High layer package substrate supplier. We have produced 20 layer FCBGA substrate with microtrace/Spacing 10um/10um. Use the Showa Denko and Ajinomoto(ABF) base materials.
In the dynamic realm of electronic engineering, the substrate design within laminate packages stands as a pivotal element, intricately woven into the fabric of device functionality. A laminate package’s substrate serves as the bedrock, the foundation upon which the intricate dance of signals and components orchestrates. It is the silent force that propels technological innovations into reality.
Brief Overview of Substrate Design in Laminate Packages
Laminate packages, in their essence, rely on substrates as the structural backbone. These substrates, typically composed of materials like fiberglass-reinforced epoxy, are the canvases upon which electronic connections are meticulously crafted. As electronic devices continue to shrink in size while escalating in complexity, the demand for substrates that can accommodate this intricate dance of electrons becomes increasingly paramount.
The substrate design, in the context of laminate packages, involves not just a mere physical scaffold but a sophisticated architecture. It encompasses the arrangement of conductive pathways, the integration of components, and the optimization of spatial configurations to ensure seamless connectivity. From the traditional rigid substrates to the advent of flexible alternatives, the evolution in substrate design mirrors the ever-accelerating pace of technological advancement.
Importance of Innovative Technologies in Advancing Substrate Design
Innovation stands as the driving force behind the evolution of substrate design. It is the spark that ignites novel solutions, pushing the boundaries of what substrates can achieve. In a landscape where miniaturization is not just a preference but a necessity, innovative technologies emerge as the guiding light.
The integration of technologies such as 3D-Molded Interconnect Device (MID) and embedded passive components signifies a paradigm shift in substrate design. These advancements go beyond traditional approaches, unlocking new dimensions of efficiency, space utilization, and overall performance. High-Density Interconnects (HDI) and flexible substrates further accentuate this trend, heralding an era where substrates not only support but actively contribute to the technological prowess of electronic devices.
As we delve deeper into this exploration of substrate design, it becomes evident that the marriage of tradition and innovation is the catalyst for progress. The importance of embracing cutting-edge technologies in substrate design cannot be overstated, for it is through this fusion that the foundation of electronic marvels is laid, shaping the future of laminate packages and the devices they power.
Emerging Technologies in Substrate Design
3D-Molded Interconnect Device (MID) Technology
1.Explanation of MID Technology
Innovative Integration: MID involves the integration of electronic circuitry directly into three-dimensional molded structures, pushing the boundaries of traditional two-dimensional substrate design.
Material Composition: MID utilizes specialized materials, such as molded thermoplastics or thermosetting polymers, that allow for the creation of intricate circuit patterns within the substrate.
2.Applications in Laminate Package Substrates
Miniaturization: MID technology enables the creation of compact and highly integrated circuits, addressing the demand for smaller form factors in laminate packages.
Enhanced Signal Integrity: The three-dimensional nature of MID reduces signal interference and enhances signal integrity, crucial for high-performance applications.
Diverse Industry Adoption: MID finds applications in various industries, from consumer electronics to automotive, showcasing its versatility in different laminate package substrates.
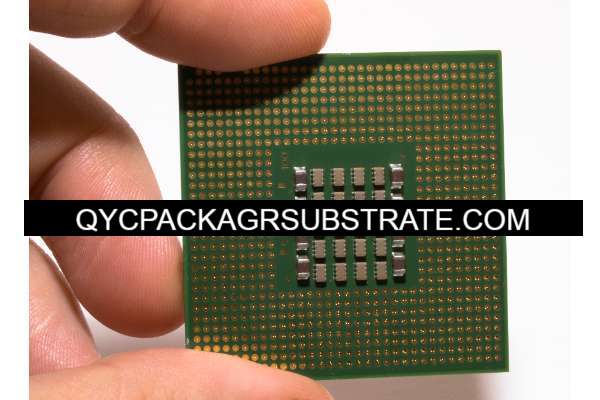
Embedded Passive Components
1.Integration of Passive Components into Substrate
Space-Efficient Design: Embedding passive components, such as resistors and capacitors, directly into the substrate eliminates the need for discrete components, optimizing space utilization.
Improved Signal Paths: Placing passive components close to active components on the substrate reduces signal path lengths, minimizing signal loss and improving overall performance.
2.Benefits in Terms of Space Efficiency and Performance
Reduced Footprint: Integration of passive components within the substrate reduces the physical footprint of the laminate package, contributing to the ongoing trend of miniaturization.
Enhanced Reliability: With fewer external components, the reliability of the overall system improves, as there are fewer points of potential failure.
Thermal Performance: Embedded passive components can contribute to better thermal management, dispersing heat more efficiently due to their proximity to active components.
By delving into 3D-Molded Interconnect Device (MID) Technology and the integration of Embedded Passive Components, substrate design not only evolves to meet the demands of miniaturization but also addresses key performance factors in laminate packages. These technologies represent a paradigm shift in the way electronic components are incorporated into substrates, offering new possibilities for space-efficient and high-performance designs.
Trends Shaping the Future of Substrate Design
In the ever-evolving landscape of laminate package substrates, the following trends stand out as pivotal contributors to future advancements.
High-Density Interconnects (HDI)
1.Overview of HDI Technology
High-Density Interconnects (HDI) represent a revolutionary leap in substrate design. Unlike traditional PCBs, HDI focuses on packing more functionality into a smaller space, optimizing the interconnection density. This is achieved through advanced manufacturing techniques that allow for finer lines and spaces, as well as multiple layers in a compact form.
The technology involves microvias, blind vias, and buried vias, enabling a three-dimensional interconnection architecture. By reducing the size of vias and increasing the number of layers, HDI brings about a significant boost in electrical performance and signal integrity.
2.How HDI Addresses Miniaturization and Enhanced Performance
HDI technology directly addresses the industry’s demand for miniaturization without compromising performance. As electronic devices continue to shrink in size, conventional PCBs face limitations in accommodating the necessary components. HDI, however, excels in space efficiency, allowing for the integration of complex circuits in smaller areas.
The increased interconnect density not only supports miniaturization but also enhances electrical performance. Shorter interconnection paths reduce signal propagation delays, improving the overall speed and reliability of the electronic system. This makes HDI an ideal solution for applications where both size and performance are critical, such as high-performance computing, mobile devices, and IoT sensors.
Flexible Substrates
1.Introduction to Flexible Substrate Materials
Flexible substrates represent a paradigm shift in the world of laminate packages. These substrates are made from materials that can bend and conform to different shapes without compromising their functionality. Polyimide and polyester are common materials used in flexible substrates due to their excellent mechanical flexibility and thermal stability.
The manufacturing process involves roll-to-roll production, allowing for the creation of continuous and flexible sheets. This flexibility opens up new design possibilities, enabling the integration of electronics into unconventional form factors.
2.Applications in Wearables and Other Flexible Electronics
Flexible substrates find notable applications in the field of wearables and flexible electronics, showcasing their remarkable adaptability to the human body’s contours. This unique characteristic positions them as ideal components for innovative devices such as smartwatches, fitness trackers, and healthcare sensors. Beyond wearable technology, flexible substrates play a pivotal role in advancing the design landscape of smartphones and portable electronic devices by enabling the development of foldable and rollable displays. This transformative capability contributes to reshaping the form and functionality of modern electronic devices. This groundbreaking feature is fundamentally transforming the design landscape of smartphones and portable electronic devices, heralding a new era characterized by flexibility and innovation.
Beyond consumer electronics, flexible substrates find applications in automotive interiors, medical devices, and even in the aerospace industry, where lightweight and bendable electronics are crucial. The trend towards flexibility not only enhances the aesthetics of electronic devices but also introduces new possibilities for innovative product designs.
Sustainability in Substrate Manufacturing
In an era where environmental consciousness is paramount, the substrate manufacturing industry is undergoing a transformative shift towards sustainability. This section delves into the sustainable practices, emphasizing the adoption of “Green Substrates” and the principles of recycling and circular design.
Green Substrates
1.Environmentally Friendly Materials:
As technology advances, so does our responsibility to minimize ecological footprints. The integration of eco-friendly materials in substrate manufacturing is a key trend. These materials, often derived from renewable sources, contribute to the reduction of environmental impact throughout the production process.
2.Impact on the Overall Lifecycle:
The choice of green substrates goes beyond mere environmental goodwill; it directly influences the entire lifecycle of laminate packages. From raw material extraction to manufacturing, distribution, and end-of-life disposal, using sustainable materials positively affects each stage. Reduced energy consumption and lower emissions further enhance the overall environmental profile of laminate packages.
Recycling and Circular Design
1.Strategies for Substrate Recycling:
Recycling is at the forefront of sustainable substrate design. Manufacturers are implementing innovative strategies to facilitate the recycling of laminate packages. This includes the development of technologies that allow for the efficient separation and recovery of materials from used substrates. By incorporating recyclable components, the industry aims to create a closed-loop system, minimizing waste and conserving resources.
2.Embracing a Circular Economy:
Moving beyond traditional linear manufacturing models, the substrate industry is embracing a circular economy approach. This involves designing substrates with recyclability in mind and fostering the development of systems that encourage the return and reuse of end-of-life substrates. The circular economy not only reduces the environmental impact but also creates economic opportunities by reintroducing materials into the production cycle.
Green substrates, recycling, and circular design are not just buzzwords; they represent a paradigm shift towards a more sustainable and responsible future for substrate manufacturing. By adopting these practices, the industry not only meets the demands of the present but also ensures a resilient and environmentally sound foundation for the technologies of tomorrow.
Case Studies: Successful Implementation of New Substrate Technologies
Real-world examples of companies adopting innovative substrate designs
1.Company X: Pioneering 3D-MID Technology
Overview of Company X’s adoption of 3D-MID technology in laminate packages.
Key features of their innovative substrate design incorporating 3D-MID.
Utilization of advanced materials and manufacturing processes.
2.Company Y: Revolutionizing with Embedded Passive Components
How Company Y strategically integrated embedded passive components into their substrates.
Discuss the specific applications within their product lines.
Insights into the design flexibility and performance enhancements achieved.
Performance improvements and business impact
1.Enhanced Performance Metrics
Examination of improved electrical performance, signal integrity, and thermal management achieved through the new substrate technologies.
Comparative analysis with traditional substrate designs, showcasing notable advancements.
2.Operational Efficiency and Cost Savings
Evaluation of how the innovative substrate designs contributed to streamlined manufacturing processes.
Cost-effectiveness in terms of materials, production time, and overall operational efficiency.
3.Market Competitiveness and Customer Satisfaction
Exploration of how these companies gained a competitive edge in the market.
Customer feedback and market response to products featuring the new substrate technologies.
4.Business Expansion and Collaborations
Examination of any new market opportunities or partnerships resulting from the adoption of innovative substrates.
Impact on the company’s overall business strategy and market positioning.
5.Sustainability Impact
Discussion on how these companies’ substrate innovations contributed to sustainability goals.
Any certifications or recognitions received for environmentally conscious substrate design.
6.ROI and Long-term Benefits
Analysis of the return on investment (ROI) associated with implementing new substrate technologies.
Discussion on the long-term benefits, including potential for scalability and adaptability.
By delving into these real-world case studies, we gain valuable insights into how companies have successfully integrated innovative substrate designs, experiencing tangible improvements in performance metrics, operational efficiency, and overall business impact. These examples serve as compelling evidence for the transformative potential of advanced substrate technologies in the electronics industry.