Ceramic Packaging Substrate Vender .High speed and high frequency material packaging substrate manufacturing. Advanced packaging substrate production process and technology.
In the realm of the semiconductor industry, ceramic packaging substrates emerge as indispensable pillars, offering a sturdy structure for encasing electronic components. Forged from materials such as aluminum oxide or aluminum nitride, these substrates showcase commendable thermal conductivity, mechanical fortitude, and electrical insulation prowess—attributes greatly coveted in scenarios demanding effective heat dissipation, especially in the domain of high-powered electronic devices.
These substrates serve as a stable bedrock for housing semiconductor chips, passive components, and various electronic system elements. Facilitating seamless electrical connections through metal traces or conductive pathways, ceramic packaging substrates ensure smooth communication between components.
In contrast to traditional organic substrates such as fiberglass-reinforced epoxy, ceramic substrates shine with superior thermal performance, heightened reliability, and increased resilience to challenging environmental conditions. These attributes make ceramic packaging substrates especially fitting for demanding electronic applications, including power amplifiers, radio-frequency (RF) devices, and other components where effective thermal management is a critical factor.
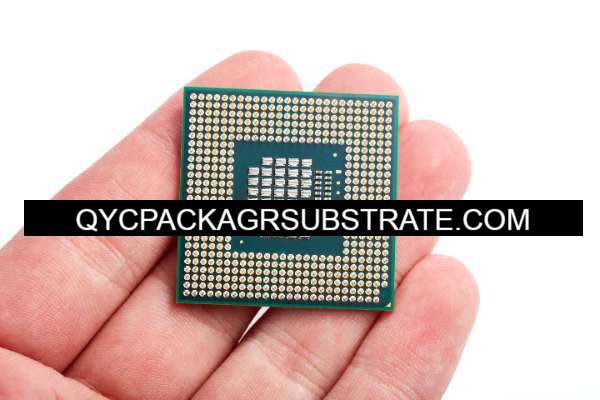
Have You Explored the Intricacies of Ceramic Packaging Substrate?
Delve into the intricate world of ceramic packaging substrates, the unsung heroes at the heart of PCB engineering, wielding a profound impact on the performance and reliability of modern electronic devices. Unraveling their unique properties becomes a journey through the essentials of integrated circuit packaging.
Distinctive Properties of Ceramic Packaging Substrates:
Ceramic Composition:
Material Palette: Forged predominantly from ceramic elements such as alumina or aluminum nitride, these substrates proudly exhibit a diverse array of thermal, mechanical, and electrical characteristics.
Key Advantages: Ceramics, renowned for their impressive thermal conductivity and robust mechanical resilience, serve as the bedrock upon which the reliability of integrated circuits is established.
Thermal Conductivity:
Heat Harmonies: At the heart of these substrates, a standout characteristic takes center stage—their remarkable thermal conductivity, conducting a symphony that elegantly orchestrates the efficient dissipation of heat.This attribute becomes paramount in maintaining optimal performance without succumbing to overheating.
Mechanical Fortitude:
Resilient Architecture: Ceramics, renowned for their mechanical strength, contribute to the robust architecture of packaging substrates. This resilience forms a shield, safeguarding delicate electronic components against physical stresses and external forces.
Electrical Insulation:
Insulating Safeguards: The insulating prowess of ceramics acts as a safeguard, preventing unintended electrical connections between components. This insulation is fundamental in preserving the integrity of the electronic circuitry and averting short circuits.
Dielectric Stability:
Consistent Performance: The stable dielectric properties of ceramics across varying temperatures ensure the unwavering electrical performance of integrated circuits. This stability becomes a cornerstone in guaranteeing reliability.
Essential Roles in Reliability and Performance:
Heat Management:
Guardians Against Overheating: The efficient dissipation of heat emerges as a critical aspect for integrated circuits. Ceramic packaging substrates step in as guardians, thwarting thermal-induced failures and fostering the sustained reliability of electronic devices.
High-Frequency Finesse:
Preservers of Signal Integrity: In the realm of high-frequency applications, ceramics shine by preserving signal integrity. Their low dielectric loss becomes the linchpin, minimizing signal distortion and rendering them indispensable for RF/microwave circuits.
Resilience to Harsh Environments:
Defenders Against Challenges: Ceramic substrates exhibit a remarkable resistance to environmental challenges—be it temperature fluctuations, humidity, or chemical exposures. This robustness becomes a shield, enhancing the reliability of electronic devices across diverse settings.
Space-Efficient Designs:
Architects of Miniaturization: The mechanical strength and thermal efficiency of ceramics contribute to the ongoing trend of miniaturization and high-density packaging in modern electronics. This feature is particularly advantageous for portable devices and applications with spatial constraints.
In summary, ceramic packaging substrates emerge as silent architects, crafting a foundation for the reliability and optimal functioning of integrated circuits. Their amalgamation of thermal prowess, mechanical robustness, and electrical insulation positions them at the forefront of PCB engineering, steering the course of electronic advancements across various industries.
What Functions Do Ceramic Packaging Substrates Serve?
Ceramic packaging substrates emerge as versatile contributors in the realm of high-performance electronics, seamlessly blending various roles to optimize functionality. Beyond providing a sturdy foundation for electronic components, these substrates act as electrical insulators, proficiently manage heat dissipation, and exhibit stability in dielectric properties. Let’s navigate through the diverse functions they undertake:
Robust Structural Support:
Stalwart Foundation: Ceramic packaging substrates stand as stalwart foundations, offering robust structural support that shields delicate components from physical stress, vibrations, and external forces.
Electrical Insulation Shield:
Guardians of Integrity: Acting as electrical insulators, they function as guardians, preventing unintended electrical connections and ensuring the unwavering integrity of the electronic circuitry.
Thermal Management Virtuosos:
Heat Symphony Conductors: With exceptional thermal conductivity, ceramic substrates conduct a symphony of efficient heat dissipation. They assume a pivotal role in averting overheating, thereby fostering sustained performance and prolonging the operational lifespan of electronic devices.
Dielectric Stability Pioneers:
Consistent Performance Anchors: Exhibiting stable dielectric properties across varying temperatures, ceramic substrates anchor consistent electrical performance, resilient even in the face of environmental fluctuations.
Custodians of Signal Integrity:
Preservers of Fidelity: In high-frequency applications, these substrates become custodians of signal integrity.With minimal dielectric loss, these substrates become maestros in minimizing signal distortion, allowing the seamless transmission of high-frequency signals with unwavering fidelity.
Resilience to Environmental Challenges:
Environmental Allies: Ceramic substrates showcase resilience in harsh environmental conditions, whether facing temperature extremes, humidity, or exposure to chemicals. This adaptability enhances the reliability of electronic devices, particularly in challenging operational settings.
Enablers of Miniaturization:
Efficient Space Navigators: Contributing to the ongoing trend of miniaturization and high-density packaging, ceramic substrates become efficient space navigators. Their mechanical robustness and thermal efficiency are particularly advantageous for compact devices and applications with spatial constraints.
In essence, ceramic packaging substrates become the unsung heroes in the orchestra of electronic functionalities, seamlessly blending their varied functions to ensure the reliability, efficiency, and longevity of high-performance electronic applications across diverse environments.
What Types of Ceramic Packaging Substrates Exist?
Embark on an exploration of the multifaceted world of ceramic packaging substrates, where a diverse array of materials and designs unfolds, meticulously crafted to meet the intricate demands of electronic applications. From the stalwart alumina-based substrates to the avant-garde possibilities presented by aluminum nitride, engineers navigate a rich tapestry of choices, each intricately designed for specific electronic requisites.
Alumina-Based Substrates:
Material Harmony: Predominantly shaped from alumina (aluminum oxide), these substrates seamlessly blend thermal conductivity, mechanical robustness, and electrical insulation.
Versatility in Action: Alumina-based substrates stand as unwavering bedrocks for integrated circuits, seamlessly intertwining with a plethora of electronic devices.
Aluminum Nitride Substrates:
Material Pinnacle: Taking the lead, aluminum nitride emerges with exceptional thermal conductivity and minimal dielectric loss.
Application Spotlight: Crafted for settings where precise thermal regulation and steadfast signal integrity are of utmost importance, aluminum nitride substrates emerge into the spotlight. Their excellence is particularly pronounced in the intricate domain of high-frequency circuits.
Silicon Carbide (SiC) Substrates:
Material Fusion: Silicon carbide, a compelling fusion of silicon and carbon, takes center stage as the elemental foundation shaping these substrates.
Dominance in Traits: SiC substrates carve a niche with a remarkable fusion of thermal conductivity and formidable resilience to elevated temperatures, establishing them as a reliable choice for applications thriving in the most unforgiving thermal environments.
Beryllium Oxide (BeO) Substrates:
Material Endurance: Beryllium oxide, renowned for high thermal conductivity, takes center stage.
Applications Unveiled: In demanding scenarios where efficient heat dissipation is paramount—such as high-power electronic devices—BeO substrates play a pivotal role.
Zirconia Substrates:
Material Brilliance: Zirconia, a ceramic virtuoso, becomes the cornerstone of these substrates.
Outstanding Traits: Zirconia-based substrates showcase resilience in high-temperature environments, carving a niche for themselves in applications facing challenging thermal conditions.
Titanate Ceramic Substrates:
Material Precision: Titanate ceramics, precision-engineered, play a pivotal role as the foundational material.
Distinctive Characteristics: Recognized for their exacting dielectric properties, titanate ceramic substrates find applications where electrical insulation is a non-negotiable requirement.
Hybrid Ceramic Substrates:
Material Fusion: Hybrid substrates weave a narrative of diversity, seamlessly merging various ceramic materials.
Versatile Ensemble: By harmonizing the strengths of materials like alumina, aluminum nitride, or others, hybrid ceramic substrates offer a versatile blend of thermal, mechanical, and electrical attributes.
In this intricate symphony of ceramic packaging substrates, engineers navigate a vast spectrum of possibilities, selecting substrates that resonate harmoniously with the unique demands of their electronic compositions. Whether optimizing thermal performance, preserving signal fidelity, or confronting the challenges of high-power applications, the diverse options in ceramic substrates provide an expansive canvas for tailored solutions.
How Do Ceramic Packaging Substrates Differ from PCBs?
Embark on an exploration into the realm of electronic design, where the distinctions between ceramic packaging substrates and traditional PCBs carve a unique narrative. From the elemental composition to their roles in motherboards, SLP, and HDI substrates, let’s unravel how these components contribute distinctly to the performance and adaptability of electronic systems.
Elemental Composition:
Ceramic Packaging Substrates: Forged from ceramics like alumina, aluminum nitride, or silicon carbide, these substrates encapsulate distinctive characteristics, boasting remarkable thermal conductivity and serving as adept electrical insulators.
Traditional PCBs: Guiding electronic pathways with the use of laminate materials, frequently embracing fiberglass-reinforced epoxy, traditional PCBs choreograph a seamless equilibrium between electrical efficacy and mechanical fortitude.
Thermal Dynamics:
Ceramic Packaging Substrates: Emerge as thermal conductive virtuosos, showcasing an extraordinary ability to dissipate heat efficiently, especially in high-power applications.
Traditional PCBs: While proficient in heat management, traditional PCBs may not match the thermal conductivity prowess exhibited by their ceramic counterparts.
Mechanical Fortitude:
Ceramic Packaging Substrates: Flaunting a reputation for mechanical robustness, ceramic substrates become stalwart supporters, offering a resilient structure for electronic components.
Traditional PCBs: Demonstrating mechanical strength, traditional PCBs rely on the specific laminate materials employed, distinct from the robustness of ceramics.
Electrical Insulation Mastery:
Ceramic Packaging Substrates: Function as natural electrical insulators, forming an impenetrable shield against unintended connections and upholding the sanctity of circuitry.
Traditional PCBs: Provide electrical insulation through chosen laminate materials, exhibiting properties that may vary compared to the innate insulation capabilities of ceramics.
Role in Motherboards:
Ceramic Packaging Substrates: Secure a place in specific sections of motherboards, contributing a thermal performance edge and enhanced reliability.
Traditional PCBs: Motherboards choreograph a harmonious ensemble of varied PCBs, each meticulously crafted to meet the distinct requirements of its assigned domain.
SLP (Substrate-Like PCBs) and HDI (High-Density Interconnect) Substrates:
Ceramic Packaging Substrates: Tailor-made for SLP and HDI applications, marrying thermal efficiency with a compact design.
Traditional PCBs: Integral to SLP and HDI scenarios, traditional PCBs introduce material variety, distinct from the ceramic landscape.
In essence, the narrative unfolds in the subtleties of material composition, thermal dynamics, and mechanical resilience. Ceramic packaging substrates shine as thermal virtuosos, especially in environments demanding heat dissipation and reliability. Traditional PCBs, versatile in their own right, may not encapsulate the distinctive advantages brought forth by ceramics in the intricate tapestry of high-performance electronic designs.
What Constitutes the Structure and Production Technologies of Ceramic Packaging Substrates?
The structure and production technologies of ceramic packaging substrates encompass intricate layers and advanced manufacturing processes. Let’s delve into the key elements that constitute the structure of these substrates and the technologies involved in their production:
Structure of Ceramic Packaging Substrates:
Ceramic Substrate:
Material Composition: At the core of the structure lies the ceramic substrate, crafted from materials such as alumina, aluminum nitride, silicon carbide, or alternative ceramics, serving as the foundational layer.
Purpose: The ceramic substrate provides the structural support and acts as a base for the entire assembly.
Conductor Traces:
Material: Typically composed of metal, such as copper, conductor traces are patterned on the ceramic substrate.
Function: Conductor traces facilitate the flow of electrical signals between various components on the substrate.
Dielectric Layers:
Material: Dielectric layers, crafted from materials exhibiting minimal electrical conductivity, serve as insulating barriers, effectively isolating and segregating conductor traces on the substrate.
Purpose: These strata serve a dual purpose: thwarting unintended electrical connections and actively bolstering the comprehensive electrical insulation of the substrate.
Solder Mask:
Material: Solder mask is a protective layer made of epoxy-based material.
Function: Applied over the conductor traces, solder mask prevents solder bridges during the assembly process and protects the underlying layers.
Via Structures:
Construction: Via structures are openings in the substrate that connect different layers, allowing signals to pass vertically through the substrate.
Purpose: Vias enable the creation of complex, multilayered circuits and connections.
Surface Finish:
Material: The surface finish, often made of metals like gold or tin, enhances the solderability of the substrate.
Function: It ensures proper bonding during the assembly of electronic components onto the substrate.
Production Technologies:
Enhanced HDI Fabrication:
Description: Delving into High-Density Interconnect (HDI) technology unveils a sophisticated tapestry of layered intricacies and minute vias, fostering heightened component density on the substrate.
Advantages:HDI fabrication stands as the catalyst for crafting ceramic substrates that are not only high-performance but also compact, perfectly tailored for the demands of miniaturized electronic devices.
Semi-Additive Process:
Description: Semi-additive processes involve selectively adding material to the substrate rather than subtracting it, allowing for precise pattern formation.
Advantages: This method enhances the accuracy of conductor trace patterns, contributing to the miniaturization and optimization of electronic circuits.
Advanced Material Deposition:
Description: Modern techniques involve advanced methods of depositing ceramic materials onto substrates, ensuring uniformity and precision.
Advantages: Improved material deposition techniques enhance the thermal and electrical properties of ceramic substrates.
Laser Drilling:
Description: Laser drilling emerges as the technique of choice for meticulously crafting precise via structures within ceramic substrates.
Advantages:Leveraging laser drilling, manufacturers achieve unparalleled precision in crafting diminutive-diameter vias, thereby enabling the fabrication of intricate and high-performance ceramic substrates.
Cofiring Technology:
Description: Cofiring involves simultaneously firing the ceramic substrate and the components, such as resistors or capacitors, in a single process.
Advantages: Cofiring technology streamlines the production process, leading to enhanced integration and reliability of components on the substrate.
In summary, the structure of ceramic packaging substrates involves multiple layers working together to create a functional and reliable platform for electronic components. The production technologies, including enhanced HDI fabrication, semi-additive processes, advanced material deposition, laser drilling, and cofiring, contribute to the precision and efficiency of manufacturing these substrates.
Have You Explored the Frequently Asked Questions (FAQs) About Ceramic Packaging Substrates?
How are Ceramic Packaging Substrates Manufactured?
The intricate manufacturing processes of ceramic substrates involve advanced techniques like enhanced HDI fabrication, semi-additive methods, laser drilling, and cofiring technology. These processes ensure precision and efficiency in creating intricate substrate structures.
In Which Applications are Ceramic Packaging Substrates Widely Used?
Ceramic substrates find applications across a spectrum of electronic devices, including high-power applications, RF/microwave circuits, LED modules, and any scenario demanding efficient heat dissipation and electrical insulation.
How Do Ceramic Packaging Substrates Contribute to Thermal Management?
The exceptional thermal conductivity inherent in ceramic substrates allows for efficient heat conduction and dissipation. This characteristic prevents overheating, ensuring sustained optimal performance of electronic components.
What challenges are associated with using ceramic packaging substrates?
Cost and brittleness are potential challenges. Ceramic substrates can be more expensive to manufacture than some organic alternatives, and their brittleness may require careful handling during assembly.
Conclusion
In conclusion, ceramic packaging substrates emerge as indispensable components in the ever-evolving landscape of electronic devices. Crafted from materials like alumina, aluminum nitride, and silicon carbide, these substrates provide a robust structural foundation while contributing significantly to thermal management and electrical insulation.
Their distinction from traditional PCBs lies in material composition, thermal conductivity, and mechanical strength, making ceramics a preferred choice for applications demanding superior thermal performance, particularly in high-power scenarios. The diverse array of substrates, from alumina-based to hybrid options, caters to specific thermal and electrical requirements, showcasing versatility in electronic design.
The multifaceted functions of ceramic substrates extend beyond structural support, encompassing roles as adept electrical insulators and managers of thermal efficiency. Advanced manufacturing processes such as enhanced HDI fabrication, laser drilling, and cofiring technology ensure the precision and efficiency needed to create intricate substrate structures.
Laser drilling, with its precision prowess, stands out as a key contributor to substrate performance, enabling the creation of small-diameter vias crucial for intricate circuit designs. Ceramic substrates find applications across a spectrum of electronic devices, from high-power applications to RF/microwave circuits and LED modules, showcasing their adaptability and reliability.
The exceptional thermal conductivity embedded in ceramic substrates ensures efficient heat conduction and dissipation, safeguarding electronic components from overheating and contributing to optimal device performance. Their resistance to harsh environmental conditions further solidifies their suitability for deployment in challenging operational settings.