LED Ceramic Substrate
LED Ceramic Substrate Manufacturer, Ceramic materials LED PCBs, and high TG BT materials LED PCBs Vendor. The finished surface is more flat, the material is resistant to high temperature, and the use time is longer.We can produce super small marks, and super small gap LED PCB, The best smallest gap are about 25um. if we use the ABF base materials. we can do the best samllest gap with 9UM.
LED ceramic substrates provide a crucial foundation for the performance and reliability of LED lighting systems. Composed of advanced ceramic materials like aluminum nitride (AlN) or aluminum oxide (Al2O3), these substrates offer exceptional thermal conductivity and electrical insulation properties. By efficiently dissipating heat generated by LED chips, they ensure optimal operating temperatures, extending the lifespan and enhancing the efficiency of LED lighting. LED ceramic substrates are engineered with precision to accommodate the intricate circuitry and mounting requirements of LED chips, providing a stable platform for their integration. With their mechanical robustness and resistance to environmental factors, such as moisture and thermal cycling, LED ceramic substrates deliver reliable performance in a wide range of applications, including lighting, displays, automotive, and electronics. Their versatility and customizable features make them essential components in the advancement of energy-efficient and high-performance LED technologies.
What is an LED Ceramic Substrate?
An LED ceramic substrate is a material used as a base for mounting and connecting LED (Light Emitting Diode) chips. These substrates are made from ceramic materials like aluminum oxide (Al2O3) or aluminum nitride (AlN), which offer excellent thermal conductivity and electrical insulation properties.
LED chips generate heat while emitting light, and effective dissipation of this heat is crucial for maintaining LED performance and longevity. Ceramic substrates provide efficient heat dissipation, ensuring that the LED chips operate at optimal temperatures. This helps prevent overheating, which can degrade the LED’s performance and lifespan.
Additionally, ceramic substrates offer mechanical stability and durability, making them suitable for various LED applications, including lighting, displays, automotive lighting, and more. They also provide a stable platform for mounting and interconnecting LED chips, enabling efficient electrical connections and reliable operation.
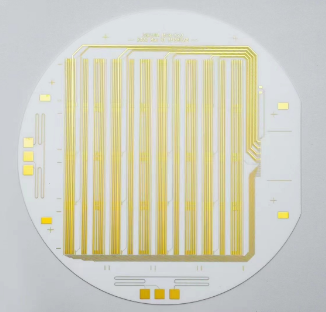
LED Ceramic Substrate
What are the LED Ceramic Substrate Design Guidelines?
Design guidelines for LED ceramic substrates typically focus on optimizing thermal management, electrical performance, and mechanical stability. Here are some common guidelines:
- Thermal Conductivity: Choose ceramic materials with high thermal conductivity, such as aluminum nitride (AlN) or aluminum oxide (Al2O3). Higher thermal conductivity facilitates better heat dissipation from the LED chips, ensuring they operate at optimal temperatures.
- Thermal Resistance: Minimize the thermal resistance between the LED chip and the ceramic substrate to enhance heat dissipation. This can be achieved by using materials with low thermal resistance and optimizing the design of the LED package to maximize thermal contact.
- Thermal Expansion: Match the coefficient of thermal expansion (CTE) between the LED chip, the ceramic substrate, and other components in the assembly to reduce thermal stress and prevent cracking or delamination.
- Electrical Insulation: Ensure that the ceramic substrate provides sufficient electrical insulation to isolate the LED chips from the rest of the circuitry. This prevents short circuits and electrical damage.
- Dielectric Strength: Choose ceramic materials with high dielectric strength to withstand high voltage and prevent electrical breakdown.
- Dimensional Stability: Design the ceramic substrate to maintain dimensional stability over a wide temperature range to prevent warping or deformation that could affect LED chip alignment and performance.
- Surface Finish: Optimize the surface finish of the ceramic substrate to improve adhesion of the LED chips and facilitate soldering or bonding processes during assembly.
- Mounting Configuration: Design the substrate layout to accommodate the desired LED chip configuration and optimize thermal performance. This may include considerations such as chip placement, interconnect layout, and the use of thermal vias for heat dissipation.
- Environmental Protection: Incorporate features to protect the LED chips and circuitry from environmental factors such as moisture, dust, and chemical exposure.
- Testing and Quality Control: Implement testing protocols to ensure the reliability and performance of the LED ceramic substrates, including thermal cycling tests, electrical characterization, and inspection for defects.
By following these guidelines, designers can optimize the performance, reliability, and lifespan of LED ceramic substrates for various applications.
What is the LED Ceramic Substrate Fabrication Process?
The fabrication process of LED ceramic substrates involves several steps to create a stable, thermally conductive, and electrically insulating platform for mounting LED chips. Here’s an overview of the typical fabrication process:
- Material Selection: Choose a ceramic material with suitable properties for LED applications, such as aluminum nitride (AlN) or aluminum oxide (Al2O3), based on factors like thermal conductivity, electrical insulation, and mechanical strength.
- Substrate Preparation: Start with ceramic sheets or wafers of the chosen material. These substrates are typically manufactured through processes like tape casting, green machining, or ceramic powder sintering to achieve the desired dimensions and surface finish.
- Circuit Design: Design the circuit layout on the ceramic substrate, including the placement of LED chip mounting pads, interconnect traces, and any additional components required for the application.
- Metallization: Deposit thin layers of conductive metal, such as aluminum or copper, onto the ceramic substrate to create the electrical circuitry. This can be done using techniques like physical vapor deposition (PVD), sputtering, or screen printing.
- Die Attachment: Apply a thermally conductive adhesive or solder paste to bond the LED chips to their mounting pads on the ceramic substrate. Precision placement equipment may be used to ensure accurate alignment of the chips.
- Wire Bonding: Connect the electrical leads of the LED chips to the substrate’s metallized traces using wire bonding techniques. This involves using fine wires (typically gold or aluminum) and a bonding tool to create electrical connections.
- Encapsulation: Optionally, apply a protective encapsulant material over the LED chips and wire bonds to provide mechanical support and environmental protection. Common encapsulant materials include epoxy resins or silicone-based compounds.
- Testing and Quality Control: Perform electrical testing, thermal characterization, and visual inspection to ensure the functionality, reliability, and quality of the fabricated LED ceramic substrates. This may include checks for electrical continuity, thermal performance, and the absence of defects.
- Packaging and Assembly: Complete the LED package assembly by mounting the ceramic substrate into a housing or enclosure, along with any necessary optics, connectors, and thermal management components.
- Final Testing and Validation: Conduct final performance testing on the assembled LED packages to verify that they meet the required specifications and performance criteria before deployment in actual applications.
By following these fabrication steps, manufacturers can produce high-quality LED ceramic substrates suitable for various lighting, display, and electronics applications.
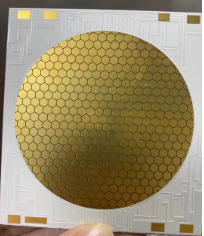
LED Ceramic Substrate
How do you manufacture LED Ceramic Substrates?
Manufacturing LED ceramic substrates involves several key processes to create a robust platform for mounting and interconnecting LED chips. Here’s a detailed overview of the typical manufacturing process:
- Raw Material Selection: Begin by selecting high-quality ceramic materials suitable for LED applications. Common choices include aluminum nitride (AlN) and aluminum oxide (Al2O3) due to their excellent thermal conductivity and electrical insulation properties.
- Preparation of Ceramic Sheets or Wafers: The manufacturing process often starts with preparing ceramic sheets or wafers of the chosen material. This can involve techniques such as tape casting, where a ceramic slurry is spread onto a carrier film and dried to form a thin ceramic sheet.
- Green Machining (Optional): In some cases, green machining may be employed to shape the ceramic substrates before firing. This involves precision cutting or machining of the green ceramic material in its unfired state to achieve the desired dimensions and surface features.
- Sintering: The ceramic sheets or wafers are then subjected to a high-temperature sintering process in a controlled atmosphere. Sintering involves heating the ceramic material to temperatures near its melting point, causing particles to bond together and form a dense, solid structure. This step is crucial for achieving the desired mechanical strength and electrical properties of the substrate.
- Surface Preparation: After sintering, the ceramic substrates may undergo surface treatment processes to improve adhesion and facilitate subsequent metallization steps. This can include cleaning, etching, or roughening the surface to promote bonding with metal layers.
- Metallization: Thin layers of conductive metal, such as aluminum or copper, are deposited onto the ceramic substrate to create the electrical circuitry. Metallization can be achieved using techniques like physical vapor deposition (PVD), sputtering, or screen printing. These metal layers serve as conductive paths for connecting the LED chips and other components.
- Die Attachment: LED chips are mounted onto the metallized areas of the ceramic substrate using a thermally conductive adhesive or solder paste. Precision placement equipment ensures accurate alignment of the chips with the substrate’s electrical traces.
- Wire Bonding: Electrical connections between the LED chips and the substrate’s metallized traces are established using wire bonding techniques. Fine wires made of materials like gold or aluminum are bonded to the LED chip pads and substrate traces using specialized bonding tools.
- Encapsulation (Optional): Optionally, a protective encapsulant material may be applied over the LED chips and wire bonds to provide mechanical support and environmental protection. Common encapsulant materials include epoxy resins or silicone-based compounds.
- Testing and Quality Control: The manufactured LED ceramic substrates undergo rigorous testing to ensure functionality, reliability, and quality. This may include electrical testing, thermal characterization, visual inspection, and other quality control measures.
By following these manufacturing steps, LED ceramic substrate manufacturers can produce high-quality substrates suitable for a wide range of LED applications, including lighting, displays, automotive lighting, and more.
How much should an LED Ceramic Substrate cost?
The cost of an LED ceramic substrate can vary depending on several factors, including its size, material, complexity, manufacturing processes, and quantity ordered. Here are some key factors that influence the cost:
- Material Cost: The type of ceramic material used for the substrate, such as aluminum nitride (AlN) or aluminum oxide (Al2O3), can impact the cost. AlN, known for its high thermal conductivity, may be more expensive compared to Al2O3.
- Manufacturing Processes: The complexity of manufacturing processes, such as sintering, metallization, die attachment, wire bonding, and encapsulation, can affect the cost. Additional steps or specialized equipment may increase manufacturing costs.
- Size and Thickness: The size and thickness of the ceramic substrate can influence its cost. Larger and thicker substrates require more material and may require additional processing steps, leading to higher costs.
- Quantity Ordered: Economies of scale typically apply in manufacturing, meaning that larger production runs can lower the cost per unit. Ordering larger quantities of LED ceramic substrates can result in volume discounts.
- Quality and Performance Requirements: Substrates designed for high-performance applications may require tighter tolerances, higher precision, and additional testing, which can increase costs.
- Customization: Customized features or designs, such as specific circuit layouts, surface finishes, or encapsulation options, may incur additional costs compared to standard substrates.
- Supplier and Market Dynamics: Prices can vary between suppliers based on factors such as geographic location, manufacturing capabilities, and market demand.
As a rough estimate, LED ceramic substrates can range in cost from a few dollars to several tens of dollars per unit, with higher-end substrates or those with specialized features commanding higher prices. It’s essential to consider the specific requirements of your application and evaluate different suppliers to determine the most cost-effective solution.
What is LED Ceramic Substrate Base Material?
The base material for LED ceramic substrates is typically a ceramic compound chosen for its thermal conductivity, electrical insulation properties, and mechanical stability. Two common materials used for LED ceramic substrates are:
- Aluminum Nitride (AlN): Aluminum nitride is a ceramic material with excellent thermal conductivity, second only to diamond among ceramics. It also has a relatively high thermal expansion coefficient, making it compatible with semiconductor materials like gallium nitride (GaN), commonly used in LED chips. AlN substrates offer efficient heat dissipation, which is crucial for maintaining the performance and longevity of LED chips.
- Aluminum Oxide (Al2O3): Also known as alumina, aluminum oxide is another widely used ceramic material for LED ceramic substrates. While it has slightly lower thermal conductivity compared to AlN, it still provides good thermal management properties and offers excellent electrical insulation. Al2O3 substrates are cost-effective and suitable for many LED applications where high thermal conductivity is not as critical.
These ceramic materials are chosen for their ability to withstand high temperatures, provide effective heat dissipation, and offer electrical insulation to prevent short circuits. They serve as a stable and durable platform for mounting and interconnecting LED chips in various lighting, display, and electronics applications.
Which company manufactures LED Ceramic Substrates?
There are many companies specialized in the manufacturing of LED ceramic substrates, including internationally renowned companies and some local manufacturers. For example, CeramTec from South Korea, Rogers Corporation from Germany, Kyocera from the United States, CoorsTek from Japan, and many others are among the major manufacturers of LED ceramic substrates.
As for our company, we are also a manufacturer of LED ceramic substrates, equipped with advanced production facilities and a skilled technical team. We are committed to providing high-quality and highly reliable LED ceramic substrate products to meet the needs of customers in the fields of lighting, displays, and electronic devices.
Our company has the following advantages and capabilities:
- Advanced Production Equipment: We invest in advanced production equipment and technologies, including high-precision CNC machining equipment, automated production lines, and advanced quality control devices to ensure product quality and production efficiency.
- Professional Technical Team: We have an experienced and highly skilled team, including engineers, technicians, and quality control experts, who can provide customized solutions and technical support to meet specific customer requirements.
- Strict Quality Control: We strictly adhere to a quality management system, from raw material procurement and production manufacturing to finished product testing, to ensure that every process and batch of products meet standard requirements, ensuring stable and reliable product quality.
- Flexible Production Capacity: We have flexible production capacity to accommodate both small-batch customized production according to customer needs and large-scale production orders, to adapt to the requirements of different customers and market changes.
In summary, our company has the technical strength, production capacity, and quality assurance system required for the production of LED ceramic substrates. We can provide high-quality, customized LED ceramic substrate products to customers and are committed to cooperating with them to promote the development and advancement of the LED industry.
What are the 7 qualities of good customer service?
Good customer service is characterized by several key qualities that contribute to positive interactions and experiences for customers. Here are seven qualities of good customer service:
- Responsiveness: Good customer service involves being prompt and attentive to customer inquiries, requests, and concerns. Responding quickly to customer needs demonstrates a commitment to addressing their issues and providing timely assistance.
- Empathy: Empathy is the ability to understand and share the feelings of others. Good customer service representatives show empathy by listening actively to customers, acknowledging their emotions, and demonstrating understanding and compassion for their situations.
- Professionalism: Professionalism entails maintaining a courteous and respectful demeanor in all interactions with customers. Good customer service representatives conduct themselves professionally, remain calm and composed, and uphold company standards and values.
- Knowledgeability: Good customer service requires having a thorough understanding of the products or services offered by the company. Customer service representatives should be knowledgeable about the features, benefits, and usage of the products or services to provide accurate information and assistance to customers.
- Adaptability: Every customer interaction is unique, and good customer service involves adapting to the specific needs and preferences of each customer. Customer service representatives should be flexible and resourceful, capable of adjusting their approach to accommodate different personalities, communication styles, and situations.
- Problem-solving Skills: Good customer service involves effectively resolving customer issues and concerns in a timely and satisfactory manner. Customer service representatives should possess strong problem-solving skills, identify root causes of problems, propose viable solutions, and follow through to ensure resolution.
- Follow-up and Follow-through: Good customer service doesn’t end with the initial interaction—it involves following up with customers to ensure their needs have been met and their issues resolved satisfactorily. Customer service representatives should follow through on commitments, communicate proactively with customers, and take ownership of issues until they are fully resolved.
By embodying these qualities, businesses can cultivate positive relationships with customers, build trust and loyalty, and ultimately, contribute to their long-term success.
FAQs
What is an LED ceramic substrate?
An LED ceramic substrate is a material used as a base for mounting and connecting LED chips. It is typically made from ceramic materials like aluminum nitride (AlN) or aluminum oxide (Al2O3) due to their excellent thermal conductivity and electrical insulation properties.
Why are LED ceramic substrates used?
LED ceramic substrates are used to provide a stable platform for mounting LED chips and ensuring efficient heat dissipation. They help maintain optimal operating temperatures for LED chips, which is crucial for their performance and longevity.
How are LED ceramic substrates manufactured?
The manufacturing process typically involves steps such as material selection, substrate preparation, metallization, die attachment, wire bonding, encapsulation (optional), and testing. Advanced techniques like sintering and thin-film deposition may be used to produce ceramic substrates with the desired properties.
What applications are LED ceramic substrates used in?
LED ceramic substrates find applications in various industries, including lighting (e.g., LED bulbs, fixtures), displays (e.g., LED screens, signage), automotive lighting, electronics, and more.
Can LED ceramic substrates be customized?
Yes, LED ceramic substrates can be customized to meet specific requirements for size, shape, thermal conductivity, electrical properties, and other factors. Customization allows for tailored solutions to different LED applications.
Where can LED ceramic substrates be purchased?
LED ceramic substrates can be purchased from specialized manufacturers, distributors, or suppliers of LED components and materials. It’s important to choose a reputable supplier with experience in producing high-quality ceramic substrates for LED applications.