Embedded IC PCB manufacturing
Embedded IC PCB manufacturing, Open a cavity or multiple cavity on the PCBs substrates. and put the IC in the cavity and assemble. we made this cavity PCBs from 4 layer to 30 layers. Advanced production technology and fast shipping time.
Embedded IC PCBs, or Embedded Integrated Circuit Printed Circuit Boards, revolutionize electronic design by integrating ICs directly within the board structure rather than mounting them on the surface. This innovative approach optimizes space utilization, enhances performance, and streamlines manufacturing processes. Embedded IC PCBs offer a compact design, reducing overall device size while improving signal integrity and thermal management. By embedding ICs within the layers of the PCB, these boards exhibit increased durability and reliability, making them ideal for applications in consumer electronics, automotive systems, medical devices, and aerospace technology. The manufacturing process involves precise alignment and bonding of ICs, as well as comprehensive testing to ensure functionality and reliability. With their ability to accommodate various types of ICs and complex circuitry, Embedded IC PCBs represent a cutting-edge solution for compact and high-performance electronic systems.
What is an Embedded IC PCB?
We are a professional Embedded IC PCB manufacturingsupplier, we mainly produce ultra-small bump pitch substrate, ultra-small trace and spacing packaging substrate and PCBs.
An Embedded IC PCB (Printed Circuit Board) refers to a type of circuit board where integrated circuits (ICs) are directly embedded within the board itself rather than being mounted on the surface. This embedding process involves placing the ICs inside the layers of the PCB during the manufacturing process.
Embedded IC PCBs offer several advantages:
- Reduced Size: By embedding ICs within the PCB, the overall size of the electronic device can be reduced since there’s no need for additional space for surface-mounted IC packages.
- Improved Performance: Embedding ICs can reduce signal distortion and electromagnetic interference (EMI), leading to improved performance and reliability of the electronic system.
- Enhanced Thermal Management: Embedding ICs within the PCB can improve thermal management since the heat generated by the ICs can be more efficiently dissipated through the board itself.
- Increased Durability: Since the ICs are protected within the layers of the PCB, they are less susceptible to physical damage and environmental factors like moisture and dust.
- Cost Savings: While the initial manufacturing cost might be higher due to the complexity of embedding ICs, the overall cost can be reduced in the long run due to the elimination of additional components and reduced assembly time.
Embedded IC PCBs are commonly used in various applications such as consumer electronics, automotive systems, medical devices, and aerospace technology where space-saving, reliability, and performance are critical requirements.
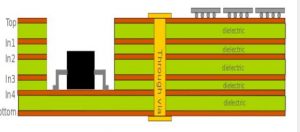
Embedded IC PCB
What are Embedded IC PCB Design Guidelines?
Embedded IC PCB design guidelines help engineers and designers ensure that the integration of ICs into the printed circuit board (PCB) is successful and optimized for performance, reliability, and manufacturability. Here are some common embedded IC PCB design guidelines:
- Thermal Management: Ensure proper heat dissipation by designing adequate thermal vias and thermal pads to transfer heat away from the embedded ICs and into the PCB layers for efficient cooling.
- Signal Integrity: Minimize signal distortion and electromagnetic interference (EMI) by carefully planning the placement and routing of signal traces, power planes, and ground planes. Use controlled impedance routing for high-speed signals.
- Layer Stackup: Design the PCB with appropriate layer stackup to accommodate the embedded ICs, power planes, ground planes, and signal traces while ensuring signal integrity and thermal management.
- Component Placement: Strategically place the embedded ICs on the PCB to minimize signal paths, reduce crosstalk, and optimize thermal performance. Consider the location of other components and connectors for ease of assembly and serviceability.
- Power Distribution: Design robust power distribution networks with low impedance paths to supply power to the embedded ICs and other components efficiently. Use decoupling capacitors and proper power plane design to minimize noise and voltage fluctuations.
- Mechanical Considerations: Ensure that the mechanical design of the PCB supports the embedding process and provides sufficient structural integrity to protect the embedded ICs from mechanical stress and environmental factors.
- Manufacturability: Design the PCB with manufacturability in mind, considering factors such as assembly process, soldering techniques, and inspection methods for embedded ICs. Minimize the complexity of the embedding process to reduce manufacturing costs and improve yield.
- Reliability: Perform thorough reliability analysis, including thermal simulations, mechanical stress analysis, and failure mode analysis, to ensure the long-term reliability of the embedded IC PCB design.
- Documentation: Create comprehensive documentation that includes detailed specifications, layout guidelines, material requirements, and assembly instructions to facilitate collaboration between design teams and manufacturers.
By following these embedded IC PCB design guidelines, engineers can create PCBs that effectively integrate ICs into the substrate, meeting performance requirements while ensuring reliability and manufacturability.
What is the Embedded IC PCB Fabrication Process?
The fabrication process for embedded IC PCBs involves several steps, including design, material selection, PCB manufacturing, embedding ICs, and assembly. Here’s an overview of the typical embedded IC PCB fabrication process:
- Design: Engineers start by designing the PCB layout using computer-aided design (CAD) software. This includes defining the placement of embedded ICs, routing signal traces, creating power and ground planes, and specifying layer stackup.
- Material Selection: Select appropriate materials for the PCB substrate and laminate based on factors such as thermal conductivity, dielectric properties, mechanical strength, and compatibility with the embedding process.
- PCB Manufacturing: The PCB manufacturing process begins with preparing the substrate material and applying copper foil layers. The substrate is then drilled to create holes for vias and component mounting.
- Embedding ICs: Once the basic PCB structure is fabricated, the embedded ICs are placed within the layers of the PCB. This can be achieved using various methods such as sequential lamination, where the PCB is built up layer by layer with embedded ICs, or using advanced embedding techniques such as plasma embedding or laser drilling.
- Circuit Patterning: After embedding the ICs, the circuit patterns are created by selectively etching away the copper layers using chemical processes or mechanical milling. This defines the interconnections between the embedded ICs and other components.
- Surface Finishing: Surface finishing processes such as solder mask application, copper plating, and surface treatment are performed to protect the PCB and improve solderability.
- Assembly: Components such as resistors, capacitors, connectors, and other ICs are assembled onto the PCB using soldering techniques such as surface mount technology (SMT) or through-hole mounting.
- Testing and Inspection: The fabricated embedded IC PCB undergoes testing and inspection to ensure that it meets quality standards and functional requirements. This may include electrical testing, visual inspection, and functional testing.
- Final Finishing: Once testing is completed and any necessary rework is done, the PCB is finished with any required coatings or markings before being packaged and shipped to the customer.
Throughout the embedded IC PCB fabrication process, careful attention is paid to quality control, process optimization, and adherence to design specifications to ensure the final product meets performance, reliability, and manufacturability requirements.
How do you manufacture an Embedded IC PCB?
Manufacturing an embedded IC PCB involves several steps, from design and fabrication to assembly and testing. Here’s a general overview of the manufacturing process:
- Design: The process starts with the design of the PCB layout, including the placement of embedded ICs, routing of traces, and creation of layer stackup. Special attention is given to thermal management, signal integrity, and mechanical considerations.
- Material Selection: Choose appropriate materials for the PCB substrate and layers based on factors such as thermal conductivity, dielectric constant, and mechanical strength. High-quality materials ensure the reliability and performance of the embedded IC PCB.
- PCB Fabrication: The fabrication process begins with the preparation of the substrate material, typically a laminate or composite material. Layers of copper foil are then bonded to the substrate, and the circuit pattern is etched onto the copper layers using photolithography or other techniques.
- Embedding ICs: After the initial layers of the PCB are fabricated, the ICs are embedded directly into the board. This can be done using several methods, such as flip-chip bonding, wire bonding, or through-silicon vias (TSVs). The embedding process requires precise alignment and bonding to ensure proper electrical connections.
- Lamination: Once the ICs are embedded, additional layers of substrate material and copper foil are laminated onto the board to encapsulate the ICs and create the desired layer stackup. Pressure and heat are applied during lamination to bond the layers together securely.
- Drilling and Plating: Holes are drilled through the PCB to create vias for interconnecting different layers. These vias are then plated with conductive material to establish electrical connections between the layers.
- Circuit Patterning: The outer layers of the PCB are patterned with the final circuit traces and features using photolithography or other techniques. Copper is deposited onto the substrate and etched to create the desired circuit pattern.
- Surface Finishing: Surface finishing processes such as solder mask application, solder plating, and surface coating are applied to protect the PCB from oxidation, improve solderability, and enhance electrical performance.
- Assembly: Once the PCB is fabricated, it undergoes assembly to attach additional components such as resistors, capacitors, connectors, and other ICs. Surface-mount technology (SMT) or through-hole assembly methods may be used depending on the design requirements.
- Testing and Inspection: The assembled PCB undergoes testing and inspection to ensure that it meets quality standards and functional requirements. This may include electrical testing, thermal testing, and visual inspection to identify any defects or issues.
- Packaging: Finally, the completed PCBs are packaged and prepared for shipment to the end user or integration into larger electronic systems.
Throughout the manufacturing process, quality control measures are implemented to ensure that the embedded IC PCBs meet performance, reliability, and safety standards. Collaboration between design engineers, fabricators, and assemblers is essential to ensure a successful outcome.
How much should an Embedded IC PCB cost?
The cost of an embedded IC PCB can vary significantly depending on several factors such as the complexity of the design, the materials used, the manufacturing processes involved, the quantity ordered, and the supplier or manufacturer chosen. Here are some factors that can influence the cost:
- Design Complexity: Complex designs with high-density components, multiple layers, and advanced features will generally incur higher costs due to the increased complexity of fabrication and assembly.
- Materials: The choice of materials for the PCB substrate, copper layers, and surface finishes can impact the cost. High-performance materials with specific properties may be more expensive than standard materials.
- Manufacturing Processes: Certain manufacturing processes, such as embedded IC technology, may add to the cost compared to traditional PCB fabrication methods. Additional processes like laser drilling, selective plating, and lamination can also contribute to higher costs.
- Quantity: Typically, larger production quantities result in lower unit costs due to economies of scale. Ordering higher volumes can help reduce the cost per unit.
- Supplier and Location: Different PCB manufacturers may offer varying pricing structures based on their capabilities, equipment, labor costs, and geographic location. Offshore manufacturers may provide lower costs but may have longer lead times and potential quality risks.
- Quality and Certification Requirements: Meeting specific quality standards or certifications, such as IPC standards or UL certification, may incur additional costs for testing, inspection, and compliance.
- Lead Time: Shorter lead times or expedited production may come at an additional cost compared to standard turnaround times.
- Additional Services: Value-added services such as design assistance, prototype development, testing, and assembly may increase the overall cost but can provide added convenience and support.
Given these factors, it’s challenging to provide a specific cost without knowing the details of the project. Generally, embedded IC PCBs can range from a few dollars for simple designs in small quantities to several hundred or even thousands of dollars for complex designs or large production runs. It’s recommended to obtain quotes from multiple PCB manufacturers and evaluate them based on factors such as quality, lead time, and overall value proposition.
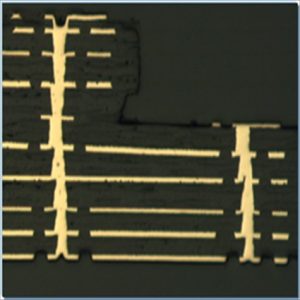
Micro cavity substrates
What is the Embedded IC PCB base material?
The choice of base material for an embedded IC PCB depends on various factors such as thermal conductivity, dielectric constant, mechanical strength, and cost. Here are some common base materials used in embedded IC PCBs:
- FR-4 (Flame Retardant 4): FR-4 is the most widely used substrate material for PCBs due to its good overall performance, high strength, and low cost. It is composed of woven fiberglass cloth impregnated with epoxy resin. FR-4 is suitable for many embedded IC applications, particularly those with moderate thermal and electrical requirements.
- High-Temperature FR-4: This variant of FR-4 is designed to withstand higher temperatures than standard FR-4 materials. It offers improved thermal stability and can be used in applications where embedded ICs generate significant heat.
- Polyimide (PI): Polyimide is a high-performance substrate material known for its excellent thermal stability, low thermal expansion coefficient, and resistance to harsh environments. It is commonly used in applications requiring high-temperature operation and superior mechanical properties.
- Rogers Corporation Materials: Rogers Corporation offers a range of high-performance substrates specifically designed for RF and microwave applications. These materials provide excellent electrical performance, low dielectric loss, and good thermal management properties, making them suitable for embedded IC PCBs in high-frequency applications.
- Metal Core PCBs (MCPCB): Metal core PCBs feature a metal core (usually aluminum or copper) sandwiched between layers of dielectric material. They offer excellent thermal conductivity, allowing efficient heat dissipation from embedded ICs. MCPCBs are commonly used in high-power LED lighting and automotive electronics.
- Ceramic Substrates: Ceramic substrates such as alumina (Al2O3) and aluminum nitride (AlN) offer exceptional thermal conductivity, electrical insulation, and mechanical strength. They are well-suited for high-power applications and environments requiring high reliability.
The choice of base material depends on the specific requirements of the embedded IC PCB, including thermal management, electrical performance, mechanical stability, and cost constraints. Designers typically select the base material that best balances these factors to achieve optimal performance and reliability.
Which company makes Embedded IC PCBs?
Many companies manufacture Embedded IC PCBs, including world-renowned electronics manufacturers such as Intel, Delta Electronics, Samsung Electronics, and many specialized PCB manufacturing suppliers and contract manufacturers. These companies have advanced technology and equipment to meet various complex Embedded IC PCB manufacturing needs.
Our company is also a professional electronics manufacturer with the capability to produce Embedded IC PCBs. We have advanced production equipment, a skilled technical team, and extensive experience to provide high-quality, customized Embedded IC PCB solutions. Our manufacturing process strictly adheres to international standards to ensure product quality and performance meet our customers’ requirements.
In our factory, we employ advanced processes and technologies to realize the manufacturing of Embedded IC PCBs, including layout design of embedded ICs, material selection, stackup design, embedding process, interlayer connection, circuit fabrication, surface treatment, and more. We also offer customized services tailored to customer requirements, including layout and circuit design of Embedded IC PCBs, material selection, and optimization of manufacturing processes.
As a professional electronics manufacturer, we are committed to providing customers with the highest quality products and services. We prioritize communication and collaboration with our customers to ensure that our Embedded IC PCBs meet their needs and exceed their expectations in terms of quality, performance, and reliability. We are dedicated to being your trusted partner, offering comprehensive support and solutions for your projects.
What are the 7 qualities of good customer service?
Good customer service is crucial for maintaining customer satisfaction, building brand loyalty, and fostering positive relationships with customers. Here are seven qualities of good customer service:
- Responsiveness: Good customer service involves promptly addressing customer inquiries, concerns, and issues. Responding to customer needs in a timely manner demonstrates attentiveness and shows that their satisfaction is a priority.
- Empathy: Empathy involves understanding and acknowledging the customer’s emotions, concerns, and perspectives. Showing empathy towards customers fosters trust and helps create a positive experience, even in challenging situations.
- Professionalism: Professionalism entails maintaining a courteous, respectful, and helpful demeanor when interacting with customers. Being knowledgeable about products or services, adhering to company policies, and conducting oneself with integrity contribute to a professional image.
- Effective Communication: Effective communication is essential for conveying information clearly, listening actively to customers’ needs, and providing relevant assistance or solutions. Using clear and concise language, asking clarifying questions, and ensuring mutual understanding facilitate productive interactions.
- Problem-Solving Skills: Good customer service involves proactively identifying and resolving customer problems or issues. Having strong problem-solving skills enables customer service representatives to address challenges efficiently and effectively, leading to satisfactory outcomes for customers.
- Personalization: Personalization involves tailoring interactions and solutions to meet the specific needs and preferences of individual customers. Recognizing repeat customers, remembering previous interactions, and offering personalized recommendations or assistance enhance the customer experience and demonstrate attentiveness.
- Follow-Up and Follow-Through: Good customer service includes following up with customers to ensure their needs have been met and following through on commitments or resolutions. Following up demonstrates care and concern for the customer’s satisfaction and helps maintain positive relationships over time.
By embodying these qualities, businesses can deliver exceptional customer service that leaves a lasting positive impression on customers and contributes to long-term success.
FAQs (Frequently Asked Questions)
What are Embedded IC PCBs?
Embedded IC PCBs are printed circuit boards where integrated circuits (ICs) are directly embedded within the board itself rather than being mounted on the surface. This integration allows for space-saving, improved performance, and enhanced reliability.
What are the advantages of Embedded IC PCBs?
Embedded IC PCBs offer several advantages, including reduced size, improved performance due to shorter interconnection lengths, enhanced thermal management, increased durability, and potentially lower costs due to fewer external components.
What types of ICs can be embedded in PCBs?
Various types of ICs can be embedded in PCBs, including microcontrollers, memory chips, sensors, and application-specific integrated circuits (ASICs). The choice of IC depends on the specific application and performance requirements.
What are the challenges of manufacturing Embedded IC PCBs?
Manufacturing Embedded IC PCBs can present challenges such as precise alignment and bonding of ICs, managing thermal issues due to the compact design, ensuring reliable electrical connections, and maintaining signal integrity.
What are some common applications of Embedded IC PCBs?
Embedded IC PCBs are used in a wide range of applications, including consumer electronics (e.g., smartphones, tablets), automotive systems, medical devices, industrial automation, aerospace technology, and Internet of Things (IoT) devices.
How are Embedded IC PCBs tested for reliability?
Embedded IC PCBs undergo various testing methods to ensure reliability, including electrical testing to verify functionality, thermal testing to assess heat dissipation, mechanical stress testing to evaluate durability, and environmental testing to assess performance under different conditions (e.g., temperature, humidity).
What factors should be considered when designing Embedded IC PCBs?
Important factors to consider during the design of Embedded IC PCBs include thermal management, signal integrity, power distribution, mechanical stability, material selection, manufacturability, and compliance with industry standards and regulations.
Can existing PCB designs be modified to accommodate embedded ICs?
Yes, existing PCB designs can be modified to accommodate embedded ICs by redesigning the layout, adjusting layer stackup, incorporating additional thermal vias or pads, and optimizing the placement of components to ensure proper functionality and reliability.