements is paramount for a fruitful collaboration.
In Which Electronic Orchestrations Do Organic Package Substrates Play a Role?
Organic Package Substrates take center stage in various electronic devices, including smartphones, tablets, computers, automotive electronics, and medical devices. Their versatility enables the construction of compact and reliable electronic assemblies.
How Can Interested Parties Engage with an Organic Package Manufacturer?
Direct engagement can be initiated through the manufacturer’s website, customer service channels, or dedicated business contacts. Providing detailed project requirements facilitates accurate quoting and opens avenues for collaboration.
What Trends Shape the Landscape of Organic Package Manufacturing?
Emerging trends include advancements in packaging technologies like System-in-Package and 3D IC integration, a growing emphasis on miniaturization, increased utilization of flexible substrates, and a focus on materials with enhanced thermal and electrical properties.
Do Organic Package Substrates Align with Lead-Free Manufacturing Processes?
Yes, many Organic Package Substrates are designed to align with lead-free manufacturing processes, adhering to environmental regulations and industry standards such as RoHS (Restriction of Hazardous Substances).
Conclusion
To sum it up, the universe of Organic Package Substrates and the artisans behind their creation stands as a pivotal domain in the intricate realm of integrated circuit packaging. These specialized entities wield substantial influence, sculpting substrates that lay the groundwork for mounting and interconnecting electronic components, particularly the indispensable integrated circuits (ICs). Through a systematic journey of production involving lamination, copper cladding, drilling, plating, and the final embellishments, these manufacturers choreograph the emergence of multilayered substrates adorned with intricate electrical pathways and protective layers.
The spectrum of substrate types, ranging from Printed Circuit Boards (PCBs), Flexible Printed Circuits (FPC), Chip-on-Board (COB), System-in-Package (SiP), to Organic Interposers, High-Density Interconnect (HDI) PCBs, and Rigid-Flex PCBs, underscores the adaptability and versatility required to meet the diverse demands of contemporary electronic applications.
Selecting an Organic Package Manufacturer involves a nuanced evaluation of experience, reputation, technological acumen, and a steadfast commitment to rigorous quality standards. The initiation of collaboration with these manufacturers unfolds through their digital portals or designated business contacts, where the articulation of intricate project requirements sets the stage for precise quoting and potentially fruitful alliances.
The burgeoning emphasis on environmental consciousness is becoming an integral thread in the fabric of manufacturing practices, with a focus on the adoption of eco-friendly materials and sustainable processes. The ripples of emerging trends, including strides in packaging technologies, the pursuit of miniaturization, and the incorporation of flexible substrates, shape the future trajectory of this industry.
As Organic Package Substrates persist in their central role within electronic devices such as smartphones, tablets, computers, and medical apparatus, the manufacturers navigate the delicate interplay between technological ingenuity and environmental stewardship. Essentially, they contribute to the symphony of modern electronics, providing the structural and functional harmonies requisite for the seamless integration of advanced electronic components.