(Flip-Chip Ball Grid Array) FC/BGA Packaging Substrate manufacturer. We use advanced Msap and Sap technology, High multilayer interconnection substrates from 4 to 20 layers.
FCBGA stands for Flip-Chip Ball Grid Array, and it refers to a type of packaging used in integrated circuits and electronic components. The packaging substrate is a crucial element of FCBGA, providing a foundation for the various components that make up the integrated circuit. Let’s delve into the key aspects of FCBGA packaging substrate:
- Flip-Chip Technology:
-
- In FCBGA, the semiconductor die is flipped upside down, and its active side is connected directly to the packaging substrate. This is in contrast to traditional packaging methods where the die is mounted upright.
- Ball Grid Array (BGA):
-
- The “Ball Grid Array” aspect refers to the arrangement of solder balls on the bottom side of the package. These solder balls serve as electrical connections between the integrated circuit and the circuit board.
- Substrate Material:
-
- The substrate is typically made of materials with good electrical and thermal properties. Common materials include organic substrates such as FR-4 (Flame Retardant 4) or more advanced materials like high-temperature laminates or ceramics.
- Signal Transmission:
-
- The substrate facilitates efficient signal transmission between the die and the external components. It provides a network of traces and vias to route electrical signals between different parts of the integrated circuit and the external environment.
- Thermal Management:
-
- Efficient heat dissipation is crucial for the reliable operation of electronic components. The substrate in FCBGA packages is designed to help dissipate heat generated by the integrated circuit, preventing overheating and ensuring optimal performance.
- Reliability:
-
- FCBGA packaging enhances the reliability of electronic devices by providing a compact and robust structure. The direct connection between the die and the substrate reduces the length of signal paths, minimizing signal delays and electromagnetic interference.
- Size and Form Factor:
-
- FCBGA packages are known for their compact size, making them suitable for applications where space is a critical factor. The ball grid array arrangement allows for a high density of connections in a relatively small area.
- Advanced Manufacturing Processes:
- The production of FCBGA packages involves advanced manufacturing processes, including precision placement of solder balls, fine-pitch traces, and sophisticated assembly techniques.
In summary, FCBGA packaging substrate is a critical component in the construction of integrated circuits, providing a foundation for efficient signal transmission, effective heat dissipation, and overall reliability in electronic devices. The design and materials used in FCBGA packaging contribute to the performance and compact form factor of modern electronic components.
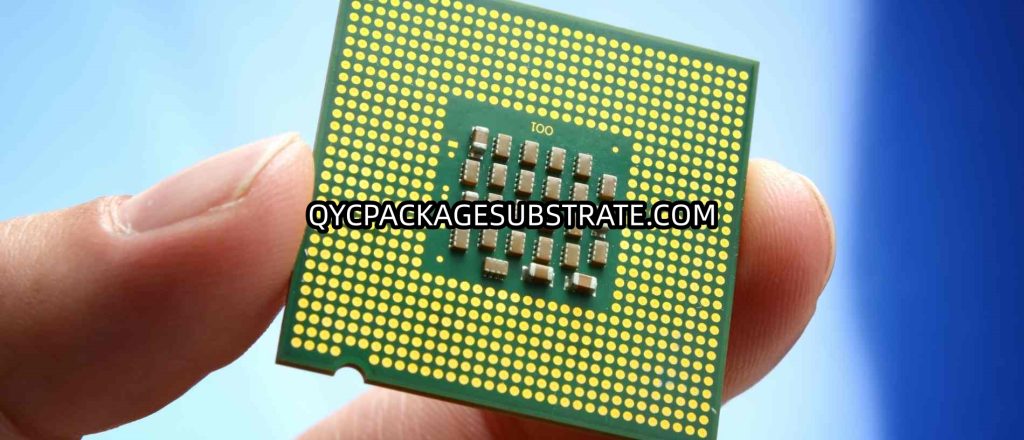
What Functions Does FCBGA Packaging Substrate Serve?
The FCBGA packaging substrate serves several key functions that are integral to the overall reliability and performance of electronic devices. Here are the multifaceted functions of the FCBGA packaging substrate:
- Efficient Signal Transmission:
-
- The substrate provides a network of traces and vias that facilitate the efficient transmission of electrical signals between the semiconductor die and external components. The close proximity of the die to the substrate in the flip-chip configuration minimizes signal delays and reduces the length of signal paths, enhancing overall signal integrity.
- Electrical Interconnection:
-
- Solder balls on the bottom of the package form a ball grid array (BGA), serving as electrical connections between the integrated circuit and the circuit board. This BGA arrangement allows for a high density of interconnections, making it suitable for complex electronic systems.
- Heat Dissipation:
-
- FCBGA packaging substrate is designed to help dissipate heat generated by the integrated circuit during operation. The efficient heat dissipation is crucial for preventing overheating and maintaining the optimal operating temperature of the electronic components.
- Mechanical Support:
-
- The substrate provides mechanical support and protection for the delicate semiconductor die. It helps in maintaining the structural integrity of the overall package and protects the die from external mechanical stresses and impacts.
- Compact Form Factor:
-
- FCBGA packaging enables a compact form factor, making it suitable for applications where space is a critical factor. The flip-chip arrangement allows for a more compact design compared to traditional packaging methods, contributing to the miniaturization of electronic devices.
- Reduced Electromagnetic Interference (EMI):
-
- The shorter signal paths and the close proximity of the die to the substrate help reduce electromagnetic interference. This is particularly important in high-frequency applications where minimizing EMI is crucial for signal integrity.
- Enhanced Reliability:
-
- The direct connection between the semiconductor die and the substrate, along with the overall design of FCBGA, contributes to the enhanced reliability of electronic devices. The reduced number of interconnects and simplified assembly processes can lead to fewer points of failure.
- Advanced Manufacturing Processes:
- The substrate is manufactured using advanced processes to ensure precision in solder ball placement, fine-pitch traces, and overall assembly. This contributes to the high quality and consistency of FCBGA packages.
In summary, the FCBGA packaging substrate plays a crucial role in ensuring efficient signal transmission, effective heat dissipation, and overall reliability in electronic devices. Its multifunctional capabilities contribute to the performance and durability of integrated circuits in a variety of applications.
What Are the Varieties of FCBGA Packaging Substrate?
FCBGA packaging substrates come in various types, each tailored to meet specific electronic requirements. Here are some common varieties of FCBGA packaging substrates:
- Organic Substrates:
-
- FR-4 (Flame Retardant 4): FR-4 is a common organic substrate material used in FCBGA packaging.FR-4 substrates, characterized by their flame-retardant properties and cost-effectiveness, are popularly employed in various electronic applications. These substrates consist of a glass-reinforced epoxy laminate and are widely utilized for their versatility across different electronic devices and systems.
- High-Temperature Laminates:
-
- Some FCBGA packages use high-temperature laminates as substrates. These laminates are designed to withstand elevated temperatures, making them suitable for applications where thermal stability is crucial.
- Ceramic Substrates:
-
- Ceramic substrates, including materials like alumina (Al2O3) or aluminum nitride (AlN), find application as substrates in specific FCBGA packages. These ceramic substrates excel in thermal conductivity, making them well-suited for applications where effective heat dissipation is crucial.
- Polyimide Substrates:
-
- Polyimide is a flexible and high-temperature-resistant material that is sometimes used as a substrate in FCBGA packaging. Polyimide substrates are suitable for applications where flexibility and thermal stability are important.
- Embedded Passives Substrates:
-
- Some FCBGA substrates incorporate embedded passive components, such as resistors and capacitors. This integration helps save space on the circuit board and can improve electrical performance in certain applications.
- Invar or Alloy Substrates:
-
- Invar, a low-expansion nickel-iron alloy, or other specialized metal alloys may be used as substrates in certain FCBGA packages. These substrates are chosen for their specific thermal and mechanical properties.
- Glass Fiber Substrates:
-
- Glass fiber substrates are used in some FCBGA packages to provide a balance of mechanical strength and electrical performance. The glass fibers enhance the substrate’s rigidity and durability.
- Metal Core Substrates:
- Some FCBGA packages use metal core substrates, typically aluminum or copper. These substrates offer excellent thermal conductivity, helping to dissipate heat effectively.
The choice of substrate material depends on various factors, including thermal requirements, cost considerations, electrical performance, and the specific needs of the electronic application. Manufacturers select the substrate type that best aligns with the intended use of the FCBGA package, balancing factors such as thermal management, signal integrity, and mechanical robustness.
How Does FCBGA Packaging Substrate Interact with IC Packages?
The symbiotic relationship between FCBGA (Flip-Chip Ball Grid Array) packaging substrate and IC (Integrated Circuit) packages is characterized by a collaborative effort to enhance the overall performance of electronic devices. Various chip package technologies leverage the advantages of FCBGA in different ways. Here are some categories that showcase how FCBGA packaging substrate interacts with IC packages for improved performance:
- Flip-Chip Technology:
-
- FCBGA is inherently tied to flip-chip technology, where the semiconductor die is flipped upside down, and its active side is connected directly to the packaging substrate. This direct connection minimizes the length of signal paths, reduces inductance, and enhances signal integrity.
- Ball Grid Array (BGA) Configuration:
-
- FCBGA utilizes a ball grid array configuration on the substrate. Solder balls form electrical connections between the integrated circuit and the circuit board. The BGA arrangement allows for a high density of interconnections, enabling the packaging of complex and high-performance ICs.
- Enhanced Thermal Management:
-
- The FCBGA packaging substrate plays a crucial role in heat dissipation. By providing a direct path for heat to flow from the semiconductor die to the substrate, it helps manage thermal issues more effectively. This is particularly important for high-performance ICs that generate significant heat during operation.
- Advanced Packaging Materials:
-
- FCBGA packaging substrates can be made from various materials, including ceramics like alumina or aluminum nitride. These materials offer excellent thermal conductivity and electrical properties, contributing to the reliability and performance of IC packages.
- Miniaturization and Compact Form Factor:
-
- FCBGA packaging allows for a more compact form factor compared to traditional packaging methods. This is advantageous for applications where space is limited, and miniaturization is a priority. The compact design contributes to the overall efficiency and portability of electronic devices.
- Mixed-Signal and RF Applications:
-
- FCBGA is well-suited for mixed-signal and radio frequency (RF) applications where signal integrity is critical. The direct connections and minimized parasitic effects make FCBGA an attractive choice for ICs that require precise analog and RF performance.
- Integration of Embedded Components:
- Some FCBGA packages integrate embedded passive components within the substrate, enhancing the overall functionality and reducing the need for additional discrete components on the circuit board.
In summary, the synergy between FCBGA packaging substrate and IC packages is evident in the enhanced performance, thermal management, and signal integrity achieved through the utilization of flip-chip technology and advanced packaging configurations. This collaboration contributes to the evolution of high-performance electronic devices across various applications.
How Does FCBGA Packaging Substrate Differ from Traditional PCBs?
The differences between FCBGA (Flip-Chip Ball Grid Array) packaging substrate and traditional printed circuit boards (PCBs) are significant, and they stem from their distinct roles in electronic assemblies. Let’s explore these differences, including FCBGA substrate, high-density interconnect (HDI) substrate, and substrate-like PCB (SLP):
- FCBGA Packaging Substrate:
-
- Role: FCBGA substrate primarily serves as the foundation for integrated circuits (ICs) using flip-chip technology. It provides a direct connection between the semiconductor die and the external circuit through a ball grid array (BGA) configuration.
- Design: FCBGA substrates are crafted to streamline effective signal transmission, proficiently dissipate heat, and deliver a space-efficient form factor. Typically composed of materials with commendable thermal conductivity, like ceramics such as alumina or aluminum nitride, these substrates play a pivotal role in optimizing the performance and thermal characteristics of integrated circuits.
- Connection Method: In FCBGA, the semiconductor die is flipped upside down, and solder balls on the bottom of the package form electrical connections with the circuit board.
- High-Density Interconnect (HDI) Substrate:
-
- Role: HDI substrates bridge the gap between traditional PCBs and advanced packaging technologies like FCBGA. They offer increased routing density, allowing for more compact designs with smaller vias and finer traces.
- Design: HDI substrates often incorporate microvias, buried vias, and blind vias to enable more complex and densely packed circuits. This enhances signal integrity and allows for miniaturization in electronic devices.
- Connection Method: HDI substrates use advanced fabrication techniques to create intricate layer structures with fine-pitch features.
- Substrate-Like PCB (SLP):
- Role: SLP is a type of PCB that mimics the characteristics of FCBGA substrates in terms of materials and manufacturing processes. It provides improved electrical performance and thermal management while maintaining compatibility with traditional PCB assembly processes.
- Design: SLPs often use high-performance materials, similar to those in FCBGA substrates, to enhance electrical and thermal properties. They may also incorporate fine-pitch traces and microvias for increased routing density.
- Connection Method: SLPs can be integrated into traditional PCB assembly processes, using soldered connections like standard PCBs.
In summary, FCBGA packaging substrates differ from traditional PCBs in their specific role as a direct connection point for flip-chip technology. HDI substrates and SLPs represent intermediate technologies that incorporate some features of FCBGA substrates, such as advanced materials and increased routing density, into traditional PCB designs. Each of these technologies caters to different electronic assembly requirements, balancing factors such as miniaturization, signal integrity, and thermal management.
What Constitutes the Anatomy and Production Technologies of FC/BGA Packaging Substrate?
The anatomy of FCBGA (Flip-Chip Ball Grid Array) packaging substrate involves a complex structure that plays a crucial role in the performance of integrated circuits. Here, we’ll delve into the components and production technologies associated with FCBGA packaging substrates, focusing on advancements in High-Density Interconnect (HDI) fabrication and the semi-additive method:
Anatomy of FCBGA Packaging Substrate:
- Base Material:
-
- The base material of the substrate is a critical element. It is often made of ceramics, such as alumina (Al2O3) or aluminum nitride (AlN), to provide excellent thermal conductivity. The choice of material is essential for effective heat dissipation.
- Copper Traces and Layers:
-
- Copper traces form the conductive pathways on the substrate, allowing for the transmission of electrical signals. In FCBGA, these traces are designed with precision to minimize signal delays and maintain signal integrity.
- Solder Mask:
-
- Solder mask is applied to the substrate to insulate the copper traces and prevent short circuits. It also provides a protective layer for the substrate against environmental factors and contaminants.
- Solder Balls:
-
- Solder balls are located on the bottom side of the FCBGA package. They form the ball grid array (BGA) configuration and serve as the electrical connections between the integrated circuit and the circuit board.
- Die Attach Material:
- The die attach material is used to bond the semiconductor die to the substrate. This material must provide a reliable and thermally conductive connection to facilitate efficient heat dissipation.
Production Technologies:
- High-Density Interconnect (HDI) Fabrication:
-
- HDI fabrication technology has significantly advanced the production of FCBGA substrates. It involves creating intricate structures with fine-pitch traces, microvias, and high-density interconnections. HDI allows for increased routing density, enabling more compact and efficient designs.
- Laser Drilling and Microvias:
-
- Laser drilling is employed to create microvias, which are small holes that connect different layers of the substrate. Microvias contribute to the reduction of signal path lengths and enhance the overall performance of the FCBGA package.
- Semi-Additive Method:
-
- The semi-additive method is an advanced manufacturing technique that involves selectively adding material to create circuit patterns. It allows for precise control in building up layers on the substrate, offering increased flexibility and accuracy in designing complex structures.
- Advanced Photolithography:
- Photolithography is a key process in FCBGA substrate fabrication. Advanced photolithography techniques enable the creation of fine features and patterns on the substrate, ensuring the precision required for signal transmission and interconnections.
In summary, the anatomy of FCBGA packaging substrate involves a carefully designed structure with materials and components optimized for efficient signal transmission, heat dissipation, and overall reliability. The production technologies, including HDI fabrication and the semi-additive method, continue to evolve to meet the demands of high-performance electronic devices.
FAQs
What are the key advantages of FCBGA packaging substrate?
FCBGA packaging substrate offers several advantages, including efficient signal transmission, enhanced thermal management, compact form factor, and improved reliability. The direct connection between the semiconductor die and the substrate contributes to shorter signal paths, reducing signal delays and electromagnetic interference.
How is FCBGA substrate different from traditional PCBs?
FCBGA substrate is specifically designed for flip-chip technology, where the semiconductor die is flipped upside down, and solder balls on the bottom form electrical connections. Unlike traditional PCBs, FCBGA substrates prioritize compact design, efficient heat dissipation, and direct die-to-substrate connections for improved performance.
What materials are commonly used in FC/BGA packaging substrate?
FCBGA substrates commonly utilize materials with high thermal conductivity, including ceramics like alumina or aluminum nitride. These materials play a crucial role in efficient heat dissipation. The selection of the substrate material is contingent upon the particular needs and specifications of the application at hand.
In what applications is FCBGA packaging commonly employed?
FCBGA packaging finds widespread applications in high-performance integrated circuits, including microprocessors for computers, graphics processing units (GPUs), network processors, and various sophisticated electronic devices. It is extensively utilized across diverse industries such as telecommunications, computing, and consumer electronics.
How is FCBGA substrate manufactured, and what advanced technologies are involved?
The manufacturing of FCBGA substrates involves advanced technologies such as High-Density Interconnect (HDI) fabrication, laser drilling for microvias, advanced photolithography, and the semi-additive method. These techniques allow for precise circuit patterns, fine-pitch traces, and increased routing density.
What criteria are considered in the selection of FCBGA packaging substrate?
The selection of FCBGA substrate involves considerations such as thermal conductivity, electrical performance, material compatibility, and the specific requirements of the electronic application. The substrate material, design complexity, and manufacturing capabilities play crucial roles in the selection process.
How does FCBGA packaging contribute to the miniaturization of electronic devices?
A: FCBGA packaging contributes to miniaturization by providing a compact form factor. The flip-chip configuration and ball grid array arrangement allow for a high density of connections in a small area, making FCBGA suitable for applications where space is a critical factor.
Conclusion:
In conclusion, the FCBGA packaging substrate emerges as a pivotal component in the ongoing evolution of electronic devices, skillfully amalgamating functionality and reliability. As technological progress continues to unfold, a comprehensive understanding of the intricacies of FCBGA packaging substrate becomes imperative for both engineers and enthusiasts. Embark on this journey where innovation converges with precision, and bear witness to the pulsating core of cutting-edge electronics.