Alumina PCB |Al2O3 PCB Manufacturer
Alumina PCB |Al2O3 PCB Manufacturer. We offer Ceramic Alumina Al2O3 PCB, ALN Ceramic PCBs from 1 layer to 30 layers. We also produce Ceramic BGA substrates with small trace and gap.
Alumina PCBs, also known as alumina ceramic printed circuit boards, represent the pinnacle of advanced electronic substrate technology. Crafted from high-purity alumina ceramic material, these PCBs offer a blend of exceptional properties essential for demanding electronic applications. Their standout feature is the remarkable thermal conductivity, allowing efficient dissipation of heat generated by high-power components. This trait makes them indispensable in industries requiring robust thermal management, such as power electronics and LED lighting. Moreover, Alumina PCBs boast excellent electrical insulation properties, ensuring reliable performance even in high-voltage environments. Their mechanical strength and resistance to temperature extremes further enhance their suitability for aerospace, automotive, and industrial applications. With customizable options available in terms of size, thickness, and surface finishes, Alumina PCBs offer versatility to cater to diverse electronic designs. From power amplifiers to RF circuits, Alumina PCBs exemplify innovation and reliability in modern electronics.
What is an Alumina PCB?
An alumina PCB, or alumina ceramic printed circuit board, is a type of circuit board made from alumina ceramic material. Alumina (Al2O3) is a ceramic material known for its excellent electrical insulation properties, high thermal conductivity, and mechanical strength.
Alumina PCBs are often used in high-power and high-frequency electronic applications where efficient heat dissipation is crucial. They are particularly well-suited for applications such as power amplifiers, LED modules, high-frequency RF circuits, and other electronics that require reliable performance under demanding conditions.
The manufacturing process of alumina PCBs involves printing conductive traces onto the alumina substrate, similar to traditional PCB fabrication methods. However, alumina PCBs offer superior thermal management compared to standard FR4 boards, making them ideal for applications where heat dissipation is a concern.
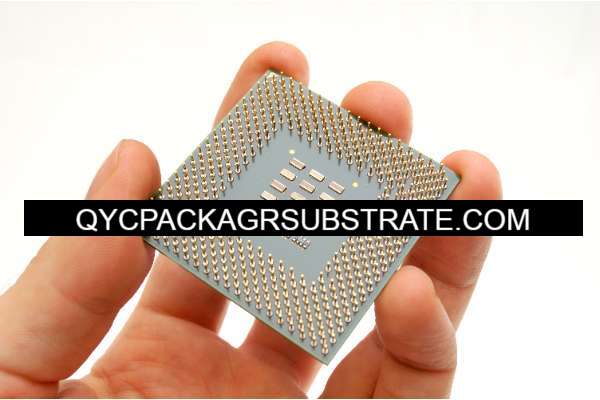
Alumina PCB |Al2O3 PCB Manufacturer
What are Alumina PCB Design Guidelines?
Designing with alumina PCBs requires attention to specific guidelines to ensure optimal performance and reliability. Here are some key design guidelines:
- Thermal Management: Alumina PCBs are prized for their excellent thermal conductivity. To maximize this advantage, ensure that heat-generating components are properly placed to allow efficient dissipation. Additionally, consider adding thermal vias or other cooling mechanisms to enhance heat transfer away from critical components.
- Material Selection: Choose the appropriate grade and thickness of alumina substrate based on the specific requirements of your application. Higher purity alumina substrates generally offer better electrical insulation properties and thermal conductivity.
- Trace Width and Spacing: Follow standard PCB design practices for determining trace width and spacing to accommodate the required current carrying capacity and electrical insulation requirements. Alumina PCBs typically allow for narrower trace widths due to their excellent dielectric properties.
- Component Placement: Carefully position components on the PCB to minimize signal interference and maximize thermal performance. Consider the placement of high-power components and heat sinks to optimize heat dissipation.
- Via Design: Use vias strategically to route traces between layers and to enhance thermal conductivity. Thermal vias can help to dissipate heat from hotspots on the PCB and improve overall thermal management.
- Copper Thickness: Select an appropriate copper thickness for the conductive traces based on the current carrying capacity and thermal requirements of the circuit. Thicker copper layers can provide lower resistance and better heat dissipation.
- Dielectric Constant: Be aware of the dielectric constant of the alumina substrate material, as it can affect the impedance and propagation characteristics of high-frequency signals. Design traces and transmission lines accordingly to minimize signal degradation.
- Mechanical Considerations: Alumina PCBs offer good mechanical strength, but they can still be brittle compared to some other materials. Consider mechanical stresses during assembly and operation to prevent mechanical failures.
- Environmental Considerations: Alumina PCBs are generally more resistant to moisture and chemicals compared to standard FR4 boards. However, consider environmental factors such as temperature extremes and exposure to corrosive substances when designing for long-term reliability.
By following these guidelines, you can design alumina PCBs that meet the performance, reliability, and thermal management requirements of your specific application.
What is the Alumina PCB Fabrication Process?
The fabrication process for alumina PCBs involves several steps, including substrate preparation, circuit design, printing, etching, and finishing. Here’s a general overview of the typical fabrication process:
- Substrate Preparation: The process begins with the preparation of alumina ceramic substrates. These substrates are typically made from high-purity alumina (Al2O3) material. The substrates are cut to the desired size and shape, and any surface imperfections are smoothed out.
- Circuit Design: Once the substrates are prepared, the circuit design is created using computer-aided design (CAD) software. The design includes the layout of conductive traces, vias, pads, and other components according to the specifications of the electronic circuit.
- Printing: The circuit design is transferred onto the alumina substrate using a printing process. This can be done using various methods, including screen printing, inkjet printing, or photolithography. Conductive ink or paste containing metals such as silver, gold, or copper is used to create the conductive traces and pads on the substrate.
- Curing: After printing, the substrate is cured to solidify the conductive traces and pads. This typically involves heating the substrate to a specific temperature for a certain period to promote adhesion and conductivity.
- Etching: In this step, any excess conductive material that is not part of the desired circuit pattern is removed through etching. Chemical etchants are applied to dissolve the unwanted material, leaving behind the desired conductive traces and pads.
- Surface Finishing: Once the etching process is complete, the surface of the alumina PCB may undergo additional finishing processes to improve its performance and reliability. This can include applying protective coatings, such as solder mask or conformal coating, to prevent oxidation and moisture ingress.
- Drilling and Vias: Holes are drilled into the substrate to create vias, which are used to establish connections between different layers of the PCB. The vias are then filled with conductive material to ensure electrical continuity throughout the board.
- Final Inspection:The fabricated alumina PCB undergoes rigorous inspection to ensure that it meets the required specifications and quality standards. This may include electrical testing, visual inspection, and dimensional measurements.
- Assembly: Once the PCBs pass inspection, they are ready for component assembly. Electronic components such as resistors, capacitors, integrated circuits, and connectors are soldered onto the PCB to complete the electronic assembly.
By following these steps, manufacturers can produce high-quality alumina PCBs suitable for a wide range of electronic applications.
How do you manufacture an Alumina PCB?
Manufacturing alumina PCBs involves several steps, each crucial for achieving high-quality, reliable circuit boards. Here’s a detailed overview of the manufacturing process:
- Substrate Preparation:
– Start with high-purity alumina ceramic material.
– Cut the alumina substrate into the desired size and shape using precision machining techniques.
– Smooth out the substrate surface to remove any imperfections and ensure uniformity.
- Circuit Design:
– Use computer-aided design (CAD) software to create the circuit layout based on the specific requirements of the electronic device.
– Design the placement of components, traces, pads, and vias on the substrate.
- Printing:
– Transfer the circuit design onto the alumina substrate using printing techniques such as screen printing, inkjet printing, or photolithography.
– Use conductive ink or paste containing metals like silver, gold, or copper to create the conductive traces, pads, and components on the substrate.
- Curing:
– Cure the printed substrate by heating it to a specific temperature for a set duration. This process solidifies the conductive material, ensuring proper adhesion and conductivity.
- Etching:
– Remove any excess conductive material that is not part of the desired circuit pattern through chemical etching.
– Apply etchants to dissolve the unwanted material, leaving behind the desired conductive traces, pads, and components.
- Surface Finishing:
– Apply surface finishes to improve the performance and reliability of the alumina PCB.
– Options include solder mask application to protect exposed copper traces, and applying conformal coatings to protect against environmental factors like moisture and corrosion.
- Drilling and Vias:
– Drill holes into the substrate to create vias, which establish connections between different layers of the PCB.
– Fill the vias with conductive material to ensure electrical continuity between layers.
- Final Inspection:
– Conduct rigorous inspection of the fabricated alumina PCB to verify that it meets quality standards.
– Perform electrical testing, visual inspection, and dimensional measurements to ensure proper functionality and accuracy.
- Assembly:
– Once the PCBs pass inspection, proceed with component assembly.
– Solder electronic components onto the PCB, including resistors, capacitors, integrated circuits, and connectors, to complete the assembly process.
- Testing and Quality Assurance:
– Conduct comprehensive testing to verify the functionality, reliability, and performance of the assembled alumina PCBs.
– Address any issues identified during testing and ensure that the final products meet or exceed customer requirements and industry standards.
By following these steps meticulously, manufacturers can produce high-quality alumina PCBs suitable for a wide range of electronic applications, including those requiring high thermal conductivity and excellent electrical insulation properties.
How much should an Alumina PCB cost?
The cost of an alumina PCB can vary significantly depending on several factors, including the size, complexity, material specifications, manufacturing processes involved, and the quantity ordered. Here are some key factors that can influence the cost:
- Size and Complexity: Larger PCBs with complex circuitry require more material and manufacturing time, leading to higher costs.
- Material Specifications: The cost of alumina ceramic material can vary based on factors such as purity, thickness, and special features like surface finishes or dielectric properties.
- Manufacturing Processes: Different manufacturing processes, such as printing, etching, drilling, and surface finishing, incur different costs based on equipment, labor, and material usage.
- Quantity: Bulk orders typically result in lower per-unit costs due to economies of scale. Ordering larger quantities may lead to volume discounts from PCB manufacturers.
- Additional Features: Special features such as impedance control, blind/buried vias, controlled depth drilling, and tight tolerances can increase the cost of alumina PCBs.
- Quality Standards: Compliance with specific quality standards or certifications may add to the overall cost of manufacturing.
- Supplier and Location: PCB suppliers located in regions with lower labor costs or offering competitive pricing may provide cost advantages.
As a rough estimate, the cost of a basic alumina PCB can range from a few dollars for simple prototypes to several hundred dollars for complex, high-quality production units. For a more accurate cost estimate, it’s best to consult with PCB manufacturers or suppliers, providing them with detailed specifications and requirements for your project. They can provide quotes based on your specific needs and volume requirements.
What is Alumina PCB base material?
The base material of an alumina PCB is alumina ceramic, also known as aluminum oxide (Al2O3). Alumina ceramic is a versatile material prized for its excellent electrical insulation properties, high thermal conductivity, mechanical strength, and resistance to high temperatures.
Alumina PCBs are made using alumina ceramic substrates as the foundation upon which the electronic circuitry is built. These substrates are typically manufactured from high-purity alumina powder, which is formed into sheets and sintered at high temperatures to achieve the desired mechanical and electrical properties.
Alumina ceramic substrates provide several advantages for PCB applications, including:
- Electrical Insulation: Alumina ceramic has high electrical insulation properties, making it suitable for use in circuits where preventing electrical leakage or short circuits is essential.
- Thermal Conductivity: Alumina ceramic exhibits excellent thermal conductivity, allowing for efficient dissipation of heat generated by electronic components. This property is particularly advantageous in high-power and high-frequency applications.
- Mechanical Strength: Alumina ceramic substrates offer good mechanical strength and dimensional stability, providing robust support for electronic components and ensuring the reliability of the PCB.
- Chemical Resistance: Alumina ceramic is resistant to many chemicals and environmental factors, making alumina PCBs suitable for use in harsh operating conditions.
Overall, alumina ceramic serves as an ideal base material for PCBs in applications that require high thermal performance, electrical insulation, and reliability.
Which company makes Alumina PCBs?
Many companies produce Alumina PCBs, some well-known manufacturers include Rogers Corporation from the United States, CeramTec from Germany, and NGK Insulators from Japan. These companies are renowned for their high-quality products and advanced manufacturing technologies, providing reliable Alumina PCB solutions for various electronic applications.
At our company, we are also one of the manufacturers of Alumina PCBs. We have advanced production equipment and an experienced technical team capable of providing high-quality, customized Alumina PCB products. Our manufacturing process strictly adheres to international standards and employs the most advanced techniques and technologies to ensure that the quality and performance of our products meet our customers’ requirements.
As a professional Alumina PCB manufacturer, our advantages include:
- Customization Capability:We can provide customized Alumina PCB solutions tailored to our customers’ specific requirements, including different sizes, thicknesses, layers, materials, and surface treatments.
- Quality Assurance:We strictly control every aspect of the production process, from material procurement to final product inspection, ensuring that each Alumina PCB meets high-quality standards.
- Fast Delivery: With efficient production capacity and flexible production planning, we can meet our customers’ order requirements promptly and ensure on-time delivery.
- Technical Support: Our technical team has extensive experience and expertise in Alumina PCB design, manufacturing, and application, providing comprehensive technical support and solutions.
Whether it’s for power electronics, high-frequency electronics, LED lighting, or other applications, we can provide our customers with high-quality Alumina PCB products and services. We are committed to establishing long-term cooperative relationships with our customers, driving innovation and development in the electronics industry together.
What are the 7 qualities of good customer service?
Good customer service is characterized by several key qualities that contribute to positive interactions and experiences for customers. Here are seven qualities of good customer service:
- Responsiveness: Good customer service involves being prompt and responsive to customer inquiries, concerns, and requests. Customers appreciate timely assistance and solutions to their problems.
- Empathy: Empathy is essential in understanding and relating to customers’ needs and emotions. Customer service representatives who demonstrate empathy can build rapport, show genuine concern, and provide personalized support.
- Clear Communication: Effective communication is crucial for conveying information clearly and accurately. Customer service representatives should communicate in a friendly and professional manner, using language that is easy to understand and avoiding jargon.
- Knowledgeability: Good customer service requires having a thorough understanding of the products or services being offered. Customer service representatives should be knowledgeable about company policies, procedures, and offerings to provide accurate information and assistance to customers.
- Problem-Solving Skills: Dealing with customer issues and complaints requires strong problem-solving skills. Customer service representatives should be proactive in identifying solutions, addressing concerns, and resolving issues in a timely manner.
- Professionalism: Professionalism encompasses attributes such as courtesy, respect, and reliability. Customer service representatives should conduct themselves professionally at all times, treating customers with dignity and demonstrating a commitment to providing excellent service.
- Follow-Up and Feedback: Good customer service extends beyond the initial interaction. Following up with customers to ensure their satisfaction and seeking feedback on their experience can help identify areas for improvement and build long-term relationships.
By embodying these qualities, businesses can deliver exceptional customer service that fosters loyalty, satisfaction, and positive word-of-mouth recommendations.
FAQs
What is an Alumina PCB?
An Alumina PCB, or alumina ceramic printed circuit board, is a type of circuit board made from alumina ceramic material. It offers excellent electrical insulation properties, high thermal conductivity, and mechanical strength.
What are the advantages of Alumina PCBs?
Alumina PCBs offer several advantages, including high thermal conductivity, excellent electrical insulation, mechanical strength, resistance to high temperatures, and chemical resistance. They are well-suited for high-power and high-frequency electronic applications.
What are the typical applications of Alumina PCBs?
Alumina PCBs are commonly used in applications requiring efficient heat dissipation and reliable performance, such as power amplifiers, LED modules, high-frequency RF circuits, and aerospace electronics.
How are Alumina PCBs manufactured?
The manufacturing process for Alumina PCBs involves substrate preparation, circuit design, printing, curing, etching, surface finishing, drilling, final inspection, and assembly. It includes techniques like screen printing, chemical etching, and surface coating.
What factors affect the cost of Alumina PCBs?
The cost of Alumina PCBs can vary based on factors such as size, complexity, material specifications, manufacturing processes, quantity ordered, additional features, quality standards, and supplier.
Are Alumina PCBs customizable?
Yes, Alumina PCBs can be customized to meet specific requirements, including different sizes, thicknesses, layer configurations, materials, surface finishes, and additional features like impedance control or controlled depth drilling.
What are the key considerations when designing with Alumina PCBs?
When designing with Alumina PCBs, important considerations include thermal management, material selection, trace width and spacing, component placement, via design, copper thickness, dielectric constant, mechanical considerations, and environmental factors.
Where can I purchase Alumina PCBs?
Alumina PCBs can be purchased from various PCB manufacturers and suppliers specializing in ceramic substrates or high-performance PCBs. It’s essential to choose a reputable supplier with experience in Alumina PCB manufacturing.