FCCSP Flip Chip Package Substrate Manufacturing. High speed and high frequency material packaging substrate production. Advanced packaging substrate production process and technology.
FCCSP, or Flip Chip Package Substrate, stands out as an innovative integrated circuit packaging solution that deviates from conventional methods. This technology involves flipping the chip and directly linking its exposed metal solder balls to corresponding pads on the packaging substrate. Unlike traditional packaging techniques, FCCSP offers enhanced performance and reliability.
By inverting the chip, FCCSP achieves shorter signal transmission paths, ultimately boosting chip performance while simultaneously reducing the overall package size. The direct connection of solder balls to pads on the substrate adds to the integration of the system. This approach proves beneficial in terms of meeting the demands for compact, lightweight, and high-performance chip packaging, especially in applications such as mobile devices, communication equipment, and computer systems.
One notable advantage of Flip Chip technology lies in its ability to decrease signal delays due to the shortened interconnects. This results in an improved operational speed for the chip. FCCSP, thus, not only caters to the need for advanced semiconductor processes but also plays a pivotal role in driving progress within the electronics industry.
In summary, FCCSP serves as a transformative packaging solution, fostering advancements in chip packaging by combining superior performance, reliability, and adaptability to diverse technological landscapes.
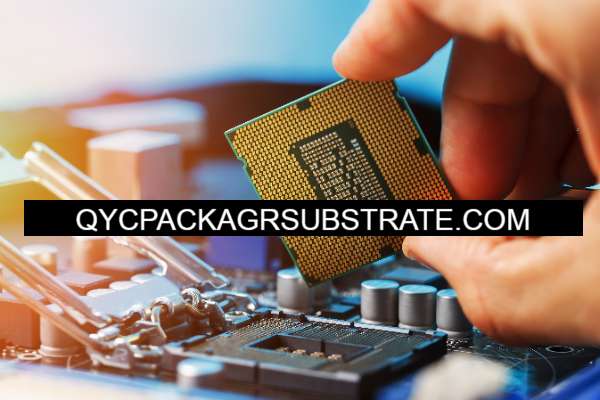
What is the Function of FCCSP Flip Chip Package Substrate?
The FCCSP (Flip Chip Package Substrate) stands out as a linchpin in the realm of flip chip packaging technology, wielding diverse functionalities that bolster the prowess and reliability of integrated circuits:
Electrical Connectivity Hub: At its fundamental core, FCCSP establishes a robust electrical nexus between the flip chip (the semiconductor maestro) and the package substrate. This entails forging direct links between the chip’s solder bumps and their counterparts on the substrate, crafting an expressway for signal transmission.
Signal Velocity Maestro: FCCSP takes the stage in orchestrating a symphony of efficient signal transmission between the chip and the package substrate. By trimming the lengths of interconnects, it conducts a melody that minimizes signal delays, thus orchestrating an uptick in the overall speed and virtuosity of the integrated circuit.
Thermal Maestro: The substrate assumes the role of a thermal maestro, conducting the symphony of heat dissipation emanating from the chip’s performance. FCCSP contributes to this harmonious act, ensuring the semiconductor luminary operates within the sweet spot of temperature, thereby harmonizing optimal performance and longevity.
Guardian of Mechanical Harmony: FCCSP, donning the mantle of a guardian, provides mechanical support, fortifying the structural integrity of the flip chip. This vigilant protection shields the integrated circuit from the rigors of mechanical duress and external whims that might challenge its instrumental functionality.
Efficiency Architect of Size and Weight: A notable laurel in FCCSP’s crown is its prowess in sculpting the overall size and weight of the integrated circuit package. This efficiency virtuoso becomes particularly resonant in applications where spatial constraints and weight nuances take center stage, such as in the orchestration of portable electronic symphonies.
Maestro of Integration Mastery: Through the artistry of direct chip-to-substrate connection, FCCSP assumes the mantle of a maestro, orchestrating a higher level of integration. This feature, akin to a crescendo, proves invaluable in applications that demand a tapestry of densely woven and miniaturized electronic components.
In summation, the FCCSP Flip Chip Package Substrate emerges not just as a component but as a virtuoso, harmonizing electrical, thermal, and mechanical cadences. Its design and multifaceted symphony contribute harmoniously to the crescendo of efficiency, reliability, and overall virtuosity of integrated circuits across diverse electronic compositions.
What are the Different Types of FCCSP Flip Chip Package Substrate?
FCCSP (Flip Chip Package Substrate) manifests in diverse types, each finely tuned to cater to specific applications and performance prerequisites. The choice of a particular FCCSP variant is contingent upon variables such as intended utility, performance benchmarks, and manufacturing intricacies. Here’s a survey of some prevalent incarnations:
Build-Up Substrate (BUS): The BUS variety leverages build-up substrate technology, incorporating a stratagem of multiple layers of insulating material and conductive traces meticulously stacked. Renowned for its prowess in achieving heightened wiring density, BUS facilitates more streamlined designs and augments electrical performance.
Organic Substrate: Forging from materials like FR-4, organic substrates present themselves as a cost-effective FCCSP solution. Marked by their lightweight nature and proficient electrical insulation, organic substrates, however, may bear limitations in thermal conductivity relative to their counterparts.
Ceramic Substrate: Crafted from materials such as alumina or aluminum nitride, ceramic FCCSP substrates earn their stripes in the realm of thermal conductivity. Tailored for applications necessitating effective heat dissipation, especially in high-powered electronic devices.
Laminated Substrate: The laminated substrate breed, characterized by layers bonded together, strikes a harmonious balance between cost considerations, electrical proficiency, and manufacturing expediency. A staple in diverse electronic applications.
Flexible Substrate: Enlisting materials like polyimide, the flexible substrate breed gives rise to a pliable FCCSP iteration. Suited for applications calling for flexibility or conformability, such as in the domain of wearable devices or the burgeoning field of flexible electronics.
Copper Pillar Substrate: This avant-garde technology substitutes the conventional solder bumps with copper pillars for chip-substrate interconnection. Bestowing advantages in realms of reliability, thermal performance, and signal integrity.
High-Density Interconnect (HDI) Substrate: HDI substrates, an epitome of cutting-edge technology, deploy advanced methodologies to achieve elevated wiring densities. This empowers intricate and miniaturized designs, a boon in applications where spatial constraints reign supreme.
Fan-Out Wafer-Level Package (FOWLP): A dynamic incarnation of FCCSP, FOWLP envelopes the entire wafer, orchestrating the redistribution of chips over an expanded area. This modus operandi finds favor in the realm of high-density packaging, particularly in the echelons of advanced semiconductor processes.
The selection among these FCCSP incarnations hinges upon the nuanced demands of the application, encompassing considerations of electrical performance, thermal dynamics, form factor intricacies, and cost-effectiveness. Manufacturers, akin to discerning artisans, meticulously navigate the landscape to select the most fitting variant aligned with the imperatives set by the developmental goals of the electronic device in focus.
What is the Relationship Between FCCSP Flip Chip Package Substrate and IC Packaging?
The alliance between FCCSP (Flip Chip Package Substrate) and IC (Integrated Circuit) packaging is a pivotal and interdependent one, showcasing a synergistic relationship that influences the way semiconductor devices are connected and encapsulated. Here’s a nuanced exploration of their interconnection:
Packaging Synergy: FCCSP, standing as a distinct packaging technology, is intricately woven into the broader landscape of IC packaging methodologies. It introduces an innovative paradigm by directly linking the flip chip to the package substrate, ushering in advantages in signal integrity, thermal efficiency, and a transformative shift in size reduction.
Electrical Nexus Establishment: IC packaging inherently revolves around the establishment of reliable electrical connections between the semiconductor device and its external environment. In the case of FCCSP, this connectivity is achieved through the direct fusion of solder balls or bumps on the flip chip with corresponding pads on the substrate, forming a robust electrical pathway.
Signal Transmission Mastery: Central to IC packaging is the facilitation of seamless signal transmission between the semiconductor device and the external milieu. FCCSP, with its focus on minimizing interconnect lengths, emerges as an adept facilitator, mitigating signal delays and elevating the overall speed and performance of the integrated circuit.
Thermal Symphony Conductor: IC packaging, including FCCSP, orchestrates a symphony of thermal management. FCCSP contributes by allowing the efficient dissipation of heat from the flip chip through the substrate, a critical aspect in maintaining the optimal operating temperature of the semiconductor device.
Size and Form Factor Shaping: The realm of IC packaging, embodied by FCCSP, actively shapes the overall size and form factor of electronic devices. The compact and streamlined nature of FCCSP paves the way for smaller, lighter packages, driving advancements in portable electronics and the realization of miniaturized systems.
Integration Density Enabler: FCCSP stands as an enabler of high integration density. By forging a direct connection between the chip and the substrate, FCCSP facilitates more compact designs, fostering the integration of intricate electronic components into a confined space.
Materials Alchemy and Manufacturing Mastery: The choice of materials and the orchestration of manufacturing processes play pivotal roles in the realm of IC packaging, including the specific selection of FCCSP. Tailored materials and processes cater to diverse applications, aligning with objectives related to performance, reliability, and cost considerations.
In essence, FCCSP represents a distinctive methodology within the expansive canvas of IC packaging. It not only exemplifies an advanced packaging technique but also actively shapes the landscape of modern electronics by addressing the evolving demands for enhanced performance, size reduction, and effective thermal management. The relationship between FCCSP and IC packaging is dynamic, with FCCSP emerging as a catalyst that shapes and refines the characteristics and capabilities of the packaged integrated circuits.
What are the Differences Between FCCSP Flip Chip Package Substrate and Traditional PCBs?
FCCSP (Flip Chip Package Substrate) and traditional PCBs (Printed Circuit Boards) are distinctive players in the electronic orchestra, each contributing its unique notes to the symphony. Let’s delve into the nuances that differentiate FCCSP from traditional PCBs:
Chip Mounting Choreography:
FCCSP: In the avant-garde dance of FCCSP, the chip takes a daring leap, flipping and embracing an upside-down stance on the substrate. This unconventional move facilitates direct electrical connections between the chip and the substrate.
Traditional PCB: On the traditional PCB stage, chips follow a more traditional posture, standing upright and establishing electrical connections through methods like wire bonding.
Interconnection Ballet:
FCCSP: The interconnection ballet in FCCSP features solder bumps or balls on the chip elegantly partnering with corresponding pads on the substrate. This dance creates a direct and efficient electrical duet.
Traditional PCB: Traditional PCBs showcase a diverse repertoire of interconnection techniques, including through-hole vias, surface mount pads, and wire bonding, involving additional components like leads and connectors.
Signal Transmission Rhythm:
FCCSP: The direct chip-to-substrate connection in FCCSP orchestrates a concise signal transmission rhythm, reducing delays and elevating the overall speed and harmony of signal integrity.
Traditional PCB: In the traditional PCB composition, signal paths may traverse longer routes due to the chip’s upright position, potentially introducing delays to the symphony.
Integration Waltz:
FCCSP: FCCSP takes the lead in the integration waltz, showcasing a penchant for high density. The direct chip-to-substrate connection choreographs a compact design, allowing for an elegant integration of diverse components within a confined space.
Traditional PCB: Traditional PCBs, with their own grace, achieve commendable integration density, yet the FCCSP’s dance often crafts a more spatially efficient performance.
Thermal Ballet:
FCCSP: In the thermal ballet, FCCSP shines. The direct chip connection gracefully dissipates heat through the substrate, conducting a symphony of cooling for the semiconductor device.
Traditional PCB: Thermal management in traditional PCBs may involve additional performers such as heat sinks or fans, dancing in tandem but not inherently intertwined with the substrate.
Materials and Manufacturing Composition:
FCCSP: FCCSP exhibits its own composition in materials and manufacturing processes, tailored to the demands of flip chip packaging, presenting a unique melody compared to the traditional PCB composition.
Traditional PCB: Traditional PCBs, composed with materials like the familiar FR-4, follow established manufacturing scores that resonate across a diverse spectrum of electronic applications.
Applications Showcase:
FCCSP: FCCSP takes center stage in applications where the spotlight shines on miniaturization, high-performance, and the allure of a direct chip connection. It graces the stages of mobile devices, high-speed communication equipment, and cutting-edge computing systems.
Traditional PCB: Traditional PCBs, versatile in their repertoire, find resonance across diverse arenas—from the grand theaters of consumer electronics to the industrial stages of machinery, where the specific nuances of FCCSP may not be the headlining act.
In essence, FCCSP and traditional PCBs script their own sonatas through chip choreography, interconnection ballets, signal symphonies, integration waltzes, thermal harmonies, materials, manufacturing compositions, and the specific applications where they take the spotlight. The choice between them is akin to selecting the right composition for an orchestral performance, meticulously curated based on the nuanced needs of the electronic device at the heart of the musical production.
What are the Main Structure and Production Technologies of FCCSP Flip Chip Package Substrate?
The FCCSP (Flip Chip Package Substrate) is crafted with a unique structure and production technologies tailored to its distinctive role in fostering a direct connection between the chip and the substrate. Let’s embark on an exploration of the primary structure and production intricacies associated with FCCSP:
Distinctive Structure:
Substrate Composition:
FCCSP substrates exhibit versatility in material choices, ranging from organic laminates and build-up substrates to ceramics like alumina or aluminum nitride. Flexible materials such as polyimide may also find application. The selection depends on factors like thermal conductivity, electrical properties, and specific application needs.
Conductive Pathways:
The substrate hosts a intricate network of conductive traces, intricately patterned on its surface. These traces act as conduits for electrical signals, linking various points on the chip to external connection points and forming the essential communication channels.
Solder Bumps or Balls:
A hallmark of FCCSP is the strategic placement of solder bumps or balls on the chip’s active side. These metallic elements serve as direct connection points to the substrate, facilitating seamless electrical contact. The choice of solder material is dictated by considerations of conductivity and reliability during the reflow process.
Incorporated Passive Components:
Depending on the application’s requirements, FCCSP may integrate passive components like resistors, capacitors, and inductors directly into the substrate. This integration optimizes electrical performance and enhances the overall functionality of the package.
Production Expertise:
Substrate Fabrication:
The production journey commences with the creation of the substrate. Techniques such as lamination, thin-film deposition, and photolithography may be employed for organic substrates, while ceramic substrates undergo processes like sintering.
Creation of Conductive Paths:
The formation of conductive traces involves precision techniques such as copper deposition and etching for organic substrates. For ceramic substrates, thick-film processes might be employed. High-Density Interconnect (HDI) technologies contribute to achieving fine-pitch traces, crucial for miniaturized designs.
Solder Bump Placement:
The placement of solder bumps on the chip is a pivotal step in the FCCSP production dance. Techniques such as solder ball attach (SBA) or solder paste printing are utilized for this purpose. Lead-free solder alloys are often chosen to align with environmental standards.
Flip Chip Bonding Elegance:
The core of FCCSP production lies in the flip chip bonding process. The chip, positioned with its active side facing down, aligns its solder bumps with corresponding pads on the substrate. A controlled reflow process ensues, melting the solder and creating robust electrical connections.
Underfill Enchantment:
Post flip chip bonding, an underfill material may be applied to enhance mechanical stability and guard against thermal stresses. This underfill material undergoes curing to create a resilient encapsulation, fortifying the structure.
Final Flourishes:
Additional steps, including the attachment of heat spreaders or the integration of passive components, are orchestrated based on the unique demands of the application. The final FCCSP emerges, ready to be seamlessly integrated into the electronic assembly.
In essence, these intricate production technologies harmonize to create an FCCSP that embodies efficiency, miniaturization, and thermal optimization. This package stands as a testament to the prowess of direct chip connection, making it a preferred choice for applications that demand cutting-edge performance and space efficiency.
FAQs
What are the standout features of FCCSP Substrates?
Key features include a diverse array of substrate materials, conductive traces designed for efficient signal transmission, solder bumps or balls for direct chip interfacing, and the potential integration of passive components. These features collectively contribute to the substrate’s efficiency and the overall performance of the semiconductor package.
How does FCCSP differ from other prevalent Packaging Technologies?
In contrast to traditional wire bonding or chip-on-board technologies, FCCSP distinguishes itself by establishing a direct connection between the chip and the substrate. This unique approach results in shorter signal paths, heightened electrical performance, and increased opportunities for miniaturization.
What are the notable Advantages of choosing FCCSP?
Advantages encompass improved electrical performance, minimized signal delays, high integration density, effective thermal management, and applicability to scenarios demanding both miniaturization and high-speed performance.
How is the process of FCCSP Flip Chip Bonding accomplished?
Flip chip bonding involves carefully placing the chip with its active side facing downward and aligning solder bumps or balls with corresponding pads on the substrate. Subsequently, a controlled reflow process takes place, melting the solder and establishing robust electrical connections.
Which Applications are well-suited for FCCSP?
FCCSP finds its niche in applications demanding superior performance, miniaturization, and a direct chip connection. Common applications include mobile devices, high-speed communication equipment, and sophisticated computing systems.
Conclusion
In conclusion, FCCSP (Flip Chip Package Substrate) emerges as a cutting-edge semiconductor packaging technology, characterized by its direct chip-to-substrate connection. As we navigate through the intricacies of FCCSP, it becomes evident that manufacturers specializing in this domain play a pivotal role in crafting substrates that are not just components but technological masterpieces.
The distinctive features of FCCSP substrates, from diverse material options to intricate conductive pathways and the integration of passive components, collectively contribute to the efficiency, miniaturization, and enhanced thermal management of semiconductor devices.
Set against the backdrop of other packaging technologies, FCCSP stands out with its direct chip connection, paving the way for shorter signal paths and heightened electrical performance. The advantages of FCCSP, including reduced signal delays, high integration density, and adaptability to applications demanding miniaturization and high-speed performance, position it as a preferred choice in the ever-evolving landscape of electronics.
Delving into the materials used in FCCSP substrates, the dance of conductive traces, the precision of flip chip bonding, and the symphony of applications where FCCSP excels, we uncover a technology that not only meets but anticipates the demands of modern electronic devices.
Moreover, the adherence to stringent quality standards by FCCSP manufacturers, such as ISO 9001, underscores their commitment to delivering reliable and high-performance substrates. When it comes to choosing an FCCSP manufacturer, considerations like industry experience, reputation, and customization capabilities come to the forefront, ensuring a seamless integration of FCCSP substrates into the broader electronic ecosystem.
In essence, FCCSP is not merely a technological advancement; it’s an orchestrated composition, a harmonious blend of materials, processes, and innovation. As we witness the crescendo of direct chip connection and the refined ballet of semiconductor packaging, FCCSP stands as a testament to the ever-evolving pursuit of efficiency, miniaturization, and performance in the realm of electronic packaging.