BT PCB Manufacturer
BT PCB Manufacturer,BT PCB, or Bismaleimide Triazine Printed Circuit Board, is a high-performance substrate known for its exceptional thermal stability and mechanical strength. It features a resin system composed of bismaleimide and triazine, offering excellent thermal resistance, low thermal expansion, and high glass transition temperature (Tg). BT PCBs are widely used in applications requiring reliability under harsh conditions, such as aerospace, automotive, and telecommunications. They support high-speed signal transmission and are compatible with lead-free soldering processes, making them ideal for modern electronic designs. BT PCBs ensure robust performance in demanding environments where reliability and performance are critical factors.
What is a BT PCB?
BT PCB (Bismaleimide-Triazine PCB) is a high-performance circuit board widely used in electronic devices that require high reliability and heat resistance. BT resin is the main substrate material of BT PCBs, known for its excellent mechanical strength, good heat resistance, and electrical insulation properties. Its chemical stability allows BT PCBs to maintain good performance in high-temperature and humid environments, making them particularly suitable for applications in automotive, aerospace, and high-frequency communications.
The manufacturing process of BT PCBs involves combining BT resin with glass fiber cloth and curing it at high temperatures to form a stable substrate. Compared to traditional FR-4 PCBs, BT PCBs can operate at higher temperatures, typically up to 180°C. Additionally, BT PCBs have a lower dielectric constant and loss, making them suitable for high-frequency applications, which is crucial for modern wireless communications and RF devices.
In terms of design, BT PCBs offer greater design flexibility, enabling the production of multilayer boards and complex circuit layouts to meet the demands of high-density integrated circuits. As electronic devices continue to become smaller and more powerful, BT PCBs are increasingly chosen for high-end electronic products due to their superior performance. Overall, BT PCBs are an indispensable part of modern electronic manufacturing, especially in applications with stringent temperature and performance requirements.
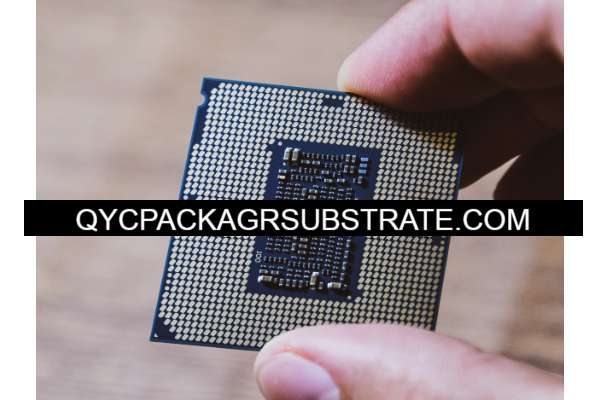
BT PCB Manufacturer
What are the BT PCB Design Guidelines?
Designing with BT PCBs (Bismaleimide-Triazine PCBs) involves adhering to specific guidelines to ensure optimal performance and reliability. Here are some key design guidelines for BT PCBs:
- Material Selection: Choose BT resin with appropriate characteristics such as thermal stability, mechanical strength, and electrical properties suitable for the application’s requirements.
- Thermal Management: Consider the thermal conductivity of the BT substrate and design adequate thermal vias or heat sinks to manage heat dissipation effectively, especially in high-power applications.
- Layer Stackup: Optimize the layer stackup to achieve desired impedance control, signal integrity, and manufacturability. BT PCBs can support complex multilayer designs; ensure proper layer sequencing and symmetry.
- Trace Width and Spacing: Follow recommended trace width and spacing guidelines to minimize signal loss, crosstalk, and electromagnetic interference (EMI). BT PCBs typically allow finer trace widths due to their lower dielectric constant.
- Via Design: Use appropriate via structures (plated through-holes or microvias) based on the density and complexity of the PCB layout. Consider aspect ratio limitations to ensure reliable plating and connectivity.
- Signal Integrity: Ensure controlled impedance for critical high-speed signals by maintaining consistent trace dimensions and dielectric thickness throughout the PCB design.
- Component Placement: Optimize component placement to minimize signal path lengths, reduce noise coupling, and facilitate efficient routing. Consider placement for thermal management and mechanical stability.
- Manufacturing Considerations: Communicate design specifications clearly with PCB manufacturers to ensure compatibility with BT PCB fabrication processes, including lamination and drilling.
- Testing and Validation: Plan for testing and validation procedures to verify electrical performance, thermal behavior, and reliability under operating conditions.
- Environmental Considerations: Evaluate environmental factors such as humidity, temperature cycling, and mechanical stress to ensure long-term durability and performance of BT PCBs.
By following these design guidelines, engineers can leverage the advantages of BT PCBs to achieve high-performance electronic designs suitable for demanding applications in industries such as aerospace, automotive, telecommunications, and high-speed computing.
What is the BT PCB Fabrication Process?
The fabrication process of BT PCBs (Bismaleimide-Triazine PCBs) involves several key steps to ensure high-quality, reliable circuit boards. Here’s an overview of the typical fabrication process:
- Material Preparation: Start with BT resin and glass fiber reinforcement materials. The resin is typically in sheet form, which is cut to the desired size for the PCB layers.
- Layer Stack-up: The layers are stacked according to the design specifications. This includes placing prepreg (the uncured BT resin) between layers of copper foil and glass fiber.
- Lamination: The stacked layers undergo lamination under heat and pressure. This process cures the BT resin, bonding the layers together and forming a solid substrate. Proper temperature and pressure are critical to ensure optimal bonding and to avoid defects.
- Drilling: After lamination, holes are drilled into the PCB for vias and component placements. High-speed drills or laser drilling can be used, depending on the precision required.
- Copper Plating: The drilled holes are plated with copper to create conductive pathways. This process often involves electroless plating followed by electrolytic plating to build up the copper layer.
- Photoresist Application: A photoresist layer is applied to the copper surface. This light-sensitive material will define the pattern of the circuit.
- Exposure and Development: The photoresist is exposed to UV light through a photomask, which contains the desired circuit pattern. After exposure, the board is developed, washing away the unexposed areas, leaving the circuit pattern protected by the remaining photoresist.
- Etching: The exposed copper is etched away using a chemical solution, removing the unprotected areas and leaving behind the desired copper traces and pads.
- Photoresist Removal: The remaining photoresist is stripped off, revealing the finished copper pattern.
- Surface Finishing: The board may undergo surface finishing processes, such as immersion gold, ENIG (Electroless Nickel Immersion Gold), or OSP (Organic Solderability Preservative) to enhance solderability and protect the copper from oxidation.
- Electrical Testing: The finished boards are electrically tested to check for shorts, opens, and other defects, ensuring functionality.
- Cutting and Routing: Finally, the PCBs are cut and routed to the specified dimensions, ready for assembly.
Each step in the fabrication process must be carefully controlled to ensure the integrity and performance of the BT PCBs, especially considering their use in high-performance and high-reliability applications.
How do you manufacture a BT PCB?
Manufacturing a BT PCB (Bismaleimide-Triazine PCB) involves several key steps. Here’s a detailed overview of the manufacturing process:
- Material Selection: Choose high-quality BT resin and glass fiber reinforcement. The resin is typically available in sheets that are cut to the required dimensions for the PCB layers.
- Layer Preparation: Cut the BT resin and glass fiber to size based on the design specifications. This includes preparing any prepreg (uncured resin) that will be used between copper layers.
- Stack-up Assembly:Assemble the layers in the desired stack-up configuration. This includes layering the prepreg between copper foils and glass fiber sheets.
- Lamination:The stacked materials are laminated using heat and pressure. This process cures the BT resin, bonding the layers together into a solid substrate. The lamination parameters (temperature and pressure) are critical for optimal results.
- Drilling: Once laminated, holes are drilled into the PCB for vias and component mounting. This can be done using high-speed drills or lasers for precision.
- Copper Plating: The drilled holes are plated with copper. This typically involves an electroless plating step followed by electrolytic plating to build up the copper thickness.
- Photoresist Application: Apply a layer of photoresist to the copper surface. This light-sensitive material is crucial for defining the circuit pattern.
- Exposure and Development: The photoresist is exposed to UV light through a photomask that contains the circuit design. After exposure, the board is developed, washing away unexposed photoresist to reveal the copper areas.
- Etching: The exposed copper is etched away using a chemical solution, leaving behind the desired circuit pattern.
- Photoresist Stripping: The remaining photoresist is removed, exposing the finished copper traces.
- Surface Finishing: The PCB may undergo surface finishing processes, such as immersion gold or ENIG (Electroless Nickel Immersion Gold), to improve solderability and protect the copper.
- Electrical Testing: The finished boards are electrically tested for shorts, opens, and other defects to ensure proper functionality.
- Routing and Cutting: Finally, the PCBs are cut to the specified dimensions and routed as needed for final assembly.
Each of these steps requires precise control to ensure the quality and reliability of the BT PCBs, especially for applications in high-performance electronics.
How much should a BT PCB cost?
The cost of a BT PCB (Bismaleimide-Triazine PCB) can vary widely based on several factors, including:
- Size and Complexity: Larger and more complex designs with multiple layers typically cost more due to increased material and manufacturing processes.
- Layer Count: BT PCBs can range from a few layers to many layers. More layers generally increase the cost due to additional materials and processing time.
- Volume: Higher production volumes can lead to cost reductions due to economies of scale. Smaller quantities may incur higher per-unit costs.
- Surface Finishing: The type of surface finish selected (e.g., ENIG, OSP, HASL) can affect pricing. More advanced finishes typically cost more.
- Turnaround Time: Rush orders or expedited manufacturing processes may result in higher costs.
- Additional Features: Special requirements such as controlled impedance, high-frequency capabilities, or specific testing may increase costs.
- Manufacturer: Different manufacturers may have varying pricing structures based on their capabilities, quality standards, and production processes.
As a rough estimate, the cost of a basic BT PCB might start around $20 to $100 for simple, small designs in low volumes. However, for more complex or high-performance applications, costs can range from $100 to several hundred dollars per board. It’s best to request quotes from manufacturers based on specific design parameters to get an accurate price.
What is BT PCB base material?
BT PCB base material refers to the substrate used in Bismaleimide-Triazine PCBs, which is composed of BT resin combined with glass fiber reinforcement. This material offers several key properties:
- Thermal Stability:BT resin has a high glass transition temperature (Tg), typically around 180°C, allowing the PCB to operate reliably in high-temperature environments.
- Mechanical Strength: The combination of BT resin and glass fiber provides excellent mechanical strength, making the material durable and suitable for demanding applications.
- Electrical Insulation: BT base material has good electrical insulation properties, ensuring reliable signal integrity and preventing short circuits.
- Low Dielectric Constant and Loss: BT PCBs exhibit low dielectric constants and loss factors, making them ideal for high-frequency applications.
- Chemical Resistance: The BT resin offers resistance to moisture and various chemicals, enhancing the PCB’s longevity and reliability in harsh environments.
Overall, BT PCB base material is commonly used in high-performance electronics, including telecommunications, aerospace, automotive, and other industries requiring high reliability and performance.
Which company makes BT PCB?
BT PCB (Bismaleimide-Triazine PCB) is a high-performance circuit board primarily used in electronic devices that require high reliability and heat resistance. Currently, several companies manufacture and supply BT PCBs, including well-known domestic and international electronic materials and PCB manufacturers.
On the international market, prominent electronic materials companies and PCB manufacturers like Rogers Corporation, Isola Group, and Park Electrochemical Corp. offer BT PCB products with excellent performance. These companies not only have advanced technology and production facilities but also provide high-quality BT PCBs customized to meet specific customer needs, widely used in aerospace, automotive, telecommunications, and other fields.
In the domestic market, there are also several PCB manufacturers with technical strength and production capabilities, such as Shenzhen XXX Electronics Co., Ltd. andShanghai XXX Electronics Technology Co., Ltd., which can provide BT PCB products that meet international standards and customer requirements. These companies typically equip advanced production equipment and implement strict quality control systems to ensure product performance and reliability.
As a company focused on high-performance PCB production, we are also capable of manufacturing BT PCBs. We possess advanced production technology and extensive experience, allowing us to offer customized BT PCB solutions based on customer design requirements and application scenarios. Our manufacturing process includes material selection, lamination, drilling, copper plating, pattern definition, etching, and surface treatment, ensuring that each BT PCB meets high-quality manufacturing standards.
Additionally, we prioritize customer needs and product quality, providing comprehensive services from design support to production delivery. Whether during the product development phase or mass production stage, we can deliver satisfactory BT PCB solutions to help our customers gain a competitive edge in the market.
In summary, BT PCBs, as a high-performance circuit board material, have broad application prospects and market demand. Both internationally renowned companies and domestic specialized manufacturers are continually enhancing product quality and technological innovation to meet diverse customer needs and challenges.
What are the 7 qualities of good customer service?
Good customer service is essential for building strong relationships with customers and fostering loyalty. Here are seven key qualities of effective customer service:
- Responsiveness: Quick and efficient responses to customer inquiries and issues show that the company values its customers’ time and needs.
- Empathy: Understanding and acknowledging customers’ feelings and concerns helps build trust and rapport, making customers feel valued and heard.
- Knowledge:Customer service representatives should possess in-depth knowledge of the products or services offered, enabling them to provide accurate information and effective solutions.
- Communication Skills: Clear, concise, and friendly communication is vital. This includes both verbal and written communication, ensuring customers understand the information provided.
- Problem-Solving Ability: Good customer service involves identifying issues and finding appropriate solutions swiftly, demonstrating a commitment to resolving customer problems.
- Patience: Dealing with customers, especially those who are frustrated, requires patience. Taking the time to listen and assist without rushing is crucial.
- Positive Attitude: A friendly and positive demeanor can greatly enhance the customer experience, leaving a lasting impression and encouraging repeat business.
These qualities contribute to an overall positive customer experience, fostering loyalty and encouraging customers to recommend the business to others.
FAQs
What are the advantages of BT PCBs?
Advantages include high thermal resistance, low dielectric constant, good electrical insulation, and chemical resistance, making them suitable for high-frequency and high-temperature applications.
Where are BT PCBs commonly used?
BT PCBs are used in industries like aerospace, automotive, telecommunications, and high-speed computing, where reliability and performance are critical.
How are BT PCBs manufactured?
The manufacturing process includes material preparation, lamination, drilling, copper plating, photoresist application, etching, and surface finishing.
What is the cost of a BT PCB?
The cost varies based on factors like size, complexity, layer count, and volume. Basic BT PCBs can start around $20, while more complex designs can cost significantly more.
Can BT PCBs be customized?
Yes, BT PCBs can be customized based on specific design requirements, including layer count, dimensions, and surface finishes.
What design considerations should be kept in mind?
Key considerations include thermal management, trace width, spacing, layer stack-up, and signal integrity to ensure optimal performance.