LED Ceramic Substrate Manufacturer
LED Ceramic Substrate Manufacturer,LED ceramic substrates serve as a critical component in LED technology, providing a robust platform for mounting and interconnecting LED chips. Made from materials like aluminum oxide, aluminum nitride, or silicon nitride, these substrates excel in thermal management, efficiently dissipating heat to prolong the life and enhance the performance of LEDs. Their excellent electrical insulation properties also ensure reliable operation in various lighting applications. Used widely in high-power LED modules, LED ceramic substrates are key to achieving high efficiency and reliability in modern lighting solutions, making them indispensable in sectors ranging from automotive to general illumination.
What is an LED Ceramic Substrate?
An LED ceramic substrate is a base material used for constructing light-emitting diodes (LEDs). It serves as a foundation upon which LED chips are mounted and connected to create LED packages. The substrate is typically made of a ceramic material such as aluminum oxide (Al2O3) or aluminum nitride (AlN), which offer excellent thermal conductivity and electrical insulation properties.
LED ceramic substrates play a crucial role in LED performance and longevity by efficiently dissipating heat generated during operation. This helps to maintain the optimal operating temperature of the LED chips, which is essential for maximizing brightness and lifespan.
Ceramic substrates are also advantageous because they are more robust and reliable compared to traditional materials like printed circuit boards (PCBs) for high-power LED applications. They can withstand higher temperatures and provide better thermal management, making them ideal for demanding environments where heat dissipation is critical.
Overall, LED ceramic substrates contribute to the efficiency, reliability, and longevity of LED lighting systems.
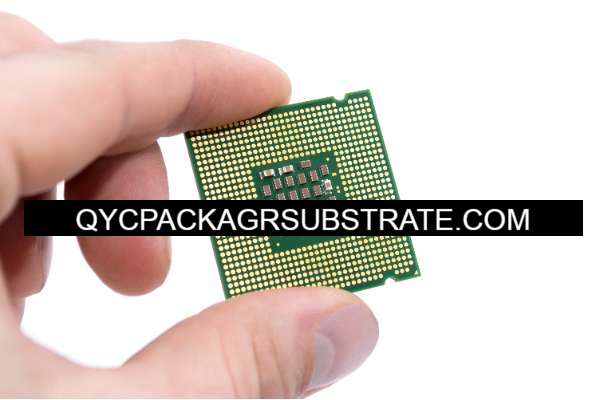
LED Ceramic Substrate Manufacturer
What are the LED Ceramic Substrate Design Guidelines?
Design guidelines for LED ceramic substrates typically focus on optimizing thermal management, electrical connectivity, and mechanical stability to ensure the performance and reliability of LED packages. Here are some key design considerations:
- Thermal Management:Efficient heat dissipation is critical to maintain LED performance and longevity. Design the substrate to have high thermal conductivity to effectively transfer heat away from the LED chips. Consider the thickness and material composition of the substrate to optimize thermal conductivity while ensuring mechanical robustness.
- Material Selection: Choose ceramic materials with high thermal conductivity, such as aluminum oxide (Al2O3) or aluminum nitride (AlN). These materials offer excellent thermal properties and electrical insulation, crucial for LED applications.
- Dielectric Properties: Ensure that the ceramic substrate provides adequate electrical insulation between conductive traces and LED chips to prevent short circuits and electrical failures.
- Layout and Interconnects: Design the substrate layout to accommodate the placement and interconnection of LED chips, as well as any additional components like resistors or capacitors. Optimize trace routing to minimize electrical losses and ensure uniform current distribution.
- Solderability: Choose substrate materials and surface finishes that facilitate reliable soldering of LED chips and electrical components. Proper solderability is essential for ensuring good electrical connections and mechanical stability.
- Mechanical Stability:Design the substrate to withstand mechanical stresses, such as thermal expansion and contraction, during operation. Consider the coefficient of thermal expansion (CTE) compatibility between the substrate and other materials in the LED package to minimize mechanical failures.
- Environmental Considerations: Take into account environmental factors such as humidity, temperature variations, and chemical exposure that may affect the performance and reliability of LED packages. Choose substrate materials and coatings that offer resistance to environmental degradation.
- Manufacturability: Design the substrate with manufacturability in mind, considering factors such as ease of fabrication, assembly, and testing. Optimize design features to streamline the manufacturing process and reduce production costs.
By adhering to these design guidelines, LED ceramic substrates can be effectively engineered to meet the performance, reliability, and manufacturability requirements of LED lighting applications.
What is the LED Ceramic Substrate Fabrication Process?
The fabrication process for LED ceramic substrates involves several steps to create the base material upon which LED chips are mounted and connected. Here’s a general overview of the typical fabrication process:
- Material Selection: The process begins with selecting the appropriate ceramic material for the substrate, such as aluminum oxide (Al2O3) or aluminum nitride (AlN), based on the desired thermal conductivity, electrical insulation, and mechanical properties.
- Substrate Preparation: The ceramic material is typically supplied in the form of sheets or plates. The substrate surface may undergo cleaning and preparation steps to remove any contaminants and ensure proper adhesion of subsequent layers.
- Layer Deposition: Thin film deposition techniques, such as physical vapor deposition (PVD) or chemical vapor deposition (CVD), may be used to deposit conductive metal layers (e.g., copper, silver) onto the substrate surface. These metal layers will serve as the conductive traces for electrical connectivity.
- Pattern Transfer: A photolithography process is employed to transfer the desired circuit patterns onto the metal layers. This involves coating the substrate with a photoresist material, exposing it to UV light through a photomask containing the circuit pattern, and developing the photoresist to reveal the patterned metal layers.
- Etching: The exposed metal areas are selectively etched away using chemical etchants, leaving behind the desired conductive traces on the substrate surface. This process defines the electrical pathways for connecting LED chips and other components.
- Surface Finishing: Surface finishing processes may be applied to the substrate to improve solderability and facilitate component attachment. This may involve applying a solder mask or surface metallization to protect the conductive traces and provide solderable surfaces.
- Quality Control and Testing: The fabricated substrates undergo rigorous quality control and testing to ensure dimensional accuracy, electrical continuity, and reliability. This may include visual inspection, electrical testing, and thermal performance characterization.
- Packaging and Assembly: Once the substrates pass quality control, they are ready for LED chip mounting and assembly. LED chips are attached to the substrate using soldering or bonding techniques, and additional components (e.g., resistors, capacitors) may be integrated as needed. The assembled LED packages are then encapsulated to protect the components and provide optical properties.
Overall, the fabrication process for LED ceramic substrates involves a combination of material preparation, deposition, patterning, and assembly steps to create robust and reliable substrates for LED applications.
How do you manufacture LED Ceramic Substrates?
Manufacturing LED ceramic substrates involves several key steps to produce the base material on which LED chips are mounted and connected. Here’s an overview of the typical manufacturing process:
- Material Selection:The process begins with selecting the appropriate ceramic material for the substrate, such as aluminum oxide (Al2O3) or aluminum nitride (AlN), based on desired thermal conductivity, electrical insulation, and mechanical properties.
- Forming: The chosen ceramic material is typically supplied in the form of sheets, plates, or discs. These raw ceramic substrates may undergo a forming process to achieve the desired size and shape for LED applications. Forming techniques may include cutting, punching, or laser machining.
- Surface Preparation: The substrate surfaces are cleaned and prepared to remove any contaminants and ensure proper adhesion of subsequent layers. Surface preparation may involve methods such as degreasing, rinsing, and drying.
- Thin Film Deposition: Thin film deposition techniques are used to deposit conductive metal layers (e.g., copper, silver) onto the substrate surface. These metal layers will serve as the conductive traces for electrical connectivity in the LED package. Common deposition methods include physical vapor deposition (PVD) or chemical vapor deposition (CVD).
- Photolithography and Etching:A photolithography process is employed to transfer the desired circuit patterns onto the metal layers. This involves coating the substrate with a photoresist material, exposing it to UV light through a photomask containing the circuit pattern, and developing the photoresist to reveal the patterned metal layers. The exposed metal areas are then selectively etched away using chemical etchants, leaving behind the desired conductive traces on the substrate surface.
- Surface Finishing: Surface finishing processes may be applied to the substrate to improve solderability and facilitate component attachment. This may involve applying a solder mask or surface metallization to protect the conductive traces and provide solderable surfaces.
- Quality Control and Testing: The fabricated substrates undergo rigorous quality control and testing to ensure dimensional accuracy, electrical continuity, and reliability. This may include visual inspection, electrical testing, and thermal performance characterization.
- Packaging and Assembly: Once the substrates pass quality control, they are ready for LED chip mounting and assembly. LED chips are attached to the substrate using soldering or bonding techniques, and additional components (e.g., resistors, capacitors) may be integrated as needed. The assembled LED packages are then encapsulated to protect the components and provide optical properties.
Throughout the manufacturing process, careful attention is paid to controlling process parameters, maintaining cleanliness, and ensuring consistency to produce high-quality LED ceramic substrates suitable for a variety of LED applications.
How much should an LED Ceramic Substrate cost?
The cost of an LED ceramic substrate can vary depending on several factors, including the substrate size, material composition, complexity of design, manufacturing processes involved, and the quantity ordered.
Generally, LED ceramic substrates are more expensive compared to traditional printed circuit boards (PCBs) due to the use of specialized ceramic materials with high thermal conductivity and electrical insulation properties. Additionally, the fabrication processes for ceramic substrates, such as thin film deposition and photolithography, can be more complex and costly compared to standard PCB manufacturing techniques.
As a rough estimate, the cost of a basic LED ceramic substrate for small-scale production runs could range from a few dollars to several tens of dollars per unit. However, for large-scale production orders, the cost per unit may decrease significantly due to economies of scale.
It’s essential to consider the overall cost of the LED package, including the cost of other components such as LED chips, drivers, and encapsulation materials, when evaluating the cost-effectiveness of LED ceramic substrates. Additionally, factors such as quality, reliability, and performance should be taken into account when determining the value proposition of LED ceramic substrates for specific applications.
What is LED Ceramic Substrate base material?
The base materials used for LED ceramic substrates are typically selected for their excellent thermal conductivity, electrical insulation properties, and mechanical strength. The most commonly used ceramic materials for LED substrates are:
- Aluminum Oxide (Al2O3): Also known as alumina, this is one of the most widely used ceramic materials for LED substrates. It has good thermal conductivity, typically around 20-30 W/m·K, and excellent electrical insulation properties. Alumina is also cost-effective and provides sufficient mechanical strength for many LED applications.
- Aluminum Nitride (AlN): This material offers superior thermal conductivity, generally in the range of 170-230 W/m·K, making it highly effective for heat dissipation in high-power LED applications. AlN also provides excellent electrical insulation and good mechanical properties. However, it is more expensive than alumina.
- Silicon Nitride (Si3N4): Silicon nitride has good thermal conductivity (about 70-90 W/m·K) and exceptional mechanical strength, making it suitable for applications where mechanical reliability is critical. It also offers good electrical insulation. Like AlN, silicon nitride is relatively expensive.
- Beryllium Oxide (BeO):Beryllium oxide has very high thermal conductivity, around 260 W/m·K, and good electrical insulation properties. However, its use is limited due to toxicity concerns during manufacturing and handling, making it less common than Al2O3 and AlN.
When selecting the base material for an LED ceramic substrate, manufacturers consider factors such as the required thermal management, electrical insulation, mechanical strength, and cost. The choice of material impacts the performance, reliability, and cost-effectiveness of the final LED package.
Which company manufactures LED Ceramic Substrates?
Manufacturing LED ceramic substrates is a complex process involving multiple industries, so there are many companies playing important roles in this field worldwide. Renowned LED ceramic substrate manufacturers include CeramTec from the United States, Murata Manufacturing from Japan, and Rogers Corporation from Europe. These companies provide high-quality ceramic substrates for the LED industry, using advanced materials and manufacturing technologies to produce various types of LED lighting products.
As a company dedicated to LED ceramic substrate manufacturing, we are committed to providing customers with high-quality and reliable LED ceramic substrate solutions. Equipped with advanced manufacturing equipment and a skilled technical team, we can meet the demands of customers for LED ceramic substrates of various specifications and requirements.
Our core competitive advantages include:
- High-Quality Materials: We select premium ceramic materials such as aluminum oxide (Al2O3) or aluminum nitride (AlN) with excellent thermal conductivity and electrical insulation properties.
- Advanced Manufacturing Technology: We employ advanced manufacturing techniques including thin film deposition, photolithography, and etching to ensure LED ceramic substrates have precise circuit patterns and excellent thermal management performance.
- Customized Solutions:We offer customized LED ceramic substrate solutions tailored to customer requirements, including different sizes, shapes, thicknesses, and circuit designs.
- Quality Control: We strictly adhere to quality control standards to ensure that every LED ceramic substrate meets customer specifications, and we ensure product reliability and stability through rigorous testing.
- Fast Delivery: With efficient production processes and supply chain management systems, we guarantee timely delivery of customer orders to meet their urgent product demands.
In summary, our company provides reliable ceramic substrate solutions for the LED industry with high-quality products, advanced manufacturing technology, and professional services. We are committed to collaborating with customers to advance the development and application of LED lighting technology.
What are the 7 qualities of good customer service?
Good customer service is characterized by several key qualities that help foster positive relationships with customers and ensure their satisfaction. Here are seven qualities of good customer service:
- Responsiveness: Good customer service involves being prompt and responsive to customer inquiries, requests, and concerns. This means acknowledging customer communication quickly and providing timely assistance or resolution to their issues.
- Empathy: Empathy is the ability to understand and share the feelings of others. Good customer service representatives demonstrate empathy by actively listening to customers, acknowledging their emotions, and showing genuine concern for their needs and concerns.
- Professionalism: Professionalism encompasses behaving in a courteous, respectful, and knowledgeable manner when interacting with customers. Good customer service representatives maintain professionalism by adhering to company policies, communicating clearly and effectively, and demonstrating competence in addressing customer inquiries or problems.
- Flexibility: Good customer service involves being flexible and adaptable to meet the diverse needs and preferences of customers. This may include accommodating special requests, offering personalized solutions, or being willing to make exceptions within reason to ensure customer satisfaction.
- Problem-solving skills: Effective problem-solving skills are essential for resolving customer issues and conflicts efficiently and effectively. Good customer service representatives possess strong analytical abilities, creativity, and resourcefulness to identify and implement solutions that meet customers’ needs and expectations.
- Consistency: Consistency is key to providing a positive customer service experience. Good customer service is consistent across all interactions and touchpoints, ensuring that customers receive the same level of quality service every time they engage with the company.
- Follow-up: Following up with customers after resolving their inquiries or concerns demonstrates a commitment to their satisfaction and helps build long-term relationships. Good customer service includes following up to ensure that customers’ needs have been met, soliciting feedback on their experience, and addressing any remaining issues or questions they may have.
By embodying these qualities, businesses can deliver exceptional customer service that fosters loyalty, enhances brand reputation, and drives customer satisfaction and retention.
FAQs (Frequently Asked Questions)
Why are ceramic substrates used for LEDs?
Ceramic substrates are preferred for LEDs because they offer excellent thermal conductivity, electrical insulation, and mechanical stability. This helps in efficient heat dissipation, which is crucial for maintaining LED performance and longevity.
What are the advantages of LED ceramic substrates over other materials?
LED ceramic substrates offer superior thermal management capabilities compared to traditional materials like printed circuit boards (PCBs). They can withstand higher temperatures and provide better heat dissipation, making them ideal for high-power LED applications.
What types of ceramic materials are used for LED substrates?
Common ceramic materials used for LED substrates include aluminum oxide (Al2O3), aluminum nitride (AlN), and silicon nitride (Si3N4). These materials offer varying degrees of thermal conductivity, electrical insulation, and mechanical strength.
How are LED ceramic substrates manufactured?
LED ceramic substrates are typically manufactured using processes such as thin film deposition, photolithography, and etching to create conductive traces and circuit patterns on the ceramic surface. The substrates are then processed and assembled to mount LED chips and other components.
What factors should be considered when selecting LED ceramic substrates?
When selecting LED ceramic substrates, factors such as thermal conductivity, electrical insulation, mechanical strength, size, shape, and cost should be considered to ensure optimal performance and compatibility with specific LED applications.
Can LED ceramic substrates be customized for specific requirements?
Yes, LED ceramic substrates can be customized to meet specific size, shape, thickness, and circuit design requirements. Manufacturers often offer customization services to tailor substrates to the needs of individual customers and applications.
Are LED ceramic substrates environmentally friendly?
LED ceramic substrates are generally considered environmentally friendly due to their long lifespan, recyclability, and non-toxic nature. Additionally, the efficient thermal management provided by ceramic substrates contributes to energy savings and reduced environmental impact in LED lighting applications.