High precision packaging substrate Manufacturer. we can produce the best samllest bump pitch with 100um, the best smallest trace are 9um. and the smallest gap are 9um. most of the design are 15um to 30um trace and spacing.
A high-precision packaging substrate is a specialized material vital for assembling and packaging electronic components, especially integrated circuits (ICs) and semiconductor devices. These substrates undergo meticulous engineering to ensure they have precise dimensions and properties, which are critical for achieving optimal performance and reliability in packaged electronic devices.
These substrates are characterized by their strict adherence to dimensional accuracy, crafted with tight tolerances to enable precise alignment and connection of electronic components. They are typically fashioned from advanced materials like ceramics or specialized polymers, chosen for their ability to maintain excellent dimensional stability across varying environmental conditions, including fluctuations in temperature and humidity.
Moreover, precision substrates excel in handling intricate pitch configurations, enabling the seamless integration of closely arranged electronic components in modern microelectronics. They are equipped with thermal management capabilities, including heat spreaders and thermal vias, which efficiently disperse heat produced by electronic components. This enhances overall reliability while minimizing the possibility of overheating issues.
These substrates are renowned for their excellent signal integrity, engineered to reduce signal distortion and interference, thus guaranteeing reliable data and electrical signal transmission within electronic devices. Their manufacturing employs cutting-edge techniques like precision machining, laser drilling, and microfabrication to achieve the necessary accuracy and high quality.
High-precision packaging substrates are crucial for enhancing the efficiency, dependability, and downsizing of electronic devices. They are tailored to meet the needs of applications requiring small sizes, fast data transfer, and strict reliability criteria.
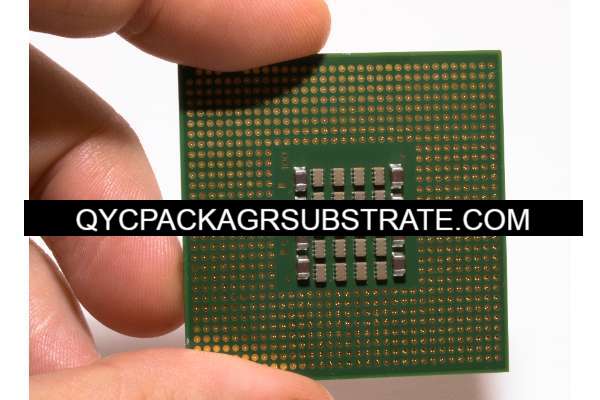
What Functions Does a High-Precision Packaging Substrate Serve?
A precise packaging substrate plays a pivotal role in the assembly and packaging of electronic devices. particularly integrated circuits (ICs) and semiconductor devices. Its functions are diverse:
Precise Alignment and Connection: These substrates ensure precise alignment and connection of electronic components, facilitating accurate assembly and dependable electrical connections.
Dimensional Stability: Crafted with meticulous precision, high-precision substrates maintain consistent dimensions and tolerances even amidst environmental variations, guarding against component distortion or misalignment.
By integrating thermal management elements such as thermal vias and heat spreaders, these substrates effectively disperse heat produced by electronic components. This process prevents excessive heat buildup, thereby maintaining consistent and dependable operation.
Maintaining Signal Integrity: Utilizing high-precision substrates reduces signal distortion and interference, ensuring the dependable transmission of electrical signals among integrated circuits and other components. This practice safeguards data integrity and optimizes system performance.
These substrates support compact configurations, facilitating the seamless integration of densely packed electronic components in modern microelectronics applications. This feature is crucial for achieving sleek form factors and high-density packaging.
Employing meticulous manufacturing techniques and premium materials, high-precision substrates notably enhance the reliability and longevity of electronic devices. This diminishes the likelihood of mechanical failures and electrical malfunctions, ensuring sustained performance over an extended lifespan.
Precise packaging substrates play a crucial role in enhancing the efficiency, dependability, and downsizing of electronic devices. They offer a steady, thermally adept, and electrically trustworthy base for assembling and packaging electronic parts, fulfilling the demanding criteria of modern electronics applications.
What are the Manufacturing Technologies for High-Precision Packaging Substrates?
Producing precise packaging substrates necessitates a coordinated blend of cutting-edge manufacturing technologies, with each component playing a pivotal role in meeting the stringent standards demanded by industries like semiconductor manufacturing, microelectronics, MEMS, and optoelectronics.
Photolithography functions as the craftsman’s tool, meticulously transferring intricate designs from photomasks onto light-sensitive chemical layers, laying the groundwork for semiconductor manufacturing and the creation of high-precision substrates.
Etching: Employing surgical precision, etching methods, whether wet or dry, intricately remove material from substrates, crafting detailed patterns with accuracy at the micron level.
Chemical Vapor Deposition (CVD): Like a chemist’s potion, CVD meticulously deposits thin films onto substrates from volatile precursor materials, allowing craftsmen to control material thickness and composition with surgical precision, crucial for applications such as silicon dioxide and metallic layers.
Physical Vapor Deposition (PVD) techniques resemble the precise strokes of an artist’s brush, delicately applying thin films through physical mechanisms. These processes grant artisans meticulous command over the thickness and consistency of the deposited layers.
Utilizing the concentrated energy of focused light, laser micromachining allows for the meticulous shaping of materials at a micro-scale. This advanced technique empowers artisans to create intricate features and patterns vital for the production of high-precision substrates.
Electroplating: Like a metallurgical alchemist, electroplating deposits metallic layers onto substrates, enabling craftsmen to forge intricate conductive traces and interconnects crucial for substrate functionality.
Chemical Mechanical Polishing (CMP): With the finesse of a master craftsman, CMP refines substrate surfaces, marrying chemical reactions with mechanical abrasion to achieve unparalleled uniformity and flatness.
Microfabrication Techniques: These techniques, akin to miniature sculpting, delicately mold micro-scale features and structures on substrates, embodying precision and intricacy in every detail.
Innovative additive manufacturing methods empower artisans to materialize digital designs with unparalleled precision and adaptability, revolutionizing substrate fabrication.
Metrology and inspection systems play a critical role as the vigilant guardians of quality control in manufacturing. They utilize optical microscopy and scanning electron microscopy (SEM) to meticulously assess dimensional accuracy and substrate integrity in every manufactured product.
By harmonizing these diverse manufacturing techniques, craftsmen breathe life into high-precision packaging substrates, imbuing them with the resilience and performance demanded by the most exacting of applications and industries.
How Do High-Precision Packaging Substrates Differ from Conventional PCBs?
High-precision packaging substrates deviate significantly from conventional printed circuit boards (PCBs) in several pivotal aspects:
Dimensional Precision: High-precision substrates are intricately crafted with exceedingly tight tolerances and precise dimensions, ensuring flawless alignment and seamless connectivity of electronic components. In contrast, conventional PCBs may exhibit looser tolerances and less stringent dimensional requirements.
Material Selection: High-precision substrates often leverage advanced materials like ceramics or specialized polymers acclaimed for their exceptional dimensional stability and superior thermal properties. Conversely, conventional PCBs typically rely on more commonplace materials such as fiberglass.
Fine Pitch Capability: High-precision substrates excel at accommodating fine pitch configurations, enabling the integration of densely packed electronic components with minimal spacing. This capability outmatches conventional PCBs, which may encounter difficulties with finer pitches and component density.
Thermal Management: High-precision substrates prioritize effective thermal regulation by incorporating sophisticated features like thermal vias and heat spreaders to efficiently dissipate heat. While conventional PCBs also address thermal concerns, their solutions may be simpler or prioritize other design considerations.
Signal Integrity: High-precision substrates are engineered to minimize signal distortion and interference, ensuring reliable transmission of data and electrical signals within the device. While conventional PCBs also tackle signal integrity, high-precision substrates may employ more advanced techniques to achieve superior signal fidelity.
Manufacturing Techniques: The fabrication of high-precision substrates entails advanced manufacturing methods such as laser micromachining, precision machining, and microfabrication. These techniques surpass the standard processes used for conventional PCB fabrication in terms of precision and complexity.
In essence, high-precision packaging substrates are meticulously tailored to meet the rigorous demands of modern microelectronics applications, offering unparalleled accuracy, reliability, and performance compared to conventional PCBs.
Are the Importance of High-Precision Packaging Substrate Manufacturers Underestimated?
Manufacturers specializing in high-precision packaging substrates are often underestimated in their significance within the electronics industry. Here’s why their importance may not receive due recognition:
Essential Electronic Infrastructure: High-precision substrates serve as the backbone of electronic devices, spanning from everyday gadgets to complex aerospace systems. Their ability to provide precise alignment and connectivity for intricate components within confined spaces is fundamental. However, the nuanced processes involved in their fabrication might not be widely acknowledged.
Substrate manufacturers serve as essential catalysts for innovation, facilitating the integration of sophisticated components into ever-shrinking devices. Despite their crucial role, the valuable contributions of these manufacturers to technological advancement often go unnoticed.
Manufacturers prioritize maintaining rigorous quality and reliability standards to guarantee the effectiveness and durability of electronic devices. Despite substantial investments in research, development, and quality control, the intricate nature of substrate manufacturing demands specialized expertise and precision, which may sometimes be overlooked.
Producers of high-precision substrates are essential contributors to economic advancement, crucial for job creation, supply chain stability, and innovation stimulation. Despite their pivotal role, their impact on economic progress often goes unrecognized.
Manufacturers in this sector forge tight collaborations with semiconductor firms, device manufacturers, and research institutions to drive innovation. These partnerships serve as catalysts for creativity and tackle evolving challenges in electronics design and manufacturing. Yet, the cooperative essence of their efforts might not always be readily apparent.
In summary, while the significance of high-precision packaging substrate manufacturers may be understated, their indispensable role as enablers of innovation, guardians of quality, economic contributors, and collaborative partners cannot be overstated. Recognizing and acknowledging their contributions is essential for the continued advancement of the electronics industry.
What is the Future Outlook for High-Precision Packaging Substrates?
The future outlook for high-precision packaging substrates is optimistic, fueled by significant advancements across several key areas:
As electronic devices evolve, the demand for highly precise substrates grows to accommodate shrinking designs. These substrates are crucial for enabling the trend towards compact and intricate electronic components. They play a vital role in supporting finer pitches and tighter form factors, which are essential for developing sophisticated electronic devices.
The increasing need for high-frequency applications is being driven by the widespread embrace of fast data transmission and communication technologies such as 5G. This shift highlights the requirement for substrates that can adeptly manage high-frequency signals with precision. Sophisticated materials and designs integrated into advanced packaging substrates will play a crucial role in preserving signal integrity and reducing loss in these applications.
Breakthroughs in materials science are driving significant advancements in high-precision packaging substrates, crucial for next-generation electronic devices. These substrates are benefiting from improved thermal conductivity, electrical performance, and reliability, thanks to innovations in various materials.
Advanced ceramics, metal-matrix composites, and polymer-based nanocomposites are at the forefront of this transformation. They are enabling substrates to meet the ever-growing demands of modern electronic devices by enhancing their capabilities and performance parameters.
The advancement of high-precision packaging substrates enables the smooth incorporation of a variety of components, including sensors, actuators, and microprocessors, into compact and versatile systems. This integration capacity simplifies the connection and fusion of different elements, resulting in improved functionality and performance in electronic devices.
Advancements in 3D integration methods, notably through-silicon via (TSV) technology and stacked die packaging, are increasingly favored for their capacity to boost device performance while shrinking form factors. The integration of multiple layers relies heavily on high-precision packaging substrates, which serve as vital structural supports and facilitate interconnections. These substrates are instrumental in enabling the seamless integration of components, a key driver in the evolution of compact yet powerful electronic devices.
Refinements in manufacturing techniques, like laser micromachining, precision machining, and additive manufacturing, are continually improving high-precision packaging substrates. These advancements allow for the creation of substrates with more complex geometries and features, enhancing flexibility and optimizing performance in electronic device design.
In summary, the future of high-precision packaging substrates looks promising, driven by evolving technology trends and the escalating demand for smaller, faster, and more reliable electronic devices. Continuous innovation in materials, design, and manufacturing processes will ensure that high-precision substrates remain at the forefront of enabling next-generation electronic systems and applications.
Conclusion
In conclusion, high-precision packaging substrates are poised to revolutionize the electronics industry. With ongoing advancements in miniaturization, materials science, and manufacturing processes, these substrates are set to address the evolving demands of next-generation electronic devices.
The increasing need for high-frequency applications, alongside the seamless integration of heterogeneous components and innovations in 3D integration techniques, underscores the pivotal role of high-precision substrates in enabling cutting-edge electronic systems. Furthermore, continuous enhancements in manufacturing processes will ensure that these substrates meet the rigorous standards of modern electronic devices while offering enhanced flexibility and performance optimization.
In essence, the future prospects for high-precision packaging substrates are highly promising. Their capacity to support the development of smaller, faster, and more reliable electronic devices positions them as indispensable drivers of innovation in the electronics industry. As technology continues to progress, high-precision substrates will remain at the forefront, driving transformative advancements in electronic systems and applications.