What is IC Substrate?
IC Substrate and package substrate manufacturer. We use advanced Msap and Sap technology, BT Base, Rogers base, Showa Denko and ABF Ajinomoto base materials to produce the IC/BGA substrates.
An IC (Integrated Circuit) substrate, often referred to as a chip carrier or package substrate, is a critical component in the assembly and packaging of integrated circuits. It serves as the fundamental platform for mounting and connecting integrated circuits, playing a crucial role in providing structural support, electrical connectivity, and thermal management for intricate electronic components.
Here’s how an IC substrate contributes to these aspects:
Structural Support:
IC substrates provide a robust physical foundation for mounting and securing the integrated circuit. They help protect the fragile silicon die (the actual IC) from mechanical stress, environmental factors, and handling during manufacturing, testing, and use.
The substrate also acts as a base for attaching other components and interconnecting various parts of the integrated circuit assembly.
Electrical Connectivity:
The IC substrate contains a network of conductive traces (usually made of copper) that connect the input and output pads of the integrated circuit to the external pins or solder balls. These traces form the electrical pathways that allow signals to flow between the IC and the rest of the electronic system.
The substrate may also incorporate additional features such as vias (plated holes) to create multi-layered structures, facilitating complex interconnections.
Thermal Management:
Efficient thermal management is crucial for the reliable operation and longevity of integrated circuits. The IC substrate often includes a thermal pad or heat spreader to help dissipate heat generated by the IC during operation.
Some substrates are designed with specific features like thermal vias, which are holes filled with thermally conductive material that extends from the top to the bottom layers. These vias help to efficiently transfer heat away from the IC to the external environment.
In advanced packaging technologies, such as flip-chip packaging, the IC may be directly attached to the substrate, allowing for better thermal performance as the heat is more effectively conducted through the substrate.
The IC substrate plays a crucial role in integrating semiconductor devices into electronic systems by offering essential physical, electrical, and thermal support. Advancements in technology drive the continual evolution of IC substrate design and materials to meet rising demands for performance, miniaturization, and reliability in electronic devices.
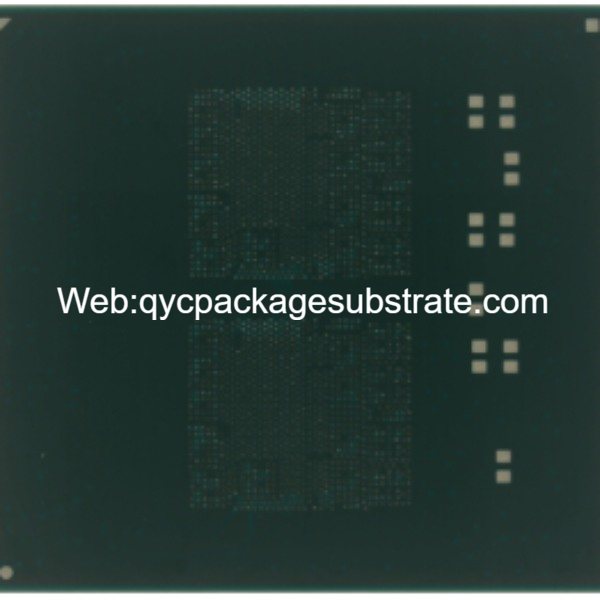
What are the Functions of BGA Substrate?
Beyond providing structural support, the IC substrate serves several additional functions that contribute to the overall performance, reliability, and connectivity of integrated circuits (ICs). Here are some key functions:
Electrical Connections:
IC substrates feature a network of conductive traces that establish electrical connections between the integrated circuit and the printed circuit board (PCB). These traces route signals, power, and ground connections, ensuring seamless communication between the IC and other components in the electronic system.
Signal Integrity and High-Speed Performance:
The design of the IC substrate, including the arrangement of traces and the use of advanced materials, plays a crucial role in maintaining signal integrity. This is particularly important for high-speed applications where signal distortion and noise can impact performance. Controlled impedance and signal routing on the substrate contribute to reliable data transmission.
Power Distribution:
IC substrates distribute power from the PCB to the integrated circuit, ensuring that the IC receives the required voltage and current for proper operation. Efficient power distribution is essential for the reliable functioning of electronic devices.
Thermal Management:
Efficient heat dissipation is critical for the reliable performance and longevity of integrated circuits. IC substrates are designed to facilitate the transfer of heat away from the IC. This may involve the use of thermal pads, heat spreaders, or thermal vias that help dissipate heat to the surrounding environment or to additional heat sink structures.
Miniaturization and Package Integration:
IC substrates contribute to the miniaturization of electronic devices by providing a compact platform for mounting and connecting ICs. Advanced packaging technologies, such as system-in-package (SiP) and multi-chip modules, leverage IC substrates to integrate multiple components into a single, space-efficient package.
Mechanical Stability and Reliability:
IC substrates enhance the mechanical stability of the overall electronic assembly, protecting the IC from mechanical stresses during manufacturing, assembly, and operation. This contributes to the overall reliability of electronic devices in various environmental conditions.
Customization and Compatibility:
IC substrates can be customized to accommodate specific requirements of different ICs and applications. They are designed to be compatible with various semiconductor technologies, allowing for flexibility in the integration of diverse ICs into electronic systems.
In summary, the IC substrate serves a multifaceted role beyond structural support, encompassing electrical connectivity, signal integrity, power distribution, thermal management, miniaturization, mechanical stability, and customization. Its design and features are crucial for enhancing the overall reliability and performance of integrated circuits in diverse electronic applications.
What are the Types of IC/BGA Substrate?
IC substrates, essential components in electronic packaging, come in diverse types, each tailored to meet specific application demands. These types include organic substrates, ceramic substrates, and laminate substrates, each offering unique characteristics:
Organic Substrates:
Material: Comprising organic materials like fiberglass-reinforced epoxy resins or polymers.
Characteristics:
Lightweight: Ideal for applications prioritizing weight considerations.
Cost-Effective: Economical choice, often selected for cost-sensitive consumer electronics.
Good Electrical Insulation: Provides effective electrical insulation, crucial for maintaining signal integrity.
Ceramic Substrates:
Material: Crafted from ceramics like alumina or aluminum nitride.
Characteristics:
High Thermal Conductivity: Known for excellent heat dissipation, crucial in applications requiring efficient thermal management.
Mechanical Strength: Offers robust mechanical strength and durability, safeguarding the integrated circuit.
High Temperature Tolerance: Withstands elevated temperatures, suitable for applications demanding temperature stability.
Laminate Substrates:
Material: Composed of multiple layers with varied materials, often blending organic and inorganic elements.
Characteristics:
Versatility: Balances features of organic and ceramic substrates, providing adaptability for diverse applications.
Customization: Allows tailored compositions to meet specific design requirements, offering flexibility.
Moderate Thermal Performance: Typically exhibits moderate thermal performance, falling between organic and ceramic substrates.
Application-specific considerations guide the selection of substrate types:
Consumer Electronics: Organic substrates are prevalent due to their lightweight nature and cost-effectiveness.
High-Performance Computing: Ceramic substrates find use where efficient thermal management is paramount.
Telecommunications and Automotive: Laminate substrates, versatile and customizable, are often favored in these applications.
As electronic devices evolve, the demand for characteristics like miniaturization, thermal performance, and cost-effectiveness propels the ongoing development and adoption of diverse IC substrate types to meet varied and evolving needs.
How does BGA/IC Substrate Differ from PCB?
IC substrates and traditional printed circuit boards (PCBs) are distinct components in electronic systems, each playing a crucial role. Here are the key differences between IC substrates and PCBs in terms of their roles and structures:
Roles:
IC Substrate:
The primary role of an IC substrate is to provide a platform for mounting and connecting integrated circuits (ICs).
It offers structural support, electrical connectivity, and thermal management specifically for the integrated circuits.
IC substrates are crucial for the integration and packaging of ICs, ensuring their proper functioning within electronic devices.
PCB:
A PCB serves as the main board or foundation for an entire electronic system.
It serves as a foundation for securing a variety of electronic elements, encompassing ICs, resistors, capacitors, and additional devices.
The PCB acts as a central nexus for electrical connections, overseeing the intricate network of signal routing and power distribution among various components throughout the entire electronic device.
Structures:
IC Substrate:
IC substrates are more specialized and often smaller in size compared to PCBs. They are designed specifically to accommodate and support individual or multiple integrated circuits.
The structure of an IC substrate includes features like conductive traces, vias, and thermal management elements tailored to the needs of the integrated circuits it houses.
IC substrates may use materials like organic substrates, ceramics, or laminates, depending on the application and performance requirements.
PCB:
PCBs are typically larger and more generalized in structure compared to IC substrates. They house a variety of components and are designed to support the entire electronic system.
A PCB’s composition comprises numerous layers of conductive traces and insulating materials. Additionally, it integrates elements like solder mask, silkscreen, and plated through-holes to facilitate the mounting of components.
PCBs can utilize diverse materials, with FR-4 being a common choice. FR-4 is a type of epoxy reinforced with fiberglass, selected to achieve a well-balanced combination of cost-effectiveness, performance, and reliability throughout the entirety of the electronic device.
Contributions to Functionality:
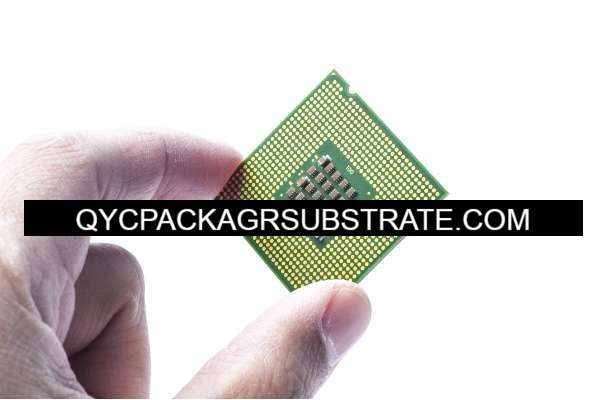
IC Substrate:
IC substrates contribute directly to the functionality of integrated circuits. They enable the connection of ICs to the larger electronic system, providing essential electrical pathways and ensuring proper thermal management.
The design of IC substrates influences the performance, reliability, and miniaturization of electronic devices.
PCB:
PCBs play a foundational role in the overall functionality of electronic devices.They serve as a foundation for integrating and interconnecting diverse components, such as ICs, to establish a unified and operational system.
The PCB design directly influences the system’s overall performance, the integrity of signals, and its capability to meet the specific requirements of the electronic device.
In summary, IC substrates are specialized components focused on supporting and connecting integrated circuits, while PCBs serve as the central platform for the entire electronic system. Both components work together to ensure the functionality, reliability, and performance of electronic devices.
What is the Structure and Production Technologies of FCBGA Substrate?
Structure of IC Substrate:
The structure of an IC substrate is composed of several layers and components designed to provide a robust foundation for mounting and connecting integrated circuits. While variations exist based on the type and design, a typical IC substrate comprises the following elements:
Substrate Material:
The foundational layer of the IC substrate, known as the base material, can take the form of organic materials such as epoxy resin, ceramic materials like alumina, or a composite laminate incorporating a blend of different materials. This layer serves as the fundamental support for the overall structure of the IC substrate.
Conductive Traces:
Thin copper traces formed on the substrate surface. These traces create the electrical pathways that connect the integrated circuit to external components and the printed circuit board (PCB).
Dielectric Layers:
Insulating layers, often made of materials like resin or glass, that separate and insulate the conductive traces to prevent electrical interference and short circuits.
Vias:
Plated through-holes or vias that penetrate the substrate layers, enabling vertical electrical connections between different layers. Vias facilitate complex multi-layered designs.
Bonding Pads:
Areas on the substrate with exposed metal surfaces where the integrated circuit is attached. These pads establish the electrical connection between the IC and the substrate.
Solder Mask:
A protective layer applied over the substrate, leaving openings for soldering components. The solder mask prevents unintended electrical contact and protects the substrate from environmental factors.
Surface Finish:
The topmost layer, providing a finish that enhances solderability and protects the substrate during assembly and use.
The intricate arrangement of these layers and components forms a functional IC substrate, offering structural support, electrical connectivity, and thermal management for integrated circuits.
IC Substrate Manufacturing Technologies:
The production of IC substrates involves several manufacturing technologies that have evolved to meet the demands of modern electronics. Two noteworthy advancements are:
Improved HDI Fabrication Technology:
High-Density Interconnect (HDI) technology involves increasing the number of connections and reducing the size of components on a substrate. Improved HDI fabrication technology enhances the density of interconnections, enabling smaller and more complex designs.
This technology allows for finer traces, smaller vias, and increased layer count, contributing to improved signal integrity and miniaturization.
Improved Semi-Additive Method:
The Semi-Additive Process (SAP) involves selectively depositing metal onto the substrate to create conductive traces. The Improved Semi-Additive method refines this process, enabling more precise and efficient trace formation.
This advancement enhances the manufacturing precision, allowing for finer features and tighter tolerances in the production of complex IC substrates.
These manufacturing technologies contribute to the production of IC substrates with enhanced performance, miniaturization, and reliability. As electronic devices continue to demand smaller form factors and increased functionality, ongoing innovations in fabrication techniques play a crucial role in shaping the evolution of IC substrate manufacturing.
FAQs
What is the role of IC substrates in electronic devices?
IC substrates serve as essential platforms for mounting and connecting integrated circuits. They provide structural support, electrical connectivity, and thermal management, contributing to the overall functionality and reliability of electronic devices.
How do IC substrates differ from printed circuit boards (PCBs)?
IC substrates and PCBs serve distinct roles in electronic systems. IC substrates are specialized components specifically designed to support and connect integrated circuits. In contrast, printed circuit boards (PCBs) function as comprehensive foundations that facilitate the integration of various electronic components throughout the entire system.
What are the main types of IC substrates, and how do they differ?
The main types of IC substrates include organic, ceramic, and laminate substrates. Variations among IC substrates arise from differences in materials, characteristics, and applications. For example, organic substrates are typically lightweight and economically efficient, whereas ceramic substrates stand out for their exceptional thermal management capabilities.
How does the internal structure of an IC substrate contribute to its functionality?
The internal structure, including layers such as substrate material, conductive traces, dielectric layers, vias, bonding pads, solder mask, and surface finish, collectively supports the electrical connectivity, thermal dissipation, and overall functionality of integrated circuits.
What advancements have been made in IC substrate manufacturing technologies?
Advancements include Improved HDI fabrication technology, enhancing interconnect density for smaller and more complex designs. The Improved Semi-Additive method refines trace formation, contributing to increased precision in the manufacturing of IC substrates.
How do IC substrates contribute to miniaturization in electronic devices?
IC substrates play a crucial role in miniaturization by providing a compact and efficient platform for mounting and connecting integrated circuits. Advancements in design and manufacturing technologies contribute to achieving smaller form factors and increased component density.
What considerations should be made when selecting an IC substrate for a specific application?
Considerations include the type of substrate (organic, ceramic, or laminate), thermal requirements, electrical performance, cost considerations, and compatibility with the intended application. Tailoring the IC substrate to meet specific needs ensures optimal performance.
How do IC substrates contribute to thermal management in electronic devices?
IC substrates incorporate features like thermal vias, pads, and spreaders to efficiently dissipate heat generated by integrated circuits. This thermal management is crucial for preventing overheating and ensuring the reliable operation of electronic devices.
Are IC substrates recyclable or environmentally friendly?
The recyclability and environmental impact of IC substrates depend on the materials used. Organic substrates may be more environmentally friendly, while ceramics pose challenges in terms of recycling. Manufacturers are increasingly considering sustainability in substrate material choices.
How do IC substrates impact signal integrity in electronic devices?
The design of IC substrates, including the arrangement of conductive traces and use of advanced materials, plays a critical role in maintaining signal integrity. Controlled impedance and optimized signal routing contribute to reliable data transmission within electronic devices.
Conclusion
In conclusion, the crucial aspects discussed underscore the indispensable role of IC substrates in shaping the landscape of modern PCB engineering. As technology advances, the significance of IC substrates becomes increasingly evident in optimizing electronic performance.
The exploration of IC substrates has revealed their multifaceted contributions to electronic devices. From providing structural support, electrical connectivity, and thermal management for integrated circuits to accommodating advancements in manufacturing technologies, IC substrates play a pivotal role in the seamless operation of electronic devices. Their ability to adapt to evolving demands, such as miniaturization, enhanced signal integrity, and thermal efficiency, highlights their importance in the dynamic field of PCB engineering.
As electronic devices continue to push the boundaries of innovation, IC substrates emerge as critical enablers, ensuring the reliability, performance, and efficiency of the interconnected electronic components. Their intricate design, coupled with advancements in fabrication techniques, exemplifies the integral role IC substrates play in the ever-evolving landscape of PCB engineering.