HDI R&D PCB Manufacturer
HDI R&D PCB Manufacturer,HDI R&D PCBs are innovative circuit boards designed for research and development purposes, boasting advanced interconnect technologies. With intricate routing patterns and multiple layers, they offer higher component density and improved signal integrity. These boards are pivotal in prototyping cutting-edge electronic devices, from compact consumer gadgets to aerospace systems. Their ability to accommodate fine-pitch components and facilitate miniaturization makes them ideal for applications where space and performance are paramount. HDI R&D PCBs represent the forefront of PCB design, enabling engineers to push the boundaries of electronic innovation.
What is an HDI R&D PCB?
An HDI R&D PCB, which stands for High-Density Interconnect Research and Development Printed Circuit Board, is a specialized type of circuit board used in the development and testing of high-density interconnect technologies. HDI PCBs are designed to accommodate complex electronic components and intricate routing patterns in a compact space, making them ideal for applications where size and weight are critical factors, such as mobile devices, aerospace systems, and medical equipment.
The R&D aspect implies that these PCBs are specifically tailored for research and development purposes, meaning they may feature experimental designs, new materials, or cutting-edge manufacturing techniques aimed at pushing the boundaries of what’s possible in terms of miniaturization, performance, and reliability.
These boards often undergo rigorous testing to assess their electrical performance, thermal management capabilities, and overall durability. Researchers and engineers use HDI R&D PCBs to prototype new electronic devices, refine existing designs, and explore innovative solutions to technical challenges.
In summary, an HDI R&D PCB is a specialized circuit board used in the research and development of high-density interconnect technologies, offering compactness, performance, and reliability for a wide range of advanced electronic applications.
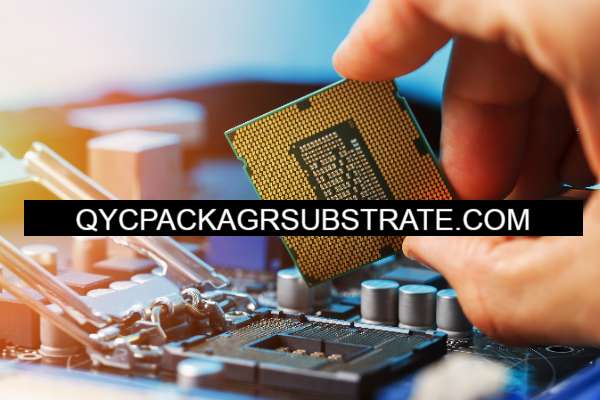
HDI R&D PCB Manufacturer
What are the HDI R&D PCB Design Guidelines?
Designing HDI R&D PCBs requires careful consideration of various factors to ensure optimal performance and manufacturability. Here are some key guidelines typically followed:
- Layer Stackup: Utilize a multilayer stackup with alternating signal and ground layers to minimize electromagnetic interference (EMI) and provide adequate power distribution.
- Via Types and Placement: Employ various via types, such as microvias, blind vias, and buried vias, to enable high-density routing. Place vias strategically to minimize signal distortion and impedance mismatch.
- Minimum Feature Size:Define minimum trace width, spacing, and pad size according to the capabilities of the manufacturing process to achieve the desired density while maintaining signal integrity.
- Signal Integrity:Ensure controlled impedance for high-speed signals by carefully selecting trace widths, dielectric materials, and layer thicknesses. Avoid sharp corners and right-angle bends to reduce signal reflections and losses.
- Thermal Management: Incorporate thermal vias and thermal pads to facilitate heat dissipation from high-power components and ensure stable operation under varying temperature conditions.
- Component Placement: Optimize component placement to minimize signal path lengths, reduce crosstalk, and facilitate efficient routing. Place critical components closer to the center of the board for better signal integrity.
- Design for Manufacturing (DFM): Adhere to DFM guidelines to simplify the manufacturing process and minimize fabrication issues. Consider factors such as material availability, tolerances, and assembly requirements.
- Design for Test (DFT): Incorporate test points, access channels, and built-in self-test features to facilitate debugging, testing, and troubleshooting during the development and validation phases.
- Design Rule Check (DRC): Perform thorough design rule checks using appropriate design software to identify and resolve potential layout errors, such as short circuits, clearance violations, and manufacturing constraints.
- Documentation:Create comprehensive design documentation, including schematics, layout files, assembly drawings, and fabrication notes, to communicate design specifications and requirements to stakeholders and manufacturing partners.
By adhering to these guidelines, designers can develop HDI R&D PCBs that meet the demanding performance, density, and reliability requirements of advanced electronic applications while expediting the research and development process.
What is the HDI R&D PCB Fabrication Process?
The fabrication process for HDI R&D PCBs involves several intricate steps to create high-density interconnects with precise routing and component placement. Here’s an overview of the typical process:
- Substrate Preparation: The process begins with preparing the substrate material, usually a high-performance laminate such as FR-4, BT (bismaleimide triazine), or polyimide. The substrate is cleaned and coated with a thin layer of copper on both sides.
- Layer Alignment and Lamination: Multiple layers of substrate material are stacked together, with each layer featuring circuit patterns and vias. Alignment holes are drilled in the layers to ensure precise registration. The layers are then laminated together under heat and pressure to form a solid panel.
- Drilling: After lamination, precision micro-drilling or laser drilling is performed to create small-diameter vias known as microvias, which connect different layers of the PCB. Blind vias, which connect an outer layer to inner layers, and buried vias, which connect inner layers, may also be drilled at this stage.
- Copper Plating: The drilled vias are plated with copper using processes such as electroplating or chemical deposition. This step builds up the conductive pathways required for interconnections between layers.
- Etching: A photolithography process is used to apply a photoresist layer to the copper-clad substrate. Circuit patterns are then exposed onto the photoresist using a mask and UV light. After development, the exposed copper is etched away, leaving behind the desired circuit traces.
- Surface Finish: Surface finish is applied to the exposed copper traces to protect them from oxidation and facilitate soldering during assembly. Common surface finish options include immersion gold, electroless nickel immersion gold (ENIG), immersion silver, and OSP (Organic Solderability Preservatives).
- Solder Mask Application: A solder mask is applied over the entire surface of the PCB, leaving only the areas for soldering exposed. The solder mask provides insulation and protection against environmental factors.
- Silkscreen Printing:Component designators, logos, and other identifying information are printed onto the PCB surface using silkscreen printing. This helps assembly technicians identify components and ensure correct placement.
- Final Inspection and Testing: The fabricated PCB undergoes rigorous inspection and testing to verify dimensional accuracy, electrical connectivity, and overall quality. Various testing methods, including automated optical inspection (AOI) and electrical testing, may be employed to ensure compliance with design specifications.
- Panelization and Separation: Multiple PCBs are often fabricated on a single panel to optimize manufacturing efficiency. After fabrication, the individual PCBs are separated from the panel using methods such as routing, scoring, or laser cutting.
Once the HDI R&D PCBs are fabricated, they are ready for assembly, where electronic components are mounted and soldered onto the board to create functional electronic devices for research and development purposes.
How do you manufacture an HDI R&D PCB?
Manufacturing HDI (High-Density Interconnect) R&D PCBs involves a series of complex steps to create densely packed circuits with high precision. Here’s a detailed overview of the manufacturing process:
- Design Preparation: The process begins with the design phase, where engineers use specialized PCB design software to create the layout of the HDI R&D PCB. This involves defining the layer stackup, placing components, routing traces, and incorporating necessary features such as microvias and buried vias.
- Material Selection: High-performance substrate materials are chosen based on the specific requirements of the HDI R&D PCB, such as dielectric properties, thermal conductivity, and dimensional stability. Common materials include FR-4, BT (bismaleimide triazine), and polyimide.
- Preparation of Substrate: The selected substrate material is cleaned and coated with a thin layer of copper on both sides to create the conductive layers for the PCB.
- Laser Drilling: Precision laser drilling is used to create small-diameter holes called microvias in the substrate. These microvias enable interconnections between different layers of the PCB, allowing for high-density routing.
- Plating Process: The drilled microvias are plated with copper using processes such as electroplating or chemical deposition. This builds up the conductive pathways required for interconnections.
- Circuit Patterning: A photolithography process is used to apply a photoresist layer onto the copper-clad substrate. Circuit patterns are then exposed onto the photoresist using a mask and UV light. After development, the exposed copper is etched away, leaving behind the desired circuit traces.
- Through-Hole Plating: Through-holes and vias are plated with copper to provide electrical conductivity between different layers of the PCB. This may involve electroplating or other plating techniques.
- Surface Finish: Surface finish is applied to the exposed copper traces to protect them from oxidation and facilitate soldering during assembly. Common surface finish options include immersion gold, ENIG (electroless nickel immersion gold), immersion silver, and OSP (Organic Solderability Preservatives).
- Solder Mask Application: A solder mask is applied over the entire surface of the PCB, leaving only the areas for soldering exposed. The solder mask provides insulation and protection against environmental factors.
- Silkscreen Printing: Component designators, logos, and other identifying information are printed onto the PCB surface using silkscreen printing. This helps assembly technicians identify components and ensure correct placement.
- Testing and Inspection: The fabricated HDI R&D PCB undergoes rigorous testing and inspection to verify dimensional accuracy, electrical connectivity, and overall quality. Various testing methods, including automated optical inspection (AOI) and electrical testing, may be employed.
- Panelization and Separation: Multiple PCBs are often fabricated on a single panel to optimize manufacturing efficiency. After fabrication, the individual PCBs are separated from the panel using methods such as routing, scoring, or laser cutting.
Once the HDI R&D PCBs are manufactured, they are ready for assembly, where electronic components are mounted and soldered onto the board to create functional electronic devices for research and development purposes.
How much should an HDI R&D PCB cost?
The cost of manufacturing an HDI (High-Density Interconnect) R&D PCB can vary widely depending on several factors, including the complexity of the design, the number of layers, the materials used, the manufacturing processes involved, and the quantity ordered.
Generally, HDI PCBs tend to be more expensive compared to traditional PCBs due to their intricate designs and specialized fabrication techniques. Here are some factors that can influence the cost:
- Complexity of Design: HDI PCBs often involve intricate routing patterns, fine pitch components, and high-density interconnects, which can increase manufacturing complexity and cost.
- Number of Layers: HDI PCBs typically have multiple layers to accommodate high-density routing. The more layers required, the higher the manufacturing cost.
- Materials: High-performance substrate materials and advanced surface finishes may be more expensive than standard materials, contributing to higher overall costs.
- Manufacturing Processes:Specialized processes such as laser drilling, sequential lamination, and controlled impedance routing may be necessary for HDI PCB fabrication, adding to the manufacturing cost.
- Quantity: Ordering larger quantities of HDI PCBs can often result in lower unit costs due to economies of scale. However, prototypes or small batch runs may incur higher costs per unit.
- Lead Time: Shorter lead times may incur expedited manufacturing charges, while longer lead times can sometimes result in cost savings.
To get an accurate cost estimate for an HDI R&D PCB, it’s best to consult with a PCB manufacturer and provide them with detailed specifications of the design, including layer count, dimensions, materials, surface finish, and any special requirements. The manufacturer can then provide a customized quote based on these specifications and the desired quantity. Additionally, comparing quotes from multiple manufacturers can help ensure competitive pricing.
What is the HDI R&D PCB base material?
The base material for HDI (High-Density Interconnect) R&D PCBs can vary depending on the specific requirements of the application and the desired performance characteristics. However, several common substrate materials are frequently used in the fabrication of HDI PCBs:
- FR-4:FR-4 (Flame Retardant 4) is one of the most widely used substrate materials for PCBs due to its affordability, good electrical insulation properties, and mechanical strength. It consists of a woven fiberglass cloth impregnated with an epoxy resin.
- BT (Bismaleimide Triazine): BT is a high-performance thermoset polymer material known for its excellent thermal stability, low dielectric constant, and good mechanical properties. It is often chosen for applications requiring high-speed and high-frequency performance.
- Polyimide: Polyimide substrates offer exceptional heat resistance, chemical resistance, and dimensional stability, making them suitable for harsh environments and high-temperature applications. They are commonly used in flexible PCBs and applications where space constraints are critical.
- Rogers Materials: Rogers Corporation produces a range of high-frequency laminate materials tailored for RF and microwave applications. These materials offer low loss tangent, tight dielectric constant control, and excellent high-frequency performance, making them ideal for HDI PCBs in communication and aerospace systems.
- Teflon (PTFE): Teflon-based materials provide excellent electrical properties, including low dielectric constant and low dissipation factor, making them suitable for high-frequency and microwave applications. They are often used in RF and microwave PCBs.
- Metal Core: Metal core substrates feature a layer of metal (such as aluminum or copper) sandwiched between insulating layers. These substrates offer efficient heat dissipation and thermal management, making them suitable for power electronics and LED applications.
The choice of base material depends on various factors, including electrical performance requirements, thermal management considerations, mechanical properties, cost constraints, and the specific needs of the application. Designers often select a substrate material that strikes the right balance between performance, reliability, and cost for their HDI R&D PCBs.
Which company manufactures HDI R&D PCBs?
Many companies manufacture HDI R&D PCBs, with some well-known manufacturers including Foxconn, O-LEADING, Epson, and Hitachi Chemical. These companies possess advanced manufacturing equipment, extensive experience, and professional teams to meet customers’ needs for high-density interconnect R&D PCBs.
As a company specializing in the field of electronics manufacturing, we are also capable of producing HDI R&D PCBs. Equipped with advanced PCB manufacturing equipment and technology, we can realize complex circuit designs and meet precise process requirements. Our team consists of experienced engineers and technicians who can provide comprehensive technical support and solutions to customers.
We prioritize quality control and customer satisfaction, adhering to strict quality management systems throughout the production process to ensure that each PCB meets customers’ requirements and standards. We also offer flexible customization services, tailoring various types of HDI R&D PCBs to customers’ needs, including different layers, materials, and surface treatments.
Whether it’s individual developers, startups, or large enterprises, we can provide high-quality HDI R&D PCB manufacturing services to help them realize innovative electronic product designs and R&D. We are committed to establishing long-term and stable partnerships with customers to jointly promote the development and progress of the electronics industry.
What are the 7 qualities of good customer service?
Good customer service is characterized by several key qualities that ensure customers feel valued, satisfied, and supported. Here are seven qualities of good customer service:
- Responsiveness: Good customer service involves being prompt and responsive to customers’ inquiries, concerns, and needs. This means acknowledging customer inquiries quickly, providing timely assistance, and resolving issues promptly.
- Empathy: Empathy is essential in understanding and acknowledging customers’ feelings, concerns, and perspectives. Good customer service representatives demonstrate empathy by actively listening to customers, showing compassion, and expressing understanding of their situations.
- Clear Communication: Effective communication is crucial in providing good customer service. Clear communication involves conveying information accurately, using language that customers can understand, and ensuring that messages are conveyed comprehensively and transparently.
- Product Knowledge: Good customer service representatives have a deep understanding of the products or services they are supporting. They can answer customers’ questions, provide relevant information, and offer expert advice to help customers make informed decisions.
- Problem-Solving Skills: Good customer service involves effectively addressing customers’ issues and resolving problems to their satisfaction. This requires problem-solving skills, critical thinking, and the ability to find creative solutions to challenges that customers may encounter.
- Professionalism: Professionalism encompasses aspects such as courtesy, respect, integrity, and reliability. Good customer service representatives conduct themselves professionally at all times, maintaining a positive attitude, upholding ethical standards, and treating customers with dignity and respect.
- Follow-Up and Feedback: Good customer service extends beyond resolving immediate issues—it involves following up with customers to ensure their needs have been met and seeking feedback to continuously improve service quality. This demonstrates a commitment to customer satisfaction and ongoing improvement.
By embodying these qualities, businesses can cultivate strong relationships with their customers, foster loyalty, and differentiate themselves in the marketplace through exceptional customer service.
FAQs
What is an HDI R&D PCB?
HDI R&D PCB stands for High-Density Interconnect Research and Development Printed Circuit Board. It’s a specialized type of PCB used in the research, development, and prototyping of high-density interconnect technologies.
What are the advantages of HDI R&D PCBs?
HDI R&D PCBs offer several advantages, including higher component density, improved signal integrity, reduced size and weight, enhanced thermal performance, and increased reliability. They are ideal for applications where space is limited and performance is critical.
What are the key features of HDI R&D PCBs?
Key features of HDI R&D PCBs include microvias, blind vias, buried vias, fine pitch components, multiple layers, controlled impedance, and advanced surface finishes. These features enable high-density routing and facilitate miniaturization without compromising performance.
What industries use HDI R&D PCBs?
HDI R&D PCBs are used in various industries, including telecommunications, consumer electronics, automotive, aerospace, medical devices, and industrial automation. They are particularly prevalent in applications such as smartphones, tablets, wearables, IoT devices, and high-speed data transmission systems.
What are some design considerations for HDI R&D PCBs?
Design considerations for HDI R&D PCBs include layer stackup, via types and placement, minimum feature size, signal integrity, thermal management, component placement, design for manufacturing (DFM), and design for test (DFT). Attention to these factors ensures optimal performance and manufacturability.
How are HDI R&D PCBs manufactured?
The manufacturing process for HDI R&D PCBs involves several steps, including substrate preparation, layer alignment and lamination, drilling, copper plating, circuit patterning, surface finish, solder mask application, silkscreen printing, final inspection, and panelization. Specialized techniques such as laser drilling and sequential lamination are often used to achieve high-density interconnects.
What are the cost factors for HDI R&D PCBs?
The cost of HDI R&D PCBs depends on factors such as complexity of design, number of layers, materials used, manufacturing processes, quantity ordered, lead time, and additional services required. Generally, HDI PCBs tend to be more expensive than traditional PCBs due to their intricate designs and specialized fabrication techniques.