Hybrid Layer Buildup Rogers 4350B/FR4 PCB Manufacturer
Hybrid Layer Buildup Rogers 4350B/FR4 PCB Manufacturer,Hybrid Layer Buildup Rogers 4350B/FR4 PCBs integrate the exceptional electrical properties of Rogers 4350B with the structural support and cost-effectiveness of FR4. This hybrid construction ensures high-frequency signal integrity while optimizing manufacturing costs. Ideal for applications demanding precision and reliability, such as RF/microwave circuits and high-speed digital designs, these PCBs offer a balanced solution for performance-driven projects. With careful design considerations and adherence to industry standards, Hybrid Layer Buildup Rogers 4350B/FR4 PCBs deliver superior signal transmission, mechanical stability, and cost-efficiency.
What is a Hybrid Layer Buildup Rogers 4350B/FR4 PCB?
A Hybrid Layer Buildup PCB, such as Rogers 4350B/FR4, combines multiple layers of different materials to achieve specific performance characteristics. Rogers 4350B is a high-frequency laminate material known for its excellent electrical properties, low loss tangent, and stable dielectric constant across a wide range of frequencies. FR4, on the other hand, is a standard PCB material known for its mechanical strength and cost-effectiveness.
In a Hybrid Layer Buildup PCB, layers of Rogers 4350B may be used for high-frequency signal transmission and to maintain signal integrity, while FR4 layers may be used for structural support and to reduce costs. This combination allows for the optimization of electrical performance where needed while keeping the overall cost of the PCB reasonable.
The specific configuration of the layers in a Hybrid Layer Buildup PCB depends on the requirements of the application, such as signal frequency, power handling, thermal management, and cost constraints. This type of PCB construction is common in applications such as high-speed digital communications, RF/microwave circuits, and other high-frequency applications where both electrical performance and mechanical reliability are crucial.
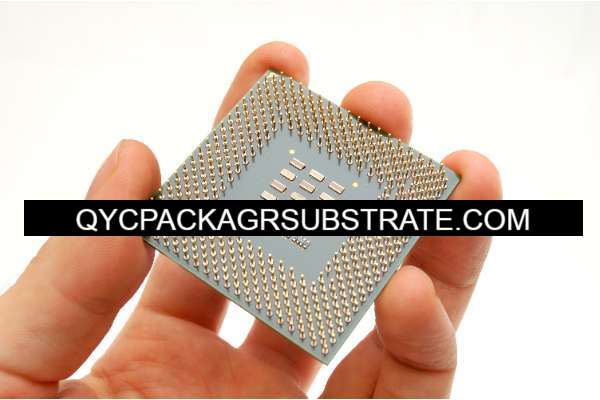
Hybrid Layer Buildup Rogers 4350B/FR4 PCB Manufacturer
What are the Hybrid Layer Buildup Rogers 4350B/FR4 PCB Design Guidelines?
Designing a Hybrid Layer Buildup PCB using Rogers 4350B and FR4 materials involves considering several guidelines to ensure optimal performance and reliability. Here are some key design guidelines:
- Layer Stackup: Plan the layer stackup carefully, placing Rogers 4350B layers where high-frequency signals will propagate to maintain signal integrity. FR4 layers can be used for structural support and cost reduction. The exact configuration will depend on the specific requirements of your design.
- Impedance Control:Ensure proper impedance matching for high-speed signals by designing controlled impedance traces on Rogers 4350B layers. Tools like impedance calculators or PCB layout software can help you determine the correct trace widths and layer configurations.
- Signal Integrity: Minimize signal distortion and crosstalk by carefully routing high-speed traces on Rogers 4350B layers. Use techniques such as differential pair routing, signal shielding, and ground stitching vias to maintain signal integrity.
- Power and Ground Planes: Design robust power and ground planes using both Rogers 4350B and FR4 layers. Proper grounding is critical for noise reduction and signal integrity. Avoid splitting ground planes unnecessarily and use multiple vias for connections between layers.
- Thermal Management: Consider thermal management requirements, especially if the design involves high-power components or operates in elevated temperatures. Ensure adequate copper pour and vias for heat dissipation, and place sensitive components away from heat sources.
- Manufacturability: Work closely with your PCB manufacturer to ensure the design is manufacturable. Consider factors such as minimum trace widths and spacing, drill sizes, and material availability. Provide clear documentation and communicate any special requirements for the hybrid layer buildup process.
- Testing and Validation: Plan for testing and validation of the PCB design to ensure it meets performance requirements. Use simulation tools to predict signal behavior and validate the design before fabrication. Perform signal integrity analysis, impedance testing, and thermal analysis as needed.
- Cost Considerations: Balance performance requirements with cost considerations. While Rogers 4350B offers excellent electrical properties, it’s typically more expensive than FR4. Optimize the layer stackup and material usage to achieve the desired performance at a reasonable cost.
By following these guidelines and working closely with your PCB manufacturer, you can design a Hybrid Layer Buildup PCB using Rogers 4350B and FR4 materials that meets your performance, reliability, and cost objectives.
What is the Hybrid Layer Buildup Rogers 4350B/FR4 PCB Fabrication Process?
The fabrication process for a Hybrid Layer Buildup PCB using Rogers 4350B and FR4 materials involves several steps. Here’s a general overview of the process:
- Design Preparation: Begin by creating the PCB layout design using appropriate PCB design software. Define the layer stackup, impedance requirements, trace routing, component placement, and other design parameters according to your specific requirements.
- Material Selection: Select the appropriate thicknesses and quantities of Rogers 4350B and FR4 laminate materials based on the design specifications. Ensure that the materials meet the required electrical, mechanical, and thermal properties.
- Preparation of Substrates: Cut the Rogers 4350B and FR4 laminates into the desired panel sizes according to the PCB layout. Clean the substrate surfaces to remove any contaminants that could affect adhesion during lamination.
- Inner Layer Processing: Begin the inner layer processing by etching copper traces and vias onto the substrate surfaces according to the PCB design. Use processes such as photolithography and chemical etching to create the desired circuit patterns.
- Layer Lamination:Alternate layers of Rogers 4350B and FR4 substrates are stacked together, along with pre-impregnated (prepreg) layers of epoxy resin, forming a multi-layered PCB panel. Apply heat and pressure to the panel using a lamination press to bond the layers together into a solid composite structure.
- Drilling: Drill holes for vias and through-hole components using a CNC drilling machine. Ensure precise alignment of the drill holes with the PCB layout design to maintain accuracy.
- Plating and Copper Deposition: Plate the inner layer copper traces and vias with additional copper to ensure proper conductivity. Use processes such as electroplating to deposit copper onto the exposed surfaces of the PCB panel.
- Outer Layer Processing: Apply solder mask and silkscreen layers to the outer surfaces of the PCB panel. The solder mask provides insulation and protection for the copper traces, while the silkscreen layer adds component markings and identifiers.
- Final Inspection and Testing: Inspect the completed PCB panel for defects such as shorts, open circuits, and dimensional inaccuracies. Perform electrical testing, including continuity checks, impedance measurements, and insulation resistance tests, to verify the functionality and reliability of the PCB.
- Routing and Separation: Use a CNC routing machine to cut the individual PCBs from the panel along the defined board outlines. Remove any excess material and smooth the edges of the PCBs as needed.
- Surface Finishing: Apply surface finishes such as HASL (Hot Air Solder Leveling), ENIG (Electroless Nickel Immersion Gold), or OSP (Organic Solderability Preservatives) to protect the exposed copper surfaces and facilitate soldering during assembly.
- Final Inspection and Packaging: Perform a final inspection of the finished PCBs to ensure they meet quality standards and specifications. Package the PCBs according to customer requirements, ready for shipment or further assembly processes.
By following these steps carefully and adhering to industry standards and best practices, you can successfully fabricate Hybrid Layer Buildup PCBs using Rogers 4350B and FR4 materials.
How do you manufacture a Hybrid Layer Buildup Rogers 4350B/FR4 PCB?
Manufacturing a Hybrid Layer Buildup PCB using Rogers 4350B and FR4 materials involves a combination of processes for preparing and assembling the different layers. Here’s an overview of the manufacturing process:
- Design Preparation:Begin by creating the PCB layout design using appropriate PCB design software. Define the layer stackup, impedance requirements, trace routing, component placement, and other design parameters according to your specific requirements.
- Material Selection: Select the appropriate thicknesses and quantities of Rogers 4350B and FR4 laminate materials based on the design specifications. Ensure that the materials meet the required electrical, mechanical, and thermal properties.
- Preparation of Substrates: Cut the Rogers 4350B and FR4 laminates into the desired panel sizes according to the PCB layout. Clean the substrate surfaces to remove any contaminants that could affect adhesion during lamination.
- Inner Layer Processing: Begin the inner layer processing by etching copper traces and vias onto the substrate surfaces according to the PCB design. Use processes such as photolithography and chemical etching to create the desired circuit patterns.
- Layer Lamination:Alternate layers of Rogers 4350B and FR4 substrates are stacked together, along with pre-impregnated (prepreg) layers of epoxy resin, forming a multi-layered PCB panel. Apply heat and pressure to the panel using a lamination press to bond the layers together into a solid composite structure.
- Drilling: Drill holes for vias and through-hole components using a CNC drilling machine. Ensure precise alignment of the drill holes with the PCB layout design to maintain accuracy.
- Plating and Copper Deposition: Plate the inner layer copper traces and vias with additional copper to ensure proper conductivity. Use processes such as electroplating to deposit copper onto the exposed surfaces of the PCB panel.
- Outer Layer Processing: Apply solder mask and silkscreen layers to the outer surfaces of the PCB panel. The solder mask provides insulation and protection for the copper traces, while the silkscreen layer adds component markings and identifiers.
- Final Inspection and Testing: Inspect the completed PCB panel for defects such as shorts, open circuits, and dimensional inaccuracies. Perform electrical testing, including continuity checks, impedance measurements, and insulation resistance tests, to verify the functionality and reliability of the PCB.
- Routing and Separation: Use a CNC routing machine to cut the individual PCBs from the panel along the defined board outlines. Remove any excess material and smooth the edges of the PCBs as needed.
- Surface Finishing: Apply surface finishes such as HASL (Hot Air Solder Leveling), ENIG (Electroless Nickel Immersion Gold), or OSP (Organic Solderability Preservatives) to protect the exposed copper surfaces and facilitate soldering during assembly.
- Final Inspection and Packaging: Perform a final inspection of the finished PCBs to ensure they meet quality standards and specifications. Package the PCBs according to customer requirements, ready for shipment or further assembly processes.
By following these steps carefully and adhering to industry standards and best practices, you can successfully manufacture Hybrid Layer Buildup PCBs using Rogers 4350B and FR4 materials.
How much should a Hybrid Layer Buildup Rogers 4350B/FR4 PCB cost?
The cost of a Hybrid Layer Buildup PCB using Rogers 4350B and FR4 materials can vary significantly depending on several factors:
- PCB Size and Complexity: Larger PCBs with more complex designs require more materials and manufacturing time, leading to higher costs.
- Layer Count: The number of layers in the PCB stackup affects the manufacturing process complexity and material requirements, thus impacting the cost.
- Material Costs: Rogers 4350B is typically more expensive than FR4, so the proportion of Rogers 4350B layers in the stackup influences the overall cost.
- Fabrication Process: Specialized processes, such as controlled impedance routing or sequential lamination, may incur additional costs.
- Surface Finish and Special Features: The choice of surface finish (e.g., HASL, ENIG, OSP) and any special features like gold plating or edge connectors can add to the cost.
- Manufacturing Volume: Larger production volumes often lead to economies of scale, reducing the cost per unit.
- Lead Time: Expedited production schedules may come with higher costs compared to standard lead times.
- Supplier and Location: PCB manufacturing costs can vary based on the supplier and their location, as well as factors like shipping and import/export fees.
To get an accurate cost estimate for a specific Hybrid Layer Buildup Rogers 4350B/FR4 PCB, it’s best to consult with PCB manufacturers or suppliers. They can provide quotes based on your design specifications and manufacturing requirements. Additionally, online PCB cost calculators can offer rough estimates based on factors like size, layer count, and material choices.
What is the Hybrid Layer Buildup Rogers 4350B/FR4 PCB base material?
The base materials used in a Hybrid Layer Buildup PCB consisting of Rogers 4350B and FR4 typically include:
- Rogers 4350B:This is a high-frequency laminate material known for its excellent electrical properties, low loss tangent, and stable dielectric constant across a wide range of frequencies. It’s often used for high-frequency signal transmission and maintaining signal integrity in RF/microwave circuits and other high-speed applications.
- FR4 (Flame Retardant 4): FR4 is a standard PCB material made from woven fiberglass cloth impregnated with epoxy resin. It’s known for its mechanical strength, thermal stability, and cost-effectiveness. FR4 is commonly used for structural support and as a substrate for mounting components in PCBs.
In a Hybrid Layer Buildup PCB, these two materials are combined to leverage the benefits of each. Rogers 4350B layers are typically used where high-frequency performance is critical, while FR4 layers are used for structural support and to reduce costs. The specific configuration of the layers depends on the requirements of the application and the desired balance between performance, reliability, and cost.
Which company makes Hybrid Layer Buildup Rogers 4350B/FR4 PCB?
Currently, there are many companies that provide Hybrid Layer Buildup Rogers 4350B/FR4 PCBs, including large electronic corporations specializing in high-performance PCB manufacturing and professional PCB manufacturers. These companies have extensive experience and technological expertise in producing high-frequency circuits and RF/microwave applications.
Our company is one of them. We specialize in the design and manufacture of high-performance PCBs, equipped with advanced production equipment and a skilled technical team. We can provide customized solutions for Hybrid Layer Buildup Rogers 4350B/FR4 PCBs according to customer requirements.
Our manufacturing process strictly adheres to international standards and employs advanced technology and quality control measures to ensure product quality and reliability. With a professional engineering team and technical staff, we offer technical support and tailored solutions to our customers.
In addition to manufacturing high-performance PCBs, we are committed to establishing long-term partnerships with our customers by providing timely communication and excellent services to meet their evolving needs. Our goal is to deliver high-quality, high-performance PCB products and become a trusted and dependable partner for our customers.
If you have any requirements or inquiries regarding Hybrid Layer Buildup Rogers 4350B/FR4 PCBs, please feel free to contact us. We are dedicated to providing the best solutions and services to meet your needs.
What are the 7 qualities of good customer service?
Good customer service is characterized by several key qualities that contribute to a positive experience for customers. Here are seven qualities:
- Responsiveness: Responding promptly to customer inquiries, requests, and concerns demonstrates attentiveness and a commitment to addressing their needs in a timely manner. Whether it’s answering a phone call, replying to an email, or assisting customers in person, being responsive shows that you value their time and prioritize their satisfaction.
- Empathy: Empathy involves understanding and acknowledging the customer’s feelings, perspectives, and situations. It means putting yourself in their shoes to comprehend their concerns and providing support or solutions that are empathetic and considerate of their emotions.
- Clear Communication:Effective communication is essential for conveying information clearly and concisely, ensuring that customers understand the assistance or guidance provided. This includes using plain language, active listening, and avoiding jargon or technical terms that may confuse customers.
- Problem-Solving Skills: Good customer service involves the ability to resolve issues and address challenges effectively. Customer service representatives should be equipped with problem-solving skills to identify root causes, propose viable solutions, and follow through to ensure customer satisfaction.
- Professionalism: Professionalism encompasses aspects such as politeness, respectfulness, and maintaining a positive attitude when interacting with customers. It involves representing the company in a professional manner, regardless of the circumstances, and upholding the organization’s values and standards.
- Consistency: Consistency in customer service ensures that customers receive a uniform level of service quality across various interactions and touchpoints with the company. Consistency builds trust and reliability, fostering long-term relationships with customers and enhancing their overall experience.
- Adaptability: Customer service representatives should demonstrate adaptability by being flexible and resourceful in addressing diverse customer needs and situations. This includes adapting communication styles, problem-solving approaches, and service delivery methods to accommodate different preferences and circumstances.
By embodying these qualities, businesses can cultivate a customer-centric culture and deliver exceptional customer service that exceeds expectations, fosters loyalty, and contributes to long-term success.
FAQs
What is a Hybrid Layer Buildup Rogers 4350B/FR4 PCB?
A Hybrid Layer Buildup PCB combines layers of Rogers 4350B and FR4 materials to leverage the high-frequency performance of Rogers 4350B and the cost-effectiveness of FR4. It’s commonly used in high-frequency applications where signal integrity is critical.
What are the advantages of using Rogers 4350B/FR4 hybrid construction?
The combination of Rogers 4350B and FR4 materials allows for optimized electrical performance where needed while reducing costs compared to using Rogers 4350B exclusively. It offers good signal integrity, mechanical stability, and cost-effectiveness.
What applications are suitable for Hybrid Layer Buildup Rogers 4350B/FR4 PCBs?
These PCBs are suitable for high-frequency applications such as RF/microwave circuits, wireless communication systems, radar systems, high-speed digital designs, and other applications requiring controlled impedance and signal integrity.
How do I determine the appropriate layer stackup for my design?
The layer stackup depends on factors such as signal frequency, impedance requirements, power handling, and thermal considerations. Consult with a PCB designer or manufacturer to determine the optimal stackup for your specific requirements.
What are the design guidelines for Hybrid Layer Buildup Rogers 4350B/FR4 PCBs?
Design guidelines include considerations for impedance control, signal integrity, power and ground planes, thermal management, manufacturability, and testing/validation. Adhering to these guidelines ensures optimal performance and reliability.
Is it more expensive to manufacture Hybrid Layer Buildup Rogers 4350B/FR4 PCBs compared to other types?
While Rogers 4350B is more expensive than FR4, the hybrid construction can offer cost savings compared to using Rogers 4350B exclusively. The overall cost depends on factors such as material usage, layer count, and manufacturing processes.
Where can I get Hybrid Layer Buildup Rogers 4350B/FR4 PCBs manufactured?
Many PCB manufacturers offer fabrication services for Hybrid Layer Buildup PCBs. Look for companies with experience in high-frequency PCB manufacturing and inquire about their capabilities and expertise in producing Rogers 4350B/FR4 hybrids.