High multilayer package substrate manufacturer. the Package Substrate will be made with Showa Denko and Ajinomoto High speed materials.or other types high speed materials and high frequency materials.
In the fast-paced world of electronics, staying at the cutting edge is essential. A critical element in this race is the 4-layer package substrate. These substrates are the unsung heroes that support and connect vital electronic components within devices, from your smartphone to your laptop and beyond.
Overview of 4-Layer Package Substrates
So, what exactly are 4-layer package substrates? These substrates are specialized circuit boards, designed with four layers, each serving a unique purpose. They act as the structural backbone, facilitating the connection of microchips, ensuring efficient heat dissipation, and enabling the seamless flow of electrical signals. With the rapid miniaturization and complexity of electronic devices, the demand for these substrates has soared.
Importance of Semiconductor Substrates in Electronics
Semiconductor substrates are the unsung heroes of modern electronics. The significance of semiconductor substrates lies in their pivotal role as a bridge connecting the intricate realm of microelectronics to the everyday functionality of macroscopic devices. These substrates not only establish a robust foundation for delicate electronic components but also serve as essential conduits for effective heat management and electrical connectivity.
It’s undeniable that the choice of semiconductor substrate exerts a profound influence on the performance, durability, and reliability of electronic devices. Consequently, the selection of the appropriate substrate material becomes a paramount consideration for engineers and manufacturers striving to meet the escalating consumer demands for faster, more powerful, and energy-efficient devices. In the subsequent sections, we will venture deeper into the domain of semiconductor substrates and investigate the prevalent semiconductor materials commonly employed in 4-layer package substrates.
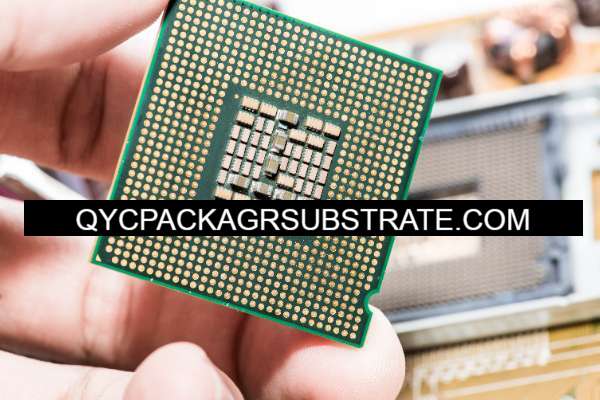
Understanding Semiconductor Substrates
Role of Substrates in Electronic Packaging
In the realm of electronic packaging, substrates play a pivotal role as the foundation upon which various components and microelectronics are mounted. They serve as the crucial interface that connects semiconductor devices to the larger electronic systems. Substrates facilitate electrical connections, heat dissipation, and structural support. Essentially, they are the unsung heroes that enable the seamless integration and functionality of electronic devices.
Key Characteristics of an Ideal Semiconductor
Substrate When it comes to selecting the right semiconductor substrate for electronic packaging, certain key characteristics are indispensable. These attributes are vital for ensuring the optimal performance and longevity of electronic components.
Thermal Conductivity
Thermal conductivity stands as a fundamental property that plays a pivotal role in determining a substrate’s ability to efficiently disperse heat generated during the operation of semiconductor devices. Effective heat dissipation is of utmost importance to prevent overheating, a condition that could adversely affect the performance and reliability of electronic components. Substrates boasting high thermal conductivity, like silicon carbide (SiC) and aluminum nitride (AlN), are the favored choice for applications where adept heat management is a top priority.
Electrical Insulation
Electrical insulation is another crucial attribute of a semiconductor substrate.Effective insulation on the substrate serves as a safeguard against electrical interference among the various electronic components. This insulation is crucial in preventing short circuits and maintaining the device’s stability.Substrates often use materials like ceramics, glass, or specific polymers to provide this electrical insulation.
Material Compatibility
Material compatibility is essential to ensure that the chosen substrate can harmoniously coexist with other components in the electronic system. Compatibility extends to factors such as coefficient of thermal expansion (CTE) and the ability to bond securely with semiconductor materials. Mismatches in material properties can lead to mechanical stress, cracking, or delamination, which can compromise the reliability of the entire system.
Common Materials Used for Semiconductor Substrates
Semiconductor substrates can be fashioned from a diverse range of materials, each possessing its unique advantages and constraints.Commonly used materials include:
Silicon (Si): Silicon wafers are widely used as substrates, especially in microelectronics. They offer good electrical properties and are compatible with semiconductor fabrication processes.
Silicon Carbide (SiC): SiC substrates are known for their high thermal conductivity, making them suitable for high-power electronic devices and applications that require robust thermal management.
Gallium Arsenide (GaAs): GaAs substrates are favored in optoelectronic applications and high-frequency devices due to their superior electronic properties.
Aluminum Nitride (AlN): AlN substrates excel in high-power and high-frequency applications, thanks to their combination of electrical insulation and excellent thermal conductivity.
Ceramic Materials: Various ceramic materials, like alumina (Al2O3), are used in semiconductor substrates due to their insulating properties and compatibility with microelectronics.
Selecting the right semiconductor substrate depends on the specific requirements of the electronic system, with careful consideration of thermal, electrical, and material compatibility characteristics.
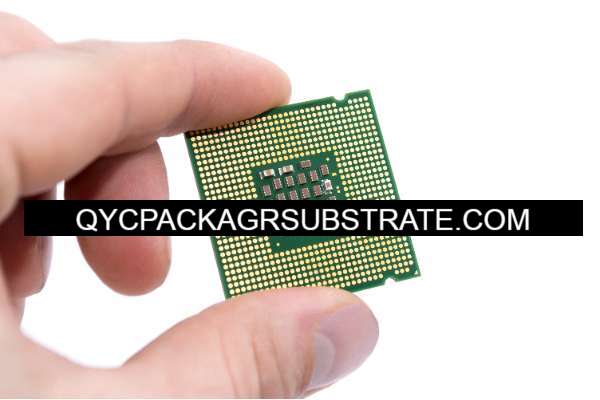
4-Layer Package Substrate
What is a 4-Layer Package Substrate?
Within the field of electronic packaging, a 4-layer package substrate holds immense significance as it serves as the fundamental platform for the installation and interconnection of semiconductor devices, integrated circuits, and other electronic elements. This intricate, multi-layered board plays a central role in enabling the smooth transmission of electrical signals and the efficient dissipation of heat within electronic systems. The term “4-layer” signifies that it comprises four discrete layers, each endowed with its distinct attributes and purposes.
The layers in a 4-layer package substrate typically include the signal and power layers, dielectric layers, and sometimes a ground plane. These layers are carefully designed and stacked to provide the required electrical connectivity while ensuring thermal management, signal integrity, and reliability. The dielectric layers insulate the conductive traces, preventing unintended electrical interactions and minimizing signal noise. This design ensures efficient and reliable electronic performance.
Advantages of Using 4-Layer Substrates
4-layer package substrates offer several advantages that make them a preferred choice in modern electronics:
High-Density Integration: 4-layer substrates facilitate the seamless integration of components at higher densities, empowering designers to condense more functionality into a reduced footprint. This capability aligns with the prevailing industry trend of downsizing electronic devices, enhancing their portability and efficiency.
Enhanced Signal Integrity: By employing dedicated signal layers and precise routing, 4-layer substrates elevate signal integrity, mitigating the potential for interference, crosstalk, and other electrical anomalies. This improvement ensures the robust and reliable performance of electronic systems.This is essential for maintaining the reliability and performance of electronic systems.
Enhanced Thermal Management: The presence of multiple layers enables efficient heat dissipation. Critical in high-performance electronic systems, where excessive heat can lead to operational failures and shorten component lifespans. Ensuring Reliability and Durability: The multi-layer structure imparts structural integrity, enhancing resilience against mechanical stress and environmental influences. This results in improved durability and long-term reliability.
Design Flexibility: Designers have more flexibility in creating complex, multi-functional electronic systems due to the versatility offered by 4-layer substrates. This adaptability is invaluable when developing cutting-edge technology.
Typical Applications of 4-Layer
Substrates 4-layer package substrates find applications across various industries, including but not limited to:
Consumer Electronics: Smartphones, tablets, and laptops utilize 4-layer substrates to accommodate the increasing number of components in a compact form factor.
Telecommunications: High-speed communication equipment such as routers, switches, and base stations rely on 4-layer substrates for their data processing capabilities and signal integrity.
Automotive Electronics: Modern vehicles incorporate advanced electronics, and 4-layer substrates are used to support various control and safety systems
Industrial Control: Industrial automation, robotics, and control systems make use of 4-layer substrates to ensure precision and reliability in manufacturing processes.
Medical Devices: Diagnostic and treatment equipment in the medical field employ 4-layer substrates to achieve compact designs and high performance.
Aerospace and Defense: , 4-layer substrates are indispensable components used in avionics, radar systems, and military-grade electronics. These substrates are chosen for their exceptional reliability, efficient thermal management, and robust signal integrity, which are crucial in demanding and harsh operational environments.
In essence, 4-layer package substrates stand as essential building blocks in contemporary electronics. They serve as a robust foundation for high-performance electronic systems, spanning a diverse spectrum of industries. Their unmatched benefits in terms of seamless integration, reliable signal transmission, and effective heat dissipation make them a pivotal element in the design and production of cutting-edge electronic devices.
The Most Commonly Used Semiconductor in 4-Layer Substrates
Introduction to Common Semiconductors
Within the domain of 4-layer package substrates, a range of semiconductor materials are carefully evaluated for their distinctive attributes and suitability. These semiconductors wield a pivotal influence over the performance and functionality of electronic devices. Among the most frequently employed semiconductor materials are silicon (Si), gallium arsenide (GaAs), and silicon carbide (SiC). Each of these materials boasts unique properties that render them apt for specific applications.
Why One Semiconductor Stands
Out Among these common semiconductor materials, silicon (Si) emerges as the most frequently chosen substrate in 4-layer package substrates. Silicon is preferred for several compelling reasons. Firstly, it offers excellent thermal conductivity, ensuring efficient heat dissipation. This aspect is of utmost importance in electronic devices, particularly those characterized by high power densities, as it serves to mitigate overheating issues and significantly prolong the lifespan of key components.
Furthermore, silicon demonstrates excellent electrical insulating properties, mitigating the likelihood of short circuits and electrical interference.This property is crucial for maintaining signal integrity in complex electronic systems.
Furthermore, silicon enjoys a significant advantage due to its abundant availability, cost-effectiveness, and established track record within the electronics industry. These attributes make silicon an easily accessible and favored option for production, further reinforcing its prominence as a preferred material of choice.
Benefits and Drawbacks of the Chosen
Semiconductor Silicon’s popularity is not without its drawbacks. Although silicon excels in several aspects, it may not be the optimal choice for every application. Silicon offers several advantages as a semiconductor in 4-layer substrates, including:
High Thermal Conductivity: Silicon’s remarkable thermal conductivity ensures efficient heat dissipation, which is essential for preventing electronic devices from overheating.
Electrical Insulation: Silicon possesses strong electrical insulation properties, reducing the risk of electrical interference and thereby enhancing signal integrity.
Abundance and Cost-Effectiveness: The widespread availability and cost-effectiveness of silicon make it a pragmatic choice for manufacturers seeking cost-efficient solutions.
Nonetheless, it is crucial to acknowledge the limitations associated with silicon as well:
Limited Operating Temperatures: Silicon’s performance may degrade at extremely high temperatures, limiting its suitability for certain applications.
Brittle Nature: Silicon can be brittle, which might lead to mechanical fragility in some cases.
Specialized Applications: In scenarios where exceptional performance is required in harsh conditions, alternatives such as gallium arsenide or silicon carbide might be better suited.
In summary, the selection of semiconductor material for 4-layer package substrates is a pivotal decision. Silicon stands as the prevailing choice due to its distinctive blend of properties. Nevertheless, it is crucial to take into account the specific needs of the application and environmental factors when determining the most suitable semiconductor for a given project.
Manufacturing and Production
How 4-Layer Package Substrates are Manufactured
4-layer package substrates play a crucial role in modern electronics, serving as the foundation for semiconductor components. The manufacturing process involves several key steps that ensure the substrate’s quality and performance. Here’s a brief overview of how 4-layer package substrates are produced:
Material Selection: The choice of the semiconductor material is critical. It needs to possess high thermal conductivity, excellent electrical insulation properties, and compatibility with the specific application. Common materials include silicon, gallium nitride (GaN), and silicon carbide (SiC).
Layer Formation: The substrate is built up layer by layer through a series of deposition processes. This involves growing or depositing the chosen semiconductor material onto a base layer. Each layer’s thickness and composition are precisely controlled to meet the substrate’s specifications.
Etching and Pattern Transfer: Etching techniques are used to create intricate patterns and circuit traces on the substrate. These patterns define the pathways for electrical connections and signal routing. Precise lithography and etching processes are employed to achieve this.
Dielectric Layers: Dielectric layers, typically made of materials like silicon dioxide or silicon nitride, are deposited to insulate different layers and prevent electrical interference. These layers ensure that the substrate functions efficiently and reliably.
Bonding and Packaging: Once the substrate’s layers are complete, it may be bonded to other semiconductor components or devices as part of the overall packaging process. This step involves precise alignment and bonding techniques to ensure the proper functioning of the final electronic assembly.
Quality Control and Testing
Ensuring the quality and reliability of 4-layer package substrates is paramount in the semiconductor industry. Rigorous quality control and testing procedures are implemented at various stages of manufacturing. These procedures include:
Visual Inspection: Visual checks are conducted to identify any surface defects, contamination, or irregularities in the substrate’s layers. Any anomalies are flagged for further investigation.
Electrical Testing: Electrical tests are performed to verify the substrate’s electrical properties, including its insulation, conductivity, and signal integrity. This ensures that the substrate meets the required specifications.
Thermal Testing: As thermal conductivity is a critical factor in substrates, thermal testing is indispensable for evaluating their heat dissipation efficiency, particularly in applications with high power demands.
Reliability Testing: Substrates undergo rigorous reliability assessments, including accelerated life tests and stress tests. These evaluations aim to ascertain the substrate’s sustained performance and reliability across diverse operational conditions.
Environmental Testing: Substrate assessment encompasses environmental tests that gauge their performance across a spectrum of conditions. These conditions encompass temperature extremes, humidity levels, and exposure to various chemical environments.
Industry Standards and Certifications
To meet the demands of the electronics industry, 4-layer package substrates must adhere to recognized industry standards and certifications. Compliance with these standards ensures product quality and reliability. Some key industry standards and certifications include:
IPC Standards: The Association Connecting Electronics Industries (IPC) provides standards and guidelines for the design, manufacture, and testing of electronic products, including substrates.
ISO Certification: Many manufacturers adhere to ISO 9001 for quality management systems and ISO 14001 for environmental management systems to ensure consistent quality and responsible production practices.
UL Certification: Underwriters Laboratories (UL) certification is often sought for electrical safety and performance, indicating that the substrate meets specific safety and quality standards.
Ensuring RoHS Compliance: Adhering to the Restriction of Hazardous Substances (RoHS) directive is imperative in guaranteeing that substrates are void of harmful materials. This commitment, combined with meticulous manufacturing protocols, comprehensive quality assessments, and alignment with industry benchmarks, empowers manufacturers to deliver top-notch 4-layer package substrates that align with the continually expanding needs of the semiconductor sector.