Flip Chip CSP Package Substrate Manufacturer. we can produce the best samllest bump pitch with 100um, the best smallest trace are 9um. and the smallest gap are 9um. most of the design are 15um to 30um trace and spacing.
In the dynamic landscape of semiconductor packaging, Flip Chip CSP (Chip Scale Package) stands out as a groundbreaking technology. Its distinctive method of flipping the chip onto the substrate, positioning the active side downward, introduces a design philosophy centered on efficiency and elegance. In the intricate ballet of Flip Chip CSP packaging, the substrate assumes a prominent role, acting as the vital bridge between the integrated circuit (IC) and the printed circuit board (PCB).
Crafted from materials like organic laminate or ceramics, the substrate plays a multifaceted part. Beyond facilitating electrical connections, it adeptly manages heat dissipation and provides essential structural support for the chip. In the elaborate choreography of Flip Chip CSP packaging, the substrate orchestrates the delicate interplay of electrical connections between the chip and external circuitry. Its design intricacies resemble a finely tuned symphony, navigating the densely packed interconnects beneath the chip to foster a high-density, compact form factor.
The term “CSP” underscores the aspiration to achieve a packaging size that seamlessly aligns with the chip’s actual dimensions, ultimately reducing the overall footprint of the device. Flip Chip CSP packages boast a spectrum of advantages, including heightened electrical performance, superior thermal management, and the flexibility to accommodate increased I/O (Input/Output) counts. These attributes position them as the preferred solution for applications where spatial constraints are paramount, such as in mobile devices, wearables, and other compact electronic systems.
To sum up, the substrate in Flip Chip CSP packages assumes a prominent role in the ever-evolving field of semiconductor packaging. Its adept management of direct chip mounting, coupled with the provision of crucial electrical connections and thermal management, sets the stage for the creation of electronic devices that not only embody compactness but also epitomize efficiency.
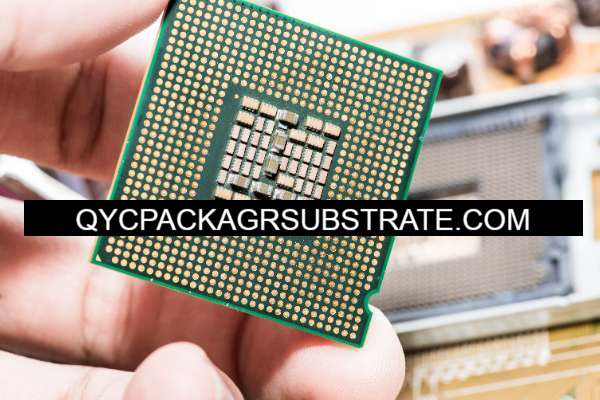
What Functions Does Flip Chip CSP Package Substrate Serve?
Within the Flip Chip CSP (Chip Scale Package), the substrate emerges as a dynamic cornerstone, undertaking a spectrum of roles to elevate the performance and dependability of the semiconductor package. Let’s delve into the diverse functions that the substrate fulfills:
Conduit for Electrical Harmony: Serving as a vital conduit, the substrate facilitates seamless electrical connections between the chip and external components like the printed circuit board (PCB). It establishes intricate pathways, ensuring a smooth flow of signals and fostering cohesive communication within the electronic system.
Mastering Heat Symphony: A maestro in thermal management, the substrate takes the stage in orchestrating the dissipation of heat generated by the operational chip. By providing an efficient thermal pathway, it conducts a symphony that maintains an optimal temperature, preserving the chip’s reliability and sustained performance.
Architect of Structural Resilience: The substrate acts as the architect of structural fortitude, imparting essential support to the chip. This robust structural foundation shields the chip from mechanical stresses and environmental variables, preventing potential issues such as warping and damage that could compromise the device’s functionality.
Enabler of Miniaturization and Connectivity Ballet: In the grand performance of Flip Chip CSP, the substrate dons the role of an enabler, seamlessly accommodating the densely packed interconnections beneath the chip. This intricate choreography contributes to a high-density arrangement, a key element in the graceful reduction of the semiconductor package’s overall size.
Guardian of Signal Fidelity: Meticulously engineered, the substrate assumes the role of a guardian, preserving the integrity of signals. With a keen focus on minimizing distortions and interference in electrical signals exchanged between the chip and external components, it ensures the harmonious and accurate functioning of electronic devices, particularly in applications demanding high-speed and high-frequency performance.
Custodian of Reliability Elegance: The substrate, through its choice of materials and intricate design, assumes the role of a custodian, enhancing the overall reliability of the semiconductor package. By addressing crucial aspects such as electrical performance, thermal equilibrium, and mechanical stability, it contributes to the enduring strength and resilience of the device.
In essence, the substrate within the Flip Chip CSP package emerges as a versatile performer, seamlessly juggling electrical connectivity, thermal finesse, structural support, and playing a crucial part in the graceful dance of miniaturization and reliability that defines the semiconductor device.
What Are the Different Types of Flip Chip CSP Package Substrate?
In the expansive domain of Flip Chip CSP (Chip Scale Package) substrates, a myriad of types caters to specific demands, weaving together aspects like performance, cost dynamics, and application intricacies. Let’s navigate through the diverse tapestry of these substrates:
Inventive Organic Variants:
Build-Up Substrates: Embracing the intricacies of build-up layer technology, these substrates artfully stack multiple insulating layers, showcasing prowess in miniaturization and accommodating high-density interconnects.
Coreless Innovations: Shedding the conventional core materials, coreless substrates emerge as nimble and cost-effective solutions, particularly resonant in weight-sensitive applications such as mobile devices.
Adaptable Ceramic Selections:
Alumina (Al2O3) Choices: Revered for exceptional thermal conductivity, alumina substrates excel in applications where efficient heat dissipation takes center stage.
Aluminum Nitride (AlN) Alternatives: Elevating thermal conductivity even further, AlN substrates become stalwarts in scenarios demanding top-notch thermal management.
Dynamic Composite Approaches:
Metal Core Varieties (MCPCB): Featuring a metal core, often aluminum, MCPCBs add a layer of sophistication by enhancing thermal conductivity, making them ideal for applications with heightened power demands.
Ceramic Polymer Blends: Merging the strengths of ceramics and polymers, these substrates strike a delicate balance between thermal efficiency and cost-effectiveness.
Flexible Substrate Explorations:
Polyimide-based Solutions: Tailored for flexibility, these substrates gracefully bend to the needs of applications requiring supple and lightweight designs, such as wearable electronics.
Cutting-Edge Low-Temperature Cofired Ceramic (LTCC) Varieties:
Suited for applications demanding a blend of high-frequency performance and miniaturization, LTCC substrates seamlessly integrate passive components into the substrate.
Advanced Glass Configurations:
Glass substrates, with their unwavering thermal stability, find their place in applications where precision and unwavering reliability are the hallmarks.
The selection of substrate type pivots on the specific intricacies of each application, encompassing thermal management, electrical finesse, miniaturization, and nuanced cost considerations. Each substrate type, akin to an artist’s brushstroke, contributes a unique blend of features, enriching the palette to meet the diverse needs of electronic devices adopting Flip Chip CSP packaging.
How is Flip Chip CSP Package Substrate Connected to IC Packaging?
In the intricate symphony of semiconductor assembly, the fusion between the Flip Chip CSP (Chip Scale Package) substrate and the Integrated Circuit (IC) packaging takes center stage. Here’s an exploration of how the substrate intricately weaves its connection with IC packaging:
Theatrical Flip Dynamics:
The Flip Chip process introduces a captivating twist as the IC elegantly flips, revealing its active side adorned with the microchip and solder bumps, all poised to engage with the substrate.
Solder bumps on the chip perform a graceful alignment, finding their match on corresponding bonding pads on the substrate, setting the stage for a seamless electrical connection.
Solder Ballet Extravaganza:
Prior to the bonding spectacle, the IC undergoes a solder bumping extravaganza. Solder bumps, akin to skilled dancers, adorn the bonding pads of the IC, ready to execute their role in the forthcoming connection masterpiece.
These solder bumps transform into conduits, orchestrating a pathway for electrical connections and playing a pivotal role in the direct bonding of the chip to the substrate.
Precision Choreography:
Precision assumes the lead role as solder bumps on the IC harmonize with bonding pads on the substrate. This delicate dance is meticulously choreographed by advanced manufacturing equipment, ensuring a flawless alignment worthy of the semiconductor stage.
Reflow Soldering Symphony:
With alignment achieved, the assembly takes part in a reflow soldering symphony. The solder bumps, like virtuoso performers, elegantly melt at an elevated temperature, forming a secure bond between the chip and the substrate.
The molten solder conducts a symphony of robust electrical and mechanical connections, seamlessly uniting the IC with the substrate in a crescendo of technological harmony.
Underfill Artistry:
To enhance structural stability and reliability, an underfill material steps into the limelight. This material gracefully fills the spaces beneath the chip, adding an artistic layer of protection between the chip and the substrate.
The underfill material, akin to an artist’s brushstroke, contributes to the resilience of the assembly, fortifying it against mechanical stresses, temperature fluctuations, and the whims of external environmental factors.
Subsequent Packaging Epilogue:
Following the Flip Chip bonding spectacle, additional acts unfold, culminating in an epilogue that may include the application of a protective mold compound and the seamless integration of the substrate with the broader package or printed circuit board (PCB).
The direct connection achieved through Flip Chip CSP packaging not only amplifies electrical performance but also conducts a symphony of efficiency, reducing signal delays and enhancing thermal management. This makes it a coveted choice for applications where compact size and heightened performance take center stage, such as in mobile devices and the forefront of electronic innovation.
What Sets Flip Chip CSP Package Substrate Apart from Traditional PCBs?
The evolution from traditional Printed Circuit Boards (PCBs) to the avant-garde Flip Chip CSP (Chip Scale Package) substrates signifies a transformative leap in electronic packaging. Here’s an exploration of the facets that distinguish Flip Chip CSP, painting a vivid contrast against the canvas of conventional PCBs:
Embrace of Direct Fusion:
Flip Chip CSP: Introduces a bold departure by directly bonding the integrated circuit (IC) to the substrate, presenting the chip’s active side in a downward orientation.
Traditional PCBs: Adheres to the conventional approach of mounting components on the top side, with connections relying on vias or through-hole techniques.
Harmony in Miniaturization and Density:
Flip Chip CSP: Showcases an artistry of compactness, achieved through the intimate attachment of the chip to the substrate, fostering a ballet of high-density interconnects.
Traditional PCBs: Reside in a larger expanse, with components dispersed across the surface, limiting the potential for achieving heightened density.
Thermal Brilliance Unveiled:
Flip Chip CSP: Unfurls a narrative of superior thermal performance, as the direct attachment paves the way for efficient dissipation of heat.
Traditional PCBs: May necessitate supplementary thermal management solutions, particularly in applications demanding robust heat handling.
Trimming Parasitic Elements:
Flip Chip CSP: Takes center stage in the meticulous choreography of minimizing inductance and capacitance, thanks to the concise distances between chip and substrate.
Traditional PCBs: Grapple with longer traces and interconnects, potentially introducing higher levels of parasitic elements.
High-Frequency Virtuosity:
Flip Chip CSP: Emerges as a virtuoso in high-frequency applications, leveraging minimized parasitic elements to ensure a symphony of improved signal integrity.
Traditional PCBs: May encounter challenges in maintaining signal fidelity, particularly when navigating the frequencies of a more demanding composition.
Mechanical Fortitude and Reliability:
Flip Chip CSP: Casts a spotlight on enhanced mechanical stability, with the option to incorporate underfill materials for an extra layer of reliability.
Traditional PCBs: Subject to the whims of mechanical stresses, with reliability influenced by the intricacies of interconnection methodologies.
Gateway to Advanced Realms:
Flip Chip CSP: Often graces the realms of advanced technologies, finding resonance in microelectronics and microprocessors craving a synthesis of high performance and compact elegance.
Traditional PCBs: Pervasive in diverse applications but may find themselves trailing in the wake of advanced technologies demanding a fusion of superior performance and miniaturization.
Underfill Symphony:
Flip Chip CSP: Crafts a symphony with the use of underfill materials, encapsulating the space between chip and substrate and adding an artistic layer of protection.
Traditional PCBs: Tend not to incorporate underfill materials in the same harmonious fashion.
In essence, Flip Chip CSP substrates redefine the narrative with their direct chip fusion, compact elegance, thermal brilliance, streamlined electrical pathways, high-frequency virtuosity, mechanical resilience, applicability in advanced technologies, and the artistry of underfill encapsulation. These elements collectively position Flip Chip CSP as the virtuoso’s choice for applications demanding advanced performance, miniaturization, and unwavering reliability.
What is the Main Structure and Production Technology of Flip Chip CSP Package Substrate?
The Flip Chip CSP (Chip Scale Package) package substrate unfolds its intricate narrative through a carefully choreographed structure and a production journey that resembles an artful performance. Let’s embark on a journey through the layers and processes that define this technology:
Structural Symphony:
Foundation Canvas:
The substrate commences with a solid foundation, a canvas woven from materials like laminate, ceramics, or metals. This foundation sets the stage for the entire package.
Layered Narratives:
Multiple dielectric layers join the storytelling, providing insulation and preventing electrical tales from intertwining. Each layer contributes to the substrate’s narrative.
Conductive Harmony:
Thin, conductive traces and pads enter the scene, delicately etched on dielectric layers. These traces compose a harmonious melody of interconnects, linking the chip to the wider electronic ensemble.
Solder Mask Elegance:
A solder mask is applied with grace, akin to a protective veil. This layer ensures that solder adorns only the designated areas during the enchanting dance of chip attachment.
Architectural Vias:
Vias emerge as architectural structures, facilitating vertical connections between layers. These conduits orchestrate the communication between the diverse layers of the substrate.
Bump Pad Landing:
Bump pads take center stage as landing sites, strategically positioned to welcome the solder bumps from the chip. These pads become the canvas where connections are painted with soldered artistry.
Underfill Ballet:
After the chip takes its place, an underfill material pirouettes in, filling the gaps between the chip and the substrate. This underfill contributes to the mechanical stability, thermal resilience, and protective ambiance of the performance.
Production Ballet:
Substrate Crafting Prelude:
The production ballet commences with crafting the substrate base, an art form often utilizing materials like FR-4, ceramics, or other carefully chosen mediums.
Layered Pas de Deux:
Dielectric layers elegantly build up, and conductive traces emerge through the dance of photolithography and etching, forming a layered pas de deux on the substrate canvas.
Vias Choreography:
Vias perform a choreography of vertical connection, involving drilling and filling with conductive material to establish a harmonious connection between layers.
Conductive Pad Waltz:
Bump pads and conductive traces take the spotlight, their formation involving the deposition of metal layers through techniques like sputtering or plating, creating a waltz of connectivity.
Solder Mask Flourish:
A solder mask is applied with a flourish, covering areas not meant for soldering. This protective layer is cured, adding a touch of resilience to the substrate.
Surface Finish Sonata:
Exposed metal surfaces are adorned with a suitable surface finish—perhaps gold or tin—a sonata of surface refinement to ensure a graceful soldering performance during chip attachment.
Testing and Inspection Drama:
The substrate undergoes a drama of testing and inspection, a theatrical act to guarantee the quality of each layer and connection in this production spectacle.
Underfill Applause:
The grand applause arrives as the chip is attached using flip chip bonding, and underfill material is dispensed and cured, creating a protective and resilient encapsulation worthy of a standing ovation.
The Flip Chip CSP package substrate is not just a technological feat but a masterpiece of manufacturing art, where each layer and step contributes to a symphony of performance, miniaturization, and reliability on the electronic stage.
Frequently Asked Questions (FAQs):
What is the primary role of a Flip Chip CSP Package Substrate Manufacturer?
A Flip Chip CSP package substrate manufacturer specializes in producing the substrates used in flip chip packaging. This involves intricate processes such as substrate fabrication, conductive trace application, interconnect creation, and ensuring the substrate meets high-quality standards.
What quality control measures do manufacturers implement?
Manufacturers of Flip Chip CSP package substrates implement rigorous quality control measures, including tests for electrical continuity, thermal performance, and overall reliability. Continuous inspections throughout the production process ensure each substrate meets defined standards.
In what applications are Flip Chip CSP Package Substrates commonly used?
Flip Chip CSP substrates find applications in diverse industries, including microelectronics, microprocessors, high-frequency devices, and advanced technologies where the combination of miniaturization and high performance is crucial.
Can Flip Chip CSP Substrates be customized for specific applications?
Yes, manufacturers often provide customization options for Flip Chip CSP substrates, allowing adaptation to the specific requirements of different applications. This may involve adjustments in size, material composition, and electrical characteristics.
How do manufacturers ensure the long-term reliability of Flip Chip CSP Substrates?
Ensuring long-term reliability involves the use of robust materials, comprehensive testing procedures, and sometimes incorporating underfill materials during manufacturing. Underfill materials enhance mechanical stability and protect against external stresses.
Conclusion
To encapsulate the essence of Flip Chip CSP (Chip Scale Package) substrates, it’s akin to a symphony in semiconductor packaging, orchestrating a departure from conventional norms. This avant-garde technology features the direct attachment of the integrated circuit (IC) to the substrate, heralding a new era focused on efficiency and a sleek form factor.
The artisans behind this transformation are the manufacturers, weaving a tapestry of intricacy in the production of Flip Chip CSP substrates. Their craftsmanship involves meticulous processes, layering dielectrics, conductive traces, bump pads, and vias to create a canvas for the unique downward-facing embrace of the IC. The use of diverse materials—laminate, ceramics, metals—coupled with advanced fabrication techniques, bestows upon the substrate commendable thermal performance, high-density interconnects, and an aura of reliability.
The advantages bestowed by Flip Chip CSP substrates—compact dimensions, superior thermal dissipation, and elevated signal integrity—propel them to the forefront of choice for applications spanning microelectronics, high-frequency devices, and the frontiers of advanced technologies.
Manufacturers, attuned to the diverse needs of applications, offer bespoke solutions through customization options. Their commitment is evident in rigorous quality control measures encompassing electrical tests, thermal scrutiny, and meticulous inspections, ensuring each substrate is a paragon of excellence.
In essence, Flip Chip CSP package substrates emerge as the trailblazers of electronic packaging, seamlessly marrying performance, streamlined design, and unswerving reliability. As technological landscapes unfold, these substrates continue to be the vanguards shaping the trajectory of semiconductor applications across multifaceted industries.