Flip Chip PCBs Manufacturer
Flip Chip PCBs Manufacturer,Flip Chip PCBs are advanced printed circuit boards where integrated circuits (ICs) are mounted upside down directly onto the substrate using solder bumps. This configuration shortens electrical paths, improving signal integrity and enabling higher I/O density. It also enhances thermal management by efficiently dissipating heat through the substrate. Flip Chip PCBs are commonly used in high-performance applications such as smartphones, computers, and medical devices due to their superior electrical performance, reliability, and compact size. They are essential for modern electronics, offering benefits like reduced signal propagation delay and better overall system performance.
What is a Flip Chip PCB?
A Flip Chip PCB (Printed Circuit Board) is a specialized type of PCB assembly where the integrated circuit (IC) or chip is flipped upside down and directly mounted onto the substrate, typically using solder bumps or balls. This “flip chip” configuration offers several advantages over traditional mounting methods like wire bonding.
In a flip chip setup, the electrical connections between the chip and the PCB are made through tiny solder bumps or balls, known as Controlled Collapse Chip Connection (C4) or solder bump technology. These connections are typically more compact and offer shorter electrical paths compared to wire bonding, resulting in improved electrical performance, higher speed, and reduced signal propagation delays.
Flip chip technology also enhances thermal management because the heat generated by the chip can be dissipated more efficiently through the PCB substrate, leading to better overall reliability and performance. Additionally, flip chip packaging allows for higher I/O density, enabling more connections in a smaller area, which is advantageous for miniaturization and space-constrained applications.
Moreover, flip chip assemblies are often more resistant to mechanical stress and environmental factors like vibration and shock compared to wire bonding, making them suitable for harsh operating conditions.
Overall, the flip chip PCB configuration offers improved electrical performance, better thermal management, higher I/O density, and enhanced reliability, making it a preferred choice for many high-performance and miniaturized electronic devices, including smartphones, tablets, computers, and high-speed communication systems.
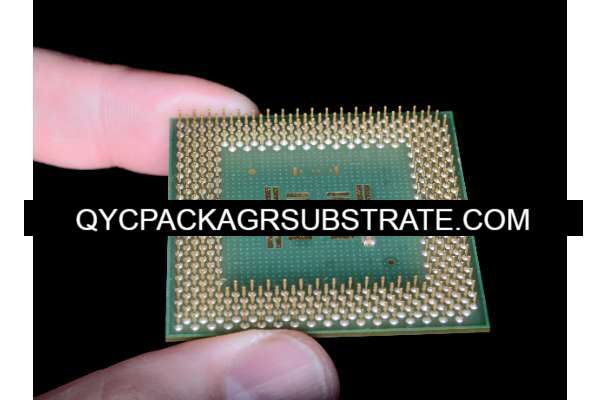
Flip Chip PCBs Manufacturer
What are the Flip Chip PCB Design Guidelines?
Designing a Flip Chip PCB requires careful consideration of various factors to ensure optimal performance, reliability, and manufacturability. Here are some key guidelines:
- Substrate Selection:Choose a substrate material with good thermal conductivity and mechanical strength to efficiently dissipate heat and withstand mechanical stresses. Common materials include FR-4, high-speed laminates like FR-4 with high-frequency (HF) cores, and ceramic substrates for high-frequency applications.
- Routing and Layout: Design the PCB layout to minimize signal path lengths and impedance mismatches. Use controlled impedance routing for high-speed signals to maintain signal integrity. Place power and ground planes strategically to minimize noise and provide stable power distribution.
- Pad Design: Design appropriate pad sizes and shapes for the flip chip solder bumps. Ensure sufficient spacing between pads to prevent short circuits during soldering. Use pad designs that provide good solder wetting and alignment with the chip’s bump layout.
- Via Design: Minimize the number of vias in high-speed signal paths to reduce signal reflections and impedance changes. Use blind or buried vias when necessary to access inner layers without affecting signal integrity.
- Thermal Management: Incorporate thermal vias and thermal pads to efficiently dissipate heat from the flip chip to the PCB substrate. Ensure adequate spacing between thermal vias to avoid electrical interference. Consider adding thermal relief structures to improve heat transfer.
- Assembly Considerations: Coordinate with the IC manufacturer to ensure compatibility between the flip chip design and the PCB assembly process. Follow recommended solder bump dimensions, pitch, and solder paste stencil design guidelines. Consider underfilling the flip chip after soldering to enhance mechanical reliability.
- Design for Testability (DFT): Include test points and access pads for testing and debugging the flip chip assembly during manufacturing and post-assembly. Design test patterns for continuity, shorts, and signal integrity testing.
- Reliability Considerations: Perform stress analysis to identify potential failure points due to thermal cycling, mechanical shock, and vibration. Design the PCB layout and substrate to minimize stress concentrations and ensure long-term reliability.
- Documentation and Communication: Document the flip chip design guidelines, specifications, and requirements clearly for communication with stakeholders, including PCB manufacturers, assembly houses, and IC suppliers.
By following these guidelines, designers can create flip chip PCB layouts that optimize performance, reliability, and manufacturability for a wide range of electronic applications.
What is the Flip Chip PCB Fabrication Process?
The fabrication process for a Flip Chip PCB involves several steps to create the substrate, prepare the flip chip, attach it to the substrate, and complete the assembly. Here’s an overview of the process:
- Substrate Fabrication: The process begins with the fabrication of the PCB substrate. This involves selecting the appropriate substrate material, typically a high-performance laminate such as FR-4 with high-frequency cores or ceramic substrates for specialized applications. The substrate is manufactured using standard PCB fabrication techniques, including layer stacking, drilling, and etching.
- Surface Preparation: Once the substrate is fabricated, the surface is prepared for flip chip attachment. This may involve cleaning the surface to remove contaminants and creating a planar surface for precise flip chip placement.
- Flip Chip Preparation: The flip chip itself undergoes preparation steps. This includes applying solder bumps or balls to the bonding pads on the chip using processes such as solder bumping or ball grid array (BGA) assembly. These solder bumps provide the electrical and mechanical connections between the chip and the substrate.
- Alignment and Placement:The flip chip is aligned and placed onto the prepared substrate. This is typically done using automated equipment that ensures precise alignment of the solder bumps with the corresponding pads on the substrate. The alignment process is critical to ensure proper electrical connections and avoid short circuits.
- Solder Reflow: Once the flip chip is aligned, the assembly undergoes solder reflow. During this process, the substrate and flip chip assembly are heated to a temperature that melts the solder bumps, forming strong metallurgical bonds between the chip and the substrate. This step requires careful control of temperature profiles to avoid damaging the components or substrate.
- Underfill (Optional): In some cases, an underfill material is applied after solder reflow to enhance the mechanical reliability of the flip chip assembly. The underfill material flows between the chip and substrate, providing additional support and stress relief to prevent solder joint failure during thermal cycling and mechanical stress.
- Testing and Inspection: After the flip chip assembly is completed, the PCB undergoes testing and inspection to ensure quality and reliability. This may include electrical testing to verify connectivity and functionality, as well as visual inspection to check for defects such as solder bridging or misalignment.
- Final Processing:Once testing and inspection are complete, the Flip Chip PCB may undergo additional processing steps, such as coating with protective materials for environmental protection or surface finishing for improved solderability.
- Packaging and Shipping: Finally, the completed Flip Chip PCBs are packaged according to customer requirements and shipped to end-users or assembly facilities for integration into electronic devices.
Overall, the fabrication process for Flip Chip PCBs requires precision, careful attention to detail, and adherence to strict quality standards to ensure reliable performance in a wide range of electronic applications.
How do you manufacture a Flip Chip PCB?
Manufacturing a Flip Chip PCB involves a series of intricate steps to create the substrate, prepare the flip chip, attach it to the substrate, and complete the assembly. Here’s a detailed overview of the manufacturing process:
- Design Preparation: The process starts with the design of the Flip Chip PCB layout. Designers use specialized software to plan the placement of components, routing of traces, and creation of solder pad patterns for the flip chip attachment.
- Substrate Fabrication: The first step in manufacturing is fabricating the PCB substrate. This involves selecting the appropriate substrate material, typically a high-performance laminate such as FR-4 with high-frequency cores or ceramic substrates for specialized applications. The substrate is manufactured using standard PCB fabrication techniques, including layer stacking, drilling, and etching.
- Surface Preparation:Once the substrate is fabricated, its surface is prepared for flip chip attachment. This may involve cleaning the surface to remove contaminants and creating a planar surface for precise flip chip placement. Surface preparation is crucial to ensure proper adhesion and electrical connectivity.
- Flip Chip Preparation: Meanwhile, the flip chip undergoes preparation steps. This includes applying solder bumps or balls to the bonding pads on the chip using processes such as solder bumping or ball grid array (BGA) assembly. These solder bumps provide the electrical and mechanical connections between the chip and the substrate.
- Alignment and Placement: With both the substrate and flip chip prepared, they are aligned and placed together. This is typically done using automated equipment that ensures precise alignment of the solder bumps with the corresponding pads on the substrate. Accurate alignment is critical to ensure proper electrical connections and avoid short circuits.
- Solder Reflow: Once the flip chip is aligned, the assembly undergoes solder reflow. During this process, the substrate and flip chip assembly are heated to a temperature that melts the solder bumps, forming strong metallurgical bonds between the chip and the substrate. This step requires careful control of temperature profiles to avoid damaging the components or substrate.
- Underfill (Optional): In some cases, an underfill material is applied after solder reflow to enhance the mechanical reliability of the flip chip assembly. The underfill material flows between the chip and substrate, providing additional support and stress relief to prevent solder joint failure during thermal cycling and mechanical stress.
- Testing and Inspection: After solder reflow (and optionally underfill), the PCB undergoes testing and inspection to ensure quality and reliability. This may include electrical testing to verify connectivity and functionality, as well as visual inspection to check for defects such as solder bridging or misalignment.
- Final Processing: Once testing and inspection are complete, the Flip Chip PCB may undergo additional processing steps, such as coating with protective materials for environmental protection or surface finishing for improved solderability.
- Packaging and Shipping: Finally, the completed Flip Chip PCBs are packaged according to customer requirements and shipped to end-users or assembly facilities for integration into electronic devices.
Manufacturing a Flip Chip PCB requires precision, careful attention to detail, and adherence to strict quality standards to ensure reliable performance in a wide range of electronic applications.
How much should a Flip Chip PCB cost?
The cost of a Flip Chip PCB can vary widely depending on several factors including complexity, size, substrate material, number of layers, quantity, and manufacturing technology used. However, generally speaking, Flip Chip PCBs tend to be more expensive than traditional PCBs due to their specialized design, fabrication, and assembly processes.
Here are some factors that can influence the cost of a Flip Chip PCB:
- Complexity: The complexity of the design, including the number of layers, fine pitch traces, and tight tolerances, can significantly impact the cost. More complex designs require advanced manufacturing processes and may involve higher material and labor costs.
- Size: Larger PCBs generally cost more than smaller ones due to the increased material and manufacturing expenses. However, extremely miniaturized Flip Chip PCBs may also incur higher costs due to the precision required in the assembly process.
- Substrate Material: The choice of substrate material can affect the cost. High-performance materials like specialized laminates or ceramic substrates may be more expensive than standard FR-4, but they offer enhanced electrical performance and reliability.
- Manufacturing Technology: Advanced manufacturing technologies such as laser drilling, sequential lamination, or embedded component technology may increase the cost of production but can offer benefits such as improved signal integrity or miniaturization.
- Quantity: Typically, the cost per unit decreases with higher order quantities due to economies of scale. Ordering larger volumes can help reduce the per-unit cost of Flip Chip PCBs.
- Assembly Process: The complexity of the flip chip assembly process, including the need for underfilling or specialized equipment, can impact the overall cost of manufacturing.
- Lead Time:Urgent orders with shorter lead times may incur expedited manufacturing fees or higher shipping costs, potentially increasing the overall cost of production.
As a rough estimate, the cost of a Flip Chip PCB can range from tens to hundreds or even thousands of dollars per unit, depending on the aforementioned factors. It’s recommended to consult with PCB manufacturers and suppliers to obtain accurate quotes based on specific project requirements.
What is Flip Chip PCB base material?
The choice of base material for Flip Chip PCBs depends on the specific requirements of the application, including electrical performance, thermal management, and cost considerations. Here are some common base materials used for Flip Chip PCBs:
- FR-4: FR-4 (Flame Retardant 4) is a widely used standard substrate material for PCBs due to its cost-effectiveness and availability. It offers good electrical insulation properties and is suitable for many general-purpose applications. However, for high-frequency and high-speed applications, FR-4 may not provide the desired performance.
- High-Speed Laminates: High-speed laminates are specifically designed for applications requiring high-frequency signal transmission. These laminates typically have low dielectric constant (Dk) and low dissipation factor (Df), which help minimize signal loss and maintain signal integrity at high frequencies. Examples include materials like Rogers Corporation’s RO4000 series, Isola’s FR408, or Taconic’s RF35.
- Ceramic Substrates: Ceramic substrates offer excellent thermal conductivity, making them ideal for applications requiring efficient heat dissipation. They also provide good dimensional stability and high mechanical strength, making them suitable for harsh environments and high-reliability applications. Aluminum oxide (Al2O3) and aluminum nitride (AlN) are common ceramic materials used for PCB substrates.
- Flexible Substrates: For applications requiring flexibility or bendability, flexible substrates such as polyimide (PI) or liquid crystal polymer (LCP) can be used. These materials offer good flexibility while still providing electrical insulation and thermal stability.
- Metal Core PCBs (MCPCBs): Metal core PCBs feature a metal core layer, typically aluminum or copper, sandwiched between layers of dielectric material. These PCBs offer excellent thermal conductivity and are often used in high-power LED lighting and other applications where efficient heat dissipation is critical.
Ultimately, the choice of base material depends on the specific requirements of the Flip Chip PCB application, including signal frequency, power requirements, thermal management needs, and budget constraints. It’s essential to carefully consider these factors when selecting the base material to ensure optimal performance and reliability of the final product.
Which company makes Flip Chip PCBs?
Many companies produce Flip Chip PCBs, including large PCB manufacturers, semiconductor companies, and specialized electronic assembly service providers worldwide. Some of these companies include Foxconn, Omron, Intel, Samsung, Texas Instruments, and Analog Devices. These companies have rich experience and advanced technologies in the field of Flip Chip PCB manufacturing, capable of meeting the needs of various applications.
In our company, we also have the capability to produce high-quality Flip Chip PCBs. We have advanced production equipment and a skilled technical team with the expertise and experience required for designing, manufacturing, and assembling Flip Chip PCBs. Here are some key capabilities of our company in producing Flip Chip PCBs:
- Professional Design Team: We have experienced PCB design engineers capable of designing customized Flip Chip PCB layouts according to the requirements and specifications of our customers.
- Advanced Manufacturing Equipment:We are equipped with state-of-the-art PCB production equipment, including high-precision printers, automated soldering equipment, and precise inspection devices, ensuring the production of high-quality Flip Chip PCBs.
- Strict Quality Control: We adhere to strict quality control standards, conducting rigorous testing and inspection at every stage from raw material procurement to production to ensure that our products meet the requirements and standards of our customers.
- Flexible Production Capacity:We have flexible production capacity to meet the needs of orders of different scales and complexities, including sample production, small-batch production, and large-scale mass production.
- Professional Technical Support:We provide professional technical support and customer service, working closely with our customers to ensure that their Flip Chip PCB projects proceed smoothly and achieve the expected performance and cost objectives.
Therefore, if you have manufacturing needs for Flip Chip PCBs, our company can provide you with high-quality, reliable solutions and ensure timely delivery of products that meet your requirements.
What are the 7 qualities of good customer service?
Good customer service is characterized by several key qualities that help foster positive relationships with customers and ensure their satisfaction. Here are seven qualities of good customer service:
- Responsiveness: Good customer service involves promptly addressing customer inquiries, concerns, and requests. Responding to customers in a timely manner demonstrates attentiveness and a commitment to meeting their needs efficiently.
- Empathy: Empathy is essential for understanding and connecting with customers on a personal level. Customer service representatives who empathize with customers’ emotions and perspectives can provide more meaningful assistance and build rapport.
- Clarity: Effective communication is vital in customer service interactions. Providing clear and concise information helps customers understand solutions, policies, and procedures, reducing confusion and frustration.
- Professionalism: Customer service representatives should conduct themselves in a professional manner at all times, demonstrating respect, courtesy, and integrity. Professionalism fosters trust and confidence in the company and its services.
- Problem-Solving Skills: Good customer service involves helping customers resolve issues and overcome challenges effectively. Customer service representatives should possess strong problem-solving skills to identify root causes, explore solutions, and implement appropriate actions.
- Adaptability: Customer service situations can vary widely, requiring flexibility and adaptability to meet diverse customer needs. Being able to adjust communication styles, problem-solving approaches, and service delivery methods ensures responsiveness to individual customer preferences and circumstances.
- Follow-Up: Following up with customers after resolving their inquiries or issues demonstrates a commitment to their satisfaction and reinforces positive relationships. Following up allows companies to gather feedback, address any remaining concerns, and show appreciation for customers’ business.
By embodying these qualities, companies can deliver exceptional customer service experiences that foster loyalty, retention, and positive word-of-mouth recommendations.
FAQs
What are the advantages of Flip Chip PCBs?
Flip Chip PCBs offer several advantages including shorter electrical paths, higher I/O density, better thermal management, and improved reliability compared to traditional mounting methods like wire bonding.
What applications are Flip Chip PCBs used for?
Flip Chip PCBs are used in various high-performance and miniaturized electronic devices including smartphones, tablets, computers, high-speed communication systems, automotive electronics, medical devices, and aerospace applications.
How are Flip Chip PCBs manufactured?
The manufacturing process for Flip Chip PCBs involves substrate fabrication, surface preparation, flip chip preparation, alignment and placement, solder reflow, optional underfilling, testing and inspection, and final processing.
What base materials are used for Flip Chip PCBs?
Common base materials for Flip Chip PCBs include FR-4, high-speed laminates, ceramic substrates, flexible substrates, and metal core PCBs. The choice depends on factors such as electrical performance, thermal management, and application requirements.
What factors affect the cost of Flip Chip PCBs?
The cost of Flip Chip PCBs can vary depending on factors such as complexity, size, substrate material, quantity, manufacturing technology, assembly process, lead time, and additional processing requirements.
Which companies manufacture Flip Chip PCBs?
Many companies worldwide manufacture Flip Chip PCBs, including large PCB manufacturers, semiconductor companies, and specialized electronic assembly service providers.
What are some design guidelines for Flip Chip PCBs?
Design guidelines for Flip Chip PCBs include substrate selection, routing and layout considerations, pad design, via design, thermal management, assembly considerations, design for testability (DFT), and reliability considerations.