Ceramics Substrate Manufacturer
We are a professional Ceramics Substrate Manufacturer, we mainly produce ultra-small bump pitch substrate, ultra-small trace and spacing packaging substrate and PCBs.
Ceramics substrates are the unsung heroes of modern electronics, providing a sturdy and reliable foundation for a myriad of electronic components. Crafted from advanced ceramic materials like alumina or aluminum nitride, these substrates offer a trifecta of essential qualities: exceptional thermal conductivity, superb electrical insulation, and robust mechanical stability.
Imagine them as the silent guardians beneath the glitz of electronic devices, efficiently whisking away heat generated by power-hungry components to maintain optimal performance. Their electrically insulating nature ensures that delicate circuits and components remain safe from short circuits and interference, safeguarding the integrity of the entire system. Meanwhile, their steadfast rigidity provides structural support, ensuring longevity and durability in the face of constant use and environmental challenges.
From high-powered semiconductors to delicate sensors, ceramics substrates play a vital role in enabling the functionality and reliability of electronic devices across industries. They embody a fusion of precision engineering and material science, quietly empowering the electronic marvels that have become indispensable in our daily lives.
What is a Ceramics Substrate?
A ceramics substrate refers to a material, typically made of ceramic compounds like alumina (Al2O3) or aluminum nitride (AlN), that is used as a base or foundation for various electronic components. These substrates provide a stable, thermally conductive, and electrically insulating platform for mounting semiconductor devices, integrated circuits (ICs), and other electronic components.
Ceramics substrates offer several advantages in electronic applications:
- Thermal Management: Ceramics have excellent thermal conductivity, which helps dissipate heat generated by electronic components. This is crucial for maintaining the performance and reliability of electronic devices.
- Electrical Insulation: Ceramics are electrical insulators, which means they do not conduct electricity. This property helps prevent short circuits and interference between different components mounted on the substrate.
- Mechanical Stability: Ceramics substrates are rigid and mechanically stable, providing support and protection to the mounted electronic components.
- Chemical Resistance: Ceramics are often resistant to chemicals and environmental factors, making them suitable for harsh operating conditions.
Ceramics substrates are commonly used in various electronic applications such as printed circuit boards (PCBs), power modules, LED packages, microwave devices, and sensors. They play a crucial role in ensuring the performance, reliability, and longevity of electronic systems.
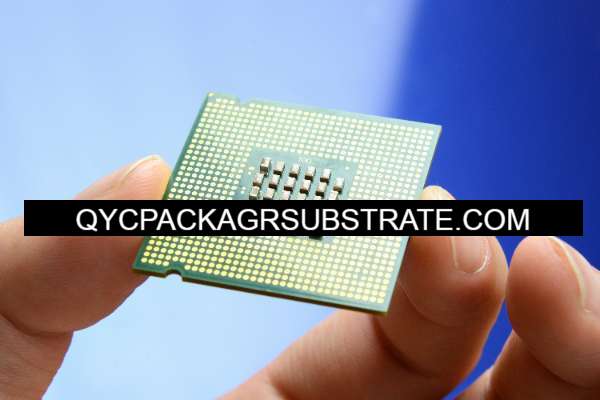
Ceramics Substrate Manufacturer
What are Ceramics Substrate Design Guidelines?
Designing with ceramics substrates involves several guidelines to ensure optimal performance and reliability of electronic components. Here are some key design guidelines for ceramics substrates:
- Thermal Management: Ensure proper thermal management by designing the substrate with adequate thermal conductivity to dissipate heat efficiently. This may involve optimizing the substrate material and thickness based on the heat dissipation requirements of the electronic components.
- Electrical Isolation: Ceramics substrates should provide sufficient electrical isolation to prevent short circuits between different components. Design the substrate layout and insulation layers to maintain appropriate electrical insulation between conductive traces and components.
- Material Selection: Choose the appropriate ceramic material based on the specific requirements of the application, such as thermal conductivity, mechanical strength, chemical resistance, and dielectric properties. Common ceramic materials used for substrates include alumina (Al2O3), aluminum nitride (AlN), and silicon nitride (Si3N4).
- Dimensional Stability: Ceramics substrates should exhibit good dimensional stability to minimize warping or distortion during manufacturing processes and operation. Consider factors such as coefficient of thermal expansion (CTE) compatibility with other materials and stress-relief features in the substrate design.
- Mounting and Attachment: Design the substrate with appropriate mounting features and attachment methods to securely hold electronic components in place. Consider factors such as solderability, adhesive bonding, or mechanical fastening depending on the application requirements.
- Signal Integrity: Maintain signal integrity by optimizing the layout and impedance matching of conductive traces on the substrate. Minimize signal loss, reflections, and electromagnetic interference (EMI) by adhering to proper high-frequency design principles.
- Environmental Compatibility: Consider the operating environment and potential exposure to factors such as moisture, temperature fluctuations, and chemical agents. Select ceramic materials and surface finishes that provide adequate protection against environmental degradation.
- Manufacturability: Design the substrate with manufacturability in mind, considering factors such as ease of fabrication, compatibility with standard manufacturing processes (e.g., CNC machining, laser cutting, screen printing), and cost-effectiveness.
By following these design guidelines, engineers can develop ceramics substrates that meet the performance, reliability, and manufacturability requirements of electronic applications.
What is the Ceramics Substrate Fabrication Process?
The fabrication process for ceramics substrates involves several steps to produce a high-quality substrate suitable for electronic applications. While specific processes may vary depending on factors such as substrate material and desired characteristics, here is a generalized overview of the ceramics substrate fabrication process:
- Material Preparation: The fabrication process begins with preparing the ceramic material for processing. This typically involves selecting raw materials, mixing them in precise proportions, and forming them into a desired shape. For example, alumina powder may be mixed with binders and additives to form a green ceramic body.
- Forming: The prepared ceramic material is then formed into the desired substrate shape. Common forming techniques include dry pressing, isostatic pressing, and injection molding. During forming, the material is compressed into a green body with the desired dimensions and features.
- Drying: After forming, the green ceramic body is dried to remove excess moisture and improve its strength. Drying may be performed using various methods such as air drying, oven drying, or microwave drying. Care must be taken to ensure uniform drying to prevent cracking or distortion.
- Firing (Sintering): The dried green ceramic body undergoes a high-temperature firing process known as sintering. Sintering involves heating the ceramic material to temperatures near its melting point, causing it to densify and bond into a solid, durable substrate. The sintering process also removes organic binders and additives, resulting in a fully ceramic substrate.
- Shaping and Machining: After sintering, the ceramic substrate may undergo additional shaping and machining processes to achieve the desired final dimensions, surface finish, and features. This may include machining operations such as grinding, lapping, drilling, and polishing to refine the substrate’s surface and ensure dimensional accuracy.
- Surface Treatment: Depending on the application requirements, the ceramic substrate may undergo surface treatment processes such as metallization or coating. Metallization involves depositing conductive metal layers onto the substrate surface to facilitate component attachment and interconnection. Coating processes may be used to enhance properties such as electrical insulation, thermal conductivity, or surface hardness.
- Quality Control and Testing: Throughout the fabrication process, rigorous quality control measures are employed to ensure the integrity and performance of the ceramic substrate. This may include inspection of raw materials, dimensional measurements, visual inspection, and various testing methods such as electrical testing, thermal testing, and mechanical testing.
- Packaging and Shipping: Once fabrication and testing are complete, the finished ceramic substrates are packaged and prepared for shipping to customers or downstream manufacturing processes where they will be integrated into electronic assemblies.
By following these steps, manufacturers can produce ceramics substrates with the necessary properties and characteristics to meet the requirements of diverse electronic applications.
How do you manufacture a Ceramics Substrate?
Manufacturing ceramics substrates involves several key steps:
- Material Selection: Choose suitable ceramic materials based on the desired properties such as thermal conductivity, electrical insulation, mechanical strength, and chemical resistance. Common materials include alumina (Al2O3), aluminum nitride (AlN), silicon carbide (SiC), and beryllium oxide (BeO).
- Powder Preparation: The selected ceramic material is typically in powder form. The powder may undergo various treatments such as milling, blending, and chemical processing to achieve the desired particle size distribution, purity, and homogeneity.
- Forming: The ceramic powder is formed into a green body with the desired shape and dimensions. Common forming techniques include dry pressing, isostatic pressing, injection molding, tape casting, and extrusion.
- Drying: The green body is dried to remove moisture and organic binders. Proper drying is crucial to prevent cracking and deformation during subsequent processing steps.
- Sintering: The dried green body undergoes sintering, a process where the ceramic particles are bonded together through diffusion and recrystallization at high temperatures (typically above 1000°C). Sintering results in densification, shrinkage, and the development of desired mechanical and electrical properties.
- Machining: After sintering, the ceramic substrate may undergo machining processes such as grinding, lapping, drilling, and cutting to achieve the final dimensions, surface finish, and tolerances.
- Surface Treatment: Surface treatments such as polishing, coating, metallization, and etching may be applied to improve the substrate’s functionality and compatibility with subsequent assembly processes.
- Quality Control: Throughout the manufacturing process, quality control measures are implemented to ensure that the ceramic substrates meet specifications regarding dimensions, mechanical properties, surface finish, and electrical performance.
Each step in the manufacturing process plays a critical role in producing ceramic substrates with the desired properties for various applications, including electronic devices, semiconductor packaging, catalytic converters, and biomedical implants.
How much should a Ceramics Substrate cost?
The cost of a ceramic substrate can vary significantly depending on several factors:
- Material: Different ceramic materials have different costs. For example, alumina (Al2O3) is generally more affordable compared to materials like aluminum nitride (AlN) or silicon carbide (SiC) due to differences in raw material availability and processing complexity.
- Size and Thickness: Larger and thicker substrates typically require more material and energy for manufacturing, leading to higher costs.
- Complexity: The complexity of the substrate’s design and features, such as intricate patterns, holes, and surface finishes, can impact manufacturing costs.
- Manufacturing Process: The chosen manufacturing process (e.g., dry pressing, tape casting, injection molding) and any additional processing steps (e.g., machining, surface treatment) influence production costs.
- Quality Requirements: Substrates manufactured to higher quality standards, with tighter tolerances and better surface finishes, may command higher prices.
- Volume: Economies of scale apply in manufacturing, meaning that larger production volumes generally result in lower per-unit costs due to efficiencies in material usage, equipment utilization, and overhead distribution.
- Supplier and Market Dynamics: Pricing may vary between suppliers based on factors such as geographic location, market demand, competition, and supplier reputation.
Given these factors, it’s challenging to provide a specific cost without more details about the substrate’s specifications, quantities, and the supplier’s pricing structure. However, for a rough estimate, ceramic substrates can range from a few dollars per piece for simpler, smaller components to several hundred dollars or more for larger, more complex substrates used in specialized applications like high-power electronics or aerospace.
What is Ceramics Substrate base material?
Ceramic substrates can be made from various ceramic materials, depending on the specific requirements of the application. Some common ceramic materials used as substrates include:
- Alumina (Al2O3): Alumina is one of the most widely used ceramic materials for substrates due to its excellent electrical insulation properties, high mechanical strength, and relatively low cost. It is commonly used in electronic applications such as integrated circuit (IC) packaging, thick film circuits, and high-power electronics.
- Aluminum Nitride (AlN): Aluminum nitride offers high thermal conductivity, making it suitable for applications requiring efficient heat dissipation, such as high-power electronic devices, LED substrates, and microwave components.
- Silicon Carbide (SiC): SiC exhibits high thermal conductivity, excellent thermal shock resistance, and high temperature stability, making it ideal for demanding applications in power electronics, automotive electronics, and aerospace components.
- Beryllium Oxide (BeO): Beryllium oxide offers exceptionally high thermal conductivity and low dielectric loss, making it suitable for applications requiring efficient heat transfer and electrical insulation in high-frequency and high-power electronic devices.
- Steatite: Steatite, also known as magnesium silicate, is valued for its good electrical insulation properties, mechanical strength, and thermal stability. It is commonly used in applications such as ceramic insulators, resistor substrates, and heating elements.
- Zirconia (ZrO2): Zirconia exhibits high mechanical strength, toughness, and thermal stability, making it suitable for applications requiring resistance to wear, corrosion, and high temperatures. It is used in applications such as cutting tools, dental implants, and oxygen sensors.
These are just a few examples of ceramic materials used as substrates. The choice of base material depends on factors such as the application requirements, including electrical, thermal, mechanical, and chemical properties, as well as cost considerations and manufacturing feasibility.
Which company makes Ceramics Substrate?
Many companies produce ceramic substrates, including well-known manufacturers such as Kyocera, CoorsTek, Murata Manufacturing in the United States, NGK Insulators, TDK in Japan, as well as Chinese companies like Rigao Electronics and BOE Technology. These companies have extensive experience and technical expertise in ceramic materials and processes, providing high-quality ceramic substrates for various applications.
As for our company, we can produce ceramic substrates because we have advanced production equipment and a skilled technical team. Our production line covers various processes from ceramic powder processing to finished product manufacturing, capable of meeting diverse requirements in terms of materials, sizes, and shapes. We employ advanced manufacturing techniques such as dry pressing, injection molding, tape casting, etc., ensuring products with high density, excellent mechanical strength, and stable electrical performance.
Furthermore, we emphasize quality control in our production process, strictly adhering to ISO quality management system to ensure products meet customer requirements and standards. We also have a professional R&D team capable of customizing special materials and designs according to customer needs, providing personalized solutions.
In summary, our company possesses the equipment, technology, and management capabilities required for ceramic substrate production, capable of meeting various application needs and providing high-quality products and services to customers.
What are the 7 qualities of good customer service?
Good customer service is essential for building strong relationships with customers and fostering loyalty. Here are seven qualities that contribute to excellent customer service:
- Responsiveness: Being responsive means acknowledging and addressing customer inquiries, concerns, and requests promptly. Responding in a timely manner demonstrates attentiveness and shows customers that their needs are being prioritized.
- Empathy: Empathy involves understanding and empathizing with the customer’s perspective and emotions. It means actively listening to their concerns, acknowledging their feelings, and showing genuine concern for their well-being. Empathetic responses help build trust and rapport with customers.
- Professionalism: Professionalism encompasses maintaining a courteous and respectful demeanor in all interactions with customers. It involves being knowledgeable about products or services, adhering to company policies and procedures, and handling challenging situations with grace and composure.
- Reliability: Reliability refers to consistently delivering on promises and commitments made to customers. It involves following through on resolutions, providing accurate information, and ensuring that customers can rely on the company to meet their needs consistently.
- Adaptability: Adaptability involves being flexible and adaptable to meet the diverse needs and preferences of customers. It means being able to adjust communication styles, problem-solving approaches, and service delivery methods to accommodate different situations and customer requirements.
- Clarity: Clarity entails communicating information clearly and concisely to customers. It involves avoiding jargon, using plain language, and providing accurate and relevant information to help customers make informed decisions or resolve issues effectively.
- Proactiveness: Proactiveness involves anticipating customer needs and taking proactive measures to address them before they escalate into problems. It means actively seeking feedback, offering personalized recommendations, and identifying opportunities to enhance the customer experience.
By embodying these qualities, organizations can provide exceptional customer service that exceeds expectations and fosters long-term loyalty and satisfaction.
FAQs (Frequently Asked Questions)
What is a ceramic substrate?
A ceramic substrate is a thin, rigid material typically made from ceramic compounds such as alumina (Al2O3), aluminum nitride (AlN), or silicon carbide (SiC). It serves as a base for mounting electronic components and provides electrical insulation and thermal management in various applications.
What are the advantages of using ceramic substrates?
Ceramic substrates offer several advantages, including high thermal conductivity, excellent electrical insulation, mechanical strength, chemical resistance, and dimensional stability. They are also lightweight, durable, and capable of withstanding high temperatures.
What are ceramic substrates used for?
Ceramic substrates are used in a wide range of applications, including electronic devices (such as integrated circuits, power modules, and LED packages), automotive components (such as catalytic converters and sensors), aerospace components, medical devices, and industrial equipment.
How are ceramic substrates manufactured?
The manufacturing process for ceramic substrates typically involves powder preparation, forming (such as pressing or molding), drying, sintering (high-temperature firing), machining (such as grinding or cutting), and surface treatment (such as coating or metallization).
What factors should be considered when selecting a ceramic substrate?
When selecting a ceramic substrate, factors to consider include the material properties (such as thermal conductivity, electrical insulation, and mechanical strength), dimensional requirements, compatibility with assembly processes, cost considerations, and environmental conditions (such as temperature and chemical exposure).
Are ceramic substrates customizable?
Yes, ceramic substrates can be customized to meet specific application requirements. Customization options include material composition, dimensions, surface finishes, metallization patterns, and electrical properties tailored to the needs of the end-use application.
How do ceramic substrates compare to other substrate materials, such as FR-4 or metal?
Ceramic substrates offer advantages over other substrate materials, such as FR-4 (a type of epoxy-based fiberglass) and metal (such as aluminum or copper), in terms of thermal conductivity, electrical insulation, mechanical strength, and temperature resistance. However, the choice of substrate material depends on the specific requirements of the application.