Bt laminate PCB manufacturing
BT Laminate PCB Manufacturing. BT BGA/IC substrates and BT smallest gap LED pcb will be made with BT Laminate base materials. and There are many kinds of BT materials, we will produce according to your requirements.
Bt laminate PCBs are printed circuit boards made using a laminate material composed of woven glass fabric impregnated with epoxy resin containing Bismaleimide Triazine (BT). They boast excellent thermal stability, a low coefficient of thermal expansion, outstanding electrical properties, and mechanical strength. Commonly employed in aerospace, military, and high-performance electronic applications, Bt laminate PCBs offer flexibility in design and cater to high-frequency, high-speed circuit requirements. They are an ideal choice for applications demanding reliability and superior performance.
What is a Bt laminate PCB?
Bt laminate PCB manufacturing. the Package Substrate will be made with Showa Denko and Ajinomoto High speed materials.or other types high speed materials and high frequency materials.
A “Bt laminate PCB” typically refers to a type of printed circuit board (PCB) that uses a laminate material composed of woven glass fabric impregnated with epoxy resin, where “Bt” stands for “Bismaleimide Triazine.”
Bismaleimide Triazine (BT) is a high-performance thermosetting resin that offers excellent thermal and mechanical properties, making it suitable for use in demanding applications such as aerospace, military, and telecommunications where reliability and performance are critical.
PCBs made with BT laminate are known for their high thermal stability, low coefficient of thermal expansion (CTE), and excellent electrical properties, which make them suitable for use in high-frequency and high-speed applications. These boards are often used in environments where there are stringent requirements for thermal management and reliability.
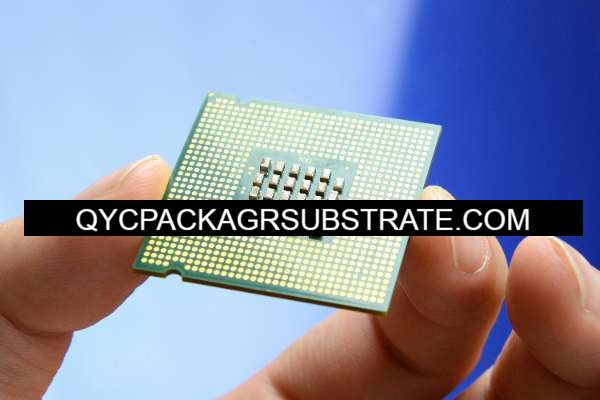
Bt laminate PCB manufacturing
What are the Bt laminate PCB Design Guidelines?
Here are some general design guidelines for Bt laminate PCBs:
- Thermal Considerations: Bt laminate PCBs typically have excellent thermal properties, but it’s still important to consider thermal management. Ensure adequate heat dissipation through proper placement of components, vias, and thermal relief pads.
- High-Speed Signal Integrity: Bt laminate PCBs are often used in high-speed applications. Pay attention to impedance control, signal trace routing, and minimizing signal reflections to maintain signal integrity.
- Component Placement: Place components strategically to minimize signal interference, optimize signal paths, and facilitate efficient PCB assembly. Follow recommended placement guidelines from component manufacturers and consider factors such as signal flow, thermal dissipation, and accessibility for testing and maintenance.
- Grounding: Implement a solid ground plane to provide a low-impedance return path for signals and to reduce electromagnetic interference (EMI). Use multiple ground vias to connect signal layers to the ground plane.
- Power Distribution: Design an efficient power distribution network with adequate power and ground traces to minimize voltage drop and noise. Use wide traces for high-current paths and minimize loop area to reduce EMI.
- Layer Stackup: Optimize the layer stackup considering signal integrity, impedance control, and manufacturing constraints. Bt laminate PCBs may have specific layer configurations for impedance matching and controlled dielectric constants.
- Manufacturability: Design with manufacturability in mind, considering fabrication processes such as drilling, plating, and solder mask application. Follow design rules provided by the PCB manufacturer to ensure the design can be manufactured reliably and cost-effectively.
- Testing and Debugging: Include test points, debug headers, and other provisions for testing and troubleshooting during PCB assembly and system integration. Design for ease of access to critical signals and components for testing and maintenance purposes.
- Compliance and Standards: Ensure the PCB design complies with relevant industry standards and regulations, especially if the end product will be used in safety-critical or regulated environments.
- Documentation: Maintain thorough documentation of the PCB design, including schematic diagrams, layout files, bill of materials (BOM), and design notes. Clear documentation facilitates collaboration, troubleshooting, and future revisions.
These guidelines should be adapted and refined based on the specific requirements of your project and the characteristics of the Bt laminate PCB material you’re using. Additionally, consulting with experienced PCB designers and manufacturers can provide valuable insights and recommendations tailored to your application.
What is the Bt laminate PCB Fabrication Process?
The fabrication process for Bt laminate PCBs follows similar steps to that of standard PCB fabrication. Here’s a general overview of the process:
- Design: The process begins with the PCB design phase, where the circuit schematic is translated into a physical layout using PCB design software. During this phase, considerations such as component placement, routing, and layer stackup are addressed.
- Material Selection: Bt laminate material, which consists of woven glass fabric impregnated with epoxy resin containing bismaleimide triazine (BT), is selected based on the specific requirements of the PCB design. The material thickness and copper foil thickness are chosen according to the design specifications.
- Preparation of Substrate: The Bt laminate material is cut to the desired size, and the copper foil is cleaned and prepared for subsequent processing. Surface preparation is crucial to ensure proper adhesion between the copper foil and the laminate material.
- Layer Alignment and Lamination: Multiple layers of Bt laminate material, each with copper foil adhered to one or both sides, are aligned and stacked according to the layer stackup defined in the PCB design. The layers are then laminated together under heat and pressure to form a single solid panel.
- Drilling: Precision holes are drilled through the laminated panel at locations specified by the PCB design. These holes accommodate through-hole components, vias, and mounting holes. High-precision drilling equipment is used to ensure accurate hole placement and size.
- Copper Etching: The unwanted copper is etched away from the surface of the panel using chemical etchants, leaving behind the desired copper traces and pads according to the PCB design. Photolithography or a similar process is typically used to define the copper traces on each layer before etching.
- Plating: Copper plating is applied to the walls of the drilled holes to create electrical connections between different layers of the PCB. This process, known as electroplating, involves immersing the panel in an electrolyte solution and passing an electric current through it to deposit copper.
- Solder Mask Application: A solder mask layer is applied to the surface of the PCB to protect the copper traces from oxidation and facilitate soldering during assembly. The solder mask is typically applied using a screen printing process and cured under UV light.
- Silkscreen Printing: Component designators, logos, and other identifying markings are printed onto the surface of the PCB using a silkscreen printing process. This step helps with component placement and assembly.
- Surface Finish: A surface finish is applied to the exposed copper surfaces to improve solderability and protect against corrosion. Common surface finish options for Bt laminate PCBs include HASL (Hot Air Solder Leveling), ENIG (Electroless Nickel Immersion Gold), and OSP (Organic Solderability Preservatives).
- Final Inspection and Testing: The finished PCBs undergo visual inspection, electrical testing, and other quality assurance checks to ensure they meet the specifications and performance requirements defined in the design. Any defects or issues are identified and addressed before the PCBs are released for assembly.
- Routing and Separation: After fabrication and testing, the panel is routed into individual PCBs using precision milling or routing equipment. Any remaining tabs or edges are removed, and the PCBs are cleaned and inspected one final time before packaging and shipping.
This process may vary slightly depending on factors such as the specific requirements of the PCB design, the capabilities of the PCB manufacturer, and the quality standards in place. Working with an experienced PCB manufacturer can help ensure a smooth and successful fabrication process for Bt laminate PCBs.
How do you manufacture a Bt laminate PCB?
Manufacturing a Bt laminate PCB involves several steps, from material preparation to final inspection. Here’s an overview of the typical manufacturing process:
- Material Selection: Choose Bt laminate material suitable for the application, considering factors such as thickness, dielectric properties, and thermal stability.
- Panel Preparation: Cut the Bt laminate material into panels of the required size, ensuring they are clean and free from contaminants.
- Layer Stackup: Determine the layer stackup based on the PCB design requirements. Align and stack multiple layers of Bt laminate material with copper foil adhered to one or both sides.
- Lamination: Place the stacked layers in a lamination press and subject them to heat and pressure. This process bonds the layers together to form a solid panel.
- Drilling: Use precision drilling equipment to drill holes at specified locations for through-hole components, vias, and mounting holes.
- Copper Deposition: Apply copper plating to the walls of the drilled holes to create electrical connections between different layers of the PCB. This process is typically done through electroplating.
- Circuit Patterning: Apply a layer of photoresist to the surface of the panel and expose it to UV light through a photomask. Develop and etch away the unwanted copper using chemical etchants, leaving behind the desired copper traces and pads.
- Solder Mask Application: Apply a solder mask layer over the exposed copper traces to protect them from oxidation and facilitate soldering during assembly. The solder mask is typically applied using a screen printing process and cured under UV light.
- Silkscreen Printing: Print component designators, logos, and other identifying markings onto the surface of the PCB using a silkscreen printing process.
- Surface Finish: Apply a surface finish to the exposed copper surfaces to improve solderability and protect against corrosion. Common surface finish options include HASL, ENIG, and OSP.
- Final Inspection and Testing: Inspect the finished PCBs visually and electrically to ensure they meet the specifications and quality standards. Any defects or issues are identified and addressed before the PCBs are released for assembly.
- Routing and Separation: After inspection, the panel is routed into individual PCBs using precision milling or routing equipment. Any remaining tabs or edges are removed, and the PCBs are cleaned and packaged for shipment.
Throughout the manufacturing process, it’s important to follow best practices for quality control and process optimization to ensure the final Bt laminate PCBs meet the desired performance, reliability, and functionality requirements. Working with experienced PCB manufacturers can help streamline the manufacturing process and achieve high-quality results.
How much should a Bt laminate PCB cost?
The cost of a Bt laminate PCB can vary widely depending on several factors, including:
- Board Size and Complexity: Larger boards with more complex designs require more material and processing time, resulting in higher costs.
- Layer Count: The number of layers in the PCB affects manufacturing complexity and material costs. Bt laminate PCBs with more layers typically cost more to produce.
- Material Specifications: The specific type and grade of Bt laminate material used can impact the cost. Higher-performance materials may come at a premium.
- Surface Finish: The choice of surface finish, such as HASL, ENIG, or OSP, can affect the cost of the PCB.
- Copper Thickness: Thicker copper layers may increase material costs and manufacturing complexity.
- Hole Size and Density: PCBs with smaller or more densely packed holes may require more precise drilling and plating processes, which can increase costs.
- Quality Standards: Meeting certain quality standards or certifications may add additional costs to the manufacturing process.
- Quantity: Typically, larger production quantities result in lower per-unit costs due to economies of scale.
As a rough estimate, the cost of a Bt laminate PCB can range from a few dollars for simple, single-layer boards to several hundred dollars or more for complex, multi-layer boards with special requirements. For a precise cost estimate, it’s best to contact PCB manufacturers directly and provide them with detailed specifications of your PCB design. They can then provide you with a quote based on your specific requirements and desired quantity.
What is Bt laminate PCB base material?
Bt laminate PCB base material refers to the substrate used in the fabrication of printed circuit boards (PCBs) that incorporates Bismaleimide Triazine (BT) resin. This base material typically consists of woven glass fabric impregnated with epoxy resin containing BT.
Bismaleimide Triazine (BT) is a high-performance thermosetting resin known for its excellent thermal and mechanical properties, making it suitable for demanding applications such as aerospace, military, and telecommunications. When combined with glass fabric and epoxy resin, BT laminate PCB base material offers several advantages:
- High Thermal Stability: BT resin provides excellent thermal stability, allowing the PCB to withstand high temperatures without significant degradation.
- Low Coefficient of Thermal Expansion (CTE): BT laminate PCBs exhibit a low CTE, which helps minimize dimensional changes and mechanical stress under temperature variations.
- Excellent Electrical Properties: The combination of BT resin with glass fabric and epoxy results in PCBs with good electrical properties, including low dielectric constant and low loss tangent.
- High Mechanical Strength: BT laminate PCBs are mechanically robust, with good tensile and flexural strength, making them suitable for harsh environments and applications with high mechanical stress.
- Chemical Resistance: BT resin provides resistance to a wide range of chemicals, enhancing the durability and reliability of the PCBs in challenging operating conditions.
Overall, Bt laminate PCB base material offers a balance of thermal, mechanical, and electrical properties, making it suitable for high-performance and high-reliability applications where stringent requirements must be met.
Which company makes Bt laminate PCB? (Our Company)
As for our company, we can also manufacture Bt laminate PCBs and have the following advantages:
- Professional Technical Team: We have an experienced and skilled team proficient in the design and manufacturing technology of Bt laminate PCBs.
- Advanced Production Equipment: We are equipped with advanced PCB production equipment and process technology to efficiently and accurately manufacture high-quality Bt laminate PCBs.
- Strict Quality Control: We implement a strict quality control system, conducting rigorous checks at every stage from raw material procurement to production manufacturing to ensure that products meet customer requirements and standards.
- Flexible Production Capacity: We have flexible production capacity to meet the varying specifications and quantities of customer orders, and we can customize production according to specific customer requirements.
- Excellent After-Sales Service: We provide comprehensive pre-sales consultation and after-sales service to ensure that customers receive timely and effective support and assistance throughout the entire cooperation process.
Through Bt laminate PCBs produced by our company, customers can obtain high-quality and highly reliable products to meet their needs in various high-performance and high-reliability application fields. We are committed to providing customers with high-quality products and services, and we look forward to growing and developing together with our customers.
What are the 7 qualities of good customer service?
Good customer service is essential for building strong relationships with customers and ensuring their satisfaction. Here are seven qualities that contribute to providing excellent customer service:
- Empathy: Empathy involves understanding and acknowledging the customer’s feelings, concerns, and needs. It means putting yourself in the customer’s shoes and showing genuine care and concern for their situation.
- Effective Communication: Effective communication is crucial for clear and concise interaction with customers. It involves active listening to understand customer inquiries or issues and providing accurate and helpful responses in a courteous manner.
- Patience: Patience is essential when dealing with customers, especially in challenging or complex situations. It means remaining calm and composed, even when faced with irate or frustrated customers, and taking the time to address their needs thoroughly.
- Product Knowledge: Having a deep understanding of the products or services offered allows customer service representatives to provide accurate information, answer questions, and offer solutions effectively. Product knowledge builds credibility and trust with customers.
- Problem-Solving Skills: Good customer service involves being proactive in resolving customer issues or complaints. It requires problem-solving skills to identify the root cause of the problem, explore possible solutions, and implement appropriate actions to resolve the issue to the customer’s satisfaction.
- Professionalism: Professionalism encompasses maintaining a positive attitude, respecting customers’ time and privacy, and adhering to company policies and standards. It involves presenting oneself in a courteous, respectful, and reliable manner at all times.
- Follow-Up and Follow-Through: Following up with customers after resolving their issues or inquiries shows commitment to their satisfaction and reinforces a positive customer experience. It involves ensuring that promised actions are completed promptly and effectively, and checking in with customers to confirm their satisfaction.
By embodying these qualities, businesses can deliver exceptional customer service that builds trust, loyalty, and positive word-of-mouth recommendations from satisfied customers.
FAQs about Bt laminate PCBs
What is Bt laminate PCB?
Bt laminate PCB is a type of printed circuit board that uses a laminate material composed of woven glass fabric impregnated with epoxy resin containing Bismaleimide Triazine (BT).
What are the advantages of Bt laminate PCBs?
Bt laminate PCBs offer high thermal stability, low coefficient of thermal expansion (CTE), excellent electrical properties, and mechanical strength. They are suitable for high-frequency and high-speed applications.
Where are Bt laminate PCBs commonly used?
Bt laminate PCBs are commonly used in industries such as aerospace, military, telecommunications, and high-performance electronics where reliability, thermal management, and signal integrity are critical.
How do Bt laminate PCBs differ from other types of PCBs?
Bt laminate PCBs differ from other types of PCBs primarily in the material composition of the laminate, which includes Bismaleimide Triazine (BT) resin. This resin provides enhanced thermal and mechanical properties compared to standard epoxy resin laminates.
What are the key considerations for designing Bt laminate PCBs?
Design considerations for Bt laminate PCBs include thermal management, signal integrity, component placement, grounding, power distribution, layer stackup, manufacturability, compliance with standards, and documentation.
Can Bt laminate PCBs be manufactured in different layer counts?
Yes, Bt laminate PCBs can be manufactured in various layer counts, ranging from single-layer to multi-layer configurations, depending on the specific requirements of the application.
What surface finish options are available for Bt laminate PCBs?
Common surface finish options for Bt laminate PCBs include HASL (Hot Air Solder Leveling), ENIG (Electroless Nickel Immersion Gold), OSP (Organic Solderability Preservatives), and others, chosen based on the application’s needs.
How can I obtain a quote for Bt laminate PCB manufacturing?
You can obtain a quote for Bt laminate PCB manufacturing by contacting reputable PCB manufacturers, providing them with detailed specifications of your design, including material requirements, layer count, dimensions, surface finish, and quantity needed.