IC/BGA Package Substrate Material. The Material type and selection of packaging substrate. BT base series, Showa Denko and Ajinomoto(ABF) Base series. or we also can use the Rogers base and other types base materials.
Brief Overview of IC Packaging
In the intricate world of integrated circuits (ICs), packaging stands as the unsung hero, providing the protective shield and structural framework for these electronic marvels. This encapsulation process not only shields ICs from environmental factors but also plays a pivotal role in their overall functionality.
Importance of Substrate Materials in Ensuring Optimal Performance
Amidst the layers of IC packaging lies a critical component— the substrate material. This unassuming layer is a silent powerhouse, influencing structural integrity, thermal dynamics, and electrical performance. As we delve into the heart of IC packaging, it becomes clear that the choice of substrate material is not merely a technicality; it’s a strategic decision that shapes the very essence of an integrated circuit’s efficiency and reliability. Let’s unravel the significance of substrate materials in this technological tapestry.
Now, we’ll seamlessly transition into the subsequent sections, exploring the multifaceted roles of substrate materials in the realm of IC packaging.
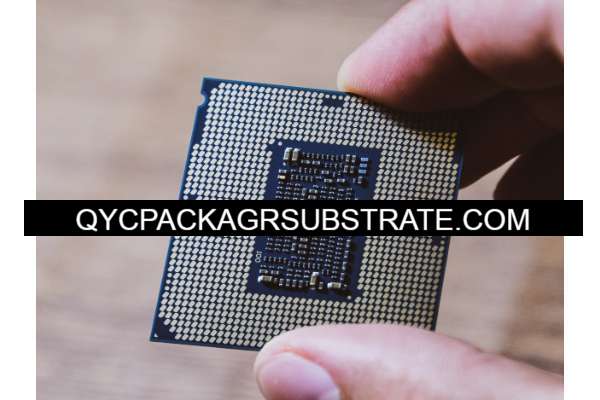
Understanding IC Packaging
Definition and Purpose of IC Packaging
IC packaging stands as a pivotal phase within the semiconductor manufacturing journey, significantly impacting the performance, reliability, and functionality of electronic devices. At its core, this process entails safeguarding the semiconductor die, commonly known as the chip, by encapsulating it within a protective package. This protective layer serves the dual purpose of shielding the chip from environmental factors and streamlining its seamless integration into electronic systems. In essence, IC packaging is the safeguarding gateway that ensures the optimal functioning of electronic devices.
Protection and Environmental Shielding: The packaging acts as a protective barrier, shielding the delicate semiconductor components from external factors such as moisture, contaminants, and mechanical stress. This protection is vital to ensure the longevity and reliability of the integrated circuit.
Electrical Isolation: The packaging provides electrical isolation, preventing interference between the integrated circuit and the external environment. This is essential for maintaining signal integrity and preventing electrical malfunctions.
Thermal Management: Efficient dissipation of heat generated during operation is facilitated by the packaging. Proper thermal management is crucial for preventing overheating, which can degrade performance and lead to long-term damage.
Mechanical Support: The packaging provides structural support, safeguarding the fragile semiconductor die from mechanical stresses that may occur during handling, assembly, or operation.
Key Components of IC Packaging Process
The IC packaging process comprises several key components, each contributing to the overall functionality and reliability of the integrated circuit. These components align with the intricate dance of technology and engineering, ensuring the successful integration of semiconductor devices into electronic systems:
Substrate Material Selection: The choice of substrate material is critical. Organic substrates like FR-4 or BT and inorganic substrates such as ceramic or silicon are selected based on factors like thermal conductivity, electrical properties, and form factor requirements.
Die Attach: The semiconductor die is securely attached to the substrate using a die attach material, commonly epoxy or solder. This step ensures proper thermal and electrical connectivity.
Wire Bonding or Flip-Chip Bonding: Wire bonding involves connecting the die to the package leads using thin wires, while flip-chip bonding directly attaches the die to the substrate, enhancing electrical performance and reducing signal propagation delays.
Encapsulation: The packaged die is encapsulated in a protective material, often epoxy resin or molding compounds, forming the final package. This encapsulation shields the die from environmental factors and provides additional mechanical support.
Lead Frame or Package Substrate: The lead frame or package substrate serves as the foundation for the entire package, providing electrical connectivity between the die and the external world. The choice of substrate material significantly influences electrical and thermal performance.
Testing and Quality Assurance: Rigorous testing is conducted to ensure the integrity and functionality of the packaged IC. This includes electrical tests, thermal analysis, and other quality assurance measures to meet industry standards and product specifications.
In summary, IC packaging is a sophisticated process that involves a synergy of materials, engineering precision, and technological innovation, with each component contributing to the overall success of the integrated circuit in its intended application.
Significance of Substrate Materials
Role in Providing Structural Support
The structural foundation of integrated circuits (ICs) hinges on the substrate material, a critical component often overshadowed but undeniably pivotal. The chosen substrate, be it organic or inorganic, forms the robust backbone that supports the delicate circuitry, ensuring mechanical stability amid various environmental conditions. This structural support is paramount, especially in applications where the ICs face physical stress or demanding operating environments.
Incorporating advanced materials such as BT (Bismaleimide Triazine) or ceramic substrates bolsters the structural integrity, aligning with the industry’s pursuit of compact, lightweight, and durable IC packages. Engineers today recognize the synergy between structural support and overall IC reliability, harmonizing intricate circuit designs with resilient substrates for enhanced performance and longevity.
Impact on Thermal Management
The thermal landscape of IC packaging is a battleground where substrate materials play a decisive role. Effective thermal management is essential for preventing overheating, which can compromise the functionality and lifespan of integrated circuits. Substrate materials, with their varying thermal conductivities, act as conduits for dissipating heat generated during operation.
In the quest for optimal thermal management, substrates like silicon and advanced ceramics emerge as champions. Their ability to efficiently conduct and disperse heat ensures that ICs can operate at peak performance without succumbing to thermal stress. This not only safeguards the circuitry but also contributes to energy efficiency, aligning with the industry’s green initiatives.
Electrical Properties and Signal Integrity
The electrical properties of substrate materials are the unsung heroes in the symphony of integrated circuitry. Signal integrity, a cornerstone for reliable electronic communication, relies heavily on the dielectric constant, loss tangent, and other electrical characteristics of the chosen substrate.
Organic substrates like FR-4, while popular, may pose challenges in maintaining signal integrity at higher frequencies. This is where advanced materials such as silicon and specialized ceramics come into play. Their superior electrical properties enable the seamless transmission of signals, especially in applications demanding high-speed data transfer and low latency.
In a world increasingly reliant on interconnected devices, the choice of substrate material becomes a strategic decision, directly influencing the efficacy of signal transmission and the overall performance of integrated circuits.
By delving into the multifaceted significance of substrate materials in IC packaging, we uncover a nuanced interplay between structural support, thermal dynamics, and electrical properties. The synergy of these elements not only fortifies the reliability of integrated circuits but also propels technological advancements towards more efficient and resilient electronic systems.
Commonly Used Substrate Materials
Organic Substrates
1.FR-4 (Flame Retardant-4)
Structural Support and Durability: FR-4, a widely adopted organic substrate, offers robust structural support, ensuring the physical integrity of the integrated circuit (IC).
Thermal Properties: The thermal stability of FR-4 enhances its performance in various electronic applications, especially those requiring resistance to heat and temperature fluctuations.
Electrical Insulation: With excellent electrical insulation properties, FR-4 promotes signal integrity and protects against unwanted interference, crucial for high-frequency applications.
2.BT (Bismaleimide Triazine)
High-Temperature Performance: BT substrates excel in high-temperature environments, making them suitable for demanding applications where thermal management is critical.
Signal Transmission: BT’s low dielectric constant contributes to efficient signal transmission, supporting the high-speed requirements of modern integrated circuits.
Reliability: Known for its mechanical strength and reliability, BT is favored in applications where the substrate material must endure challenging conditions, ensuring long-term functionality.
Inorganic Substrates
1.Ceramic
Thermal Conductivity: Ceramic substrates exhibit exceptional thermal conductivity, facilitating efficient heat dissipation and contributing to overall system reliability.
Miniaturization Support: The inherent properties of ceramic materials make them suitable for miniaturized electronic devices, aligning with the trend toward smaller, more powerful ICs.
High-Frequency Applications: Ceramic’s low loss tangent makes it ideal for high-frequency applications, addressing the growing demand for faster and more efficient electronic devices.
2.Silicon
Integration with Semiconductor Components: Silicon substrates seamlessly integrate with semiconductor components, providing a solid foundation for the fabrication of advanced ICs.
Signal Integrity: Silicon’s low electrical resistance enhances signal integrity, ensuring reliable communication between components on the IC.
Compatibility with Microfabrication Processes: Silicon’s compatibility with microfabrication processes supports the development of intricate, high-performance ICs, meeting the evolving needs of the electronics industry.
Emerging Trends
1.Flexible Substrates
Bendable Electronics: Flexible substrates, a cutting-edge trend, enable the creation of bendable electronics, catering to the demand for flexible and wearable devices.
Application in IoT Devices: The flexibility of these substrates makes them ideal for Internet of Things (IoT) devices, contributing to the expansion of interconnected technologies.
2.3D Packaging Technology
Enhanced Performance and Integration: 3D packaging technology represents a paradigm shift, allowing for increased integration of components and improved overall performance.
Reduction in Footprint: By stacking multiple layers of components, 3D packaging reduces the physical footprint of ICs, addressing the need for compact yet powerful electronic devices.
Advanced Thermal Management: The vertical stacking in 3D packaging enhances thermal management, crucial for maintaining optimal operating temperatures in densely packed electronic systems.
By exploring these commonly used and emerging substrate materials, we gain a deeper understanding of the dynamic landscape shaping the future of IC packaging, blending traditional strengths with innovative trends to meet the demands of the ever-evolving electronics industry.
Thermal Considerations
Heat Dissipation Challenges in IC Packaging
1.Introduction to Heat Dissipation Challenges
Overview of the escalating demand for higher performance in integrated circuits (ICs)
Challenges posed by increased power density and miniaturization
2.Keyword Integration
Highlighting the critical role of efficient heat dissipation in meeting performance demands
Balancing power and thermal considerations in IC design
3.Miniaturization Effects on Heat Dissipation
Discussion on how smaller form factors intensify heat dissipation challenges
Examples of miniaturized devices facing thermal limitations
Substrate Material’s Role in Thermal Management
1.Structural Support and Thermal Pathways
Emphasizing the interconnectedness of substrate materials and thermal management
How substrate materials act as conduits for heat dissipation
2.Organic vs. Inorganic Substrates in Thermal Management
Analyzing the thermal properties of common substrate materials
Integrating keywords such as FR-4 and ceramic in the context of heat dissipation
3.Innovations in Thermal-Enhanced Substrates
Discussing how substrate materials are evolving to address thermal challenges
Integration of phrases like “advanced thermal conductivity” and “heat dissipation solutions”
Advances in Thermal Conductive Substrate Materials
1.Overview of Thermal Conductive Substrate Materials
Introducing materials designed specifically for superior thermal conductivity
Highlighting the importance of material selection for thermal performance
2.Application of Advanced Materials in IC Packaging
Examining real-world applications of materials with enhanced thermal conductivity
Case studies on the positive impact of these materials on heat dissipation
3.Keyword Integration and Future Prospects
Incorporating key terms like “thermal conductive substrates” and “innovative thermal solutions”
Exploring ongoing research and potential breakthroughs in thermal management
By delving into the specifics of heat dissipation challenges, the role of substrate materials, and the latest advances in thermal conductive substrates, this section aims to provide a comprehensive understanding of how the evolving landscape of IC packaging addresses critical thermal considerations.