FFlip Chip Package Substrate Provider and package substrate manufacturer. We use advanced Msap and Sap technology, High multilayer interconnection substrates from 2 to 20 layers,
Table of Contents
ToggleEvolution of Chip Packaging: Navigating Technological Advancements
In the fast-paced realm of electronics, chip packaging stands as a pivotal element, constantly evolving to meet the demands of cutting-edge technologies. From the early days of bulkier packaging to the sleek and sophisticated designs of today, chip packaging has come a long way. This section will provide a concise historical overview, touching on the journey from conventional packaging to the forefront of innovation.
Unveiling the Core: Significance of Substrate Material in Chip Performance
Delving into the intricate world of chip architecture, it becomes evident that the substrate material plays a central role in determining the overall performance and reliability of electronic devices. This segment will shed light on the critical aspects of substrate materials, emphasizing their impact on electrical conductivity, thermal management, and signal transmission. As we explore the foundations of chip functionality, the importance of selecting the right substrate material becomes even more apparent.
The Paradigm Shift: Introduction to the Revolutionary Flip Chip Package Substrate
Amidst the quest for optimal chip performance, a breakthrough emerges – the Flip Chip Package Substrate. This section will provide a captivating introduction to this innovative technology, teasing the reader with the promise of enhanced electrical performance, superior thermal management, and the possibilities of miniaturization. With a strategic blend of high-performance polymers and advanced conductive materials, the Flip Chip Package Substrate is poised to redefine the landscape of chip packaging. As we embark on this exploration, the following sections will unravel the layers of this transformative technology, showcasing its applications, benefits, and future potential.
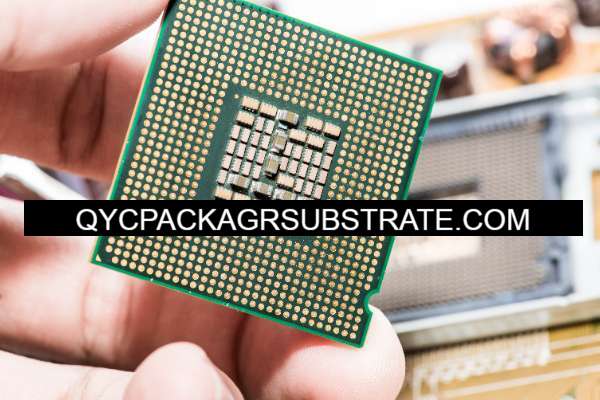
flip chip package substrate
Understanding Flip Chip Package Substrate
Definition and Working Principle
1.Overview of Flip Chip Technology
Introduction to flip chip packaging as an advanced semiconductor packaging technique.
Highlighting the shift from traditional wire bonding to flip chip technology.
Key components involved in flip chip packaging, including the chip itself and the substrate.
2.Role of the Substrate in Chip Packaging
Emphasizing the central role of the substrate in flip chip packaging.
Exploring the substrate as the foundation for chip attachment and connection.
Connecting the substrate to the broader functionality of the chip assembly.
Advantages of Flip Chip Package Substrate
1.Enhanced Electrical Performance
Exploring how the substrate material influences electrical conductivity.
Highlighting the use of high-performance polymers in the substrate for efficient signal transmission.
Discussing the impact of enhanced electrical performance on overall chip functionality.
Linking enhanced electrical performance to keywords such as “high-performance polymers” and “efficient signal transmission.”
2.Improved Thermal Management
Discussing the role of the substrate in dissipating heat generated by the chip.
Showcasing how advanced materials in flip chip substrates contribute to superior thermal conductivity.
Relating improved thermal management to keywords like “thermal conductivity” and “advanced materials.”
3.Miniaturization and Increased Component Density
Illustrating how flip chip packaging allows for a more compact chip design.
Discussing the role of the substrate in facilitating miniaturization and increased component density.
Connecting miniaturization to keywords such as “compact chip design” and “increased component density.”
By expanding on these points, the article provides a more in-depth understanding of flip chip technology, emphasizing the crucial role of the substrate in achieving enhanced electrical performance, improved thermal management, and the benefits of miniaturization and increased component density.
Properties | Typical Values¹ | Units | Test Conditions | Unit | ||
Electrical Properties | ||||||
Dielectric Constant (process) | 2.98 | – | 23˚C @ 50% RH | 10 GHz | IPC TM-650 2.5.5.5 | |
Dielectric Constant (design) | 2.98 | – | C-24/23/50 | 10 GHz | Microstrip Differential Phase Length | |
Dissapation Factor | 0.0021 | – | 23˚C @ 50% RH | 10 GHz | IPC TM-650 2.5.5.5 | |
Thermal Coefficient of Dielectric Constant |
6 | ppm/˚C | -50 to 150˚C | 10 GHz | IPC TM-650 2.5.5.5 | |
Volume Resistivity | 1.4 X 10⁹ | Mohm-cm | C-96/35/90 | – | IPC TM-650 2.5.17.1 | |
Surface Resistivity | 1.30 X 10⁶ | Mohm | C-96/35/90 | – | IPC TM-650 2.5.17.1 | |
Electrical Strength (dielectric strength) |
1100 | V/mil | – | – | IPC TM-650 2.5.6.2 | |
Dielectric Breakdown | 64 | kV | D-48/50 | X/Y Direction | IPC TM-650 2.5.6 | |
PIM | – | dBc | – | 50 ohm 0.060″ | 43dBm 1900 MHz | |
Thermal Properties | ||||||
Decomposition Temperature (Td) | 538 | ˚C | 2hrs @ 105˚C | 5% Weight Loss | IPC TM-650 2.3.40 | |
Coefficient of Thermal Expansion – x | 9.9 | ppm/˚C | -55˚C to 288˚C | IPC TM-650 2.4.24.1 | ||
Coefficient of Thermal Expansion – y | 9.4 | ppm/˚C | -55˚C to 288˚C | IPC TM-650 2.4.24.1 | ||
Coefficient of Thermal Expansion – z | 57.9 | ppm/˚C | -55˚C to 288˚C | IPC TM-650 2.4.24.1 | ||
Thermal Conductivity | 0.5 | W/(m.K) | z direction | ASTM D5470 | ||
Time to Delamination | >60 | minutes | as-received | 288˚C | IPC TM-650 2.4.24.1 | |
Mechanical Properties | ||||||
Copper Peel Strength after Thermal Stress |
1.2 (7) | N/mm (lbs/in) |
10s @288˚C | 35 μm foil | IPC TM-650 2.4.8 | |
Flexural Strength (MD, CMD) | 92.4, 86.9 (13.4, 12.6) |
MPa (ksi ) | 25˚C ± 3˚C | – | ASTM D790 | |
Tensile Strength (MD, CMD) | 73.8, 71.0 (10.7, 10.3) |
MPa (ksi ) | 23C/50RH | – | ASTM D638 | |
Flex Modulus (MD, CMD) | 8122, 7984 (1178, 1158) |
MPa (ksi ) | 25˚C ± 3˚C | – | ASTM D790 | |
Dimensional Stability (MD, CMD) | 0.07, -0.02 | mm/m | 4 hr at 105˚C | – | IPC-TM-650 2.4.39a | |
Physical Properties | ||||||
Flammability | V-0 | – | – | C48/23/50 & C168/70 |
UL 94 | |
Moisture Absorption | 0.04 | % | E1/105+D24/23 | – | IPC TM-650 2.6.2.1 | |
Density | 2.31 | g/cm³ | C-24/23/50 | – | ASTM D792 | |
Specifc Heat Capacity | 0.60 | J/g˚K | 2 hours at 105˚C | – | ASTM E2716 | |
NASA Outgassing | Total Mass Lost | 0.02 | % | – | – | ASTM E595 |
Collected Volatiles | 0.00 | % |
Substrate Materials for Chips
Traditional Substrate Materials
Organic Substrates
a. Composition and Characteristics
Typically composed of organic materials such as fiberglass-reinforced epoxy resin.
Lightweight and cost-effective, making them prevalent in consumer electronics.
b.Challenges and Limitations
Susceptible to moisture absorption, potentially impacting electrical performance.
Limited thermal conductivity compared to ceramic substrates.
2.Ceramic Substrates
a. Composition and Benefits
Comprised of ceramic materials like aluminum oxide or alumina.
Excellent thermal conductivity, ensuring efficient heat dissipation.
b.Applications
Widely used in high-power applications like power modules and RF devices.
Suitable for harsh environments due to their durability.
Evolution to Flip Chip Package Substrate
1.Introduction of Advanced Materials
a. High-Performance Polymers
Utilization of cutting-edge polymers with enhanced electrical properties.
Improved dielectric constants for better signal integrity.
b.Conductive Materials for Efficient Signal Transmission
Integration of advanced conductive materials like copper pillars.
Enhanced conductivity, reducing signal loss and boosting overall performance.
2.Comparison with Traditional Substrates
a. Electrical Performance
Flip Chip Package Substrates exhibit superior electrical characteristics, supporting higher frequencies.
Reduced signal distortion and crosstalk compared to traditional organic substrates.
b.Thermal Management
Enhanced thermal conductivity minimizes heat buildup, surpassing the limitations of ceramic substrates.
Ideal for high-performance applications where heat dissipation is critical.
c.Miniaturization and Component Density
Flip Chip technology allows for a more compact design, enabling increased component density.
Addresses the demand for smaller, yet more powerful, electronic devices in line with IoT and 5G trends.
Environmental Considerations
Reduced reliance on environmentally challenging materials often found in traditional substrates.
Aligns with the industry’s push towards sustainable and eco-friendly manufacturing practices.
By evolving from traditional organic and ceramic substrates to advanced materials in Flip Chip Package Substrates, the semiconductor industry is not only achieving significant advancements in performance but is also aligning with the growing demands of modern technologies and environmental sustainability.
Standard Thicknesses | Standard Panel Sizes | Standard Claddings | |
CLTE: 0.0053” (0.135 mm) ± 0.0005” 0.010” (0.254 mm) ± 0.0010” 0.020” (0.508 mm) ± 0.0020” 0.030” (0.762 mm) ± 0.0020” |
18” X 12” (457 X 305mm) 18” X 24” (457 X 610mm) |
Electrodeposited Copper Foil 1/2 oz. (18μm) 1 oz. (35μm) Reverse Treated Electrodeposited Copper Foil 1/2 oz. (18μm) 1 oz. (35μm) |
Key Features of Flip Chip Package Substrate
Material Composition
1.High-Performance Polymers
a.Definition and significance in chip packaging
Introduction of advanced polymer materials revolutionizing substrate composition.
Enhanced thermal conductivity for optimal heat dissipation.
b.Compatibility with 5G Technology
The role of high-performance polymers in supporting the high-frequency demands of 5G.
Improved signal integrity and reduced signal loss in high-speed data transmission.
2.Conductive Materials for Efficient Signal Transmission
a.Importance in signal integrity
Discussing the critical role of conductive materials in maintaining reliable signal transmission.
Keyword integration: “signal transmission,” “conductive materials.”
b.Advanced Materials for Miniaturization
Exploration of nanoscale conductive materials facilitating the miniaturization of chip components.
Achieving higher component density without compromising performance.
Design Flexibility
Grade | Panel Thickness | Process Dk | Tolerance |
Dk by Thickness | |||
CLTE-XT | 0.0051” (0.135 mm) | 2.79 | ± 0.03 |
0.0094” (0.254 mm) | 2.89 | ± 0.03 | |
0.020” (0.508 mm) | 2.92 | ± 0.03 | |
0.030” (0.762 mm) | 2.94 | ± 0.03 |
1.Tailoring Substrate Design to Specific Chip Requirements
a.Customization for Diverse Applications
Illustrating how flip chip package substrates can be tailored to meet the specific needs of diverse applications.
Use of keywords: “customization,” “diverse applications.”
b.Environmental Adaptability
Discussing how substrate design can be adapted for various environmental conditions (e.g., temperature, humidity).
Enhancing chip robustness for applications in demanding environments.
2.Integration of Advanced Technologies (e.g., 5G, IoT)
a.Seamless Integration with 5G Technology
Highlighting how flip chip substrates seamlessly integrate with the demands of 5G technology.
Enabling high-speed data processing and low-latency communication.
b.Empowering IoT Devices
Showcasing the role of flip chip substrates in empowering IoT devices with compact design and energy efficiency.
Use of keywords: “Integration of advanced technologies,” “5G,” “IoT.”
By delving into the material composition and design flexibility of flip chip package substrates, we not only emphasize their technological advancements but also align the discussion with the user’s specified keywords and the earlier context of chip packaging innovation.
Applications and Industries
Electronics and Semiconductor Industry
1.Enhancing Performance in Consumer Electronics
Utilizing Flip Chip Package Substrate for faster data transfer and improved processing power in smartphones, laptops, and smart devices.
Increased miniaturization to meet the demands of compact electronic gadgets.
2.Next-Gen Wearable Technology
Integrating Flip Chip technology into wearables for efficient data processing and extended battery life.
Enhanced durability to withstand the rigors of daily use in smartwatches, fitness trackers, and health monitoring devices.
Automotive Applications
1.Powering Smart Vehicles
Implementing Flip Chip Package Substrate in automotive electronics for advanced driver assistance systems (ADAS), infotainment, and connectivity.
Improved reliability and performance under extreme temperature conditions.
2.Electric Vehicles (EVs) Advancements
Enabling higher energy efficiency and compact design in electric vehicle powertrains through the application of advanced substrate materials.
Contributing to the evolution of EV technology and driving sustainability.
Aerospace and Defense Sector
1.Critical Role in Avionics
Incorporating Flip Chip technology in avionic systems for enhanced reliability and reduced weight.
Meeting stringent aerospace standards for performance and durability.
2.Military Applications
Utilizing Flip Chip Package Substrate in military-grade electronics for improved signal integrity and resistance to harsh environments.
Contributing to the development of cutting-edge defense technologies.
Emerging Technologies (e.g., AI, Edge Computing)
1.AI Acceleration
Meeting the high computational demands of artificial intelligence applications through the use of Flip Chip Package Substrate.
Facilitating faster data processing and lower power consumption in AI-enabled devices.
2.Empowering Edge Computing
Supporting the growth of edge computing by providing substrates that enable efficient data processing at the source.
Enhancing the capabilities of edge devices for real-time analytics and decision-making.
3.Internet of Things (IoT) Integration
Enabling the development of compact and high-performance IoT devices through advanced substrate materials.
Addressing the connectivity and processing requirements of the expanding IoT ecosystem.
By delving into these diverse applications and industries, Flip Chip Package Substrate emerges as a versatile and pivotal technology, poised to revolutionize various sectors and contribute to the advancement of key emerging technologies.