Professional Ceramic Package Substrate Supplier, we mainly produce ultra-small bump pitch substrate, ultra-small trace and spacing packaging substrate and PCBs.
Why is Ceramic Package Substrate Integral to Modern PCB Engineering?
The Ceramic Package Substrate stands as a linchpin in contemporary PCB engineering, offering indispensable features that elevate the reliability and performance of electronic devices.
Efficient Thermal Management:
Ceramic substrates shine in thermal conductivity, proficiently dissipating heat from electronic components. This capability is pivotal to prevent overheating and sustain stable device operation over time.
Robust Mechanical Support:
Endowed with high mechanical strength, ceramic materials provide robust support, shielding delicate electronic components against mechanical stress and environmental factors. This ensures enduring durability in diverse operational conditions.
Low Dielectric Loss:
Ceramic substrates exhibit minimal dielectric loss, curbing energy dissipation as heat. This attribute proves vital in high-frequency applications, curtailing signal interference and preserving signal integrity.
Enabler of Miniaturization and High-Density Packaging:
Ceramic substrates play a pivotal role in facilitating device miniaturization, accommodating high-density packaging with fine-pitch components and multilayer structures. This fosters the creation of compact and efficient electronic systems.
Excellent Electrical Insulation:
Ceramic materials deliver superior electrical insulation, adeptly mitigating signal crosstalk and interference within intricate electronic circuits, bolstering overall system reliability.
Ideal for High-Frequency Applications:
Tailored for high-frequency applications like wireless communication and RF circuits, ceramic substrates maintain stable electrical properties at elevated frequencies, complemented by a low loss tangent, ensuring optimal performance.
Chemical Resistance:
Exhibiting resistance to chemicals and environmental factors, ceramic substrates enhance device durability and reliability, particularly in demanding operating conditions.
Hermetic Sealing Capability:
Ceramic packages provide hermetic sealing, safeguarding internal components from moisture and contaminants. This sealing prowess is instrumental in preserving component integrity over extended operational periods.
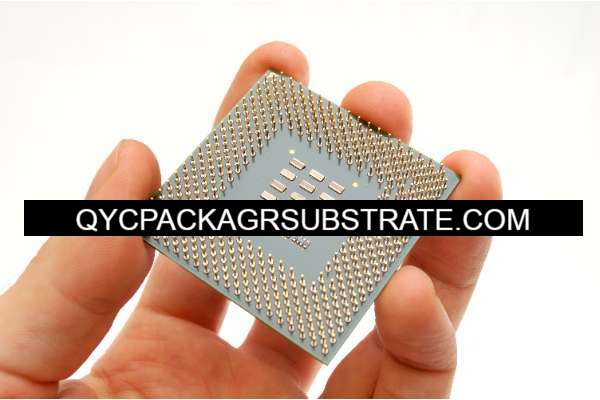
How Does Ceramic Package Substrate Function to Enhance Performance and Reliability?
Ceramic package substrates play a vital role in pushing the boundaries of electronic device performance and reliability, particularly in the realm of integrated circuits (ICs) and semiconductor packages. These substrates, often composed of materials like alumina (Al2O3) or aluminum nitride (AlN) for their exceptional thermal and electrical properties, fulfill key functions:
Smart Heat Regulation:
In the dynamic world of electronic components, ceramic package substrates take center stage in intelligently managing the heat generated during operation. Leveraging their impressive thermal conductivity, ceramics become conductive maestros, swiftly directing and dissipating heat away from sensitive components. This prowess is a cornerstone in preventing overheating, ensuring a steady performance, and elongating the operational life of electronic components.
Electrical Insulation Mastery:
Ceramics are the unsung heroes in the electrical realm, mastering the art of insulation within semiconductor devices. Their role is pivotal in creating a safe distance between various conductive components, warding off short circuits, preserving signal integrity, and mitigating unwarranted interference. This insulation wizardry guarantees the unwavering reliability of the device.
Rock-Solid Mechanical Support:
Enter the stage of mechanical prowess, where ceramic package substrates play the role of stalwart supporters for delicate semiconductor components. Their inherent strength is the backbone, allowing them to weather the storms of manufacturing, assembly, and daily operations. This robust support significantly amplifies the durability and reliability of electronic devices.
Dimensional Consistency Magic:
Picture ceramics as the guardians of consistency, maintaining their shape and structure unwaveringly across temperature fluctuations and environmental shifts. This magical quality is paramount in ensuring a seamless alignment and connection of semiconductor components throughout the device’s entire lifespan.
Miniaturization and Fusion Facilitation:
Ceramics step into the spotlight as catalysts for the miniaturization revolution in electronic devices, enabling the seamless fusion of numerous components within confined spaces. This transformative role is particularly crucial in today’s electronics landscape, where the mantra is smaller form factors. By densely packing components, ceramic substrates become architects of heightened system performance and functionality.
Harmony with Manufacturing Symphony:
Ceramic materials become integral players in the symphony of modern semiconductor manufacturing processes, effortlessly harmonizing with standard procedures to facilitate cost-effective mass production. This dance of compatibility is the linchpin for efficiently crafting electronic devices that meet lofty standards of performance and reliability.
In summary, ceramic package substrates significantly contribute to advancing the performance and reliability of electronic devices by efficiently managing heat, providing electrical insulation, offering sturdy mechanical support, ensuring dimensional stability, enabling miniaturization, and maintaining compatibility with manufacturing processes. These substrates play an indispensable role in enhancing the capabilities and longevity of contemporary electronic systems.
What are the Various Types of Ceramic Package Substrates and Their Unique Characteristics?
Embarking on an exploration of ceramic package substrates reveals a kaleidoscope of options, each meticulously crafted to tackle the distinctive challenges posed by electronic applications. Serving as the bedrock for electronic components, these substrates unfold a tapestry of traits tailored to navigate the intricacies of modern devices.
Unraveling the Individuality in Traits and Applications Across Ceramic Substrate Categories:
Alumina (Al2O3):
Attributes: Alumina, an omnipresent ceramic foundation, showcases impressive thermal conductivity and robust mechanical strength.. Its adeptness in electrical insulation seamlessly aligns with the diversity of electronic components.
Applications: Alumina substrates find their footing in power modules, high-frequency devices, and the housing of LEDs.
Aluminum Nitride (AlN):
Attributes: With a penchant for high thermal conductivity, aluminum nitride excels in applications craving efficient heat dissipation. Its innate electrical insulation prowess further enhances its allure.
Applications: AlN substrates stake their claim in high-power electronic circuits, microwave components, and solutions addressing thermal management challenges.
Silicon Carbide (SiC):
Attributes: Striking a delicate balance between high thermal conductivity and exceptional hardness, silicon carbide stands resilient against extreme temperatures, embodying robust thermal stability.
Applications:SiC substrates make their mark in electronic devices operating at elevated temperatures and high power, finding applications in areas like automotive power modules and aerospace components.
Beryllium Oxide (BeO):
Attributes: Beryllium oxide distinguishes itself with high thermal conductivity coupled with remarkable lightweight properties. Its applicability to scenarios demanding both thermal excellence and reduced weight is noteworthy.
Applications: BeO substrates play pivotal roles in aerospace and military realms, where weight holds critical significance, as well as in high-power RF devices.
Glass Ceramic:
Attributes: The amalgamation of glass and ceramic advantages births glass ceramics, offering a delicate blend of reliable electrical insulation and moderate thermal conductivity.
Applications: Glass ceramic substrates find utility in consumer electronics, sensors, and applications requiring a nuanced equilibrium between thermal and electrical attributes.
Understanding the idiosyncrasies of each ceramic substrate type is pivotal in tailoring electronic packaging solutions to meet the unique demands of diverse applications. This approach ensures not just optimal performance but also unwavering reliability in the dynamic landscape of electronic technologies.
How Does Ceramic Package Substrate Differ from Traditional PCBs and IC Package Technologies?
Contrasting Ceramic Package Substrate with IC Package Technologies:
Ceramic package substrates emerge as a distinctive player in electronic packaging, setting themselves apart from traditional IC package technologies.Unlike standard packages, ceramic substrates undergo meticulous engineering to cater to the exacting requirements of high-performance electronic devices. They demonstrate an edge in terms of superior thermal control, robust mechanical integrity, and electrical proficiency.
Departing from the conventions of IC package technologies, which frequently depend on organic substrates, ceramic packages leverage the distinctive properties inherent in materials such as alumina, aluminum nitride, or silicon carbide. This material selection empowers ceramic substrates to excel in efficiently dissipating heat, making them particularly well-suited for applications where thermal considerations are paramount, such as in power modules and high-frequency devices.
Illuminating Contrasts Between Ceramic Substrates and Standard PCBs:
Ceramic substrates deviate from the conventional path tread by standard PCBs in several pivotal aspects. While traditional PCBs commonly feature organic materials like fiberglass or epoxy, ceramic substrates embrace inorganic materials, contributing to their heightened thermal conductivity and mechanical fortitude. This distinction holds significance, especially in electronic devices where efficient thermal dissipation and robust mechanical durability are non-negotiable.
Moreover, the manufacturing processes for ceramic substrates involve a symphony of precision machining, laser drilling, and advanced metallization techniques. These processes not only signify technological sophistication but also pave the way for the creation of intricate, high-density circuitry on ceramic substrates, surpassing the capabilities of traditional PCB manufacturing methods.
In the realm of applications, ceramic substrates ascend to prominence in environments characterized by harsh conditions and elevated power levels, such as in automotive power modules and aerospace components. Standard PCBs, on the contrary, find more common ground in less demanding electronic applications.
In essence, the divergence lies not only in material composition but also in the applied manufacturing processes and the specific performance characteristics catered to by ceramic package substrates. Their distinctive advantages position them as the preferred choice for electronic devices where unwavering reliability, thermal efficiency, and mechanical resilience take center stage.
What Sets Apart Ceramic Package Substrate, PCBs, and PWBs, and How Does it Impact Motherboards?
Distinguishing Ceramic Package Substrate, PCBs, and PWBs:
Unraveling the disparities among ceramic package substrates, printed circuit boards (PCBs), and printed wiring boards (PWBs) is pivotal to understanding their distinct roles in the electronic domain. Ceramic package substrates emerge as specialized components intricately designed to augment thermal efficiency, bolster mechanical resilience, and optimize electrical performance. In contrast to conventional PCBs and PWBs, which often embrace organic materials, ceramic substrates opt for inorganic alternatives like alumina, aluminum nitride, or silicon carbide. This shift in material preference imparts superior thermal conductivity and mechanical robustness to ceramic substrates, rendering them exceptionally well-suited for applications with exacting demands.
Unveiling the Essential Role of Ceramic Substrate in Motherboards:
The fundamental role played by ceramic substrates in shaping the architecture and functionality of motherboards cannot be overstated. Their extraordinary capabilities in thermal management significantly contribute to the overall stability of electronic components nestled on the motherboard. By facilitating efficient heat dissipation—an essential aspect in high-performance computing—ceramic substrates emerge as indispensable contributors. Moreover, the mechanical sturdiness they provide enhances the overall durability of the motherboard, establishing a reliable foundation for the interconnected components. The integration of ceramic technology into motherboards amplifies their performance, reliability, and longevity.
Navigating the Diversity of Substrate, Substrate-like PCBs (SLP), and HDI Substrate:
In the expansive domain of electronic components, decoding the subtleties among substrate, substrate-like PCBs (SLP), and high-density interconnect (HDI) substrates is crucial. Substrates serve as the underpinning for electronic circuits, offering not just mechanical support but also enabling electrical connectivity. SLPs, mirroring the functionality of traditional PCBs, introduce heightened characteristics, often embracing materials like liquid crystal polymer to enhance performance. HDI substrates, renowned for their intricate design and heightened circuit density, carve a niche in compact electronic devices. Each of these components assumes a specific role within electronic systems, collectively contributing to the overall efficiency and functionality of the powered devices.
What Constitutes the Structure of Ceramic Package Substrate, and What are the Advanced Production Technologies?
Unraveling the Composition of Ceramic Package Substrate: Exploring Core Structures
Peeling back the layers of ceramic package substrates unveils the intricate composition essential to electronic devices. These substrates, integral components in the electronic realm, are typically crafted from layers of ceramic materials like alumina or aluminum nitride. These layers are meticulously arranged to form a cohesive unit, with the foundational base layer hosting the etched or deposited circuitry. Further layers are strategically added to enhance complexity and functionality. Comprehending these structures serves as a gateway to understanding the fundamental underpinnings of ceramic package substrates.
Immersing in Innovative Manufacturing Technologies for Ceramic Substrates
Navigating the production landscape of ceramic substrates reveals a realm of innovative manufacturing technologies that contribute to precision and efficiency. Precision machining, laser drilling, and advanced metallization techniques take center stage, shaping intricate circuitry on ceramic surfaces. These cutting-edge technologies ensure high-density configurations and precise alignment, aligning with the exacting demands of contemporary electronics. The integration of such advanced manufacturing technologies is instrumental in achieving the intricate designs necessary for optimal electronic performance.
Advancing Ceramic Package Substrate Production through Enhanced HDI Fabrication Technology
The trajectory of ceramic package substrate production advances with the incorporation of Enhanced High-Density Interconnect (HDI) fabrication technology. This sophisticated approach involves intricate layering and microvia techniques, facilitating increased circuit density and improved signal integrity. HDI fabrication propels substrate capabilities in terms of miniaturization and performance, emerging as a pivotal element in the production of compact and high-functioning electronic devices.
Transforming Manufacturing with the Innovative Semi-Additive Method
Manufacturing processes for ceramic package substrates undergo a transformative phase with the introduction of the Innovative Semi-Additive Method. This method optimizes the deposition of conductive materials, resulting in enhanced precision and reduced material waste. By selectively adding conductive layers only where needed, this approach minimizes environmental impact and production costs while maximizing overall substrate efficiency.
In essence, the production journey of ceramic package substrates not only involves decoding their core structures but also embraces innovative manufacturing technologies, including precision machining, HDI fabrication, and groundbreaking methods such as the Innovative Semi-Additive approach. Together, these advancements contribute to the creation of sophisticated substrates that align seamlessly with the exacting requirements of contemporary electronic devices.
FAQs
What are the main structures of ceramic package substrates?
Ceramic package substrates usually consist of multiple layers of ceramic material arranged to form a cohesive unit. The main structures include a base layer for circuitry, with subsequent layers adding complexity and functionality.
How does High-Density Interconnect (HDI) fabrication technology enhance ceramic substrate production?
HDI fabrication technology involves intricate layering and microvia techniques, increasing circuit density and improving signal integrity. It enhances the capabilities of ceramic substrates, particularly in terms of miniaturization and overall performance.
What is the Innovative Semi-Additive Method in ceramic substrate manufacturing?
The Innovative Semi-Additive Method optimizes the deposition of conductive materials with enhanced precision and reduced material waste. This method selectively adds conductive layers only where needed, minimizing environmental impact and production costs.
What is the role of ceramic substrates in motherboards?
Ceramic substrates play a crucial role in motherboards by providing exceptional thermal management capabilities, efficient heat dissipation, and mechanical robustness. They contribute to the overall stability, performance, and durability of electronic components on the motherboard.
In which electronic devices are ceramic package substrates commonly used?
Ceramic package substrates find applications in electronic devices with demanding requirements, such as high-temperature and high-power environments. Common uses include automotive power modules, aerospace components, and high-frequency devices.
In Conclusion, How Have We Explored the Pivotal Aspects of Ceramic Package Substrate?
Summarizing the Explored Dimensions of Ceramic Package Substrate:
Our journey into the realm of ceramic package substrates has been a comprehensive exploration of these specialized components that hold a central role in the contemporary landscape of electronics. We unraveled the intricate anatomy, providing insights into the fundamental structures that underpin various electronic devices. The distinction from conventional PCBs was emphasized, emphasizing the strategic use of inorganic materials like alumina, aluminum nitride, or silicon carbide, introducing heightened thermal conductivity and mechanical resilience.
Venturing further, we delved into the forefront of manufacturing technologies, where precision machining, laser drilling, and advanced metallization techniques intricately shape the circuitry on ceramic surfaces. The revolutionary Enhanced High-Density Interconnect (HDI) fabrication technology took the spotlight, showcasing its prowess in enhancing circuit density and refining signal integrity. The Innovative Semi-Additive Method emerged as a transformative force, optimizing material deposition with precision and efficacy.
Reflecting on the Transformative Influence of Ceramic Substrates on Modern Electronics:
As we conclude our exploration, it becomes evident that ceramic substrates have ushered in a transformative era within modern electronics. Their unparalleled thermal efficiency, mechanical robustness, and electrical reliability position them as indispensable components in diverse applications, spanning from automotive power modules to aerospace components. With advanced manufacturing technologies at their core, ceramic substrates facilitate the creation of intricate, high-density circuitry, precisely meeting the demanding requirements of contemporary electronic devices.
In essence, the exploration of ceramic package substrates extends beyond mere physical attributes, venturing into the realm of innovation where these components act as catalysts for progress in electronic technologies. Their profound impact on critical components like motherboards, high-power devices, and compact electronic systems underscores their significance in shaping the trajectory of electronic design and functionality.