Megtron6 Materials PCB Manufacturer
Megtron6 Materials PCB Manufacturer and package substrate Manufacturer. We use advanced Msap and Sap technology, High multilayer interconnection substrates from 4 to 18 layers,
Megtron6 Materials PCBs represent the pinnacle of high-performance printed circuit board technology. Engineered by Panasonic Corporation, Megtron6 is a cutting-edge epoxy-based laminate material renowned for its exceptional electrical properties, thermal conductivity, and mechanical strength. With a low dielectric constant and loss, Megtron6 ensures precise signal transmission, making it ideal for high-speed digital and RF applications where signal integrity is paramount. Its high thermal conductivity facilitates efficient heat dissipation, enhancing the reliability and longevity of electronic devices, even under demanding operating conditions. Additionally, Megtron6 boasts excellent dimensional stability and mechanical strength, ensuring the PCB maintains its integrity and reliability over time. Whether in telecommunications, aerospace, automotive electronics, or high-speed computing, Megtron6 Materials PCBs deliver unparalleled performance, meeting the stringent requirements of today’s most advanced electronic systems.
What is a Megtron6 Materials PCB?
Megtron6 is a type of high-performance material used in printed circuit boards (PCBs). PCBs are essential components in electronic devices, providing the necessary structure and connections for electrical components to function together. Megtron6 material offers several advantages over traditional PCB materials, making it particularly suitable for demanding applications.
Firstly, Megtron6 is known for its excellent electrical properties. It has low dielectric constant and loss, which means it can efficiently transmit electrical signals with minimal distortion or attenuation. This is crucial in high-speed digital and RF (radio frequency) circuits where signal integrity is paramount.
Moreover, Megtron6 exhibits superior thermal conductivity compared to standard PCB materials. This helps dissipate heat generated by components more effectively, reducing the risk of overheating and ensuring the reliability and longevity of the electronics.
Additionally, Megtron6 offers good dimensional stability, which means it maintains its shape and size even under varying temperature and humidity conditions. This stability is essential for precise manufacturing processes and ensures that the PCB maintains its integrity throughout its lifespan.
Furthermore, Megtron6 has excellent mechanical strength and durability, making it resistant to bending, flexing, and vibration. This makes it suitable for applications where the PCB may be subjected to harsh environmental conditions or mechanical stress.
Overall, Megtron6 materials PCBs are favored in high-performance electronic devices such as telecommunications equipment, aerospace systems, high-speed computing devices, and automotive electronics, where reliability, signal integrity, and thermal management are critical requirements. While Megtron6 may come at a higher cost compared to traditional PCB materials, its performance benefits often justify the investment in demanding applications.
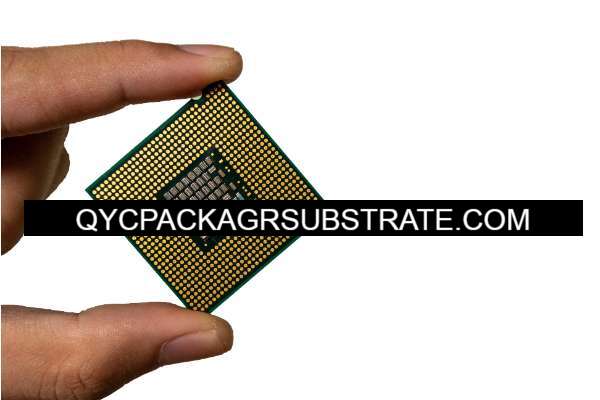
Megtron6 Materials PCB Manufacturer
What are the Megtron6 Materials PCB Design Guidelines?
Designing a PCB using Megtron6 materials requires careful consideration of its unique properties and characteristics to ensure optimal performance and reliability. Here are some general design guidelines for working with Megtron6 materials:
- Signal Integrity Considerations: Megtron6 offers excellent signal integrity properties, but high-speed digital and RF designs may still require controlled impedance traces. Follow recommended trace width, spacing, and layer stackup guidelines to maintain signal integrity and minimize signal loss.
- Thermal Management: Utilize the superior thermal conductivity of Megtron6 to dissipate heat effectively from high-power components. Place thermal vias strategically to improve heat transfer to inner layers and thermal relief pads for components connected to large copper pours.
- Dimensional Stability: Megtron6 has good dimensional stability, but thermal expansion and contraction can still affect the PCB’s performance. Minimize temperature gradients across the board and avoid placing components with significantly different coefficients of thermal expansion (CTE) close to each other.
- Mechanical Design: Design the PCB with mechanical strength and durability in mind, especially for applications subjected to mechanical stress or vibration. Reinforce areas around mounting holes, connectors, and any components likely to experience mechanical loading.
- Layer Stackup Optimization: Optimize the layer stackup to meet the specific requirements of your design while taking advantage of Megtron6’s properties. Consider the number of signal layers, power and ground plane distribution, and impedance control requirements.
- Copper Plating and Thickness:Megtron6 supports thicker copper plating for improved current carrying capacity and better thermal management. Specify appropriate copper thicknesses for power and ground planes, signal traces, and vias based on the application’s requirements.
- Manufacturability: Ensure that the PCB design is manufacturable within the capabilities of PCB fabrication processes. Follow standard design rules for minimum trace width, spacing, annular ring sizes, and other manufacturing constraints.
- Environmental Considerations: If the PCB will be used in harsh environments with exposure to moisture, chemicals, or other contaminants, select surface finishes and solder mask materials compatible with Megtron6 to enhance its durability and reliability.
- Compliance and Standards: Verify that the PCB design complies with relevant industry standards and regulations governing electrical safety, electromagnetic compatibility (EMC), and environmental requirements.
- Simulation and Testing: Use simulation tools to analyze signal integrity, thermal performance, and mechanical stress factors before fabrication. Conduct thorough testing of prototypes to validate the design’s performance under real-world conditions.
By following these guidelines and leveraging the unique properties of Megtron6 materials, you can design PCBs that meet the demanding requirements of high-performance electronic applications while ensuring reliability and longevity.
What is the Megtron6 Materials PCB Fabrication Process?
The fabrication process for a PCB using Megtron6 materials is similar to that of traditional PCBs, but with some considerations specific to the properties of Megtron6. Here’s a general overview of the fabrication process:
- Preparation of Design Files: The fabrication process begins with the preparation of design files using PCB design software. These files include the PCB layout, layer stackup information, drill files, and any other necessary documentation.
- Material Selection: Select Megtron6 laminate materials suitable for the intended application based on factors such as thickness, copper foil type, and surface finish compatibility.
- Layer Stackup Design: Design the layer stackup based on the specific requirements of the PCB design, taking into account signal integrity, thermal management, and mechanical strength considerations. Ensure that the Megtron6 layers are properly aligned and bonded together.
- Image Transfer: Transfer the PCB layout onto the Megtron6 laminate using a process called imaging. This typically involves printing the circuit pattern onto a photosensitive material called a photoresist and then exposing it to UV light through a film mask containing the PCB pattern.
- Etching: Etch away the unwanted copper from the Megtron6 substrate using chemical etchants, leaving behind the desired circuit traces. The photoresist acts as a mask, protecting the copper traces during the etching process.
- Drilling: Drill holes at specified locations for through-hole components and vias using precision drilling machines. Ensure that the drill diameters and tolerances are within the design specifications.
- Plating: Plate the drilled holes with conductive materials such as copper to establish electrical connections between different layers of the PCB. This process, known as electroplating, forms the vias and through-hole interconnects.
- Surface Finishing: Apply surface finishes to protect the exposed copper traces from oxidation and facilitate soldering during assembly. Common surface finishes for Megtron6 PCBs include ENIG (Electroless Nickel Immersion Gold), HASL (Hot Air Solder Leveling), and OSP (Organic Solderability Preservatives).
- Solder Mask Application: Apply a solder mask over the entire PCB surface, leaving openings only for component pads and vias. The solder mask protects the copper traces from environmental damage and prevents solder bridges during assembly.
- Silkscreen Printing: Optionally, apply a silkscreen layer to the PCB surface to indicate component placement, polarity markings, and other important information. This layer is typically printed using white ink for visibility.
- Final Inspection and Testing: Conduct a thorough inspection of the fabricated PCB to ensure that it meets the design specifications and quality standards. Test the electrical continuity, insulation resistance, and other relevant parameters to verify the functionality and reliability of the PCB.
Once the fabrication process is complete and the PCB passes inspection and testing, it is ready for assembly with electronic components to form a functional electronic device.
How Do You Manufacture a Megtron6 Materials PCB?
Manufacturing a PCB using Megtron6 materials involves several steps, similar to the fabrication process for traditional PCBs. Here’s a detailed overview of the manufacturing process specific to Megtron6 materials:
- Material Selection: Choose Megtron6 laminate materials suitable for the intended application based on factors such as thickness, dielectric constant, thermal conductivity, and mechanical strength. Megtron6 laminates are typically supplied by manufacturers in standard sheet sizes.
- Preparation of Design Files: Use PCB design software to create the PCB layout and generate design files, including the Gerber files, drill files, and any other necessary documentation. Ensure that the design meets the specific requirements of the application and complies with industry standards.
- Panelization: Arrange multiple PCB designs into a panel layout for efficient manufacturing. Panelization helps optimize material usage and facilitates automated manufacturing processes such as imaging, etching, and drilling.
- Imaging: Transfer the PCB layout onto the Megtron6 laminate sheets using a process called imaging. This involves printing the circuit pattern onto a light-sensitive photoresist material using a film mask and exposing it to UV light. The UV light hardens the exposed areas of the photoresist, leaving the circuit pattern behind.
- Developing: Remove the unexposed photoresist using a developing solution, leaving behind the desired circuit traces on the Megtron6 substrate. This process reveals the copper layers that will form the conductive pathways on the PCB.
- Etching: Etch away the unwanted copper from the Megtron6 substrate using chemical etchants. The photoresist acts as a mask, protecting the copper traces during the etching process. The result is a patterned copper layer that corresponds to the desired circuit layout.
- Drilling: Drill holes at specified locations for through-hole components and vias using precision drilling machines. Megtron6 materials require special attention during drilling due to their high mechanical strength and thermal conductivity. Use carbide drills and appropriate drilling parameters to ensure clean and precise holes.
- Plating: Plate the drilled holes with conductive materials such as copper to establish electrical connections between different layers of the PCB. This process, known as electroplating or through-hole plating, forms the vias and through-hole interconnects required for multi-layer PCBs.
- Surface Finishing: Apply a surface finish to protect the exposed copper traces from oxidation and facilitate soldering during assembly. Common surface finishes for Megtron6 PCBs include ENIG (Electroless Nickel Immersion Gold), HASL (Hot Air Solder Leveling), and OSP (Organic Solderability Preservatives).
- Solder Mask Application: Apply a solder mask over the entire PCB surface, leaving openings only for component pads and vias. The solder mask protects the copper traces from environmental damage and prevents solder bridges during assembly.
- Silkscreen Printing: Optionally, apply a silkscreen layer to the PCB surface to indicate component placement, polarity markings, and other important information. This layer is typically printed using white ink for visibility.
- Final Inspection and Testing:Conduct a thorough inspection of the manufactured PCB to ensure that it meets the design specifications and quality standards. Test the electrical continuity, insulation resistance, and other relevant parameters to verify the functionality and reliability of the PCB.
Once the Megtron6 PCBs pass inspection and testing, they are ready for assembly with electronic components to form functional electronic devices.
How Much Should a Megtron6 Materials PCB Cost?
The cost of a Megtron6 materials PCB can vary depending on several factors including the complexity of the design, the size of the board, the number of layers, the quantity ordered, and the manufacturer’s pricing structure. Megtron6 is a high-performance material, which typically comes at a higher cost compared to standard FR-4 or other materials used in PCB fabrication.
As a rough estimate, the cost of a Megtron6 PCB can range from $50 to $500 or more per square foot, depending on the aforementioned factors. This cost may increase for PCBs with high layer counts, fine pitch components, impedance-controlled traces, and other advanced features.
It’s essential to consider the trade-offs between cost and performance when choosing Megtron6 for a PCB project. While Megtron6 offers superior electrical properties, thermal conductivity, and mechanical strength compared to other materials, the higher cost may not be justified for every application. It’s important to assess the specific requirements of your project and weigh them against the cost implications to make an informed decision. Additionally, obtaining quotes from multiple PCB manufacturers can help you get a better understanding of the potential cost range for your Megtron6 PCBs.
What is Megtron6 Materials PCB Base Material?
Megtron6 is a high-performance epoxy-based laminate material used as the base material for PCBs. It is manufactured by the company Panasonic Corporation, specifically under their brand name “Megtron.”
The base material of Megtron6 consists of a reinforced glass fabric substrate impregnated with epoxy resin. This substrate provides the structural foundation for the PCB and contributes to its mechanical strength and dimensional stability. Additionally, Megtron6 incorporates advanced additives and fillers to enhance its electrical properties, thermal conductivity, and reliability.
Key characteristics of Megtron6 base material include:
- Low Dielectric Constant and Loss: Megtron6 exhibits low dielectric constant (εr) and dielectric loss (tan δ), making it suitable for high-frequency applications where signal integrity is critical.
- High Thermal Conductivity:Megtron6 has superior thermal conductivity compared to standard FR-4 materials, allowing for efficient heat dissipation from high-power components and improving the overall thermal management of the PCB.
- Excellent Dimensional Stability: Megtron6 offers good dimensional stability over a wide range of temperatures and humidity levels, minimizing the risk of warping or distortion during fabrication and operation.
- High Mechanical Strength: Megtron6 is engineered to have high mechanical strength and rigidity, making it resistant to bending, flexing, and mechanical stress. This ensures the reliability and durability of the PCB in demanding environments.
- Compatibility with High-Speed Designs: Due to its excellent electrical and thermal properties, Megtron6 is well-suited for high-speed digital and RF (radio frequency) designs that require precise signal transmission and minimal signal loss.
Overall, Megtron6 base material provides a robust foundation for manufacturing high-performance PCBs that meet the demanding requirements of modern electronic applications, such as telecommunications, aerospace, automotive, and computing systems.
Which Company Makes Megtron6 Materials PCB?
Megtron6 materials are manufactured by Panasonic Corporation. As a globally renowned electronics manufacturer, Panasonic has extensive experience and advanced technology dedicated to providing high-quality, high-performance PCB materials. Megtron6, one of their high-performance PCB materials, boasts excellent electrical properties, thermal conductivity, and mechanical strength, suitable for various demanding electronic applications.
At our company, we also produce PCBs using Megtron6 materials. Equipped with advanced manufacturing equipment and an experienced technical team, we can meet the demands for high-performance PCBs. Our production process strictly adheres to industry standards, with quality control at every stage from material selection and design confirmation to production processing, ensuring customers receive satisfactory products.
Our team possesses rich experience and can provide customized designs according to specific customer requirements, offering professional technical support and top-notch services. We are committed to establishing long-term partnerships with customers, providing reliable solutions to help them stand out in the market competition.
Whether in fields like telecommunications, aerospace, automotive electronics, or computing systems, we can deliver high-quality Megtron6 materials PCBs to meet customers’ design and performance requirements. We look forward to cooperating with customers, achieving mutual development, and creating win-win situations!
What Are the 7 Qualities of Good Customer Service?
Good customer service is essential for building positive relationships with customers and fostering loyalty. Here are seven qualities that characterize good customer service:
- Responsiveness: Good customer service involves being prompt and responsive to customer inquiries, concerns, and requests. Customers appreciate timely assistance and solutions to their problems, whether it’s through phone calls, emails, live chat, or in-person interactions.
- Empathy: Empathy is the ability to understand and share the feelings of others. Good customer service representatives listen actively to customers, acknowledge their emotions, and show genuine concern for their needs and issues. By demonstrating empathy, companies can build trust and rapport with customers.
- Clear Communication: Effective communication is crucial in delivering good customer service. Customer service representatives should communicate clearly and concisely, using language that is easy for customers to understand. They should also provide accurate information and avoid jargon or technical terms that may confuse customers.
- Problem-Solving Skills: Good customer service involves the ability to effectively resolve customer problems and address their concerns. Customer service representatives should be resourceful, creative, and solution-oriented, finding ways to meet customer needs and exceed their expectations.
- Professionalism: Professionalism encompasses a range of qualities, including courtesy, respect, and integrity. Good customer service representatives maintain a positive attitude, remain calm and composed, and treat customers with dignity and respect, regardless of the situation.
- Product Knowledge: Having a deep understanding of the products or services offered is essential for providing good customer service. Customer service representatives should be knowledgeable about their company’s offerings, features, and benefits, enabling them to answer customer questions accurately and provide helpful recommendations.
- Follow-Up and Feedback: Good customer service doesn’t end after the initial interaction. Follow-up is important for ensuring customer satisfaction and addressing any remaining concerns. Additionally, soliciting feedback from customers allows companies to continuously improve their products and services and enhance the customer experience over time.
By embodying these qualities, companies can deliver exceptional customer service that builds loyalty, generates positive word-of-mouth, and contributes to long-term success.
FAQs
What is Megtron6?
Megtron6 is a high-performance material used in printed circuit boards (PCBs). It offers excellent electrical properties, thermal conductivity, and mechanical strength, making it suitable for demanding electronic applications.
What are the key properties of Megtron6?
Megtron6 has low dielectric constant and loss, high thermal conductivity, excellent dimensional stability, and high mechanical strength. These properties make it ideal for high-speed digital and RF applications.
What are the advantages of using Megtron6 materials PCBs?
The advantages of using Megtron6 materials include improved signal integrity, better thermal management, enhanced reliability, and suitability for high-frequency and high-power applications.
What applications are suitable for Megtron6 materials PCBs?
Megtron6 materials are commonly used in telecommunications equipment, aerospace systems, automotive electronics, high-speed computing devices, and other applications requiring high-performance PCBs.
Is Megtron6 more expensive than other PCB materials?
Yes, Megtron6 materials typically come at a higher cost compared to standard FR-4 or other materials used in PCB fabrication. However, the performance benefits often justify the investment for demanding applications.
Can Megtron6 materials PCBs be manufactured with standard PCB processes?
Yes, Megtron6 materials can be processed using standard PCB fabrication processes, but some adjustments may be necessary due to their unique properties. Manufacturers with experience in handling high-performance materials like Megtron6 can ensure proper fabrication.
Are there specific design considerations for Megtron6 materials PCBs?
Yes, designing PCBs with Megtron6 materials requires consideration of factors such as controlled impedance traces, thermal management, layer stackup optimization, and mechanical design for reliability. Following design guidelines and consulting with experienced PCB designers is recommended.
Where can I purchase Megtron6 materials PCBs?
Megtron6 materials PCBs can be purchased from PCB manufacturers or suppliers specializing in high-performance materials. It’s essential to choose a reputable manufacturer with experience in handling Megtron6 materials to ensure quality and reliability.