High Speed package Substrate Manufacturer.High speed and high frequency material packaging substrate manufacturing. Advanced packaging substrate production process and technology
A high-speed packaging substrate is a specialized material essential for electronic packaging, particularly in devices demanding rapid data processing, such as computer processors, graphics cards, and networking hardware. It serves as the fundamental support structure for mounting and connecting various electronic components.
These substrates undergo meticulous engineering to enable high-frequency signal transmission with minimal loss and to ensure dependable electrical connections between components. Employing advanced materials and construction techniques, they are designed to sustain swift data transfer rates, mitigate electromagnetic interference, and uphold signal integrity.
Key attributes of high-speed packaging substrates encompass:
Optimized electrical conductivity to facilitate efficient signal propagation.
Reduced dielectric constant to diminish signal dispersion and uphold signal fidelity.
Controlled impedance to maintain uniform electrical characteristics across the substrate.
Reduced skew and crosstalk to forestall interference among signal paths.
Effective thermal management features to dissipate heat generated during operation.
Support for fine-pitch interconnects, enabling compact component layouts and integration of high-pin-count ICs.
Materials for these substrates vary, encompassing laminates such as FR-4, polyimide, and liquid crystal polymer, alongside specialized options like ceramic substrates and metal-core PCBs (MCPCBs). Advanced manufacturing techniques such as multilayer construction and microvia drilling are commonly employed to achieve desired performance benchmarks.
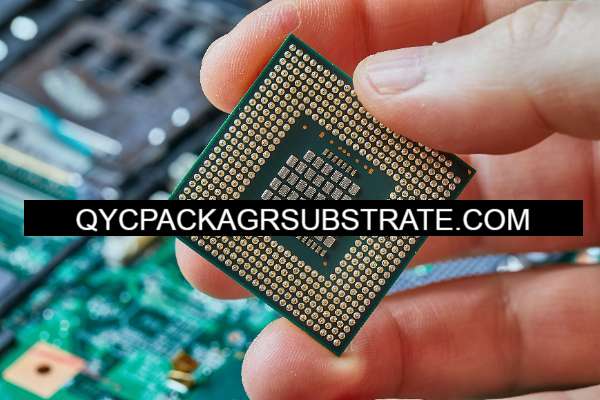
What are the functions of high-speed packaging substrates?
High-speed packaging substrates are vital components in electronic devices, especially those requiring fast data processing and high-frequency signal transmission:
Structural Foundation: These substrates provide a sturdy base for securing electronic components such as integrated circuits (ICs), resistors, capacitors, and connectors. Their robust design ensures device stability and resilience under different mechanical stresses.
Electrical Integration: Facilitating seamless electrical connections among various components, high-speed packaging substrates enable efficient signal and power transmission. Through conductive pathways or traces, they establish reliable electrical pathways crucial for device functionality.
Signal Fidelity: Engineered to minimize signal degradation, these substrates offer low-impedance pathways for high-frequency signals, preserving signal integrity and minimizing distortions. This ensures accurate data transmission, particularly vital for demanding applications.
Efficient Thermal Management: Incorporating features for effective heat dissipation, such as thermal vias or heat dissipation layers, these substrates prevent component overheating and maintain stable device performance.
Space Optimization: Supporting compact designs, high-speed packaging substrates enable the integration of fine-pitch interconnects and densely packed layouts, maximizing component density within limited space.
Environmental Protection: Additionally, these substrates shield electronic components from environmental factors like moisture, dust, and contaminants, safeguarding them from potential damage and extending device lifespan.
In summary, high-speed packaging substrates play a pivotal role in enhancing the performance, reliability, and functionality of electronic devices across various industries, including computing, telecommunications, and automotive sectors.
What role do high-speed packaging substrate manufacturers play?
High-speed packaging substrate manufacturers are integral to the electronics industry, essential for device assembly and functionality. Their core functions include:
Advancing Research and Development (R&D) to innovate materials, technologies, and manufacturing processes for high-speed substrates, focusing on performance enhancement and cost efficiency.
Providing tailored Design and Engineering Support, optimizing substrate designs for signal integrity, thermal management, and mechanical performance.
Managing Manufacturing and Production in specialized facilities, ensuring consistent, high-quality substrates meeting industry standards and customer specifications.
Enforcing stringent Quality Assurance and Testing procedures to validate product performance and reliability across electrical, thermal, mechanical, and reliability metrics.
Streamlining Supply Chain Management to source raw materials, components, and equipment efficiently, ensuring timely availability and optimized logistics.
Delivering comprehensive Technical Support and Customer Service, guiding product selection, integration, and troubleshooting for successful substrate implementation.
In summary, high-speed packaging substrate manufacturers drive innovation, enable technological advancements, and support electronic device development across diverse industries.
What are the differences between high-speed packaging substrates and traditional PCBs?
High-speed packaging substrates and traditional PCBs exhibit differences across various domains:
Material Composition:
High-speed packaging substrates rely on advanced materials tailored for swift signal transmission, such as those with low dielectric constant and low loss tangent. Conversely, traditional PCBs may utilize standard materials like fiberglass or epoxy resin, lacking specific optimizations for high-speed performance.
Signal Integrity:
High-speed packaging substrates prioritize maintaining signal integrity and minimizing distortion, particularly at high frequencies. They incorporate features like controlled impedance traces and differential pairs for reliable signal transmission. In contrast, traditional PCBs may not emphasize signal integrity to the same degree.
Layer Stackup:
High-speed packaging substrates often boast more intricate layer configurations compared to traditional PCBs. Additional signal and ground layers, along with specific arrangements to mitigate electromagnetic interference and crosstalk, are common. Traditional PCBs may have simpler layer structures.
Manufacturing Process:
High-speed packaging substrates necessitate advanced manufacturing techniques for precise signal routing and tight tolerances. Specialized processes such as laser drilling, sequential lamination, and controlled impedance testing are typical. Traditional PCBs may undergo more conventional manufacturing methods.
Applications:
High-speed packaging substrates are predominantly utilized in applications where speed, reliability, and signal integrity are paramount, such as high-speed data transmission and telecommunications. Conversely, traditional PCBs find application in a broader spectrum of industries, ranging from consumer electronics to automotive, where high-speed performance may not be as critical.
In essence, high-speed packaging substrates are engineered to meet the rigorous demands of rapid signal transmission, while traditional PCBs cater to a diverse range of applications with varying performance requirements.
What are the main structures and production technologies of high-speed packaging substrates?
The development and fabrication of high-speed packaging substrates involve intricate procedures and specialized techniques:
Structural Design:
High-speed packaging substrates are meticulously engineered with multiple layers, including signal, ground, and power planes, aimed at enhancing signal fidelity and mitigating electromagnetic interference.
Incorporating controlled impedance traces is pivotal to ensure consistent signal transmission and minimal distortion, essential for maintaining reliable signal propagation.
Employing differential pairing enables pairs of traces to carry equal but opposite signals, enhancing noise immunity and preserving signal integrity, particularly critical in high-speed applications.
Microvias, small apertures drilled into the substrate, facilitate interconnections between layers, enabling efficient trace routing and minimizing signal propagation delays.
Manufacturing Processes:
Precision laser drilling is utilized to create microvias with exceptional accuracy, ensuring precise interconnections between layers.
Sequential layer bonding through lamination enables the creation of intricate multilayer structures with precise alignment and impedance control.
Copper plating and etching methods are employed to form conductive traces, depositing copper onto the substrate and selectively etching it to create desired trace patterns, including controlled impedance traces and differential pairs.
Advanced dielectric materials, such as low-loss laminates and high-frequency ceramics, are applied to enhance signal integrity and minimize signal attenuation at high frequencies, ensuring optimal performance in high-speed applications.
In summary, high-speed packaging substrates rely on sophisticated design features and manufacturing processes to optimize signal transmission, minimize distortion, and ensure reliability in high-speed environments.
Frequently Asked Questions (FAQs):
What defines high-speed packaging substrates?
High-speed packaging substrates are specialized materials essential for transmitting high-frequency signals in electronic packaging. They ensure signal integrity and minimize interference.
What are the primary characteristics of high-speed packaging substrates?
These substrates typically feature controlled impedance traces, differential signaling capabilities, microvia interconnects, and advanced dielectric materials, all crucial for high-frequency applications.
What are the manufacturing methods for high-speed packaging substrates?
Manufacturing processes usually involve precision laser drilling, sequential layer bonding, copper plating and etching, and the use of advanced dielectric materials to ensure optimal performance.
What factors should be considered when selecting high-speed packaging substrates?
Material properties, signal frequency requirements, impedance matching, thermal management capabilities, and reliability considerations are vital factors in substrate selection.
How do high-speed packaging substrates differ from traditional PCBs?
High-speed packaging substrates are specifically designed and manufactured for high-frequency applications, featuring controlled impedance traces, differential signaling, and advanced materials, unlike traditional PCBs.
Conclusion
In summary, high-speed packaging substrates are vital components for transmitting high-frequency signals with optimal integrity and minimal interference. They serve diverse industries including telecommunications, automotive, aerospace, consumer electronics, and medical devices where rapid signal transmission is imperative. Engineered with specialized features like controlled impedance traces, differential signaling, and advanced dielectric materials, these substrates meet stringent requirements of high-speed electronic systems. Manufacturing employs precision techniques such as laser drilling, sequential layer bonding, and copper plating to ensure impeccable performance. Overall, high-speed packaging substrates offer superior signal integrity, reduced distortion, enhanced noise immunity, and dependable operation in high-speed applications.