Flip Chip Package Substrate Manufacturing .High speed and high frequency material packaging substrate manufacturing. Advanced packaging substrate production process and technology
A flip chip packaging substrate is a crucial component in the assembly of semiconductor devices using flip chip technology. Flip chip packaging is a method where the active side of the semiconductor die (the chip) is attached face-down to a substrate or a carrier. This is in contrast to traditional packaging methods where the chip is mounted upright and connected using wire bonding.
The substrate in flip chip packaging serves several important functions:
Electrical Interconnection: The substrate provides a platform for creating electrical connections between the flip chip and the rest of the electronic system. These connections are typically achieved through metal traces, vias, and bumps on the substrate.
Heat Dissipation: As semiconductor devices generate heat during operation, efficient heat dissipation is crucial for maintaining optimal performance and reliability. The substrate may incorporate materials with good thermal conductivity or features to aid in heat dissipation.
Mechanical Support: The substrate offers mechanical support to the flip chip, securing it in place and protecting it from external stresses, such as temperature variations and mechanical vibrations.
Signal Routing: The substrate facilitates the routing of signals between the flip chip and other components in the electronic system. This includes providing pathways for power supply, data signals, and other communication lines.
Alignment and Packaging Structure: The substrate is designed to ensure accurate alignment of the flip chip during the assembly process.Additionally, it plays a role in shaping the overall packaging structure, taking into account factors such as size, form factor, and seamless integration into the final electronic product.
Flip chip packaging substrates are crafted from diverse materials, encompassing organic options like FR-4 and BT, ceramic selections such as alumina and aluminum nitride, copper substrates, laminates like liquid crystal polymer and polyimide, among others. The selection of substrate material hinges on factors like application specifications, thermal needs, and cost limitations.
In summary, a flip chip packaging substrate plays a critical role in providing electrical connectivity, heat management, and structural support for semiconductor devices using flip chip technology.
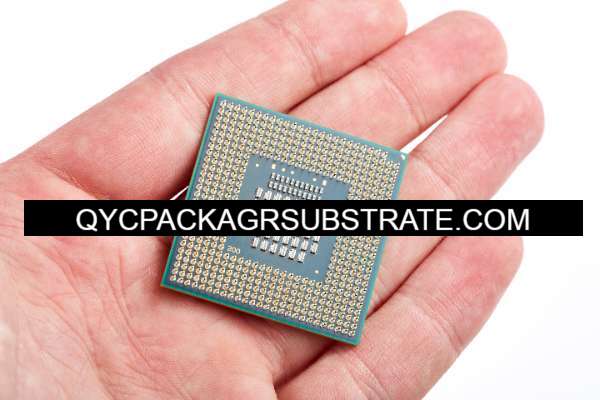
What are the Materials Used in a Flip Chip Packaging Substrate?
Flip chip packaging is a prevalent semiconductor technology employed for affixing integrated circuits (ICs) onto substrates. The substrate plays a pivotal role in flip chip packaging by facilitating essential electrical and mechanical connections between the IC and the broader electronic system.Several materials are commonly used in flip chip packaging substrates. Some of these materials include:
- Organic Substrates:
-
- FR-4 (Flame Retardant 4): FR-4 is a common epoxy-based substrate material. It is cost-effective and widely used in various electronic applications.
- BT (Bismaleimide Triazine): BT is another organic substrate material known for its high-temperature stability and low dielectric constant. It is suitable for high-performance applications.
- Ceramic Substrates:
-
- Alumina (Al2O3): Alumina, a ceramic material renowned for its combination of high thermal conductivity and excellent electrical insulation properties, proves advantageous in applications where effective heat dissipation is crucial.
- Aluminum Nitride (AlN): Alumina, a ceramic material renowned for its combination of high thermal conductivity and excellent electrical insulation properties, proves advantageous in applications where effective heat dissipation is crucial.
- Copper Substrates:
-
- Copper (Cu): Copper substrates are used in advanced flip chip packaging for their high thermal conductivity. Multilayer structures incorporating copper substrates are utilized to enhance heat dissipation efficiency in flip chip packaging.
- Laminates:
-
- Liquid Crystal Polymer (LCP):LCP, a thermoplastic with favorable attributes such as a low dielectric constant and excellent electrical properties, serves as a substrate material in electronic applications.
- Polyimide: Polyimide serves as a flexible substrate material ideal for applications demanding flexibility.
- Leadframe Substrates:
-
- Copper or Alloy Leadframes: In some flip chip packages, a leadframe made of copper or a copper alloy may be used as a substrate. The leadframe provides structural support and electrical connections.
- High-Density Interconnect (HDI) Substrates:
- Build-up Layers: HDI substrates often involve build-up layers of materials such as polyimide or other dielectric materials to enable high-density interconnections.
The choice of substrate material depends on various factors, including the specific application requirements, thermal management needs, cost considerations, and performance specifications. Different industries and applications may prioritize different substrate materials based on their unique characteristics and performance demands.
What are the types of Flip Chip Packaging Substrate?
There are several types of flip chip packaging substrates, each with its own characteristics and applications. Here are some common types:
- Organic Substrates:
-
- FR-4 (Flame Retardant 4): A widely used epoxy-based substrate known for its cost-effectiveness.
- BT (Bismaleimide Triazine): Offers high-temperature stability and a low dielectric constant, suitable for high-performance applications.
- Ceramic Substrates:
-
- Alumina (Al2O3): Ceramic material with good thermal conductivity and electrical insulation properties, suitable for applications requiring heat dissipation.
- Aluminum Nitride (AlN): Known for excellent thermal conductivity, used in applications requiring efficient heat dissipation.
- Copper Substrates:
-
- Copper (Cu): Utilized in advanced flip chip packaging for its high thermal conductivity; often part of a multilayer structure for heat dissipation.
- Laminates:
-
- Liquid Crystal Polymer (LCP): Thermoplastic material with low dielectric constant and excellent electrical properties.
- Polyimide: A flexible substrate material suitable for applications where flexibility is a requirement.
- Leadframe Substrates:
-
- Copper or Alloy Leadframes: Copper or copper alloy-based structures providing structural support and electrical connections.
- High-Density Interconnect (HDI) Substrates:
- Build-up Layers: Involves the use of build-up layers, often utilizing materials like polyimide or other dielectrics, to enable high-density interconnections.
The selection of a specific flip chip packaging substrate depends on factors such as the application’s requirements, thermal considerations, cost constraints, and desired performance specifications. Different industries and applications may opt for different substrate types based on their specific needs and priorities.
When is It Ideal to Use Flip Chip Packaging Substrate?
Flip chip packaging is ideal in various scenarios, and its adoption is driven by certain advantages it offers over traditional packaging methods. Here are situations where flip chip packaging substrates are particularly beneficial:
- Miniaturization and High-Density Applications:
-
- Flip chip technology allows for a compact and high-density arrangement of semiconductor devices. It is well-suited for applications where space is at a premium, and a higher number of connections in a smaller area is essential.
- High-Frequency Applications:
-
- The short interconnection lengths in flip chip packaging reduce parasitic capacitance and inductance, making it suitable for high-frequency applications such as RF (radio frequency) and microwave devices.
- Improved Electrical Performance:
-
- Flip chip connections offer shorter signal paths, leading to lower resistance and inductance, resulting in improved electrical performance compared to traditional wire bonding methods.
- Enhanced Thermal Performance:
-
- The direct attachment of the chip to the substrate or heat sink facilitates efficient heat dissipation, making flip chip packaging suitable for applications where thermal management is crucial.
- Advanced Semiconductor Technologies:
-
- With the continuous advancement of semiconductor technologies, where smaller feature sizes and increased functionality are achieved, flip chip packaging provides a means to take full advantage of these developments.
- High-Performance Computing and Graphics:
-
- Flip chip technology is frequently employed in high-performance computing, graphics processing units (GPUs), and various applications where there is a substantial need for both processing power and interconnectivity.
- Automotive Electronics:
-
- The automotive industry often employs flip chip packaging for its reliability, compact design, and ability to withstand harsh operating conditions, including temperature variations and mechanical stress.
- Multi-Chip Modules (MCMs):
-
- Flip chip packaging is particularly suitable for Multi-Chip Modules (MCMs), where several chips are integrated into a unified package. This enables enhanced functionality and performance within a more compact form factor.
- Consumer Electronics:
-
- Portable devices and consumer electronics benefit from the space-saving advantages of flip chip packaging, contributing to the development of smaller and lighter products.
- Wafer-Level Packaging:
- Flip chip technology is often used in wafer-level packaging, where the entire wafer is processed to create individual packaged chips, leading to improved cost efficiency.
Although flip chip packaging provides various benefits, it may not be the optimal solution for all applications. Considerations such as cost, development complexity, and the specific needs of a particular application should be taken into account when selecting the most appropriate packaging method.
How is a Flip Chip Packaging Substrate?
The construction of a flip chip packaging substrate involves several key steps and components. Here is a general overview of the process:
- Substrate Material Selection:
-
- The first step is selecting the appropriate substrate material based on the application’s requirements. Common materials include organic substrates like FR-4 or BT, ceramic substrates like alumina or aluminum nitride, copper substrates, laminates such as liquid crystal polymer (LCP) or polyimide, and others.
- Substrate Fabrication:
-
- The chosen substrate material is then processed to create the substrate. This may involve techniques such as etching, layer deposition, and drilling to achieve the desired substrate structure.
- Surface Preparation:
-
- The substrate surface that will come into contact with the flip chip is carefully prepared. This may include cleaning, planarization, and applying adhesion-promoting layers to ensure a strong bond between the chip and the substrate.
- Metallization:
-
- The substrate is metallized to create the interconnects that will facilitate electrical connections between the flip chip and the rest of the electronic system. This may involve depositing metal layers using techniques like sputtering or electroplating.
- Bump Formation:
-
- Bumps or solder balls are formed on the active side of the flip chip. These bumps serve as the electrical connections between the chip and the substrate. Bump formation can be done through processes like solder ball attachment or copper pillar bumping.
- Flip Chip Attachment:
-
- The flip chip is precisely aligned and attached to the substrate with the bumps facing down. This can be achieved using various techniques, such as solder reflow or thermo-compression bonding. The alignment is crucial for accurate electrical connections.
- Underfill Encapsulation:
-
- An underfill material is often applied between the flip chip and the substrate to provide mechanical support and improve reliability. This material is cured after application to secure the flip chip in place.
- Encapsulation (Optional):
-
- In some cases, the entire assembly may be encapsulated for protection against environmental factors such as moisture, contaminants, and mechanical stress.
- Final Testing and Packaging:
- The completed flip chip package undergoes final testing to validate its functionality, and it is then prepared for shipping or integration into electronic systems.
The specific details of the flip chip packaging process may vary based on the chosen substrate material, application requirements, and manufacturing technologies employed by the semiconductor industry.
Where to Find Flip Chip Packaging Substrate?
You can find flip chip packaging substrates from various suppliers, and one such company that offers these products is SHENZHEN QYC CO.,LTD. They specialize in providing a range of substrates suitable for flip chip packaging applications. You may visit their official website or contact them directly to inquire about specific substrate materials, capabilities, and customization options. Additionally, other semiconductor packaging material suppliers and distributors may also offer flip chip packaging substrates, and you can explore industry-specific platforms or trade shows to discover more options.