Cavity | High Frequency PCB Manufacturer
Cavity | High Frequency PCB Manufacturer,Cavity High Frequency PCBs are specialized circuit boards designed to operate at high frequencies with minimal signal loss and interference. These PCBs feature cavities or recessed areas to accommodate components, reducing signal path lengths and enhancing performance. They are constructed using high-quality materials that ensure excellent signal integrity and low dielectric loss, making them ideal for applications in telecommunications, radar systems, and satellite communications. The cavity design also aids in efficient thermal management and component isolation. Cavity High Frequency PCBs are crucial for advanced electronic systems requiring precise signal transmission and reliability at high frequencies.
What is a Cavity | High Frequency PCB?
A “cavity” in the context of High Frequency PCBs (Printed Circuit Boards) refers to an intentionally created hollow space or recess within the PCB material. This cavity can be used to enhance the performance of the PCB in high-frequency applications, particularly in RF (Radio Frequency) and microwave circuits.
The primary purpose of incorporating cavities into high-frequency PCBs is to reduce signal loss and improve signal integrity. By designing cavities, engineers can create specific electromagnetic environments that can help in controlling impedance, reducing signal interference, and minimizing the dielectric losses that often occur in high-frequency signals.
Cavities are typically fabricated by etching or machining the PCB substrate material, and they are often filled with dielectric materials to achieve the desired electrical properties. This design approach helps in managing the signal propagation characteristics and ensuring efficient performance of high-frequency circuits.
In summary, cavities in High Frequency PCBs are crucial for optimizing signal transmission and performance, especially in applications where high-speed and high-frequency signals are involved.
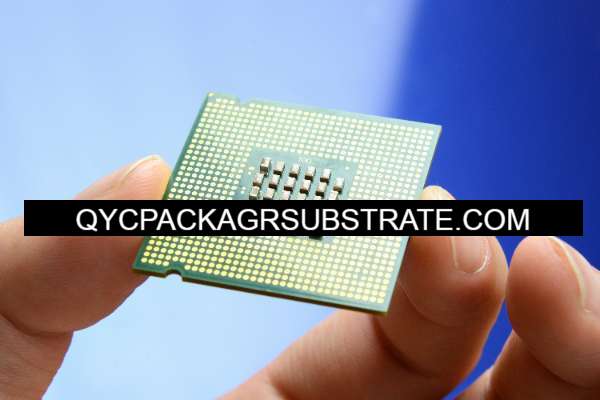
Cavity | High Frequency PCB Manufacturer
What are the Cavity | High Frequency PCB Design Guidelines?
When designing high-frequency PCBs with cavities, several guidelines should be followed to ensure optimal performance and signal integrity:
- Cavity Dimensions: Carefully calculate the dimensions of the cavity to align with the target frequency. The size and shape of the cavity can impact impedance and signal behavior. Commonly, cavities are designed to be a quarter-wavelength or a multiple of the wavelength of the signal frequency.
- Dielectric Material: Choose dielectric materials with low loss tangent and stable electrical properties to fill the cavity. This helps minimize signal loss and maintain consistent performance across varying temperatures.
- Cavity Placement:Position cavities strategically to influence signal propagation and impedance matching. Ensure they are located where they can most effectively impact signal integrity, such as near critical components or signal paths.
- Board Thickness: Maintain consistent board thickness around the cavity to avoid uneven signal propagation and ensure mechanical stability.
- Edge Treatment: Smooth the edges of the cavity to prevent signal reflections and discontinuities. Sharp edges can cause unwanted electromagnetic effects and signal loss.
- Grounding and Shielding: Implement proper grounding and shielding techniques around cavities to minimize electromagnetic interference (EMI) and ensure a clean signal path.
- Thermal Management: Consider thermal management strategies, as high-frequency operations can generate heat. Proper ventilation and heat dissipation methods should be integrated into the cavity design.
- Simulation and Testing: Utilize simulation tools to model the cavity’s impact on high-frequency signals. Validate the design through rigorous testing to ensure it meets performance specifications and expectations.
By adhering to these guidelines, designers can create high-frequency PCBs with cavities that effectively manage signal integrity and enhance overall performance.
What is the Cavity | High Frequency PCB Fabrication Process?
The fabrication process for High Frequency PCBs with cavities involves several key steps to ensure accurate and effective implementation of the cavity features. Here’s an overview of the typical process:
- Design and Layout: Start with detailed design and layout of the PCB, including the specification of cavity dimensions and placement. Use high-frequency PCB design software to create accurate schematics and layout that incorporate the cavities.
- Material Selection: Choose appropriate PCB base materials with low dielectric loss and high-frequency performance characteristics. Common choices include Rogers, Arlon, and Taconic materials.
- Substrate Preparation: Prepare the PCB substrate by cutting it to the desired size and shape. Ensure that the substrate material has been properly prepped to accommodate cavity machining.
- Cavity Milling or Etching: Create cavities in the PCB substrate using precise milling or etching techniques. CNC milling is often used for creating larger or complex cavity shapes, while etching can be used for simpler designs. The depth and dimensions of the cavities are carefully controlled to match design specifications.
- Dielectric Filling: Fill the cavities with suitable dielectric materials, such as epoxy-based fillers or specialized high-frequency materials. This step ensures that the dielectric constant and loss properties are optimized for high-frequency applications.
- Laminate and Copper Layering:Apply copper layers to the PCB, including any necessary plating or bonding processes. The cavities may require special attention to ensure that the copper layers are properly aligned and do not introduce signal integrity issues.
- Circuit Patterning: Use photolithography or other patterning techniques to define the circuit traces and components on the PCB. This step involves applying and developing a photoresist layer, followed by etching to remove excess copper.
- Assembly: Assemble the PCB by attaching components, soldering, and making any necessary connections. Ensure that the assembly process does not compromise the cavity structures or overall performance.
- Testing and Inspection: Conduct thorough testing and inspection of the PCB to verify that the cavities and overall design meet the required specifications. This includes checking signal integrity, impedance, and other performance parameters.
- Final Touches: Perform final cleaning, coating, and packaging of the PCB. Apply any protective coatings or finishes to ensure durability and reliability in the final product.
By following these fabrication steps, manufacturers can produce high-frequency PCBs with cavities that meet performance requirements and are suited for advanced RF and microwave applications.
How do you manufacture a Cavity | High Frequency PCB?
Manufacturing a High Frequency PCB with cavities involves several precise and detailed steps to ensure the final product meets performance standards. Here’s an overview of the typical manufacturing process:
- Design and Planning: Develop detailed PCB designs including the dimensions and placement of cavities. Use high-frequency PCB design software to ensure accurate specifications for the cavities and overall circuit layout.
- Material Selection: Choose a high-frequency substrate material with low dielectric loss and appropriate electrical properties, such as Rogers or Taconic materials. Ensure the material can support cavity milling or etching.
- Substrate Preparation: Cut the substrate material to the required size and shape. This involves precision cutting to ensure the substrate is ready for the cavity machining process.
- Cavity Creation:
– Milling: Use CNC machines to mill cavities into the substrate. This process involves precise cutting to create cavities of specific dimensions and shapes as per the design requirements.
– Etching: For simpler cavity designs, chemical etching can be employed to remove material and create cavities. This method requires careful control to ensure accurate cavity depth and dimensions.
- Dielectric Material Filling: After cavities are created, fill them with appropriate dielectric materials to achieve the desired electrical properties. Common dielectric fillers include epoxy-based materials or other high-frequency specific fillers.
- Laminate Layering:Apply additional laminate layers as needed. This may include bonding copper layers to the PCB, which involves processes such as lamination, plating, and etching to define the circuit traces and patterns.
- Circuit Patterning: Apply and develop a photoresist layer, then use photolithography to define the circuit patterns. Etch the copper layers to create the necessary circuit traces while ensuring the cavities are not compromised.
- Assembly: Assemble the PCB by soldering and attaching components. Ensure that the cavity structures are not disrupted during this process and that all components are correctly positioned.
- Testing and Quality Control: Conduct comprehensive testing and inspection to verify the performance of the PCB. This includes checking signal integrity, impedance, and the accuracy of cavity dimensions. Perform both electrical and mechanical inspections to ensure the product meets specifications.
- Final Finishing: Apply protective coatings or finishes to the PCB to enhance durability and reliability. Perform final cleaning and packaging of the PCB for shipment.
By carefully following these manufacturing steps, you can produce high-frequency PCBs with cavities that deliver optimal performance in RF and microwave applications.
How much should a Cavity | High Frequency PCB cost?
The cost of a High Frequency PCB with cavities can vary widely depending on several factors, including:
- Material: High-frequency substrates like Rogers, Taconic, or Arlon tend to be more expensive than standard FR-4 materials. The cost will also depend on the specific type of dielectric material used in the cavities.
- Design Complexity: The complexity of the PCB design, including the number and size of cavities, will impact the cost. More intricate designs require more precise fabrication and often lead to higher costs.
- Cavity Dimensions and Quantity: Larger and more numerous cavities generally increase the manufacturing cost. Precision machining or etching for cavities adds to the complexity and expense.
- Layer Count: Multi-layer PCBs, which are common in high-frequency applications, are more costly than single-layer boards. The number of layers required can affect the overall price.
- Volume: Production volume affects cost per unit. High-volume orders often benefit from economies of scale, reducing the cost per PCB. Conversely, low-volume or prototype runs may be more expensive per unit.
- Additional Features: Extra features like specialized coatings, advanced circuit patterns, or high-precision tolerances can add to the cost.
- Manufacturer and Location: Different manufacturers have varying pricing structures, and location can affect labor and material costs. Domestic production may be more expensive than overseas manufacturing, but it may offer advantages in lead time and quality control.
These estimates are general and can fluctuate based on specific requirements and market conditions. For an accurate quote, it’s best to consult with PCB manufacturers or suppliers who can provide detailed pricing based on your particular design and production needs.
What is Cavity | High Frequency PCB base material?
The base material for a Cavity High Frequency PCB is crucial for achieving the desired performance in high-frequency applications. The material chosen must have specific electrical and thermal properties to support the requirements of high-frequency circuits. Here are the common base materials used:
- Rogers Materials:Rogers offers a range of high-frequency PCB materials such as Rogers RO4000, RO3000, and RO5880 series. These materials are known for their low dielectric loss, stable electrical performance, and high thermal conductivity. They are suitable for applications requiring precise signal integrity and minimal signal degradation.
- Taconic Materials: Taconic provides high-performance substrates like Taconic RF-35 and Taconic TLY-5. These materials are designed to offer low loss tangent and high thermal stability, making them ideal for RF and microwave applications.
- Arlon Materials: Arlon’s high-frequency materials, such as Arlon AD-series and Arlon 25N, are known for their low dielectric constants and low loss tangent. These materials are used in applications where signal integrity and high-frequency performance are critical.
- Isola Materials: Isola’s high-frequency materials, including the IS410 and IS420 series, are engineered for high-speed and high-frequency performance. They provide stable dielectric properties and are suitable for advanced RF and microwave circuits.
- PTFE (Polytetrafluoroethylene): PTFE-based materials, such as those from companies like Rogers and Taconic, are highly effective for high-frequency applications due to their low dielectric constant and low loss tangent. PTFE is often used in conjunction with copper foil to achieve desired performance.
- Ceramic Materials: For some high-frequency applications, ceramic substrates are used due to their excellent dielectric properties and high thermal conductivity. Ceramics can be particularly effective for creating cavities that need specific electromagnetic characteristics.
- Glass-Reinforced Materials: Materials like FR4 with glass reinforcement can also be used for high-frequency applications, though they typically offer higher dielectric losses compared to specialized high-frequency materials.
By selecting the appropriate base material, manufacturers can ensure that Cavity High Frequency PCBs achieve optimal performance and reliability in their intended applications.
Which company makes Cavity | High Frequency PCB?
In the field of high-frequency applications, several companies specialize in manufacturing high-frequency printed circuit boards (PCBs) with cavities. These companies use advanced manufacturing technologies and high-performance base materials to ensure the optimal performance of their products in RF (radio frequency) and microwave circuits. Here are some key manufacturers:
- Rogers Corporation: Rogers is a leading supplier of high-frequency PCB materials, offering a range of high-performance substrates such as the RO4000, RO3000, and RO5880 series. Their materials are well-regarded for their low dielectric loss, stable electrical performance, and excellent thermal conductivity. Rogers also provides PCB solutions supporting cavity designs to meet the needs of complex high-frequency applications.
- Taconic: Taconic provides high-performance materials like RF-35 and TLY-5, which feature low dielectric constants and low loss tangents, making them ideal for high-frequency applications. Taconic’s products effectively reduce signal attenuation and interference when designing high-frequency PCBs.
- Arlon: Arlon’s high-frequency materials, such as the AD series and 25N series, are known for their low dielectric constants and low loss tangents. These products are widely used in high-frequency and high-speed circuits, providing stable electrical performance and good signal integrity.
- Isola: Isola’s IS410 and IS420 series high-frequency materials excel in stable dielectric performance and low loss. These materials are designed for high-frequency and high-speed applications, suitable for complex RF circuits.
- Advanced Circuitry International (ACI): ACI specializes in high-frequency and RF PCB design and manufacturing, offering customized cavity designs and high-performance material solutions.
- Shenzhen Suntak PCB: As a leading PCB manufacturer in China, Suntak provides various PCB solutions, including high-frequency PCBs, to meet different high-frequency application needs.
Our company also manufactures Cavity High Frequency PCBs. We use advanced manufacturing technologies and high-quality base materials to ensure our products perform exceptionally well in high-frequency applications. We offer customized design services, enabling us to design and manufacture cavity high-frequency PCBs with high precision and performance according to customer specifications. Whether you need complex cavity structures or special material requirements, we can provide comprehensive solutions and ensure product quality and reliability.
Our manufacturing capabilities include precision CNC milling and chemical etching technologies to create cavities that meet design specifications. We use advanced high-frequency materials, such as Rogers and Taconic substrates, to ensure electrical performance and signal integrity. Through rigorous testing and quality control, our Cavity High Frequency PCBs deliver stable performance and reliable operation in various high-frequency applications.
In summary, whether you require high-frequency signal processing, RF applications, or microwave circuits, our company can provide high-quality cavity high-frequency PCB solutions that meet your needs.
What are the 7 qualities of good customer service?
Good customer service is essential for building and maintaining strong relationships with customers. Here are seven key qualities that characterize excellent customer service:
- Responsiveness: Quick and efficient responses to customer inquiries, complaints, and requests are crucial. Customers appreciate timely feedback and solutions to their issues. Ensuring that service representatives are available through multiple channels (phone, email, chat) and that they respond promptly enhances customer satisfaction.
- Empathy: Understanding and addressing the customer’s needs, emotions, and concerns with genuine care is vital. Empathetic service involves actively listening to customers, acknowledging their feelings, and providing support that makes them feel valued and understood.
- Knowledgeability: Providing accurate and thorough information about products, services, and policies is essential. Service representatives should be well-trained and knowledgeable to answer questions effectively, resolve issues, and guide customers through processes with confidence.
- Politeness and Professionalism: Courteous and respectful interaction is fundamental. Service representatives should maintain a professional demeanor, use polite language, and handle all interactions with a positive attitude, even in challenging situations.
- Reliability: Consistently delivering on promises and maintaining a high standard of service reliability fosters trust. Customers need to feel confident that their concerns will be addressed and that the company will stand by its commitments.
- Personalization: Tailoring service to individual customer needs and preferences enhances the overall experience. Personalizing interactions by using the customer’s name, remembering past interactions, and providing relevant recommendations can make customers feel special and valued.
- Problem-Solving Skills:Effective problem-solving involves not only addressing immediate issues but also finding long-term solutions. Service representatives should be adept at identifying the root cause of problems, offering practical solutions, and ensuring that similar issues are prevented in the future.
By embodying these qualities, companies can deliver exceptional customer service that meets or exceeds customer expectations, fosters loyalty, and enhances overall satisfaction.
FAQs
What is the typical lead time for a Cavity | High Frequency PCB?
The lead time can vary depending on the complexity and quantity of the order but generally ranges from 2 to 6 weeks.
Can you help with the design of a Cavity | High Frequency PCB?
Yes, our engineering team can assist with the design to ensure optimal performance and manufacturability.
What testing do you perform on Cavity | High Frequency PCBs?
We perform a variety of tests, including impedance testing, signal integrity testing, and thermal cycling, to ensure the highest quality.
Do you offer prototypes for Cavity | High Frequency PCBs?
Yes, we offer prototyping services to help you validate your design before full-scale production.
What file formats do you accept for PCB designs?
We accept various file formats, including Gerber files, ODB++, and IPC-2581.
Can you handle high-volume production?
Yes, we have the capacity to handle both low and high-volume production runs.
What certifications do you have?
Our facilities are ISO 9001 and IPC-6012 certified, ensuring high-quality manufacturing standards.