CPU Package Substrates Manufacturer
CPU Package Substrates Manufacturer,CPU Package Substrates are crucial components that provide electrical and mechanical support for central processing units (CPUs) in electronic devices. These substrates are designed with high-density interconnects (HDI) to ensure efficient communication between the CPU and other system components. They feature advanced materials like ceramic or organic substrates with embedded conductive traces and vias for enhanced signal integrity and thermal management. CPU Package Substrates are engineered to dissipate heat effectively, ensuring optimal CPU performance and reliability. They play a pivotal role in modern computing devices, facilitating faster data processing, lower power consumption, and compact form factors essential for high-performance computing applications.
What is a CPU Package Substrate (CPS)?
A CPU Package Substrate (CPS) is a crucial component in modern central processing unit (CPU) designs, serving as the foundational structure that supports and connects the CPU die (the actual silicon chip where computing occurs) to the motherboard. The substrate is typically made of materials like organic resins, ceramics, or silicon, chosen for their ability to provide electrical insulation, mechanical support, and thermal management.
The primary function of the CPS is to facilitate communication between the CPU die and the motherboard. This involves hosting the intricate network of electrical connections that link the tiny, densely packed transistors on the CPU die to the broader circuitry of the computer system. These connections are established through a combination of metal traces, vias (vertical interconnections), and solder balls or pins arranged in a grid array format, such as a Ball Grid Array (BGA) or Land Grid Array (LGA).
Beyond electrical connectivity, the CPS also plays a vital role in managing the physical and thermal properties of the CPU. It helps in dissipating heat generated by the CPU during operation, often incorporating thermal management features like heat spreaders or thermal vias. This is essential to maintain the performance and longevity of the CPU by preventing overheating.
Furthermore, the substrate contributes to the overall mechanical stability of the CPU package. It provides a rigid platform that supports the fragile silicon die and protects it from mechanical stresses that could arise from handling, installation, or operation.
In summary, the CPU Package Substrate is a multifunctional component that ensures reliable electrical connections, efficient thermal management, and mechanical stability, enabling the seamless operation of modern CPUs within computer systems.
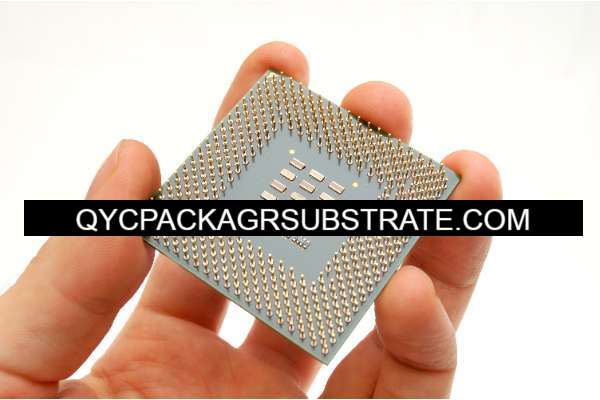
CPU Package Substrates Manufacturer
What are the CPS Design Guidelines?
The design of a CPU Package Substrate (CPS) is governed by several key guidelines and considerations to ensure optimal performance, reliability, and manufacturability. Here are some of the essential CPS design guidelines:
- Electrical Integrity:The substrate must provide low electrical impedance paths between the CPU die and the motherboard to maintain signal integrity and minimize electrical noise. Designers must carefully plan the layout of power delivery networks (PDNs) and signal traces to minimize impedance mismatches and crosstalk.
- Signal Routing: The substrate design involves routing thousands of signals between the CPU die and the motherboard. Signal traces must be carefully routed to avoid signal interference, maintain controlled impedance, and ensure proper signal integrity throughout the substrate.
- Thermal Management:Effective thermal management is crucial to prevent the CPU from overheating. The CPS design should include features such as thermal vias, heat spreaders, and thermal pads to efficiently transfer heat away from the CPU die to the heatsink or cooling solution on the motherboard.
- Mechanical Stability:The CPS must provide robust mechanical support to protect the delicate CPU die from mechanical stresses during handling, shipping, and installation. It should be designed to withstand bending, shock, and vibration without compromising the integrity of electrical connections.
- Manufacturability:Designers must consider manufacturability aspects such as substrate material selection, layer stack-up design, and fabrication processes. The substrate design should be optimized for high-volume manufacturing techniques like PCB (Printed Circuit Board) fabrication and assembly.
- Reliability and Durability:The CPS must be designed to ensure long-term reliability under various operating conditions, including temperature extremes, humidity, and mechanical shocks. This involves selecting materials with appropriate thermal expansion coefficients and ensuring robust bonding between layers.
- Compatibility and Standards:The design should adhere to industry standards and specifications for CPU packaging, such as JEDEC (Joint Electron Device Engineering Council) standards for BGA (Ball Grid Array) or LGA (Land Grid Array) packages.
- Size and Form Factor:The CPS design must fit within the specified dimensions and form factors required for compatibility with the CPU socket on the motherboard and other system components.
By adhering to these CPS design guidelines, engineers can ensure that the CPU package substrate meets the stringent performance, reliability, and manufacturability requirements essential for modern high-performance computing systems.
What is the CPS Fabrication Process?
The fabrication process of a CPU Package Substrate (CPS) involves several intricate steps to create a robust and reliable substrate that connects the CPU die to the motherboard. Here’s an overview of the typical CPS fabrication process:
- Substrate Material Selection:The fabrication begins with selecting suitable substrate materials based on thermal, electrical, and mechanical requirements. Common materials include organic substrates (such as fiberglass-reinforced epoxy resin), ceramic substrates, or even silicon substrates for advanced applications.
- Layer Stack-up Design:The substrate is designed with multiple layers of material, each serving specific purposes like signal routing, power distribution, and mechanical support. The layer stack-up design is crucial for achieving optimal electrical performance and thermal management.
- Substrate Preparation:The fabrication process starts with preparing the substrate materials. This involves cleaning and inspecting the materials to ensure they are free from contaminants that could affect the performance or reliability of the substrate.
- Lamination:For organic substrates, the layers are typically laminated together using heat and pressure. This process creates a solid and uniform substrate structure with defined electrical vias and conductive traces between layers.
- Drilling and Vias Formation:After lamination, precision drilling is performed to create holes (vias) that connect different layers of the substrate. These vias are essential for electrical connections between the CPU die, substrate layers, and the motherboard.
- Circuit Patterning: Conductive traces and pads are patterned onto the substrate layers using photolithography and etching processes. This step defines the electrical pathways that will carry signals and power across the substrate.
- Surface Finish:The substrate surfaces are finished to ensure proper solderability and reliability of the electrical connections. This may involve applying metal finishes such as solder mask, gold plating, or other surface treatments depending on the application requirements.
- Assembly and Attachment:Once the substrate is fabricated, it is assembled with the CPU die using advanced packaging techniques such as Ball Grid Array (BGA) or Land Grid Array (LGA). This involves precise alignment and attachment of the CPU die to the substrate using solder balls or pins.
- Testing and Inspection:Throughout the fabrication process, rigorous testing and inspection are conducted to ensure the substrate meets quality standards and specifications. Electrical testing verifies the integrity of signal paths and power delivery, while thermal testing checks the substrate’s ability to manage heat effectively.
- Packaging:After testing and inspection, the CPS is packaged securely to protect it during shipping and installation. This final packaging ensures that the substrate remains intact and functional when integrated into the final CPU product.
Overall, the CPS fabrication process is highly complex and requires precise engineering and manufacturing techniques to achieve high-performance substrates that meet the stringent requirements of modern CPU designs. Each step in the process is critical to ensuring the reliability, electrical performance, and thermal management capabilities of the substrate within the CPU package.
How do you manufacture a CPS?
Manufacturing a CPU Package Substrate (CPS) involves a detailed process that integrates material selection, fabrication techniques, and quality control measures to ensure the substrate meets stringent performance standards. Here’s a structured overview of how CPS is manufactured:
- Material Selection:Begin by selecting substrate materials suitable for the CPS’s intended application. Common materials include organic substrates (such as fiberglass-reinforced epoxy resin), ceramics, or silicon, chosen based on thermal conductivity, electrical properties, and mechanical strength requirements.
- Design and Layout:Develop a detailed design plan for the CPS, considering factors like layer stack-up, signal routing, power distribution, and thermal management. CAD (Computer-Aided Design) software is typically used to create the substrate layout, ensuring optimal placement of vias, traces, and component mounting areas.
- Substrate Preparation:Clean and prepare the substrate materials to remove contaminants and ensure uniformity. This step is crucial to prevent defects and ensure the substrate’s mechanical and electrical properties meet specifications.
- Layer Formation:Depending on the substrate type, layers may be formed through processes like lamination for organic substrates or deposition and sintering for ceramic substrates. Each layer is carefully inspected to verify thickness, adhesion, and uniformity.
- Drilling and Vias Formation:Precision drilling is performed to create vias that connect different substrate layers. Vias are typically created using laser drilling or mechanical drilling techniques, ensuring precise alignment and depth control.
- Circuit Patterning:Apply conductive patterns onto the substrate layers using photolithography and etching processes. This defines the paths for electrical signals and power distribution across the substrate. Metal deposition techniques like sputtering or electroplating are used to create conductive traces and pads.
- Surface Finishing:Apply surface finishes to the substrate to enhance solderability and ensure reliability of electrical connections. Common finishes include solder mask application, gold plating for contact pads, and surface treatments to improve durability and corrosion resistance.
- Assembly: Precisely align and attach the CPU die to the substrate using advanced packaging techniques such as BGA (Ball Grid Array) or LGA (Land Grid Array). This step involves soldering the CPU die to the substrate, ensuring secure electrical and mechanical connections.
- Testing and Quality Control:Perform rigorous testing throughout the manufacturing process to verify the CPS’s performance. Electrical tests check for continuity, impedance, and signal integrity, while thermal tests evaluate the substrate’s heat dissipation capabilities. Inspections for defects, such as solder joint integrity and substrate warping, are also conducted to ensure high reliability.
- Packaging and Final Inspection:Once testing is complete and the CPS meets quality standards, package the substrate securely for shipment and installation. Final inspections ensure the substrate is free from defects and meets all specifications before integration into the final CPU product.
By following these manufacturing steps with precision and adhering to strict quality control measures, manufacturers can produce CPS that meet the demanding requirements of modern CPUs, ensuring reliable performance, thermal management, and durability in various computing applications.
How much should a CPS cost?
The cost of a CPU Package Substrate (CPS) can vary widely depending on several factors, including the substrate material, complexity of design, manufacturing processes involved, and the volume of production. Here are some key considerations that influence the cost:
- Substrate Material:Different materials have varying costs. Organic substrates (such as fiberglass-reinforced epoxy resin) are generally less expensive compared to ceramic or silicon substrates, which are more costly but offer superior thermal and electrical properties.
- Design Complexity:The complexity of the CPS design affects manufacturing costs. More intricate designs with densely packed signal traces, multiple layers, and advanced features (such as high-density interconnects or embedded passives) require more sophisticated manufacturing processes and may incur higher costs.
- Manufacturing Processes:The fabrication processes involved, such as lamination, drilling, metallization, and surface finishing, contribute to the overall cost. Advanced techniques like laser drilling or fine-pitch photolithography add to manufacturing expenses.
- Volume of Production:Economies of scale play a significant role in CPS costs. Higher volumes typically lead to lower per-unit costs due to efficiencies in manufacturing, bulk material purchasing, and optimized production setups.
- Quality and Reliability Requirements: Meeting stringent quality standards and reliability specifications may necessitate additional testing and inspection procedures, which can increase manufacturing costs.
- Market Dynamics:Market conditions, supply chain factors, and competition among substrate manufacturers can influence pricing. Pricing may also vary based on customer-specific requirements and negotiations.
To provide a rough estimate, CPS costs can range from a few dollars to tens of dollars per unit in mass production scenarios. For high-performance CPUs in consumer electronics or server applications, where reliability, thermal management, and electrical performance are critical, CPS costs tend to be higher due to the need for advanced materials and manufacturing processes.
Ultimately, the exact cost of a CPS would need to be determined through detailed discussions with substrate manufacturers, considering specific design requirements, material choices, production volumes, and quality expectations.
What is CPS base material?
The base material of a CPU Package Substrate (CPS) typically depends on the specific requirements of the application, but there are several common materials used in CPS fabrication:
- Organic Substrates:These are the most widely used base materials for CPS. Organic substrates are typically composed of layers of fiberglass-reinforced epoxy resin (FR4) or other similar materials. They offer good electrical insulation properties, cost-effectiveness, and ease of manufacturing. Organic substrates are suitable for most consumer electronics and general computing applications.
- Ceramic Substrates:Ceramic materials, such as alumina (Al2O3) or aluminum nitride (AlN), are used in CPS where higher thermal conductivity, better electrical performance at high frequencies, and improved mechanical strength are required. Ceramic substrates can withstand higher temperatures and provide excellent thermal management capabilities, making them suitable for high-performance CPUs and server applications.
- Silicon Substrates:Silicon substrates are used in advanced applications where integration with semiconductor processes is required. Silicon substrates offer unique advantages such as compatibility with silicon ICs, high thermal conductivity, and the potential for integration of passive components. They are more expensive and typically used in specialized applications.
- Metal Substrates:In some cases, metal substrates such as copper or aluminum may be used for their high thermal conductivity and mechanical strength. Metal substrates are less common in CPS compared to organic or ceramic substrates but may be used in specific applications where thermal dissipation is critical.
The choice of CPS base material depends on factors such as thermal management requirements, electrical performance, mechanical stability, cost considerations, and the specific needs of the CPU design. Each material has its own advantages and trade-offs, and manufacturers select the most appropriate material based on the performance requirements and constraints of the application.
Which company makes CPS?
Currently, many companies manufacture CPU Package Substrates (CPS), including major international semiconductor and electronic component manufacturers such as Intel, TSMC, UMC, Micron Technology, and Samsung Electronics. These companies possess advanced manufacturing technologies and facilities worldwide, enabling them to produce various types of CPU package substrates to meet the needs of different applications.
For our company to produce CPU package substrates, we need to have advanced semiconductor manufacturing technologies and specialized process capabilities. Our company has many years of experience in electronics manufacturing, focusing on the design and production of high-performance electronic components. Our manufacturing processes meet international standards, and we have advanced equipment that can meet customer demands for high-quality CPU package substrates.
Specifically, our company can provide the following services and capabilities:
- Process Technology:We have advanced PCB (Printed Circuit Board) manufacturing technologies, including multi-layer board design and manufacturing, high-density interconnect technology, and fine line creation. These technologies form the foundation for producing complex CPU package substrates.
- Material Selection:Depending on customer requirements and application scenarios, we can choose suitable substrate materials, such as organic substrates, ceramic substrates, or silicon substrates, to meet different electrical performance, thermal management, and mechanical stability requirements.
- Quality Assurance:We implement strict quality control measures, from material procurement and production process control to final product testing and verification, ensuring that each CPU package substrate meets customer specifications and quality standards.
- Customer Customization: We can customize the design and manufacturing of CPU package substrates according to specific customer needs. Whether in circuit layout optimization, thermal management solution design, or specific material selection, we can provide professional advice and solutions.
- Cost Efficiency: We are committed to offering competitive cost-efficiency by optimizing production processes and improving efficiency, providing high-quality products while maintaining reasonable pricing.
In summary, our company has extensive manufacturing experience and technical capabilities to provide customers with high-performance CPU package substrates that meet international standards. Whether in consumer electronics, computer servers, or industrial automation, we can meet diverse customer needs and continuously improve product quality and service levels through innovation and ongoing improvement.
What are the 7 qualities of good customer service?
The 7 qualities of good customer service are crucial for ensuring customer satisfaction, loyalty, and positive business reputation. Here are the key qualities, described in detail:
- Professionalism:Good customer service should always maintain a high level of professionalism. This includes being respectful, courteous, and well-mannered in all interactions. Professionalism also means having a deep understanding of the company’s products and services, allowing representatives to provide accurate and helpful information to customers.
- Empathy:Showing empathy involves understanding and sharing the feelings of customers. Good customer service representatives listen actively to customer concerns, acknowledge their emotions, and respond with genuine care and concern. This helps in building a strong emotional connection and trust with customers.
- Responsiveness:Prompt and timely responses to customer inquiries and issues are essential. Responsiveness means quickly addressing customer needs, whether through email, phone, chat, or social media. It also involves following up on unresolved issues to ensure they are addressed satisfactorily.
- Knowledge:A thorough understanding of the company’s products, services, and policies is critical for providing effective customer service. Representatives should be well-trained and continuously updated on new developments to accurately address customer questions and problems.
- Problem-Solving Skills:Customers often reach out with issues or challenges that need resolution. Good customer service involves strong problem-solving skills, allowing representatives to identify the root cause of problems and offer effective solutions. This can involve creative thinking and the ability to stay calm under pressure.
- Communication Skills:Clear and effective communication is fundamental to good customer service. Representatives should be able to explain information in a straightforward and concise manner, ensuring customers fully understand the solutions or information provided. Good communication also involves being an active listener and interpreting customer needs accurately.
- Positive Attitude:A positive attitude can greatly enhance the customer service experience. This involves staying upbeat, enthusiastic, and patient, even when dealing with difficult or frustrated customers. A positive demeanor helps in creating a pleasant interaction and can often defuse tense situations.
By embodying these seven qualities, companies can ensure their customer service teams provide exceptional support, fostering customer loyalty and promoting a positive brand image.
FAQs about CPS
What is a CPU Package Substrate (CPS)?
A CPS is a crucial component in CPUs that serves as a base for mounting and connecting the CPU die to the motherboard. It provides electrical connections, thermal management, and mechanical support for the CPU.
What materials are used to make CPS?
CPS can be made from various materials depending on the application requirements. Common materials include organic substrates (like fiberglass-reinforced epoxy resin), ceramic substrates (such as alumina or aluminum nitride), and silicon substrates.
How does CPS contribute to CPU performance?
CPS plays a critical role in CPU performance by ensuring efficient electrical connectivity, managing heat dissipation to prevent overheating, and providing structural support to the CPU die.
What are the key features of a CPS?
Key features include high-density interconnects for signal routing, thermal vias or heat spreaders for heat dissipation, and robust mechanical properties to withstand physical stresses.
How is CPS manufactured?
CPS manufacturing involves processes like substrate material selection, layer stack-up design, drilling vias for electrical connections, circuit patterning, surface finishing, assembly with the CPU die, testing, and packaging.
What are the different types of CPS designs?
CPS designs can vary based on the substrate material, number of layers, interconnect density, and specific thermal and electrical requirements of the CPU design. Common designs include BGA (Ball Grid Array) and LGA (Land Grid Array) configurations.
What factors affect the cost of CPS?
CPS costs depend on factors such as the substrate material chosen (organic, ceramic, silicon), complexity of design, manufacturing processes involved, volume of production, and quality assurance requirements.