Flip-Chip Substrate Manufacturer
Flip-Chip Substrate Manufacturer. the Package Substrate will be made with Showa Denko and Ajinomoto High speed materials.or other types high speed materials and high frequency materials.
Flip-Chip Substrates are advanced semiconductor packaging solutions that revolutionize the way integrated circuits (ICs) are assembled and interconnected. Unlike traditional packaging methods, Flip-Chip Substrates mount the semiconductor die upside down onto the substrate, allowing direct electrical connections between the chip and the substrate through solder bumps or balls. This design offers several benefits, including reduced package size, enhanced electrical performance, higher signal speeds, improved thermal management, and increased reliability. Flip-Chip Substrates are widely used in various high-performance electronic devices such as microprocessors, graphics processors, memory chips, and communication devices. With their compact size, superior performance, and efficient heat dissipation capabilities, Flip-Chip Substrates play a crucial role in advancing the capabilities of modern electronics, enabling smaller, faster, and more reliable devices across industries.
What is a Flip-Chip Substrate?
A Flip-Chip Substrate is a specialized type of semiconductor packaging technology used in integrated circuits (ICs) and microelectronics assembly. In a Flip-Chip Substrate, the semiconductor die is mounted upside down (flip-chip) onto the substrate, allowing direct connections between the chip and the substrate through solder bumps or balls.
This packaging technique offers several advantages over traditional wire-bonding methods. Firstly, it reduces the size of the package, enabling more compact and lightweight electronic devices. Secondly, it provides shorter interconnection lengths, leading to improved electrical performance and higher signal speeds. Additionally, Flip-Chip Substrates offer better thermal performance due to the direct heat dissipation path from the chip to the substrate.
The substrate itself is typically made of materials like silicon, organic laminate, or ceramic, depending on the specific requirements of the application. It serves as a support structure for the chip and provides electrical connections between the chip and the external circuitry.
Overall, Flip-Chip Substrates are widely used in high-performance and high-density electronic devices such as microprocessors, graphics processors, and memory chips, where compact size, high-speed operation, and efficient heat dissipation are crucial design considerations.
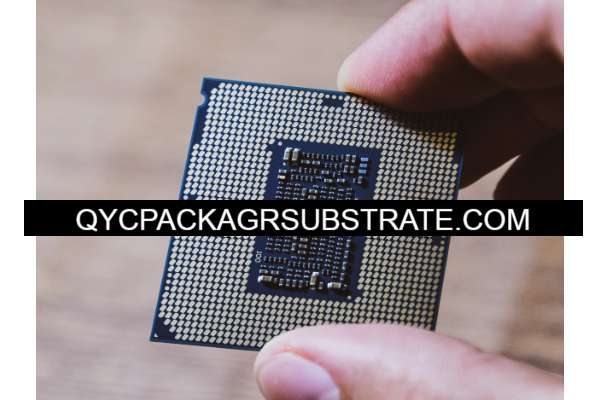
Flip-Chip Substrate Manufacturer
What are the Flip-Chip Substrate Design Guidelines?
Designing with Flip-Chip Substrates requires careful consideration of various factors to ensure optimal performance and reliability. Here are some general guidelines:
- Bump Design: Pay attention to the size, shape, and pitch of the solder bumps. Ensure uniformity and proper alignment for reliable electrical connections between the chip and substrate.
- Substrate Material Selection: Choose substrate materials with appropriate thermal conductivity, coefficient of thermal expansion (CTE) matching that of the chip, and electrical properties suitable for the application.
- Substrate Layout: Optimize the layout of the substrate to minimize signal integrity issues such as signal crosstalk, noise coupling, and impedance mismatch. Proper signal routing and power distribution are crucial.
- Thermal Management: Implement effective thermal management techniques such as thermal vias, heat spreaders, and thermal pads to dissipate heat generated by the chip efficiently and prevent overheating.
- Die Attach Process: Ensure proper alignment and accurate placement of the chip during the die attach process to avoid misalignment issues that can lead to electrical failures or solder joint reliability problems.
- Underfill Encapsulation: Apply underfill material between the chip and substrate to enhance mechanical strength, reduce stress on solder joints, and improve resistance to thermal cycling and mechanical shock.
- Package Size and Thickness:Optimize the size and thickness of the package to meet space constraints and mechanical requirements while maintaining electrical performance and thermal characteristics.
- Reliability Testing: Perform thorough reliability testing, including thermal cycling, mechanical shock, and accelerated aging tests, to validate the robustness and long-term reliability of the Flip-Chip Substrate design.
- Assembly and Handling Guidelines: Follow proper assembly and handling procedures to prevent damage to the delicate solder bumps, minimize contamination, and ensure consistent quality during manufacturing.
- Design for Manufacturing (DFM): Collaborate closely with manufacturing partners to address manufacturability issues early in the design process and optimize the Flip-Chip Substrate design for efficient and cost-effective production.
By adhering to these guidelines and considering the specific requirements of the application, designers can develop Flip-Chip Substrate designs that offer superior performance, reliability, and manufacturability.
What is the Flip-Chip Substrate Fabrication Process?
The fabrication process for Flip-Chip Substrates involves several steps to create a substrate capable of hosting flip-chip mounted semiconductor dies. Here’s a general overview of the process:
- Substrate Preparation: Initially, a suitable substrate material is selected based on the specific requirements of the application. Common substrate materials include silicon, organic laminate (e.g., FR-4), or ceramic. The substrate is then prepared by cleaning and planarizing its surface to ensure uniformity.
- Dielectric Layer Deposition:A dielectric layer is deposited onto the substrate surface using techniques like physical vapor deposition (PVD), chemical vapor deposition (CVD), or spin coating. This dielectric layer serves as insulation and provides a smooth surface for subsequent processing steps.
- Metal Deposition: Metal layers, typically consisting of copper or aluminum, are deposited onto the substrate surface using techniques such as sputtering, electroplating, or chemical deposition. These metal layers form the conductive traces and interconnects on the substrate.
- Lithography and Etching: Photolithography is used to pattern the metal layers, defining the layout of the interconnects and bonding pads. A photoresist is applied to the metal layer, exposed to UV light through a mask with the desired circuit pattern, and developed to remove the unexposed areas. Subsequently, the exposed metal is etched away, leaving behind the desired conductor traces and bonding pads.
- Surface Finish: A surface finish is applied to the metal layers to improve solderability and prevent oxidation. Common surface finishes include electroless nickel immersion gold (ENIG), organic solderability preservative (OSP), and electroplated gold or tin.
- Solder Mask Application: A solder mask layer is applied over the metal traces and bonding pads to insulate them and protect against solder bridging during the flip-chip assembly process. The solder mask is selectively patterned to expose the bonding pads for solder attachment.
- Bumping:Solder bumps or balls are formed on the exposed bonding pads using techniques such as solder paste printing followed by reflow soldering, electroplating, or solder ball placement using stencil printing and reflow.
- Flip-Chip Assembly: The semiconductor dies are attached to the substrate in an inverted orientation, aligning the solder bumps on the die with the corresponding bonding pads on the substrate. The assembly is then heated to reflow the solder, forming electrical connections between the die and substrate.
- Underfill Encapsulation: An underfill material is dispensed around the perimeter of the flip-chip assembly to enhance mechanical strength, reduce stress on the solder joints, and improve reliability. The underfill is then cured to form a rigid encapsulation.
- Testing and Inspection: The fabricated Flip-Chip Substrates undergo various electrical tests and inspections to ensure proper functionality, solder joint integrity, and reliability before being incorporated into electronic devices.
By following these fabrication steps with precision and care, manufacturers can produce Flip-Chip Substrates that meet the demanding requirements of high-performance microelectronics applications.
How Do You Manufacture a Flip-Chip Substrate?
Manufacturing a Flip-Chip Substrate involves several stages of fabrication and assembly processes. Here’s a detailed overview of the typical manufacturing process:
- Design and Layout:The process begins with the design of the Flip-Chip Substrate, including the layout of electrical traces, bonding pads, and other features. Design software is used to create the layout, taking into account factors such as signal integrity, thermal management, and mechanical stability.
- Substrate Fabrication:The substrate material, often a semiconductor-grade material like silicon, organic laminate (e.g., FR-4), or ceramic, is prepared. This involves cleaning and planarizing the substrate surface to ensure uniformity and cleanliness.
- Dielectric Layer Deposition: A thin layer of dielectric material is deposited onto the substrate surface. This layer serves as insulation between the metal layers and provides a smooth surface for subsequent processing steps. Deposition methods may include physical vapor deposition (PVD), chemical vapor deposition (CVD), or spin coating.
- Metal Deposition and Patterning: Metal layers, typically copper or aluminum, are deposited onto the substrate surface using techniques such as sputtering, electroplating, or chemical deposition. These metal layers form the conductive traces and interconnects on the substrate. Photolithography and etching processes are then used to pattern the metal layers, defining the layout of the interconnects and bonding pads.
- Surface Finish: A surface finish is applied to the metal layers to improve solderability and prevent oxidation. Common surface finishes include electroless nickel immersion gold (ENIG), organic solderability preservative (OSP), and electroplated gold or tin.
- Solder Mask Application: A solder mask layer is applied over the metal traces and bonding pads to insulate them and protect against solder bridging during assembly. The solder mask is selectively patterned to expose the bonding pads for solder attachment.
- Bumping: Solder bumps or balls are formed on the exposed bonding pads using techniques such as solder paste printing followed by reflow soldering, electroplating, or solder ball placement using stencil printing and reflow.
- Flip-Chip Assembly: The semiconductor dies are attached to the substrate in an inverted orientation, aligning the solder bumps on the die with the corresponding bonding pads on the substrate. The assembly is then heated to reflow the solder, forming electrical connections between the die and substrate.
- Underfill Encapsulation: An underfill material is dispensed around the perimeter of the flip-chip assembly to enhance mechanical strength, reduce stress on the solder joints, and improve reliability. The underfill is then cured to form a rigid encapsulation.
- Testing and Inspection: The manufactured Flip-Chip Substrates undergo various electrical tests and inspections to ensure proper functionality, solder joint integrity, and reliability before being packaged and integrated into electronic devices.
Throughout the manufacturing process, stringent quality control measures are implemented to ensure the consistency, reliability, and performance of the Flip-Chip Substrates. Collaboration between design, engineering, and manufacturing teams is essential to optimize the process and address any challenges that may arise.
How Much Should a Flip-Chip Substrate Cost?
The cost of a Flip-Chip Substrate can vary widely depending on several factors such as:
- Complexity: The complexity of the substrate design, including the number of layers, the density of interconnects, and the size of the substrate, can significantly impact the cost. More complex designs often require specialized fabrication techniques and materials, driving up the cost.
- Materials: The choice of substrate materials, dielectric layers, metal layers, and surface finishes can influence the overall cost. High-quality materials with specific electrical, thermal, and mechanical properties may be more expensive than standard materials.
- Manufacturing Process: The manufacturing processes involved in producing Flip-Chip Substrates, including deposition, patterning, bumping, assembly, and testing, contribute to the overall cost. Advanced fabrication techniques and specialized equipment may increase manufacturing expenses.
- Volume: Economies of scale play a significant role in determining the cost of Flip-Chip Substrates. Larger production volumes typically result in lower per-unit costs due to efficiencies in material utilization, equipment utilization, and overhead expenses.
- Supplier Relationships: The relationship between the buyer and the substrate manufacturer can impact pricing. Long-term partnerships, volume commitments, and negotiated contracts may lead to more favorable pricing terms.
- Customization and Additional Services: Customized features, additional testing requirements, and value-added services such as design support, engineering consultation, and quality assurance may incur additional costs.
- Market Dynamics: Market demand, supply chain disruptions, raw material prices, and industry trends can influence substrate pricing over time. Fluctuations in these factors may lead to price volatility.
As a rough estimate, the cost of a Flip-Chip Substrate can range from a few dollars to several hundred dollars per unit, depending on the aforementioned factors. For precise pricing information, it’s best to consult with substrate manufacturers or suppliers who can provide quotes based on specific design requirements, volumes, and other considerations.
What is Flip-Chip Substrate Base Material?
The base material for a Flip-Chip Substrate can vary depending on the specific requirements of the application. Common materials used as the base substrate include:
- Silicon: Silicon is often used as the substrate material for Flip-Chip Substrates, especially in applications where high-performance semiconductors are required. Silicon substrates offer excellent thermal conductivity, mechanical stability, and compatibility with semiconductor manufacturing processes.
- Organic Laminate: Organic laminate materials, such as FR-4 (Flame Retardant 4), are widely used for Flip-Chip Substrates in consumer electronics and other applications where cost-effectiveness and flexibility are important. Organic laminate substrates offer good electrical insulation, ease of fabrication, and a wide range of available properties.
- Ceramic: Ceramic substrates, such as alumina (Al2O3) or aluminum nitride (AlN), are preferred for high-power and high-frequency applications due to their excellent thermal conductivity, low coefficient of thermal expansion (CTE), and high mechanical strength. Ceramic substrates are often used in automotive, aerospace, and telecommunications industries.
- Glass: Glass substrates are sometimes used in specialized applications requiring high precision, such as microelectromechanical systems (MEMS) and bioelectronics. Glass substrates offer excellent dimensional stability, chemical resistance, and optical transparency.
The choice of base material depends on factors such as electrical performance, thermal management requirements, mechanical stability, cost considerations, and compatibility with assembly processes. Designers select the most suitable substrate material based on the specific needs of the Flip-Chip Substrate application.
Which Company Makes Flip-Chip Substrate?
Many companies produce Flip-Chip Substrates, including well-known semiconductor manufacturers, packaging service providers, and companies specializing in substrate manufacturing. Some major companies include Intel, TSMC, UMC, Qualcomm, Samsung Electronics, Micron Technology, Epson, Amkor, ASM International, and others.
In our company, we can also manufacture high-quality Flip-Chip Substrates. We have advanced manufacturing equipment and technology, a professional engineering team, and extensive experience to meet the needs of our customers. Our manufacturing process strictly adheres to industry standards and quality control requirements to ensure the production of reliable and high-performance Flip-Chip Substrates.
Our manufacturing capabilities include:
- Design and Engineering Support: We have experienced design and engineering teams that can provide comprehensive support from concept to production. We collaborate with customers to customize designs according to their specific requirements and provide professional advice and technical support.
- Material Selection and Procurement: We work with reliable suppliers to ensure the selection and procurement of high-quality, compliant substrate materials and related materials. We can provide a variety of options according to customer requirements and ensure timely delivery.
- Manufacturing Processes: We employ advanced manufacturing processes and equipment, including deposition, patterning, bumping, assembly, and testing processes. We strictly control each manufacturing step to ensure product quality and consistency.
- Quality Control: We implement strict quality control measures, from raw material inspection to final product inspection, to ensure that each Flip-Chip Substrate meets customer specifications and standards. Our quality management system complies with international standards such as ISO 9001.
- Customer Service: We focus on communication and collaboration with customers to tailor solutions according to their needs and provide timely technical support and after-sales service. We are committed to building long-term, stable partnerships and achieving mutual success.
In summary, as a professional manufacturer, we have the capability to provide high-quality, reliable Flip-Chip Substrates and offer comprehensive support and services to our customers.
What are the 7 Qualities of Good Customer Service?
Good customer service is characterized by several key qualities that contribute to positive interactions and relationships with customers. Here are seven qualities of good customer service:
- Responsiveness: Good customer service involves being prompt and responsive to customer inquiries, requests, and concerns. Customers appreciate quick and efficient assistance, whether it’s answering questions, resolving issues, or providing support.
- Empathy: Empathy is the ability to understand and share the feelings of others. Good customer service representatives demonstrate empathy by actively listening to customers, acknowledging their concerns, and showing genuine care and understanding.
- Professionalism: Professionalism entails maintaining a courteous and respectful demeanor in all interactions with customers. Good customer service representatives are knowledgeable, well-trained, and conduct themselves professionally, regardless of the situation.
- Reliability: Reliability is essential for building trust and confidence with customers. Good customer service involves consistently delivering on promises, meeting deadlines, and providing accurate information and solutions.
- Flexibility: Good customer service requires flexibility and adaptability to meet the diverse needs and preferences of customers. Representatives should be willing to accommodate reasonable requests, offer personalized solutions, and adjust strategies as needed to ensure customer satisfaction.
- Problem-solving skills: Effective problem-solving skills are crucial for addressing customer issues and resolving conflicts efficiently. Good customer service representatives are proactive in identifying problems, analyzing root causes, and implementing solutions to prevent recurrence.
- Positive attitude: A positive attitude can make a significant difference in customer interactions. Good customer service representatives maintain a friendly and optimistic demeanor, even in challenging situations, which helps to create a positive customer experience and foster customer loyalty.
By embodying these qualities, organizations can deliver exceptional customer service that not only meets but exceeds customer expectations, ultimately leading to increased customer satisfaction, loyalty, and advocacy.
FAQs
What is a Flip-Chip Substrate?
A Flip-Chip Substrate is a specialized semiconductor packaging technology where the semiconductor die is mounted upside down (flip-chip) onto the substrate, allowing direct connections between the chip and the substrate through solder bumps or balls.
What are the advantages of Flip-Chip Substrates?
Flip-Chip Substrates offer several advantages, including reduced package size, improved electrical performance, higher signal speeds, better thermal management, and increased reliability compared to traditional wire-bonding methods.
What materials are used in Flip-Chip Substrates?
Common substrate materials for Flip-Chip Substrates include silicon, organic laminate (e.g., FR-4), ceramic, and glass. The choice of material depends on factors such as electrical performance, thermal conductivity, mechanical stability, and cost considerations.
How are solder bumps applied to Flip-Chip Substrates?
Solder bumps or balls are typically applied to Flip-Chip Substrates using techniques such as solder paste printing followed by reflow soldering, electroplating, or solder ball placement using stencil printing and reflow.
What is the underfill encapsulation process in Flip-Chip Substrates?
Underfill encapsulation involves dispensing an underfill material around the perimeter of the flip-chip assembly to enhance mechanical strength, reduce stress on the solder joints, and improve reliability. The underfill is then cured to form a rigid encapsulation.
How are Flip-Chip Substrates tested for reliability?
Flip-Chip Substrates undergo various reliability tests, including thermal cycling, mechanical shock, and accelerated aging tests, to validate their robustness and long-term reliability. Electrical tests are also performed to ensure proper functionality and solder joint integrity.
What are some common applications of Flip-Chip Substrates?
Flip-Chip Substrates are used in a wide range of high-performance electronic devices, including microprocessors, graphics processors, memory chips, application-specific integrated circuits (ASICs), system-on-chip (SoC) devices, and high-speed communication devices.
What factors influence the cost of Flip-Chip Substrates?
The cost of Flip-Chip Substrates depends on factors such as substrate complexity, materials used, manufacturing processes, volume production, customization requirements, and market dynamics.