IC Substrate Vender .High speed and high frequency material packaging substrate manufacturing. Advanced packaging substrate production process and technology.
IC substrate (Integrated Circuit Substrate) is a fundamental component used to support and connect integrated circuit (IC) chips. Typically, an IC substrate is a thin, flat board with circuits, wires, and other necessary components designed on it to provide support and connectivity to the IC chip. The design of IC substrates aims to offer electrical connections, signal transmission, and heat dissipation functions for the IC chip.
The primary functions of an IC substrate include:
Electrical Connections: Through wires and connectors, IC substrates provide electrical connections, allowing IC chips to communicate with other electronic components or systems.
Signal Transmission: The wires and circuits on IC substrates are designed for signal transmission, ensuring effective data transfer between the chip and other components.
Support and Protection: IC substrates provide physical support for IC chips and help protect them from mechanical and environmental damage.
Heat Dissipation: Some IC substrate designs include heat dissipation elements to help efficiently dissipate the heat generated by the IC chip, ensuring stable operation.
Encapsulation: IC substrates are often used for encapsulating IC chips, providing a convenient form for integration and use in electronic devices.
IC substrates exhibit diverse types and designs customized to meet specific application needs and chip specifications. The array of IC substrates encompasses single-layer substrates, multi-layer substrates, and high-density interconnect (HDI) substrates, each delivering distinct advantages tailored to specific applications. For instance, HDI substrates prove highly effective in high-performance and high-density scenarios, while multi-layer substrates are preferred for situations requiring more intricate circuitry.
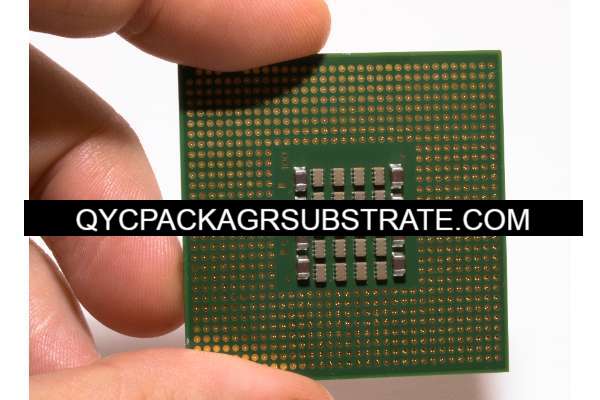
What Constitutes IC Substrate?
IC substrate, commonly referred to as a package substrate, plays a foundational role in the assembly of integrated circuits (ICs). Functioning as a crucial platform, it provides support and facilitates the interconnection of diverse electronic components housed within an IC package.The substrate is a crucial part of the overall IC design, providing a physical foundation for the IC and facilitating the electrical connections between different parts of the circuit.
The essential components and features of an IC substrate include:
Substrate Material:
The substrate is commonly composed of materials with effective electrical insulating properties, such as ceramics or organic substances like epoxy resin reinforced with fiberglass. Ceramic substrates, favored for their exceptional thermal conductivity, are frequently utilized in high-performance applications.
Conducting Layers:
The substrate contains multiple conducting layers, usually made of copper, that form the electrical pathways for signals to travel between different components on the IC.
Via Holes:
Via holes are openings in the substrate that allow electrical connections between different layers of the substrate. These are crucial for creating vertical connections within the IC.
Solder Mask:
A solder mask is applied to the substrate to insulate and protect the conducting layers. It prevents unintended electrical connections and helps ensure that solder is applied only to specific areas during the assembly process.
Ball Grid Array (BGA) or Quad Flat Package (QFP):
Depending on the packaging technology, the substrate may have a specific arrangement of contact points or solder balls that connect the IC to the external circuitry on a printed circuit board (PCB).
Die Attach Pad:
The substrate includes a die attach pad, which is the area where the actual semiconductor chip (IC die) is attached. This pad provides mechanical support and thermal conductivity for efficient heat dissipation.
Understanding the composition and structure of the IC substrate is crucial for designing reliable and high-performance integrated circuits. It plays a vital role in ensuring proper electrical connections, heat dissipation, and overall functionality of the IC package.
What Functionality Does IC Substrate Serve?
The IC substrate serves several key functions in the packaging of integrated circuits (ICs). Its primary functionalities include:
Electrical Connectivity: The IC substrate acts as a medium for electrical connections between the chip and other components within the IC package. Through the use of conductive traces and metal layers on the substrate, it facilitates the transmission of electric current and signals, enabling communication between the chip and other elements.
Structural Support: Beyond electrical connections, the IC substrate provides structural support to the IC package. It maintains the stable positioning of the chip and other components, protecting them from external environmental influences.
Heat Management: As ICs operate, they generate heat, and the IC substrate contributes to heat conduction and dissipation. By designing effective heat dissipation structures on the substrate, it helps disperse heat to the external environment, preventing the chip from overheating and potential damage.
Signal Transmission Optimization: The configuration of the IC substrate significantly influences signal transmission performance. By employing well-designed wiring and materials, it becomes feasible to minimize signal transmission delays and improve signal quality. This, in turn, enhances the overall efficiency and performance of the integrated circuit.
In summary, the IC substrate plays a crucial bridging role in IC packaging, connecting the chip to other essential components while providing structural support and contributing to effective heat management to ensure the reliable operation of the entire IC.
What Diverse Types Does IC Substrate Take?
IC substrates come in various types, catering to diverse application requirements and showcasing the adaptability of IC substrate technology. Here are some common types:
Ceramic Substrates: Ceramic substrates are favored for their superior thermal conductivity and robust mechanical strength, making them particularly effective in applications involving elevated temperatures and high frequencies. They are well-suited for electronic devices that demand efficient heat dissipation and stability, including RF modules and power amplifiers.
Organic Substrates: Organic substrates commonly employ materials such as epoxy resins reinforced with glass fibers or polyimides. Given their lightweight properties and cost-effectiveness, these substrates are ideal for economical and lightweight design purposes, especially within the domain of consumer electronics.
Sapphire Substrates:Sapphire substrates, known for their outstanding insulating properties and exceptional transparency, find extensive use in the optoelectronics industry. These substrates are essential in high-brightness LEDs and laser diode applications, making substantial contributions to the field of optoelectronics.
Molybdenum Substrates: Molybdenum substrates distinguish themselves through their notable thermal conductivity and robust mechanical strength, making them particularly suitable for integrated circuits with rigorous power density requirements.They play a crucial role in applications where effective heat dissipation is essential, including power modules and high-performance computing devices.
Glass Substrates: Glass substrates excel in particular applications, notably in the realm of biosensors and medical devices. Their superior performance in these specific areas underscores their significance in these specialized fields.Their flatness and biocompatibility make them suitable for certain biomedical fields.
Different types of IC substrates play key roles in various applications based on their characteristics, highlighting the diversity and adaptability of IC substrate technology.
How Does IC Substrate Relate to PCBs?
IC (Integrated Circuit) substrates and Printed Circuit Boards (PCBs) have a close relationship within the intricate web of electronic components. The IC substrate is a specialized type of board designed to support and connect chips encapsulated in integrated circuit packages. Here’s how IC substrates relate to traditional PCBs and the intricate relationship they share with the encapsulation and interconnection of semiconductor devices within a package.
Relationship between IC Substrates and PCBs:
Chip Support: IC substrates are specifically designed to support and connect chips. IC substrates play a vital role in ensuring the effective operation of chips by establishing essential electrical connections, facilitating signal transmission, and managing power distribution.
Size and Layout: The dimensions and arrangement of IC substrates are intricately tied to the specific packaging used for enclosing the chips. It must accommodate the shape and size of the chip to ensure good mechanical and electrical performance.
High-Density Interconnection: Due to the small and densely packed components on IC substrates, high-density interconnection technologies, such as micro-sized circuits and holes, are often required.
Differences from Traditional PCBs:
Size and Density: IC substrates are typically smaller than traditional PCBs because they are specifically designed to encapsulate individual chips. Additionally, they often require higher interconnect density to accommodate the tiny components in integrated circuit packages.
Specialized Design: The design of IC substrates is tailored to meet the requirements of specific chips, whereas traditional PCBs may have a more generic design for connecting multiple components.
Hierarchical Structure: IC substrates often have a more complex hierarchical structure to accommodate intricate signal routing and power distribution requirements.
Relationship with Encapsulation and Interconnection:
Encapsulation: IC substrates are a crucial component of the encapsulation process. They provide mechanical support for the chip and establish electrical connections to the external world.
Interconnection: The interconnection network on IC substrates is responsible for transmitting signals and power between the chip’s internal components and the encapsulation. Precision is essential in the design of these interconnections to guarantee optimal performance, minimize power consumption, and enhance overall reliability.
In summary, IC substrates play a vital role in the entire integrated circuit packaging process. Through providing mechanical support and intricate interconnections, they enable chips to function effectively in various applications.
How Does IC Substrate Differ from PCB?
IC Substrate vs. PCB (Differences Between IC Substrate and Printed Circuit Board)
There are several key distinctions between an Integrated Circuit Substrate (IC Substrate) and a Printed Circuit Board (PCB). IC Substrates are specialized components designed to carry integrated circuit chips. In contrast, PCBs are more widely used for the interconnection and support of various electronic components. The design of IC Substrates is more complex, considering the packaging and connection of integrated circuit chips, while PCBs are primarily used for the overall interconnection in electronic devices.
Differences Between PWBs and PCBs (Printed Wiring Boards vs. Printed Circuit Boards)
Although Printed Wiring Boards (PWBs) and Printed Circuit Boards (PCBs) are occasionally used interchangeably, they exhibit nuanced distinctions. PWBs primarily emphasize the wires and connections on the board, while PCBs encompass the entirety of the circuit board, including connections and integrated circuits.
Role of IC Substrate in a Motherboard (The Crucial Role of IC Substrate in a Motherboard)
The IC Substrate plays a crucial role in motherboards, serving as the foundation for connecting and supporting various integrated circuit chips. The IC Substrate on the motherboard provides electrical connections, thermal management, and mechanical support, ensuring seamless collaboration among different components. The design of the IC Substrate is paramount for the overall performance and stability of the motherboard.
Definition and Significance of SLP (Substrate-like PCBs)
Substrate-like PCBs (SLP) represent a technology that bridges the gap between traditional PCBs and IC Substrates. Incorporating design principles similar to IC Substrates, SLP proves superior in high-frequency and high-speed applications. SLP finds widespread application in slim electronic devices such as smartphones and laptops, offering enhanced performance and heat dissipation capabilities.
Impact of HDI Substrate on Miniaturization (Exploring the Influence of High-Density Interconnect Substrates on Device Miniaturization)
High-Density Interconnect (HDI) substrates are an advanced printed circuit board technology that achieves device miniaturization by reducing component spacing and increasing connection density. HDI substrates play a crucial role in compact electronic devices like smartphones and tablets, allowing them to maintain performance while becoming more compact and lightweight.
What Constitutes the Main Structure and Production Technologies of IC Substrate?
Integrated Circuit Substrate (IC Substrate) is a critical component that supports integrated circuit chips, providing electrical connections and mechanical support. Here’s a detailed overview of the main structure and production technologies of IC substrates:
Main Structure of IC Substrate
IC substrates typically consist of multiple layers, each serving specific functions and characteristics. Here’s the typical structure of an IC substrate:
Substrate Layer: The substrate is the foundational layer of the IC substrate, usually made of dielectric materials, providing mechanical support and electrical isolation.
Conductive Layers: These layers include conductive materials such as copper foil, facilitating the creation of circuit connections and communication paths.
Insulation Layers: Situated between conductive layers, insulation layers prevent electrical short circuits and provide interlayer insulation.
Solder Ball Layer: Located at the bottom of the substrate, this layer is used for connecting IC chips and other components.
Production Technologies of IC Substrate
The manufacturing of IC substrates involves various technologies and processes, with some key production technologies including:
Printed Circuit Board (PCB) Technology: PCB technology forms the foundation of IC substrate manufacturing, involving processes such as chemical etching, copper plating, and printing.
Thin Film Technology: Thin film technology is employed to create intricate circuit structures while reducing the overall thickness of the substrate.
Laser Drilling Technology: Laser drilling allows for the creation of small apertures and high-density circuit layouts.
Metalization Treatment Technology: Metalization treatment of conductive layers, such as copper electroplating, enhances electrical conductivity.
Evolution of HDI Manufacturing Technology
High-Density Interconnect (HDI) is a crucial trend in IC substrate manufacturing, aiming to improve circuit performance by reducing component distances and increasing layer density. The evolution of HDI manufacturing technology includes:
Fine Circuitry: Utilizing fine circuitry technology achieves higher line density and smaller component spacings.
Thin Film Layers: Increasing the number of thin film layers accommodates more circuit components within limited space.
Multilayer Stacking: HDI technology allows for stacking multiple circuit layers on the same substrate, thereby enhancing integration.
Significance of the Semi-Additive Method
The semi-additive method is a consequential manufacturing approach in IC substrate fabrication. In contrast to traditional full additive methods, the semi-additive method reduces waste and environmental pollution, enhancing production efficiency. This method adds metal only where necessary, as opposed to applying metal across the entire surface, enabling more precise circuit patterns.
In summary, the structure and production technologies of IC substrates are continually evolving, especially with the application of HDI manufacturing technology and the significance of the semi-additive method, driving the development and performance improvement of integrated circuits.
What Are the FAQs about IC Substrate?
What is an IC Substrate?
An IC substrate is a critical component of integrated circuits (ICs) that provides electrical connections and support for IC chips. Typically made of insulating materials, it features vias, metal layers, and other structures for connecting IC chips and other system components.
What is the role of an IC Substrate?
The primary role of an IC substrate is to provide support, electrical connections, and thermal management to ensure the proper functioning of IC chips. It also contributes to size reduction, improved performance, and enhances the stability and reliability of integrated circuits.
What are the different types of IC Substrates?
IC substrates are available in diverse types, such as single-layer, multi-layer, rigid, and flexible substrates. Each type is tailored for specific applications and comes with unique advantages. The selection of a particular type depends on the specific requirements of IC design and application needs.
What is the manufacturing process of IC Substrates?
The production of IC substrates comprises several essential steps, including the careful selection of materials, the printing of circuit patterns, drilling, metallization, precision cutting, and thorough testing. The quality and precision maintained throughout the manufacturing process play a pivotal role in ensuring the optimal performance of integrated circuits.
What role does an IC Substrate play in electrical performance?
IC substrates play a crucial role in electrical performance, affecting signal transmission speed, power consumption, noise, and more. Designing and selecting the appropriate IC substrate can optimize circuit performance.
How do Flexible IC Substrates differ from Rigid IC Substrates?
Traditional IC applications commonly employ rigid IC substrates, whereas flexible IC substrates find suitability in applications requiring specific shapes and sizes, such as wearable devices. The use of flexible substrates provides benefits in terms of adaptability and lightweight design.
Why is thermal design important in IC Substrates?
Thermal design is a critical aspect of IC substrate design, directly impacting chip temperature management and stability. Effective thermal design can enhance IC performance, prolong its lifespan, and reduce the risk of failures due to overheating.
What are the applications of IC Substrates in electronic products?
IC substrates find broad application in a variety of electronic devices, encompassing smartphones, computers, automotive electronics, medical devices, and other electronic components. Their diverse applications make IC substrates an indispensable component of modern electronic products.
How do the size and thickness of IC Substrates affect design?
The size and thickness of IC substrates directly impact circuit layout, heat dissipation, and overall dimensions. Balancing these factors is essential in the design process to meet the specific requirements of the application.
What are the future trends in IC Substrate technology?
Future trends in IC substrate technology may involve further miniaturization, higher performance, increased density, and the use of more advanced materials. As electronic products continue to innovate, IC substrate technology will evolve to meet new challenges and demands.
Have You Discovered the Profound Role of IC Substrate?
Integrated circuit substrates, abbreviated as IC substrates, are pivotal for the functionality and performance of electronic devices. They act as the structural cornerstone for integrated circuits (ICs), offering a foundation for the assembly and interconnection of electronic components. The selection of substrate material and design has a notable influence on the overall effectiveness, dependability, and dimensions of electronic devices.
Here are some key points regarding the profound role of IC substrates:
Physical Support: IC substrates serve as a structural support for the integrated circuits. They provide structural support and facilitate the interconnection of diverse components, including transistors, resistors, and capacitors, in a streamlined and orderly fashion.
Electrical Interconnection: IC substrates facilitate electrical connections between different components on the integrated circuit. They provide the necessary wiring and pathways for signals to travel between elements, ensuring proper functionality.
Thermal Management: Effective heat dissipation is vital to ensure the dependable performance of electronic components. IC substrates commonly integrate materials possessing excellent thermal conductivity to disperse the heat produced during operation, averting overheating and potential damage.
Miniaturization and Packaging: Advances in IC substrate technology contribute to the ongoing trend of miniaturization in electronics. Smaller, more efficient substrates allow for the development of compact and powerful electronic devices.
Signal Integrity: The design and material properties of IC substrates influence signal integrity, affecting the speed and reliability of data transmission within the integrated circuit. Proper substrate design helps minimize signal losses and interference.
Reliability and Durability: The choice of substrate materials and manufacturing processes impacts the overall reliability and durability of electronic devices. Robust IC substrates contribute to the longevity and performance stability of integrated circuits.
Understanding and appreciating the profound role of IC substrates can lead to advancements in electronic engineering. Engineers and researchers can delve into groundbreaking substrate materials, designs, and manufacturing methods to extend the limits of existing technology and open up novel horizons in electronic devices. This ongoing exploration is vital in addressing the escalating needs for electronic systems that are smaller, quicker, and more dependable.