FC-CSP Substrates Manufacturer. we can produce the best samllest bump pitch with 100um, the best smallest trace are 9um. and the smallest gap are 9um. most of the design are 15um to 30um trace and spacing.
An FC-CSP substrate, short for Flip-Chip Chip Scale Package substrate, is an essential component within advanced semiconductor packaging. Its primary function is to offer a compact and efficient platform for the mounting and interconnection of microelectronic devices like integrated circuits (ICs) and microprocessors.
Crafted from thin, flat materials such as silicon or laminate, FC-CSP substrates boast intricate arrays of copper traces and vias meticulously etched onto their surfaces. These configurations facilitate seamless electrical connections between the microelectronic components and external circuitry, enabling swift data transmission and effective power delivery.
Furthermore, FC-CSP substrates are engineered to proficiently manage thermal dissipation, averting overheating and ensuring peak performance during operation. This thermal management proficiency is indispensable across diverse sectors, including consumer electronics, telecommunications, automotive systems, and industrial equipment.
As the demand escalates for smaller, faster, and more energy-efficient electronic devices, FC-CSP substrates play an instrumental role in propelling technological advancement and fostering the creation of cutting-edge semiconductor products.
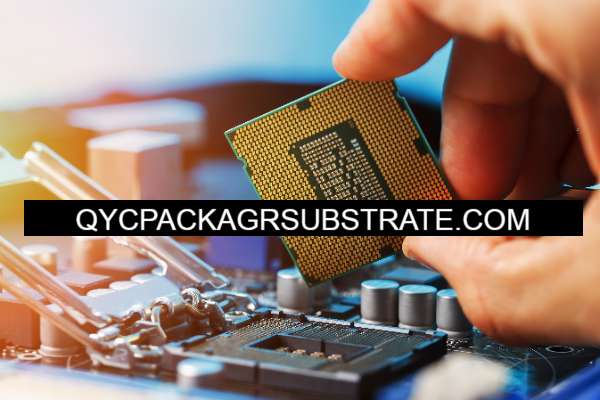
What is the Function of FC-CSP Substrates?
At the heart of advanced semiconductor packaging, FC-CSP (Flip-Chip Chip Scale Package) substrates serve as vital conduits, seamlessly integrating and linking microelectronic components like integrated circuits (ICs) and microprocessors.
Crafted from thin, refined materials such as silicon or laminate, FC-CSP substrates exhibit intricate networks of copper traces and vias delicately etched onto their surfaces. These configurations enable fluid electrical connections, facilitating swift data transmission and efficient power distribution between the microelectronic components and external circuitry.
Moreover, FC-CSP substrates are engineered to skillfully dissipate heat, warding off overheating and preserving the peak performance and reliability of the enclosed devices.
In essence, FC-CSP substrates fuel innovation, propelling the evolution of smaller, swifter, and more energy-efficient electronic devices across a spectrum of industries, from consumer electronics to telecommunications, automotive systems, and industrial sectors.
Why are FC-CSP Substrates Manufacturers Important?
Producers in the domain of FC-CSP (Flip Chip Chip-Scale Package) substrates wield substantial influence across a multitude of dimensions:
Component Fusion: FC-CSP substrates streamline the amalgamation of diverse semiconductor elements within a unified package. This not only enhances functionality and performance but also curtails the overall device footprint. Manufacturers play a pivotal role in fabricating substrates adept at seamlessly accommodating these integrated circuits.
Dimensional Optimization: FC-CSP substrates contribute to the reduction in sizes of electronic devices, making them more compact and portable. This is particularly important in consumer electronics, where the appeal of compact design is a key selling point. Manufacturers are tasked with producing substrates characterized by precise dimensions and heightened reliability to align with the ongoing trend of miniaturization.
Rapid Signal Transmission: Designed for swift electrical signal transmission between integrated circuits, FC-CSP substrates are essential for applications like mobile devices, data centers, and high-performance computing. Manufacturers must ensure that their substrates exhibit low electrical resistance, minimal signal loss, and impeccable signal integrity to meet the demanding requirements of these applications.
Effective Heat Management: Efficiently dissipating heat is crucial for maintaining the reliability and efficiency of electronic devices, especially as they become more powerful and compact. FC-CSP substrates often incorporate advanced thermal management features such as heat sinks and thermal vias. Manufacturers are pivotal in developing substrates with optimal thermal performance.
Quality Assurance and Reliability: Similar to any electronic component, the reliability and quality of FC-CSP substrates are paramount. Manufacturers adhere to stringent quality control standards throughout the production process to ensure that their substrates meet the reliability requirements of diverse industries, including automotive, aerospace, telecommunications, and healthcare.
Driving Innovation and Customization: Manufacturers lead the way in innovating FC-CSP substrates by introducing new materials, processes, and designs to meet the evolving needs of the electronics industry. Collaborating closely with customers, manufacturers customize substrates for specific applications, delivering tailored solutions that optimize both performance and cost.
In essence, the role of FC-CSP substrate manufacturers is pivotal in propelling the continual evolution of electronic devices. They provide packaging solutions for integrated circuits characterized by high performance, compactness, and unwavering reliability.
How are FC-CSP Substrates Related to IC Packaging?
FC-CSP (Flip Chip Chip-Scale Package) substrates play a central role in IC (Integrated Circuit) packaging, intricately woven into the packaging process of integrated circuits. Let’s explore the nuanced connections between FC-CSP substrates and IC packaging:
Prioritizing Compactness and Spatial Efficiency: FC-CSP substrates actively contribute to the overarching goal of miniaturization in electronic devices. In the realm of IC packaging, reducing the overall size of electronic products is crucial, and FC-CSP facilitates this by enabling a compact packaging approach. The flip-chip design involves directly attaching the chip to the substrate, minimizing spatial requirements.
Adopting Flip Chip Technology: FC-CSP relies on flip chip technology, deviating from traditional wire bonding methods. In this approach, the semiconductor chip is inverted and directly affixed to the substrate or package. The advantages of this flip chip methodology include shorter interconnects, reduced parasitic effects, and enhanced electrical performance.
Enhancing Electrical Performance: FC-CSP substrates are meticulously designed to elevate the electrical performance of integrated circuits. The direct chip-to-substrate connection results in shorter signal paths, mitigating signal delays and losses. This attribute is particularly crucial for applications demanding high-speed and high-frequency characteristics, prevalent in contemporary electronic devices.
Integrating Thermal Management: Inherent to IC packaging is the consideration of heat dissipation associated with the integrated circuit. FC-CSP substrates often feature advanced thermal management elements like heat sinks and thermal vias to efficiently disperse heat. Effective thermal management is indispensable for sustaining the reliability and performance of electronic devices.
Facilitating Integration of Multiple Components: FC-CSP facilitates the integration of several semiconductor components within a single package. This involves mounting multiple chips on a singular substrate. In the context of IC packaging, this integration proves advantageous for creating sophisticated and multifunctional devices while optimizing spatial utilization.
Utilizing Advanced Materials and Processes: The development of FC-CSP substrates involves the use of advanced materials and manufacturing processes. This encompasses the incorporation of materials with high thermal conductivity, precision in manufacturing techniques, and innovations in substrate design. These advancements collectively contribute to the overall performance and reliability of IC packaging.
In essence, FC-CSP substrates stand as a fundamental component of IC packaging, offering advantages such as miniaturization, heightened electrical performance, efficient thermal management, and the ability to seamlessly integrate multiple components. The interconnected nature of FC-CSP substrates and IC packaging underscores their pivotal role in shaping compact, high-performance electronic devices.
What are the Differences Between FC-CSP Substrates and Regular PCBs?
The relationship between FC-CSP substrates and IC packaging is foundational and multifaceted:
Mounting and Connectivity Hub: FC-CSP substrates serve as the core for mounting and connecting ICs and other microelectronic components. They provide the structural backbone required for these components and facilitate seamless electrical connections with external circuitry.
Compact Packaging Solution: FC-CSP substrates offer a compact solution for IC packaging, featuring a small form factor and dense interconnects. This compact design optimizes space utilization, resulting in sleek and more efficient electronic devices.
Enablement of High-Speed Data Transmission: Engineered for high performance, FC-CSP substrates support rapid data transmission between ICs and other components. Their design minimizes signal delays and interference, enhancing the speed and efficiency of electronic systems.
Efficient Heat Management: FC-CSP substrates play a vital role in managing heat within IC packaging. They are designed to dissipate heat generated by the ICs during operation, ensuring that the devices maintain optimal temperature conditions for reliable performance.
Enhancement of Reliability and Endurance: By providing robust structural support and efficient thermal management, FC-CSP substrates contribute to the reliability and durability of IC packaging. They can withstand mechanical stress, temperature fluctuations, and environmental factors, ensuring consistent performance over time.
In essence, FC-CSP substrates are indispensable components in IC packaging, offering a compact and high-performance platform for mounting, connecting, and safeguarding integrated circuits in electronic devices.
What are the Main Structures and Production Technologies of FC-CSP Substrates Manufacturers?
The creation of FC-CSP (Flip Chip Chip-Scale Package) substrates is a sophisticated process that melds intricate structures with cutting-edge manufacturing technologies. Let’s delve into the foundational components shaping the structure of FC-CSP substrates and the dynamic production processes orchestrated by manufacturers:
Structural Components of FC-CSP Substrates:
Substrate Material:
FC-CSP substrates are meticulously fashioned from materials, including organic laminate or coreless laminate, and inorganic options like ceramics. The material selection hinges on considerations such as thermal performance, electrical characteristics, and economic viability.
Build-Up Layers:
The architecture of FC-CSP substrates often incorporates a stratified build-up layer structure. Comprising insulating and conductive materials, these layers create a sophisticated routing framework, facilitating efficient signal navigation within a compact spatial framework.
Microvias and Through-Holes:
Facilitating vertical connections between substrate layers, microvias and through-holes assume pivotal roles. Microvias, characterized by smaller diameters, cater to high-density interconnections, while through-holes traverse the substrate, providing vertical connectivity.
Solder Mask and Surface Finish:
Protective solder masks are meticulously applied to shield the circuitry and define areas for precise solder attachment. Surface finishes, such as OSPs or ENIG, streamline the soldering process for flip-chip components.
Dielectric and Conductor Layers:
Dielectric layers insulate between conductive layers, while conductor layers facilitate the seamless flow of electrical signals. The strategic arrangement and thickness of these layers are calibrated to meet exacting electrical and thermal performance standards.
Stiffener and Heat Spreader:
Certain FC-CSP designs incorporate stiffeners to fortify mechanical support. Additionally, heat spreaders or heat sinks may be integrated to optimize thermal management, ensuring effective dissipation of heat from the integrated circuit.
Production Technologies Enlisted by Manufacturers:
Laser Drilling and Ablation:
Manufacturers leverage laser drilling and ablation to carve out microvias and intricate features on the substrate. This precision-driven process is instrumental in achieving high-density interconnections.
Photolithography:
A pivotal step in delineating the circuit pattern involves photolithography. Application of a photoresist layer, exposure to light through a mask, and subsequent development create the circuit pattern for subsequent etching or plating procedures.
Etching:
Chemical etching is deployed to meticulously strip away excess copper from the substrate, delineating the circuit traces with precision. This ensures that conductive pathways align precisely with the specified circuit layout.
Plating:
Electroplating takes center stage to deposit thin metal layers onto the substrate, constructing conductive pathways and enhancing the thickness of metal features. This step is indispensable for layer buildup and attaining the requisite electrical conductivity.
Copper Filling and Planarization:
Copper filling is employed to populate vias and establish a planar surface. Chemical mechanical planarization (CMP) enters the scene to level and homogenize the substrate, ensuring uniformity for subsequent layers.
Screen Printing and Lamination:
The application of the solder mask is a nuanced process involving techniques like screen printing, while lamination serves to bind multiple layers seamlessly. These processes contribute significantly to the holistic structure and functionality of FC-CSP substrates.
Quality Control and Testing:
Stringent quality control measures and comprehensive testing protocols are interwoven throughout the manufacturing trajectory. These encompass checks for dimensional accuracy, electrical continuity, and other performance benchmarks, safeguarding the reliability and functionality of FC-CSP substrates.
In essence, the orchestration of FC-CSP substrates is an intricate dance between diverse materials and state-of-the-art manufacturing methodologies. Manufacturers navigate this complex terrain to realize designs that are not only compact and high-performing but also adept at efficient thermal management to meet the demands of contemporary semiconductor packaging.
Frequently Asked Questions (FAQs)
What roles do FC-CSP substrates play?
FC-CSP substrates serve pivotal functions, including providing structural support for ICs, facilitating seamless electrical connections between ICs and external circuitry, managing thermal dissipation, and augmenting the overall reliability of semiconductor packaging.
What materials are used in FC-CSP substrates?
FC-CSP substrates are primarily constructed from materials like silicon, laminate, or organic substrates. These materials are meticulously chosen for their favorable electrical and thermal characteristics, often characterized by their thin and flat nature.
How are FC-CSP substrates intertwined with IC packaging?
FC-CSP substrates are an integral part of IC packaging, offering a compact and high-performance platform for the assembly, connection, and protection of integrated circuits within electronic devices.
What benefits are associated with FC-CSP substrates?
FC-CSP substrates offer numerous advantages, such as compact packaging solutions, high-speed data transmission capabilities, efficient heat dissipation, and improved reliability and longevity for electronic devices.
How do FC-CSP substrates contribute to electronics miniaturization?
FC-CSP substrates contribute significantly to electronics miniaturization by providing compact packaging solutions. Their small form factor and dense interconnects optimize space utilization, enabling the development of smaller, more portable electronic devices.
Conclusion
In summary, FC-CSP substrates stand as pivotal components in semiconductor packaging, providing a sturdy base for integrating and linking various microelectronic elements. Employing cutting-edge materials and manufacturing techniques, FC-CSP substrates facilitate seamless electrical connections, effective heat dissipation, and heightened reliability within electronic devices.
Their compact dimensions and high-performance attributes propel the ongoing trend toward miniaturization in the electronics sector, enabling the creation of smaller yet potent devices without sacrificing functionality or durability.
As technological progress marches forward, FC-CSP substrates are poised to assume an increasingly central role in shaping the landscape of semiconductor packaging. They drive innovation, meet evolving consumer and industry needs, and promise to be a cornerstone of future electronic advancements.