Metallized Ceramic Substrates Manufacturer
Metallized Ceramic Substrates Manufacturer,Metallized Ceramic Substrates are advanced electronic components designed for high-performance applications requiring superior thermal and electrical conductivity. These substrates consist of a ceramic base, typically made from materials like alumina or aluminum nitride, which is coated with a metal layer. The metalization process enhances electrical connections and provides excellent thermal dissipation, crucial for high-power and high-frequency applications. Metallized ceramic substrates are widely used in power electronics, microwave circuits, and automotive systems due to their ability to withstand extreme temperatures and harsh conditions. Their robust performance and reliability make them essential in demanding electronic environments.
What is Metallized Ceramic Substrate?
Metallized ceramic substrates are advanced materials used in electronic and electrical applications to provide robust, high-performance support for various components. These substrates consist of a ceramic base material, typically aluminum oxide (Al₂O₃) or aluminum nitride (AlN), which is coated with a thin layer of metal. The metallization process can involve various metals, including copper, silver, or nickel, depending on the specific requirements of the application.
The primary purpose of metallized ceramic substrates is to combine the high thermal conductivity and electrical insulation properties of ceramics with the excellent electrical and thermal conductivity of metals. This combination is crucial in applications where efficient heat dissipation and reliable electrical connections are essential. For instance, in high-power electronic devices such as power amplifiers, LED lighting, and automotive electronics, metallized ceramic substrates help to manage heat effectively, ensuring the longevity and stability of the components.
The metallization process typically involves sputtering, plating, or other deposition techniques to apply a thin metallic layer onto the ceramic surface. This metal layer can serve as a conductive path for electrical signals or as a thermal interface to spread heat away from sensitive areas. Additionally, the metal layer can also facilitate the attachment of electronic components through methods such as soldering or wire bonding.
Overall, metallized ceramic substrates offer a unique combination of mechanical strength, thermal and electrical performance, and durability, making them indispensable in modern electronic and electrical systems. Their ability to withstand high temperatures and harsh environments while maintaining reliable performance underscores their significance in advanced technology applications.
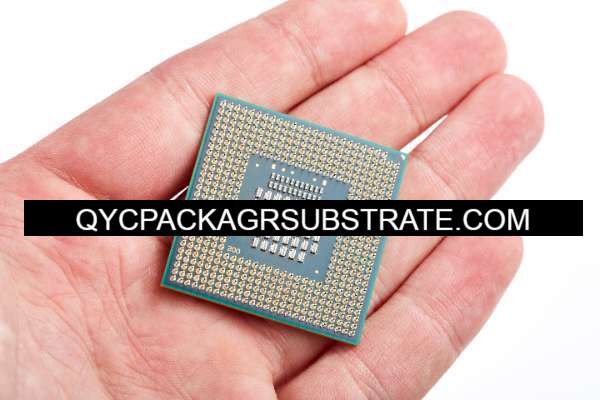
Metallized Ceramic Substrates Manufacturer
What are the Metallized Ceramic Substrates Design Guidelines?
Designing metallized ceramic substrates involves several critical guidelines to ensure optimal performance and reliability in electronic applications. These guidelines focus on material selection, design considerations, and manufacturing processes:
- Material Selection: Choose the appropriate ceramic material based on thermal conductivity, electrical insulation, and mechanical strength requirements. Common choices include aluminum oxide (Al₂O₃) for general applications and aluminum nitride (AlN) for higher thermal conductivity needs.
- Metallization Process: Select a suitable metallization technique, such as sputtering, plating, or screen printing, to apply the metal layer. The choice of metal (copper, silver, nickel) should align with the electrical and thermal conductivity requirements. Ensure that the metal layer adheres well to the ceramic and provides consistent conductivity.
- Thermal Management:Design for effective heat dissipation by optimizing the thickness and placement of the metal layer. Incorporate thermal vias or pads if necessary to enhance heat transfer from critical components. Ensure that the substrate can withstand thermal cycling and high temperatures without degradation.
- Electrical Performance: Ensure that the metal layer is designed to handle the required current densities and minimize signal loss. Consider the impedance matching and minimize parasitic inductances and capacitances by optimizing trace widths and layout.
- Mechanical Considerations: Design the substrate to accommodate thermal expansion differences between the ceramic and metal layers. Properly account for mechanical stresses to avoid delamination or cracking. Ensure that the ceramic substrate has sufficient mechanical strength to support mounted components.
- Manufacturing Tolerances: Maintain tight tolerances in both the ceramic and metal layers to ensure consistent performance and reliability. Control factors such as layer thickness, surface roughness, and alignment during the manufacturing process.
- Surface Finish: Ensure that the surface finish of the metallized areas is suitable for subsequent soldering or bonding processes. A clean, well-prepared surface is crucial for achieving strong, reliable electrical connections.
- Testing and Quality Control: Implement rigorous testing and quality control procedures to verify the performance of the metallized ceramic substrates. This includes electrical testing, thermal cycling, and visual inspections to ensure that the substrates meet all design specifications and reliability standards.
By adhering to these design guidelines, engineers can create metallized ceramic substrates that deliver high performance, durability, and reliability in demanding electronic applications.
What is the Metallized Ceramic Substrates Fabrication Process?
The fabrication process for metallized ceramic substrates involves several key steps to ensure high-quality performance and reliability in electronic applications. Here’s a detailed overview of the process:
- Substrate Preparation: Begin with the selection and preparation of the ceramic substrate material, typically aluminum oxide (Al₂O₃) or aluminum nitride (AlN). The ceramic is cut to the desired size and shape, and its surface is cleaned and polished to remove any contaminants and achieve the required smoothness.
- Surface Activation: To ensure good adhesion of the metal layer, the ceramic surface must be activated. This can involve processes such as etching or using a primer to improve the bonding between the ceramic and the metal.
- Metallization: Apply a metal layer to the activated ceramic surface. Common metallization techniques include:
– Sputtering: A physical vapor deposition (PVD) method where metal atoms are ejected from a target and deposited onto the ceramic surface.
– Plating: Electroplating or electroless plating techniques where a metal layer is deposited onto the ceramic through chemical or electrochemical reactions.
– Screen Printing: A process where metal paste is applied to the ceramic surface through a screen mask and then cured.
- Metal Layer Processing: After metallization, the metal layer may need additional processing, such as patterning to create electrical traces or pads. Techniques like photolithography or laser ablation are used to define the desired metal patterns.
- Firing: The ceramic substrate with the metallized layer is subjected to a high-temperature firing process. This step ensures that the metal adheres properly to the ceramic and achieves the required mechanical and electrical properties. The firing temperature and duration are carefully controlled to avoid damaging the substrate.
- Patterning and Etching: If the metal layer needs specific patterns or circuitry, the substrate undergoes etching. A photoresist is applied to protect areas that should remain metalized, and the exposed metal is etched away using chemical solutions. The photoresist is then removed.
- Final Processing: Additional steps may include applying a protective coating or solder mask to the metalized areas to prevent oxidation and enhance durability. The substrate is then inspected for quality, including checking the metal adhesion, pattern accuracy, and overall surface integrity.
- Cutting and Packaging: Finally, the substrate is cut to its final dimensions and packaged for delivery. The substrates are typically inspected and tested to ensure they meet all specifications and performance standards before being shipped.
By following these steps, manufacturers can produce metallized ceramic substrates with excellent thermal and electrical properties, suitable for a wide range of high-performance electronic applications.
How Do You Manufacture Metallized Ceramic Substrates?
Manufacturing metallized ceramic substrates involves several intricate steps to ensure high performance and reliability in electronic applications. Here’s an overview of the process:
- Ceramic Substrate Preparation: The process begins with the selection of appropriate ceramic materials, such as aluminum oxide (Al2O3), aluminum nitride (AlN), or silicon nitride (Si3N4). These ceramics are chosen for their excellent thermal conductivity, electrical insulation properties, and mechanical strength. The chosen ceramic material is then shaped into the desired substrate form using techniques like pressing, extrusion, or injection molding.
- Sintering: The shaped ceramic green body is subjected to a high-temperature sintering process. Sintering involves heating the ceramic material to a temperature just below its melting point, allowing the particles to fuse together and form a dense, solid substrate. This step is crucial for achieving the desired mechanical properties and ensuring the substrate’s structural integrity.
- Surface Preparation: Once sintered, the ceramic substrate’s surface is prepared for metallization. This involves cleaning the substrate to remove any impurities or contaminants and often includes etching or roughening the surface to improve the adhesion of metal layers. Techniques such as plasma treatment or chemical etching may be employed to create a suitable surface profile.
- Metallization: The metallization process involves depositing a thin layer of metal onto the ceramic substrate. There are several methods for metallization:
– Sputtering: This technique uses a high-energy plasma to eject metal atoms from a target and deposit them onto the ceramic surface.
– Electroplating: A thin metal layer is deposited onto the ceramic substrate through an electrochemical process.
– Chemical Vapor Deposition (CVD): Metal is deposited from a gaseous phase onto the ceramic substrate in a vacuum chamber.
- Patterning and Etching: After metallization, the metal layer is patterned to create the desired circuit design. This is done using photolithography, where a photosensitive coating (photoresist) is applied to the metal layer. Ultraviolet light is then used to expose and develop the photoresist, creating a mask for the subsequent etching process. Etching removes unwanted metal, leaving behind the desired circuit pattern.
- Adhesion Enhancement: To improve the adhesion of the metal layer to the ceramic substrate, additional processes such as annealing may be performed. Annealing involves heating the substrate to promote better bonding between the metal and ceramic.
- Testing and Quality Control: The final step involves rigorous testing and quality control. This includes electrical testing to ensure the integrity of the metallized circuit, thermal cycling tests to check the substrate’s performance under varying temperatures, and mechanical tests to confirm the substrate’s durability.
- Final Processing: Depending on the application, additional processing steps such as mounting, bonding, or encapsulation may be performed to integrate the metallized ceramic substrate into electronic devices.
Each of these steps is critical for ensuring that the metallized ceramic substrates meet the high standards required for modern electronic applications, including their thermal management, electrical performance, and mechanical stability.
How Much Should Metallized Ceramic Substrates Cost?
The cost of metallized ceramic substrates can vary widely depending on several factors:
- Material Type: The base ceramic material (e.g., aluminum oxide (Al2O3), aluminum nitride (AlN), or silicon nitride (Si3N4)) significantly impacts the cost. High-performance materials like AlN or Si3N4 are more expensive due to their superior thermal and electrical properties.
- Complexity of Design: The complexity of the circuit patterns and the precision required in the metallization process can influence costs. More intricate designs and tighter tolerances generally increase the cost.
- Size and Thickness: Larger substrates or those with thicker metal layers will generally be more expensive. Custom sizes and thicker substrates often require more material and processing time.
- Manufacturing Volume:Economies of scale come into play. Larger production volumes can reduce the per-unit cost due to the amortization of setup costs over a greater number of units.
- Metallization Technique: The choice of metallization method (sputtering, electroplating, or chemical vapor deposition) affects costs. High-precision methods or those requiring more advanced equipment tend to be more expensive.
- Additional Processes: Additional processes like surface treatment, patterning, and final testing add to the cost. Specialized processes and extensive quality control can further increase the price.
- Quality and Reliability: Higher quality and reliability standards, such as those required for aerospace or high-reliability electronics, can also lead to higher costs due to rigorous testing and higher-grade materials.
Ultimately, to get an accurate estimate, it’s essential to consult with manufacturers who can provide quotes based on specific requirements, including material, design complexity, and volume.
What is Metallized Ceramic Substrate Base Material?
The base material for metallized ceramic substrates is a type of high-performance ceramic that serves as the foundation for the metallization process. This base material is chosen for its combination of thermal, electrical, and mechanical properties, which are essential for the performance of electronic components. Here’s a detailed look at the common base materials used:
- Aluminum Oxide (Al2O3): Aluminum oxide, commonly known as alumina, is one of the most widely used ceramic materials for substrates. It offers excellent electrical insulation, high thermal conductivity, and good mechanical strength. Alumina substrates are cost-effective and suitable for a broad range of electronic applications. They are often used in power electronics and high-frequency circuits. The typical purity ranges from 85% to 99.9%, with higher purity grades offering better electrical and thermal performance.
- Aluminum Nitride (AlN): Aluminum nitride is another popular ceramic substrate material known for its superior thermal conductivity, often higher than that of alumina. It also provides excellent electrical insulation and has a high thermal expansion coefficient that matches well with many metals. This makes AlN particularly suitable for high-power and high-frequency applications where efficient heat dissipation is crucial. Its high thermal conductivity helps in managing the heat generated in electronic devices, improving overall performance and reliability.
- Silicon Nitride (Si3N4): Silicon nitride is a high-performance ceramic material with excellent mechanical properties, including high strength and toughness. It also provides good thermal conductivity and electrical insulation. Silicon nitride substrates are often used in applications requiring high durability and thermal shock resistance. This material is particularly advantageous in harsh environments or for components subjected to extreme temperatures.
- Beryllium Oxide (BeO):Beryllium oxide is known for its exceptional thermal conductivity and electrical insulation properties. It has a high melting point and provides excellent thermal management. However, due to its toxicity and high cost, beryllium oxide is used less frequently compared to alumina and aluminum nitride. It is typically reserved for specialized applications where its superior thermal properties are indispensable.
- Magnesium Aluminate Spinel (MgAl2O4):Spinel is another ceramic material used for specific applications. It offers a good balance of thermal and electrical properties, with advantages in certain high-temperature or high-stress environments. Spinel substrates are less common but are chosen for their particular performance characteristics in specialized electronic devices.
- Zirconia (ZrO2): Zirconia, or zirconium dioxide, is used in some high-performance applications due to its high mechanical strength, wear resistance, and thermal insulation properties. It is less commonly used compared to alumina or aluminum nitride but is valuable in niche applications requiring its specific properties.
Each of these base materials is selected based on the specific requirements of the application, including factors such as thermal management, electrical insulation, mechanical strength, and cost. The choice of base material significantly impacts the performance and reliability of the metallized ceramic substrate in electronic devices.
Which Company Makes Metallized Ceramic Substrates?
Metallized ceramic substrates are produced globally by a number of companies that are dedicated to providing high-performance solutions for a variety of electronic applications. Here are some well-known manufacturers and their features:
CTS Corporation: CTS is a leading global manufacturer of electronic components, providing various types of ceramic substrates, including metallized ceramic substrates. Their products are widely used in fields such as communications, automobiles, and medical equipment.
Kyocera Corporation: Kyocera is an internationally renowned manufacturer of electronic and ceramic materials, providing high-quality metallized ceramic substrates. Kyocera’s products are highly regarded for their superior thermal conductivity and electrical performance and are suitable for high-frequency, high-power electronic equipment.
Planar Monolithics Industries, Inc. (PMI): PMI specializes in the manufacturing of high-performance microwave and millimeter-wave components, including metallized ceramic substrates. The company is known for its precise manufacturing processes and high-reliability products, primarily serving the aerospace and defense sectors.
Rogers Corporation: Rogers Corporation produces a variety of high-performance circuit board materials, including metallized ceramic substrates. Their products are widely used in high frequency and high power applications, providing excellent thermal management and electrical performance.
NTK Ceratec: NTK Ceratec is a Japanese company specializing in manufacturing ceramic substrates. Their metallized ceramic substrates are used in various electronic and semiconductor applications and have gained market recognition for their excellent quality and reliability.
Dow Corning: In addition to silicon materials, Dow Corning also produces a variety of ceramic substrate materials, including metallized ceramic substrates. Their products are widely used in high-tech industries, providing advanced material solutions.
Our company is also able to produce metallized ceramic substrates. We use advanced manufacturing technology and strict quality control processes to ensure our substrates meet high standards in performance and reliability. Our metallized ceramic substrates have excellent thermal conductivity, electrical insulation and mechanical strength and are widely used in various electronic products and high-power electronic equipment. We are committed to providing customers with customized solutions to meet their specific needs in terms of performance, size and application environment.
What are the 7 Qualities of Good Customer Service?
Good customer service is essential for maintaining customer satisfaction and loyalty. Here are seven key qualities that define excellent customer service:
- Empathy:The ability to understand and share the feelings of the customer is crucial. Showing empathy helps in creating a connection with customers, making them feel valued and understood. It involves active listening and responding with compassion and understanding.
- Responsiveness: Timely and efficient responses to customer inquiries and issues are vital. Good customer service involves promptly addressing customer concerns, providing quick solutions, and keeping customers informed about the progress of their requests.
- Knowledgeability: A deep understanding of the products or services being offered is essential. Customer service representatives should be well-trained and knowledgeable, able to provide accurate information, answer questions, and solve problems effectively.
- Patience: Dealing with customers, especially those who are upset or confused, requires a lot of patience. Good customer service representatives remain calm and composed, giving customers the time they need to express their concerns and ensuring they feel heard and respected.
- Communication Skills: Clear, concise, and courteous communication is key to effective customer service. This includes not only verbal communication but also written communication, such as emails or chat messages. Good communication helps in conveying information accurately and building trust with customers.
- Problem-Solving Skills:The ability to quickly and effectively resolve issues is a hallmark of good customer service. Representatives should be resourceful, able to think on their feet, and find solutions that satisfy the customer while also aligning with company policies.
- Positive Attitude: Maintaining a positive and friendly demeanor can greatly enhance the customer experience. A positive attitude can turn a potentially negative interaction into a pleasant one, leaving the customer with a good impression of the company.
By embodying these qualities, customer service teams can provide exceptional service that not only meets but exceeds customer expectations, fostering loyalty and long-term satisfaction.
FAQs about Metallized Ceramic Substrates
What are Metallized Ceramic Substrates used for?
They are used in high-performance electronic devices for their excellent thermal and electrical properties.
How durable are Metallized Ceramic Substrates?
They are highly durable, with resistance to heat, corrosion, and mechanical stress.
Can Metallized Ceramic Substrates be customized?
Yes, they can be customized based on specific design and performance requirements.
What industries use Metallized Ceramic Substrates?
They are commonly used in automotive, aerospace, telecommunications, and industrial electronics.
How do I choose the right Metallized Ceramic Substrate?
Consider factors like thermal conductivity, electrical insulation, mechanical strength, and compatibility with your application.