Advance Ceramic Substrate Vender. the Ceramic Package Substrate will be made with ALUMINUM AI2O3 base materials. or other types Ceramic base materials.
Advanced ceramic packaging substrates stand as specialized materials meticulously designed for encapsulating electronic components, with a pronounced focus on semiconductor devices. These substrates assume a pivotal role by furnishing structural support, electrical insulation, and effective thermal management for integrated circuits and a myriad of electronic components. The utilization of advanced ceramics in packaging substrates bequeaths distinct advantages, including heightened thermal conductivity, exceptional electrical insulation properties, and formidable mechanical strength. Here, we delve into key attributes and applications associated with advanced ceramic packaging substrates:
Optimized Thermal Governance: Advanced ceramic substrates excel in deftly regulating temperature, facilitating the dissipation of heat emanating from electronic components. This proves indispensable for sustaining the optimal operating temperature of integrated circuits, mitigating performance degradation, and ensuring overall reliability.
Inherent Electrical Insularity: Ceramics inherently boast excellent insulating properties, a pivotal characteristic in forestalling unintended electrical interactions among diverse components within a circuit. This innate electrical insulation minimizes signal interference, contributing to the steadfast operation of electronic devices.
Exemplary Mechanical Tenacity: Renowned for their robust mechanical strength, ceramics aptly buttress and shield delicate semiconductor components throughout the stages of manufacturing, assembly, and operational use. This mechanical fortitude enhances the overall durability and reliability of electronic devices.
Adaptability to Miniaturization: In sync with the ongoing trend of electronic devices diminishing in size and escalating in complexity, there is an escalating demand for packaging solutions in resonance with the trajectory of miniaturization. Advanced ceramic substrates, endowed with precision manufacturing capabilities, accommodate fine features and stringent tolerances, facilitating the integration of smaller and more densely packed components.
Chemical Resilience: Ceramics, by and large, exhibit chemical resilience, constituting a protective bulwark against corrosion and environmental exigencies. This resilience contributes to the protracted longevity and heightened reliability of electronic devices, especially in challenging operational environments.
Tailored Customization: Advanced ceramic packaging substrates offer a high degree of customization to meet specific design prerequisites. This adaptability empowers engineers to finetune the substrate’s properties, aligning them with the distinctive demands of diverse applications, spanning aerospace, automotive, telecommunications, and consumer electronics.
Materials recurrently enlisted in advanced ceramic packaging substrates encompass alumina (aluminum oxide), aluminum nitride, silicon carbide, and beryllium oxide. The material selection hinges on the specific exigencies and requirements intrinsic to the application.
In summation, advanced ceramic packaging substrates occupy a central role in safeguarding the efficiency, reliability, and sustained functionality of electronic devices, particularly within the dynamic realm of semiconductor packaging.
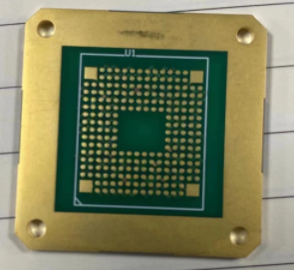
How do Advance Ceramic Packaging Substrates Operate?
The functionality of advanced ceramic packaging substrates is intricately woven through a symphony of structural resilience, thermal equilibrium, and electrical insulation, offering indispensable support and safeguarding for electronic components, particularly in the realm of semiconductor devices. Let’s unravel the distinctive mechanisms that define how these substrates operate:
Structural Stamina:
Material Vigor: Meticulously chosen from the repertoire of advanced ceramics like alumina, aluminum nitride, silicon carbide, or beryllium oxide, these substrates embody a robust mechanical strength. This strength forms the bedrock for providing unwavering structural support during the intricate phases of manufacturing, assembly, and the lifecycle of semiconductor components.
Thermal Symbiosis:
Elevated Thermal Conductivity: The hallmark of advanced ceramics lies in their impressive thermal conductivity. This inherent trait empowers these substrates to adeptly navigate and disperse the thermal currents emanating from electronic components. The adept dissipation of heat is paramount in averting overheating conundrums and preserving the optimal operational integrity of integrated circuits.
Electrical Seclusion:
Innate Electrical Insulation: Ceramics, by their very nature, boast stellar electrical insulation properties. This innate quality assumes a pivotal role in thwarting unintended electrical liaisons among an array of components within a circuit. This minimization of signal interference becomes a linchpin in ensuring the consistent and dependable performance of electronic devices.
Miniaturization Ally:
Precision Craftsmanship: In tandem with the ongoing trend of electronic devices embracing miniaturization, advanced ceramic substrates align seamlessly with this evolution through precision manufacturing methodologies. This precision facilitates the integration of diminutive and densely packed electronic components, aligning harmoniously with the ever-evolving landscape of electronic design.
Chemical Tenacity:
Corrosion Resilient Nature: Many advanced ceramics boast a commendable stability in the face of chemical challenges, standing resilient against corrosion and environmental adversities. This inherent resilience amplifies the endurance and reliability of electronic devices, particularly when subjected to the rigors of demanding or adverse operational conditions.
Tailored Versatility:
Customized Calibration: Advanced ceramic packaging substrates extend a high degree of adaptability through meticulous customization. Engineers wield the power to finely calibrate the material composition and manufacturing processes, precisely aligning the substrate’s properties with the nuanced demands of specific design prerequisites. This adaptability empowers the substrates to seamlessly integrate into diverse applications, spanning the domains of aerospace, automotive, telecommunications, and consumer electronics.
In essence, advanced ceramic packaging substrates operate as a harmonious amalgamation of strength, thermal efficacy, and electrical insulation. They play an instrumental role in orchestrating efficient heat dissipation, quelling electrical interference, and elevating the overall reliability and longevity of electronic devices. The nuanced performance pivots on the judicious selection of ceramic materials, their inherent attributes, and the artful calibration to meet the distinctive demands of the intended application.
What Types of Advance Ceramic Packaging Substrates Exist?
Certainly! Advanced ceramic packaging substrates encompass a diverse range of materials, each tailored to specific applications within electronic packaging. The choice of substrate material plays a critical role in determining thermal conductivity, electrical performance, and overall reliability. Here are some types of advanced ceramic packaging substrates and the impact of different materials on key properties:
Alumina (Aluminum Oxide) Substrates:
Material Composition: Inorganic
Key Characteristics:
Thermal Conductivity: High thermal conductivity for efficient heat dissipation.
Electrical Performance: Excellent electrical insulation properties.
Reliability: Mechanical robustness and chemical stability contribute to overall reliability.
Applications: Commonly used in power electronic modules, LED packages, and scenarios prioritizing reliability.
Aluminum Nitride (AlN) Substrates:
Material Composition: Inorganic
Key Characteristics:
Thermal Conductivity: Exceptional thermal conductivity, facilitating effective heat dissipation.
Electrical Performance: Solid electrical insulation, making it suitable for high-power electronics.
Reliability: Resilient in harsh environments, enhancing overall reliability.
Applications: Thrives in high-power electronics, microwave components, and as substrates for LEDs.
Silicon Carbide (SiC) Substrates:
Material Composition: Inorganic
Key Characteristics:
Thermal Conductivity: Outstanding thermal conductivity, especially at elevated temperatures.
Electrical Performance: High-temperature stability, suitable for high-power applications.
Reliability: Stands robust in demanding environments, ensuring prolonged durability.
Applications: Applied in automotive power modules, aerospace systems, and high-temperature electronic setups.
Organic Substrates (e.g., FR-4):
Material Composition: Organic
Key Characteristics:
Thermal Conductivity: Exhibits comparatively lower thermal conductivity than inorganic counterparts.
Electrical Performance: Generally solid, though it may not match the insulation prowess of certain inorganic substrates.
Reliability: Typically chosen for less demanding applications due to its lower thermal performance.
Applications: Finds utility in consumer electronics and applications with lower heat intensity.
Beryllium Oxide (BeO) Substrates:
Material Composition: Inorganic
Key Characteristics:
Thermal Conductivity: Possesses high thermal conductivity despite its lightweight nature.
Electrical Performance: Exhibits excellent electrical insulation properties.
Reliability: Suited for high-frequency and microwave applications due to its unique combination of properties.
Applications: Commonly deployed in high-frequency and microwave applications, as well as compact electronic devices.
Glass Ceramic Substrates:
Material Composition: Inorganic
Key Characteristics:
Thermal Conductivity: Presents moderate thermal conductivity, balanced with other favorable properties.
Electrical Performance: Offers good electrical insulation with precision machinability.
Reliability: Frequently chosen for applications requiring precision and thermal stability.
Applications: Serves in sensors, microelectronics, and situations demanding precision.
The selection of advanced ceramic packaging substrates involves a nuanced consideration of the specific requirements of each application. Inorganic substrates often excel in high-performance scenarios, while organic substrates find their place in less demanding applications. Glass ceramics offer a balanced solution for applications requiring a harmonious blend of thermal, electrical, and precision-related characteristics.
How do Advance Ceramic Packaging Substrates Differ from Traditional PCBs?
Dive into the distinctions between advanced ceramic packaging substrates and traditional Printed Circuit Boards (PCBs), navigating through their diverse material compositions, thermal conductivities, electrical performances, mechanical attributes, applications, and manufacturing methodologies.
Material Composition:
Advanced Ceramic Packaging Substrates:
Crafted from inorganic materials such as alumina, aluminum nitride, silicon carbide, and glass ceramics.
Boast a trifecta of high thermal conductivity, stellar electrical insulation, and mechanical robustness.
Traditional PCBs:
Fashioned from organic materials, chiefly fiberglass-reinforced epoxy resin (FR-4).
May feature copper layers to facilitate electrical conduction.
Thermal Conductivity:
Advanced Ceramic Packaging Substrates:
Exhibit heightened thermal conductivity, facilitating efficient heat dissipation, especially apt for power electronics.
Traditional PCBs:
Possess lower thermal conductivity, potentially restricting their prowess in dissipating heat effectively.
Electrical Performance:
Advanced Ceramic Packaging Substrates:
Showcase an excellent repertoire of electrical insulation, particularly tailored for high-power and high-frequency applications.
Traditional PCBs:
Furnish reliable electrical insulation but may not match the prowess of advanced ceramics in demanding scenarios.
Mechanical Properties:
Advanced Ceramic Packaging Substrates:
Feature a robust profile of high mechanical strength and stability, ensuring durability in challenging environments.
Traditional PCBs:
Possess commendable mechanical properties but might lack the ruggedness of ceramics in extreme conditions.
Applications:
Advanced Ceramic Packaging Substrates:
Primarily find their niche in high-performance electronic realms, such as power modules and components navigating harsh conditions.
Traditional PCBs:
Widespread adoption in standard electronic devices where stringent thermal and mechanical demands take a back seat.
Manufacturing Processes:
Advanced Ceramic Packaging Substrates:
Encompass specialized ceramic processing techniques, featuring the likes of sintering and precision machining.
Might incorporate co-firing of metal layers to facilitate electrical connectivity.
Traditional PCBs:
Undergo manufacturing through a series of processes including photolithography, etching, and the application of a solder mask.
In essence, the world of advanced ceramic packaging substrates and traditional PCBs unfolds with nuances in material properties, thermal dynamics, electrical attributes, mechanical resilience, applications, and the intricacies of manufacturing. Advanced ceramics shine in the crucible of demanding electronic applications, while traditional PCBs hold sway in the realm of standard electronic devices.
What is the Structure and Production Technologies of Advance Ceramic Packaging Substrates?
Unlocking the intricacies of advanced ceramic packaging substrates involves navigating their varied structures and the nuanced technologies employed in their production. The structural designs differ based on the ceramic material, showcasing layered configurations, composite structures, or multilayered compositions, each tailored for specific functionalities.
Structure of Advanced Ceramic Packaging Substrates:
Layered Complexity:
Inorganic Ceramics (e.g., Alumina, Aluminum Nitride, Silicon Carbide):
Feature a stratified architecture with multiple ceramic layers.
Integration of metal traces within the ceramic layers facilitates electrical connectivity.
Additional layers cater to distinct functions like insulation or heat dissipation.
Harmony in Composition:
Glass Ceramic Substrates:
Embrace a composite structure that harmonizes glass and ceramic materials.
This blend achieves equilibrium in thermal, electrical, and mechanical properties.
The composite design allows for precision machining and customizable configurations.
Strategic Layering:
Beryllium Oxide (BeO) Substrates:
Crafted with a multilayered approach to amplify thermal and electrical efficiency.
Leveraging the high thermal conductivity of beryllium oxide, these substrates excel in dissipating heat effectively.
Production Technologies:
Refinement in Powder:
Raw Material Artistry:
Meticulous selection and preparation of ceramic powders.
Treatments like milling and blending sculpt the powders into their desired composition.
Forming Prowess:
The shaped green bodies emerge through forming techniques such as pressing or casting.
Green bodies serve as the initial canvas, embodying the substrate’s foundational structure.
Transformation in Sintering:
Densification Drama:
Green bodies undergo the transformative act of sintering.
This high-temperature process fuses ceramic particles, birthing a denser and more resilient structure.
Shrinkage Symphony:
Precision in controlling sintering conditions is paramount to manage shrinkage and preserve the substrate’s intended dimensions.
Innovative Additions (Optional):
Layering with 3D Precision:
In certain scenarios, advanced ceramic substrates come to life through additive manufacturing, including 3D printing.
This innovative approach allows for intricate designs and tailored configurations.
Metallization Magic (Optional):
Metallic Infusion:
Metal layers make their appearance through techniques like thin-film deposition or sputtering.
These additions enhance electrical conductivity, contributing to the substrate’s functionality.
Co-Firing Collaboration (Optional):
Simultaneous Fusion:
Co-firing witnesses the simultaneous fusion of ceramic and metal layers.
This synchronized act ensures a robust and enduring bond between the two elements.
Precision in Machining:
Post-Sintering Sculpting:
Post-sintering, substrates undergo precision machining, sculpting them to their final dimensions and surface finish.
CNC machining and laser precision contribute to the substrate’s refined form.
Guardians of Quality:
Rigorous Vigilance:
Robust testing protocols, including dimensional scrutiny, thermal conductivity assessments, and electrical tests, stand as guardians of the substrate’s quality.
The production odyssey of advanced ceramic packaging substrates entails a fusion of material expertise, engineering finesse, and specialized manufacturing choreography. The selection of production methodologies dances intricately with the chosen ceramic material, shaping substrates with tailored characteristics.
Where do Advance Ceramic Packaging Substrates Fit in Chip Package Technology Classification?
Step into the intricate world of chip packaging technologies, where advanced ceramic packaging substrates seamlessly integrate, shaping the landscape across diverse classifications. Crafted from materials like alumina, aluminum nitride, and silicon carbide, these substrates play a pivotal role in sculpting the architecture of semiconductor devices. Let’s unravel the synergy between these advanced ceramics and different chip packaging technologies:
Chip Packaging Technologies:
Surface Mount Technology (SMT):
Ceramic Mastery:
At the heart of surface mount packages, advanced ceramic substrates provide a robust foundation for affixing ICs onto printed circuit boards (PCBs).
Applications:
Pervasive in consumer electronics and compact electronic marvels.
Through-Hole Technology (THT):
Adaptive Ceramics:
Certain ceramic substrates gracefully adapt to through-hole technology, accommodating component leads for meticulous soldering.
Applications:
A niche presence in applications demanding precision.
Ball Grid Array (BGA):
Efficiency Unleashed:
Advanced ceramic substrates take center stage in BGA packaging, delivering the thermal and electrical prowess required for seamless heat dissipation.
Applications:
Dominant in high-performance realms such as microprocessors and GPUs.
Quad Flat Package (QFP):
Ceramic Empowerment:
Stepping into the arena of high-density QFP packages, ceramic substrates assert their dominance for superior thermal management.
Applications:
The go-to choice for microcontrollers and memory chips.
Chip-on-Board (COB):
Direct Liaison with Ceramics:
Ceramic substrates play a foundational role in the COB approach, facilitating the direct mounting of ICs.
Applications:
A preferred option where space efficiency and miniaturization take the spotlight.
System in Package (SiP):
Versatile Ceramic Canvas:
Within the realm of SiP, ceramic substrates provide a canvas for seamlessly integrating diverse functionalities into a unified package.
Applications:
A linchpin in complex systems like mobile devices and IoT applications.
3D Package Technology:
Ceramic Ascent:
Advanced ceramics elevate 3D packaging, enabling the vertical stacking of multiple IC layers and heralding a new era of component density.
Applications:
Deployed in advanced computing systems and data centers.
Advantages of Ceramic Substrates:
Thermal Prowess:
The elevated thermal conductivity of ceramic substrates ensures the proficient dissipation of heat, a critical factor in high-performance applications.
Electrical Insulation Mastery:
Exceptional electrical insulation properties shield against signal interference, elevating the overall reliability quotient.
Robust Mechanical Fortitude:
The mechanical robustness of ceramics emerges as a stalwart, ensuring durability even in the face of challenging environments.
Enabling Miniaturization:
A key contributor to the ongoing saga of miniaturization, advanced ceramics empower the creation of compact, efficient designs.
In essence, advanced ceramic packaging substrates emerge as orchestral conductors in the symphony of chip packaging technologies, contributing significantly to the efficiency, reliability, and relentless pursuit of miniaturization in semiconductor devices across an array of applications.
FAQs: Deciphering Advance Ceramic Packaging Substrates
What Are the Key Manufacturing Processes in Crafting Advanced Ceramic Substrates?
The production journey involves powder processing, forming, sintering, and potential augmentations like metallization, co-firing, and precision machining. These intricate steps are orchestrated to attain specific material properties.
In What Way Do Ceramic Substrates Contribute to Thermal Regulation?
The elevated thermal conductivity of ceramic substrates plays a pivotal role in efficiently dispersing heat from electronic components. This quality is instrumental in preventing overheating and ensuring the steadfast reliability of electronic devices.
Are Environmental Considerations Integral to Advanced Ceramic Packaging Substrates?
Renowned for their stability in challenging environments, advanced ceramics find a natural fit in aerospace, automotive, and industrial settings. Their durability becomes a cornerstone for the endurance of electronic devices.
Can Advanced Ceramic Substrates be Tailored to Specific Applications?
Absolutely, customization is within reach. Advanced ceramic substrates can be tailored based on unique application requirements, accommodating variations in material composition, dimensions, and additional features to meet specific needs.
What Role Do Advanced Ceramic Substrates Play in 3D Package Technology?
In the realm of 3D packaging, advanced ceramic substrates take center stage by facilitating the vertical stacking of multiple IC layers. This elevates component density and enhances performance, particularly in advanced computing systems and data centers.
Conclusion
In summary, the realm of advanced ceramic packaging substrates is a dynamic tapestry of innovation, precision, and adaptability. These specialized materials, whether hailing from alumina, aluminum nitride, silicon carbide, or other ceramic variants, play a pivotal role in sculpting the electronic packaging landscape. Navigating the intricate details reveals several key insights:
Diverse Array of Types:
Advanced ceramic substrates encompass a spectrum of materials, including alumina, aluminum nitride, silicon carbide, and glass ceramics. Each variant brings forth distinct thermal, electrical, and mechanical properties tailored to specific applications.
Mastery in Thermal Management:
The inherent high thermal conductivity of these substrates emerges as a critical asset. It adeptly disperses heat from electronic components, ensuring optimal performance and reliability, particularly in high-power scenarios.
Excellence in Electrical Insulation:
Advanced ceramic substrates showcase prowess in providing electrical insulation, safeguarding against signal interference. This quality is foundational in applications where precise electrical performance is non-negotiable.
Versatility Across Applications:
From high-performance electronics like power modules and microprocessors to challenging environments in aerospace, automotive, and medical electronics, advanced ceramic substrates prove their worth. Their reliability and durability make them indispensable in diverse applications.
Customization and Flexibility:
The adaptability of these substrates shines through in their capacity to be tailored for specific applications. Whether adjusting material composition, dimensions, or incorporating additional features, customization ensures a seamless fit for a variety of electronic needs.
Intricate Manufacturing Journey:
The odyssey from powder processing, forming, and sintering to optional steps like metallization and co-firing is a meticulous manufacturing process. This intricate journey guarantees that substrates meet stringent quality standards and performance criteria.
Integral Role in Technological Advancements:
Advanced ceramic substrates play pivotal roles across various chip packaging technologies, from the intricacies of Surface Mount Technology (SMT) to the cutting-edge dimensions of 3D Package Technology. Their contributions to thermal regulation, miniaturization, and overall reliability position them as key enablers in advancing electronic systems.
In essence, advanced ceramic packaging substrates embody a seamless fusion of material science, precision engineering, and adaptive solutions. As technology continues its relentless evolution, these substrates stand resiliently as pillars supporting the escalating demands for efficiency, reliability, and miniaturization in the ever-evolving electronic devices landscape.