FR408HR Materials PCB Manufacturer
FR408HR Materials PCB Manufacturer,FR408HR Materials PCBs are advanced printed circuit boards fabricated using FR408HR materials, renowned for their high-performance characteristics in demanding applications. These PCBs feature a low dielectric constant and dissipation factor, ensuring excellent signal integrity and minimal signal loss at high frequencies. FR408HR Materials PCBs are designed for use in high-speed digital and RF/microwave applications, where reliable performance and impedance control are critical. They offer superior thermal stability and mechanical strength, making them suitable for aerospace, telecommunications, and high-frequency electronic devices. FR408HR Materials PCBs are manufactured with precision to meet stringent industry standards for reliability and performance in complex electronic systems.
What is an FR408HR Materials PCB?
FR408HR Materials PCB is a high-performance printed circuit board (PCB) that uses the FR408HR resin system as its substrate. Developed by Isola Group, this material is renowned for its superior thermal and electrical properties, making it widely used in high-frequency and high-speed digital applications.
Firstly, FR408HR material has a high glass transition temperature (Tg), typically above 230°C. This means it can maintain its physical and electrical properties at high temperatures without deformation, making it suitable for electronic devices that need to withstand high temperatures. Additionally, it has a low coefficient of thermal expansion (CTE), which helps reduce mechanical stress caused by thermal cycling, thereby improving the reliability of the PCB.
Secondly, FR408HR material performs excellently in high-frequency applications. Its low dielectric constant (Dk) and dielectric loss factor (Df) enable it to maintain signal integrity and stability in high-speed signal transmission. This is particularly important in fields such as 5G communication devices, servers, and high-performance computing.
Moreover, the manufacturing process of FR408HR material is well-established and compatible with standard PCB manufacturing processes. This allows it to be used alongside other common PCB materials like FR4 without adding complexity or cost to production.
In summary, FR408HR Materials PCB combines high thermal stability, excellent electrical properties, and good processability, making it an ideal choice for high-performance electronic devices and applications requiring high reliability, such as telecommunications, data centers, and advanced computing systems. By using FR408HR material, designers can enhance the performance and reliability of their products, meeting the stringent demands of modern electronic products for high-frequency, high-speed, and high-temperature environments.
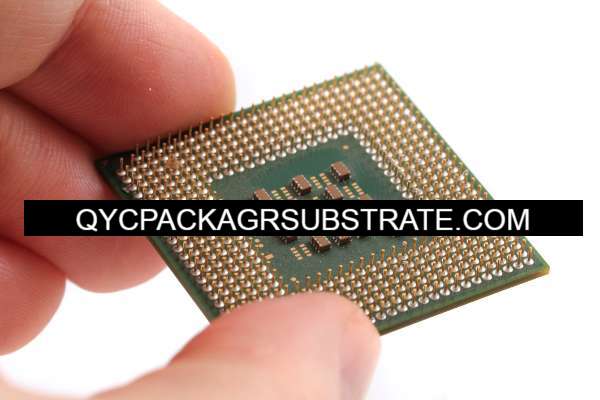
FR408HR Materials PCB Manufacturer
What are the FR408HR Materials PCB Design Guidelines?
Designing with FR408HR Materials PCB involves several key guidelines to ensure optimal performance and reliability:
- Consider High Tg Requirements: FR408HR has a high glass transition temperature (Tg), typically above 230°C. Designers should leverage this property for applications requiring resistance to high temperatures.
- Controlled Impedance Design: Due to its low dielectric constant (Dk) and stable electrical properties, FR408HR is suitable for controlled impedance applications. Design traces to achieve desired impedance values and maintain signal integrity.
- Thermal Management: Utilize the low coefficient of thermal expansion (CTE) of FR408HR to minimize thermal stress and ensure reliability during temperature fluctuations. Design for adequate heat dissipation in high-power applications.
- Stackup Design: Optimize PCB stackup considering signal integrity, power distribution, and thermal requirements. Utilize the dielectric properties of FR408HR to achieve desired layer stack configurations.
- Signal Integrity Considerations: Maintain signal integrity by minimizing signal losses and reflections. Ensure proper grounding and signal routing techniques to mitigate electromagnetic interference (EMI) and crosstalk.
- Manufacturing Compatibility: FR408HR is compatible with standard PCB manufacturing processes. Design PCBs with standard design rules and ensure manufacturability without introducing complexities.
- Mechanical Design: Consider mechanical aspects such as board stiffness and dimensional stability. Design for mechanical reliability to withstand handling, assembly, and environmental stresses.
- Testing and Validation:Conduct rigorous testing and validation processes to ensure that the designed PCB meets performance specifications under operational conditions. Include signal integrity testing and thermal cycling tests as necessary.
By adhering to these design guidelines, designers can harness the superior thermal and electrical properties of FR408HR Materials PCB effectively, ensuring high performance and reliability in diverse electronic applications.
What is the FR408HR Materials PCB Fabrication Process?
The fabrication process for FR408HR Materials PCB typically follows these steps:
- Preparation of Substrate Materials: The process begins with preparing the FR408HR laminate sheets. These sheets consist of a core layer made from FR408HR resin impregnated with woven glass fabric.
- Drilling: Holes for through-holes and vias are drilled into the laminate sheets using precision drilling machines. This step requires careful alignment and control to ensure accuracy.
- Electroless Copper Deposition: The drilled laminate sheets undergo electroless copper deposition. This process deposits a thin layer of copper on the walls of the drilled holes, creating a conductive surface for subsequent plating.
- Plating: Copper plating is performed to increase the thickness of the copper layers both on the surfaces and inside the drilled holes. This step ensures sufficient conductivity and durability of the PCB traces and vias.
- Lamination:Multiple layers of pre-preg (pre-impregnated fiberglass material) and copper-clad laminate are stacked according to the PCB design specifications. The stack is then pressed together under heat and pressure to bond the layers into a single rigid board.
- Etching: A photoresist pattern is applied to define the copper traces and features on the PCB surface. The board undergoes etching to remove unwanted copper, leaving behind the desired circuit traces and pads.
- Surface Finish:After etching, the PCB surface is prepared with a surface finish to protect the copper traces from oxidation and to facilitate soldering during assembly. Common surface finishes include HASL (Hot Air Solder Leveling), ENIG (Electroless Nickel Immersion Gold), and OSP (Organic Solderability Preservatives).
- Silkscreen Printing: Information such as component outlines, reference designators, and logos are printed onto the PCB surface using a silkscreen printing process. This step aids in assembly and identification of components.
- Quality Inspection: Throughout the fabrication process, various inspections are conducted to ensure quality and adherence to design specifications. This includes dimensional checks, electrical testing, and visual inspection of the finished PCBs.
- Final Testing: The completed PCBs undergo final electrical testing to verify functionality and performance. This may include continuity checks, impedance testing, and other electrical measurements.
- Routing and Profiling: After testing, individual PCBs are routed from the panel and their edges are profiled to their final dimensions. This step prepares them for assembly into electronic products.
By following these fabrication steps, manufacturers can produce FR408HR Materials PCBs with precise circuitry, reliable electrical characteristics, and mechanical durability, suitable for a wide range of high-performance electronic applications.
How do you manufacture an FR408HR Materials PCB?
Manufacturing an FR408HR Materials PCB involves a detailed process to ensure high-quality and reliable performance:
- Material Preparation: Begin by preparing FR408HR laminate sheets. These consist of a core layer made from FR408HR resin impregnated with woven glass fabric. Ensure the laminate sheets meet required specifications for thickness and Tg (glass transition temperature).
- Drilling:Use precision drilling machines to drill holes for through-holes and vias in the FR408HR laminate sheets. Accurate drilling is critical to ensure alignment and integrity of the PCB design.
- Electroless Copper Deposition: After drilling, apply an electroless copper deposition process to the drilled laminate sheets. This deposits a thin layer of copper on the walls of the holes, creating a conductive surface for subsequent plating.
- Copper Plating: Perform copper plating to increase the thickness of copper layers on both surfaces and inside the drilled holes. This step ensures adequate conductivity and durability of PCB traces and vias.
- Layer Stacking and Lamination:Stack multiple layers of pre-preg (pre-impregnated fiberglass material) and copper-clad laminate according to the PCB design. Use heat and pressure in a lamination process to bond the layers together into a single rigid board structure.
- Etching: Apply a photoresist layer to define the copper traces and features on the PCB surface. Use etching chemicals to remove unwanted copper, leaving behind the desired circuit patterns and pads.
- Surface Finish Application: Apply a surface finish to protect the exposed copper traces from oxidation and facilitate soldering during assembly. Common surface finishes include HASL, ENIG, and OSP, chosen based on application requirements.
- Silkscreen Printing: Use silkscreen printing to add component outlines, reference designators, and other markings to the PCB surface. This aids in assembly and identification of components during PCB population.
- Quality Inspection: Conduct rigorous inspections throughout the manufacturing process to ensure adherence to design specifications and quality standards. Inspections include dimensional checks, electrical testing, and visual inspection of finished PCBs.
- Final Electrical Testing: Perform final electrical testing to verify functionality and performance of the completed PCBs. Testing may include continuity checks, impedance measurements, and other electrical tests.
- Routing and Profiling: After testing, separate individual PCBs from the panel using routing machines. Profile the edges of the PCBs to their final dimensions, preparing them for assembly into electronic products.
By following these manufacturing steps, PCB manufacturers can produce FR408HR Materials PCBs with precise circuitry, reliable electrical characteristics, and mechanical robustness, suitable for demanding high-frequency and high-speed electronic applications.
How much should an FR408HR Materials PCB cost?
The cost of FR408HR Materials PCBs can vary based on several factors including:
- Board Size and Complexity: Larger boards or those with complex designs (dense trace routing, multiple layers) generally cost more due to increased material usage and longer manufacturing times.
- Layer Count: PCBs with more layers typically cost more due to additional material and manufacturing complexity.
- Surface Finish: Different surface finishes (e.g., HASL, ENIG, OSP) have varying costs, with ENIG generally being more expensive than HASL due to the use of precious metals.
- Copper Weight: Thicker copper layers (e.g., 2 oz, 3 oz) increase material costs and affect manufacturing processes, influencing overall pricing.
- Tolerances and Specifications: Tighter tolerances and specific design requirements (e.g., controlled impedance) can increase manufacturing complexity and cost.
- Volume: Larger production runs typically result in lower per-unit costs due to economies of scale. Prototype or small batch orders may be more expensive per unit.
- Lead Time: Expedited manufacturing or shorter lead times often incur additional costs compared to standard production schedules.
As a rough estimate, FR408HR Materials PCBs can range from a few dollars per square inch for simple designs and standard specifications to tens or even hundreds of dollars per square inch for complex, high-specification boards. For precise pricing, it’s best to consult with PCB manufacturers who can provide detailed quotes based on specific design requirements and quantities needed.
What is an FR408HR Materials PCB base material?
An FR408HR Materials PCB base material refers to the core substrate used in the fabrication of printed circuit boards (PCBs) utilizing FR408HR resin system. FR408HR is a type of high-performance laminate developed by Isola Group. It consists of a composite material comprising:
- FR408HR Resin: This resin system is designed to offer high thermal stability, with a glass transition temperature (Tg) typically above 230°C. It provides excellent mechanical strength and dimensional stability even at elevated temperatures, making it suitable for applications requiring resistance to heat and thermal cycling.
- Glass Reinforcement: The core of FR408HR laminate includes woven glass fabric reinforcement. This reinforcement enhances the PCB’s mechanical strength and provides excellent dielectric properties essential for high-frequency signal transmission.
- Copper Foil: Thin layers of copper foil are laminated to both sides of the FR408HR core during the manufacturing process. These foils serve as conductive pathways for electrical signals and power distribution throughout the PCB.
- Pre-preg Layers: Pre-preg layers, consisting of resin-impregnated fiberglass cloth, are used between copper layers to bond them together during lamination. These layers ensure the integrity and stability of the PCB structure.
FR408HR Materials PCB base material is chosen for its superior electrical performance, including low dielectric loss (Df) and a stable dielectric constant (Dk), which are crucial for maintaining signal integrity in high-frequency and high-speed applications. Its robust thermal properties make it suitable for use in demanding environments where temperature extremes and thermal management are concerns.
Overall, FR408HR Materials PCB base material is favored in applications such as telecommunications, aerospace, and high-speed computing, where reliability, thermal performance, and signal integrity are critical requirements.
Which company makes FR408HR Materials PCBs?
FR408HR Materials PCBs are produced by Isola Group. Isola Group is a leading global manufacturer specializing in high-performance materials, focusing on the development and production of various printed circuit board (PCB) materials, including high-performance resin systems and composite materials required for high-frequency and high-speed applications.
FR408HR, as a flagship product of Isola Group, is widely recognized in the industry for its superior thermal stability and electrical performance. It features a glass transition temperature (Tg) typically exceeding 230°C, maintaining stable physical and electrical performance in high-temperature environments, making it particularly suitable for applications requiring high temperature resistance and thermal cycling durability.
Our company is also capable of manufacturing FR408HR Materials PCBs. As a company dedicated to high-performance electronic materials and PCB manufacturing, we have advanced production equipment and a skilled technical team capable of precisely manufacturing FR408HR Materials PCB products according to customer design requirements and technical specifications.
Our production process includes precise lamination, drilling, copper foil deposition, plating, etching, surface treatment, and final electrical testing. We rigorously control each manufacturing step to ensure product quality and performance meet customer expectations.
Whether in telecommunications equipment, high-speed computing, medical electronics, aerospace, or other high-performance electronic device fields, our FR408HR Materials PCBs provide reliable solutions. We are committed to delivering the highest quality products and services to our customers, meeting their various needs and challenges in complex electronic applications through technological innovation and excellent manufacturing processes.
What are the 7 qualities of good customer service?
Good customer service typically embodies the following seven qualities:
- Responsiveness: A prompt and timely response to customer inquiries, concerns, or requests is crucial. Customers appreciate being acknowledged promptly and receiving timely updates or resolutions to their issues.
- Empathy: Showing empathy involves understanding and acknowledging the customer’s emotions, concerns, and perspective. Empathetic responses help build rapport and trust with customers, demonstrating that their feelings and experiences are valued.
- Clear Communication: Effective communication is essential in customer service. This includes using clear and concise language, actively listening to customers, and ensuring information is conveyed accurately. Clear communication reduces misunderstandings and enhances the customer’s understanding of solutions or processes.
- Knowledgeability: Customer service representatives should possess adequate knowledge about products, services, policies, and procedures. Being knowledgeable allows them to provide accurate information, answer questions confidently, and offer relevant advice or solutions to customers.
- Professionalism: Maintaining professionalism in interactions with customers involves being courteous, respectful, and maintaining a positive attitude, even in challenging situations. Professional behavior instills confidence in customers and reflects well on the company’s image.
- Problem-solving Skills: Effective customer service involves the ability to identify and resolve customer issues efficiently. This includes analyzing problems, proposing solutions, and following through until the issue is resolved to the customer’s satisfaction.
- Personalization: Tailoring interactions to meet the specific needs and preferences of each customer contributes to a positive customer experience. Personalization may involve remembering customer preferences, addressing them by name, and offering personalized recommendations or solutions.
By embodying these qualities, companies can foster strong customer relationships, enhance satisfaction, and differentiate themselves positively in the marketplace.
FAQs
What is FR408HR material?
FR408HR is a high-performance resin system used in printed circuit boards (PCBs). It has a high glass transition temperature (Tg) and is known for its excellent thermal stability and electrical performance, making it suitable for high-frequency and high-speed applications.
What are the key advantages of using FR408HR Materials PCBs?
FR408HR Materials PCBs offer superior thermal stability, low dielectric loss (Df), and a stable dielectric constant (Dk), which are crucial for maintaining signal integrity in high-frequency applications. They also exhibit excellent mechanical strength and dimensional stability at elevated temperatures.
What applications are FR408HR Materials PCBs suitable for?
FR408HR Materials PCBs are used in various applications requiring high reliability, thermal performance, and signal integrity. Typical applications include telecommunications equipment, high-speed computing, aerospace systems, medical electronics, and more.
What surface finishes are compatible with FR408HR Materials PCBs?
FR408HR Materials PCBs are compatible with a range of surface finishes including HASL (Hot Air Solder Leveling), ENIG (Electroless Nickel Immersion Gold), OSP (Organic Solderability Preservatives), and others. The choice of surface finish depends on specific application requirements.
Can FR408HR Materials PCBs be manufactured with controlled impedance?
Yes, FR408HR Materials PCBs can be designed and manufactured with controlled impedance. The low dielectric constant (Dk) and stable electrical properties of FR408HR make it suitable for applications requiring precise control over signal transmission characteristics.
How does the cost of FR408HR Materials PCBs compare to other PCB materials?
The cost of FR408HR Materials PCBs varies based on factors such as board size, complexity, layer count, surface finish, and volume. Generally, FR408HR Materials PCBs may be more expensive than standard FR4 PCBs due to their advanced material properties and manufacturing requirements.
What should be considered when designing FR408HR Materials PCBs?
Design considerations for FR408HR Materials PCBs include optimizing layer stackup for signal integrity, ensuring adequate thermal management, specifying controlled impedance requirements, and selecting appropriate surface finishes. It’s also important to work with experienced PCB manufacturers familiar with handling high-performance materials like FR408HR.