Micro LED PCB manufacturing
Micro LED PCB Manufacturing, Ultra-small marks, ultra-thin finished board thickness, ultra-small spacing, we produce the Micro LED PCBs from 2 layer to 16 layers with 30um gaps. Micro LED PCBs, also known as Micro LED printed circuit boards, represent the pinnacle of display technology innovation. These specialized PCBs serve as the backbone for Micro LED displays, integrating thousands or even millions of microscopic LEDs onto a single substrate. Their compact design and high-density layout enable the creation of stunningly vivid and high-resolution displays with unparalleled brightness and energy efficiency.
The fabrication of Micro LED PCBs involves intricate processes to ensure precise placement and connection of the tiny LEDs. Advanced manufacturing techniques are employed to optimize thermal management, signal integrity, and overall performance. With their potential for flexible and transparent displays, Micro LED PCBs are revolutionizing industries ranging from consumer electronics to automotive displays and medical devices.
These cutting-edge PCBs offer exceptional contrast, color accuracy, and durability, making them ideal for applications where superior image quality and reliability are paramount. As technology continues to advance, Micro LED PCBs are poised to reshape the future of display technology, ushering in a new era of immersive visual experiences.
What is a Micro LED PCB?
A Micro LED PCB (Printed Circuit Board) refers to a specialized type of PCB designed specifically for Micro LED technology. Micro LED is an emerging display technology that utilizes microscopic light-emitting diodes (LEDs) to create high-resolution and high-brightness displays. These LEDs are much smaller than traditional LEDs, often measuring less than 100 micrometers in size.
A Micro LED PCB serves as the foundation for mounting and connecting these tiny LEDs. It typically consists of a substrate material, such as fiberglass or ceramic, onto which conductive traces are printed or etched. These traces provide electrical connections between the individual Micro LEDs and other electronic components, such as drivers and controllers.
The design and fabrication of Micro LED PCBs require high precision and advanced manufacturing techniques to ensure accurate placement of the tiny LEDs and reliable electrical connections. These PCBs may also incorporate additional features, such as heat dissipation mechanisms, to maintain optimal performance and reliability of the Micro LED display.
Overall, Micro LED PCBs play a crucial role in enabling the development of Micro LED displays, offering benefits such as high resolution, high brightness, energy efficiency, and potential for flexible and transparent displays.
What are Micro LED PCB Design Guidelines?
Micro LED PCB design guidelines ensure that the printed circuit board (PCB) meets the specific requirements for integrating Micro LED technology effectively. Here are some key guidelines:
- Miniaturization: Micro LED PCBs require precise and miniaturized designs to accommodate the small size of Micro LEDs. Trace widths and spacings should be carefully optimized to ensure reliable electrical connections without interference between adjacent components.
- High Density Integration: Micro LED PCBs often need to integrate a large number of Micro LEDs within a small area. Design guidelines should focus on maximizing component density while maintaining electrical isolation and signal integrity.
- Thermal Management: Efficient heat dissipation is critical for maintaining the performance and longevity of Micro LED displays. PCB designs should incorporate thermal vias, heat sinks, or other thermal management techniques to dissipate heat generated by the LEDs effectively.
- Signal Integrity: Micro LED PCBs must maintain signal integrity to ensure proper communication between the LEDs and control electronics. Design guidelines should include recommendations for minimizing signal reflections, crosstalk, and impedance mismatches.
- Flexibility and Durability: Depending on the application, Micro LED PCBs may need to be flexible or rigid. Flexible PCB designs should consider materials and manufacturing processes that ensure durability and reliability despite bending or flexing.
- Alignment and Placement: Precise alignment and placement of Micro LEDs on the PCB are crucial for achieving uniform brightness and color consistency across the display. Design guidelines should specify tolerances for LED placement and alignment features to facilitate accurate assembly.
- Manufacturability: PCB designs should be manufacturable using standard fabrication processes while meeting the specific requirements of Micro LED technology. Design guidelines should consider factors such as material selection, surface finish, and assembly techniques to ensure ease of manufacturing and assembly.
- Testing and Quality Control: Design guidelines should include provisions for testing and quality control to verify the functionality and reliability of Micro LED PCBs. This may involve testing electrical connectivity, thermal performance, and optical characteristics of the LEDs.
By adhering to these Micro LED PCB design guidelines, designers can develop PCB layouts that effectively integrate Micro LED technology and optimize the performance, reliability, and manufacturability of Micro LED displays.
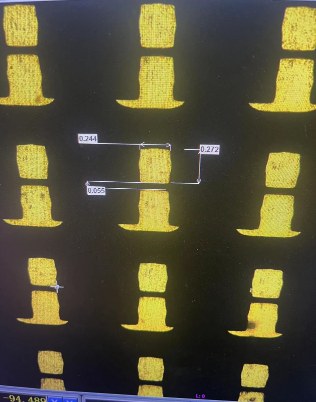
Micro LED PCB
What is the Micro LED PCB Fabrication Process?
The fabrication process for Micro LED PCBs involves several steps to create the printed circuit board that integrates Micro LED technology. Here’s an overview of the typical process:
- Design: The process begins with the design of the Micro LED PCB using computer-aided design (CAD) software. Designers create the layout of the PCB, including the placement of Micro LEDs, electrical traces, and other components. Design considerations such as miniaturization, thermal management, and signal integrity are taken into account during this phase.
- Substrate Selection: The choice of substrate material is critical for Micro LED PCBs. Common substrate materials include fiberglass (FR-4), ceramic, and flexible materials like polyimide for flexible PCBs. The substrate provides the foundation for mounting components and routing electrical connections.
- Preparation of Substrate: The substrate is cleaned and prepared for the fabrication process. This typically involves processes such as cleaning, surface treatment, and application of adhesion promoters to ensure proper adhesion of the conductive traces.
- Conductive Traces: Conductive traces are patterned onto the substrate to create the electrical connections between components. This is usually done using techniques such as etching or additive processes like screen printing, inkjet printing, or electroplating. The conductive traces may be made of copper or other metals.
- Insulating Layers: Insulating layers are applied over the conductive traces to electrically isolate them from each other and protect against short circuits. These layers are typically made of dielectric materials such as epoxy or solder mask.
- Via Formation: Vias are small holes drilled or etched into the PCB to create electrical connections between different layers of the board. For Micro LED PCBs, thermal vias may also be incorporated to aid in heat dissipation.
- Component Placement: Micro LEDs and other surface-mount components are then placed onto the PCB according to the design layout. Precision placement equipment may be used to ensure accurate positioning of the tiny Micro LEDs.
- Soldering: The components are soldered onto the PCB using techniques such as reflow soldering or solder paste deposition. Care must be taken to avoid overheating the Micro LEDs during this process.
- Testing and Inspection: Once assembly is complete, the Micro LED PCB undergoes testing and inspection to ensure functionality and quality. This may include electrical testing, visual inspection, and possibly testing of optical characteristics for Micro LED performance.
- Packaging: After passing inspection, the Micro LED PCBs may be packaged and prepared for integration into final display products.
Throughout the fabrication process, strict quality control measures are implemented to ensure that the Micro LED PCBs meet the required specifications for performance, reliability, and manufacturability.
How do you manufacture a Micro LED PCB?
Manufacturing a Micro LED PCB involves a series of specialized processes to create a printed circuit board that integrates Micro LED technology. Here’s a detailed step-by-step guide:
- Design:The process starts with designing the Micro LED PCB layout using computer-aided design (CAD) software. Designers determine the placement of Micro LEDs, electrical traces, and other components, considering factors such as miniaturization, thermal management, and signal integrity.
- Substrate Selection: Choose a suitable substrate material for the Micro LED PCB. Common options include fiberglass (FR-4), ceramic, or flexible materials like polyimide for flexible PCBs. The substrate provides the foundation for mounting components and routing electrical connections.
- Preparation of Substrate: Clean and prepare the substrate for the fabrication process. This typically involves cleaning the substrate surface, applying surface treatment, and possibly using adhesion promoters to ensure proper adhesion of the conductive traces.
- Conductive Traces Formation: Pattern conductive traces onto the substrate to create electrical connections between components. This can be achieved using techniques such as etching or additive processes like screen printing, inkjet printing, or electroplating. Conductive traces are usually made of copper or other metals.
- Insulating Layers: Apply insulating layers over the conductive traces to electrically isolate them from each other and protect against short circuits. These layers are typically made of dielectric materials such as epoxy or solder mask.
- Via Formation: Create vias, which are small holes drilled or etched into the PCB to establish electrical connections between different layers. For Micro LED PCBs, thermal vias may also be incorporated to aid in heat dissipation.
- Component Placement: Place Micro LEDs and other surface-mount components onto the PCB according to the design layout. Precision placement equipment may be used to ensure accurate positioning of the tiny Micro LEDs.
- Soldering: Solder the components onto the PCB using techniques such as reflow soldering or solder paste deposition. Special care must be taken to avoid overheating the Micro LEDs during this process.
- Testing and Inspection: Conduct testing and inspection to ensure the functionality and quality of the Micro LED PCB. This may involve electrical testing, visual inspection, and testing of optical characteristics for Micro LED performance.
- Packaging: After passing inspection, package the Micro LED PCBs and prepare them for integration into final display products.
Throughout the manufacturing process, stringent quality control measures are implemented to ensure that the Micro LED PCBs meet the required specifications for performance, reliability, and manufacturability. Additionally, specialized equipment and expertise are often necessary to handle the precise placement and assembly of Micro LEDs on the PCB.
How much should a Micro LED PCB cost?
The cost of a Micro LED PCB can vary widely depending on several factors such as:
- Size and Complexity: Larger PCBs with more complex designs typically cost more to manufacture due to increased material and manufacturing time.
- Material: The choice of substrate material can significantly impact the cost. Higher-performance materials such as ceramic or flexible substrates tend to be more expensive than standard fiberglass (FR-4).
- Layer Count: The number of layers in the PCB affects the cost, as each additional layer requires more material and fabrication steps.
- Component Density: PCBs with a higher density of components, including Micro LEDs and other electronic components, may require more precise manufacturing processes and incur higher costs.
- Manufacturing Process: The specific manufacturing techniques used, such as additive processes for creating conductive traces or advanced assembly methods for placing Micro LEDs, can influence the cost.
- Quantity: Economies of scale apply in PCB manufacturing, meaning that larger production quantities typically result in lower per-unit costs.
- Quality and Reliability Requirements: Meeting stringent quality and reliability standards may involve additional testing and inspection steps, which can increase the overall cost.
- Supplier and Location: The choice of PCB manufacturer and their location can impact costs due to differences in labor rates, overhead costs, and manufacturing capabilities.
Given these factors, it’s challenging to provide a specific cost for a Micro LED PCB without detailed information about the design, specifications, and production volume. Generally, Micro LED PCBs tend to be more expensive than traditional PCBs due to their specialized requirements and the precision involved in integrating Micro LED technology. However, as the technology matures and production volumes increase, the cost of Micro LED PCBs is expected to decrease over time.
What is Micro LED PCB base material?
The base material used for Micro LED PCBs can vary depending on the specific requirements of the application, but there are several common options:
- FR-4 (Fiberglass Epoxy): FR-4 is the most widely used substrate material for PCBs. It is a composite material made of woven fiberglass cloth impregnated with epoxy resin. FR-4 offers good mechanical strength, electrical insulation properties, and cost-effectiveness. However, it may not be suitable for applications requiring high thermal conductivity or flexibility.
- Ceramic:Ceramic substrates, such as alumina (Al2O3) or aluminum nitride (AlN), are chosen for their excellent thermal conductivity and high mechanical strength. Ceramic PCBs provide efficient heat dissipation, making them suitable for applications requiring high power or operating in harsh environments. However, they tend to be more expensive than FR-4.
- Flexible Materials: Flexible PCBs are made of flexible substrates such as polyimide (PI) or polyester (PET). These materials offer the advantage of flexibility, allowing the PCB to bend or conform to curved surfaces. Flexible PCBs are commonly used in applications where space constraints or mechanical flexibility are critical.
- Metal Core PCBs (MCPCB): Metal core PCBs feature a metal core, typically aluminum or copper, sandwiched between layers of insulating material. The metal core provides excellent thermal conductivity, making MCPCBs suitable for high-power applications that require efficient heat dissipation.
- Other Specialty Materials: In some cases, specialty materials may be used for Micro LED PCBs to meet specific requirements such as high frequency, high temperature, or enhanced mechanical properties. Examples include high-frequency laminates, high-temperature laminates, and composite materials.
The choice of base material for a Micro LED PCB depends on factors such as thermal management requirements, mechanical flexibility, electrical performance, and cost considerations. Designers must carefully evaluate these factors to select the most suitable material for their application.
Which company makes Micro LED PCBs?
Currently, there are many companies playing important roles in the manufacturing of Micro LED PCBs. Some well-known companies include Samsung, LG, Huawei, Sony, as well as some smaller companies focusing on semiconductor and display technologies. These companies have accumulated rich experience and advanced technologies in the manufacturing of Micro LED PCBs, and they continue to drive the development and application of Micro LED technology.
As a company dedicated to the electronics manufacturing industry, our company is also capable of producing high-quality Micro LED PCBs. We have advanced manufacturing equipment and a skilled technical team to meet the customized needs of our customers. Our manufacturing process strictly adheres to international standards and industry best practices to ensure product quality and reliability.
Our strengths include:
- Technical expertise: We have an experienced and skilled team capable of addressing complex manufacturing requirements for Micro LED PCBs and providing professional technical support and consulting services.
- Flexible customization:We can customize Micro LED PCBs according to the specific requirements of our customers, including different sizes, layers, materials, and special process requirements.
- Quality assurance: We rigorously control every manufacturing step to ensure product quality and stable performance. Our products undergo strict testing and quality inspection, conforming to international certification standards.
- Timely delivery: We can deliver high-quality Micro LED PCBs according to customer requirements, ensuring the smooth progress of customer projects.
In summary, as a company with rich experience and technical capabilities in the electronics manufacturing industry, we have the ability to produce high-quality Micro LED PCBs and provide customers with excellent customized services. We are committed to establishing long-term cooperative relationships with customers to jointly promote the development and application of Micro LED technology.
What are the 7 qualities of good customer service?
Good customer service is essential for maintaining positive relationships with customers and ensuring satisfaction. Seven qualities of good customer service include:
- Responsiveness: Good customer service involves promptly addressing customer inquiries, concerns, and requests. Responding in a timely manner demonstrates attentiveness and shows that the customer’s needs are a priority.
- Empathy: Empathy involves understanding and sharing the feelings of customers. Good customer service representatives empathize with customers’ situations, acknowledge their emotions, and strive to provide solutions that meet their needs.
- Clear Communication: Effective communication is crucial for good customer service. Customer service representatives should communicate clearly, using language that is easy to understand and avoiding jargon. They should listen actively to customers and provide information in a concise and accurate manner.
- Knowledgeability: Good customer service representatives are knowledgeable about the products or services offered by the company. They should be able to answer questions, provide recommendations, and offer assistance based on a deep understanding of the company’s offerings.
- Problem-Solving Skills: Customers may encounter issues or problems, and good customer service involves effectively resolving these issues. Customer service representatives should possess strong problem-solving skills, be proactive in finding solutions, and take ownership of issues until they are resolved satisfactorily.
- Professionalism:Good customer service is conducted with professionalism and courtesy at all times. Customer service representatives should remain calm and composed, even in challenging situations, and treat customers with respect and dignity.
- Follow-Up: Following up with customers after resolving an issue or completing a transaction is an important aspect of good customer service. It demonstrates care and concern for the customer’s satisfaction and provides an opportunity to address any remaining concerns or gather feedback for improvement.
By embodying these qualities, companies can provide exceptional customer service that builds trust, loyalty, and positive brand reputation.
FAQs
What are Micro LED PCBs?
Micro LED PCBs are specialized printed circuit boards designed for integrating Micro LED technology. These PCBs serve as the foundation for mounting and connecting Micro LEDs to create high-resolution and high-brightness displays.
What are the advantages of Micro LED PCBs?
Micro LED PCBs offer several advantages, including high resolution, high brightness, energy efficiency, fast response times, wide color gamut, and potential for flexible and transparent displays. They also provide excellent contrast and durability.
How are Micro LED PCBs different from traditional PCBs?
Micro LED PCBs are different from traditional PCBs in several ways. They are specifically designed to accommodate the small size and high density of Micro LEDs, requiring precise placement and routing of electrical connections. Additionally, Micro LED PCBs may incorporate thermal management features to dissipate heat effectively.
What factors should be considered when designing Micro LED PCBs?
Designing Micro LED PCBs requires consideration of factors such as miniaturization, thermal management, signal integrity, flexibility (if applicable), component placement accuracy, and manufacturability. It’s essential to optimize these factors to ensure optimal performance and reliability of the Micro LED display.
How are Micro LED PCBs manufactured?
The manufacturing process for Micro LED PCBs involves steps such as substrate selection, preparation, conductive traces formation, insulating layers application, via formation, component placement, soldering, testing, and inspection. Specialized equipment and expertise are often necessary to handle the precise placement and assembly of Micro LEDs.
What applications are suitable for Micro LED PCBs?
Micro LED PCBs are suitable for a wide range of applications, including consumer electronics (such as smartphones, tablets, and TVs), automotive displays, augmented reality (AR) and virtual reality (VR) devices, signage, wearable devices, and medical displays.
Are Micro LED PCBs expensive?
The cost of Micro LED PCBs can vary depending on factors such as size, complexity, materials, manufacturing processes, and quantity. While they may be more expensive than traditional PCBs due to their specialized requirements and precision, advancements in technology and manufacturing processes are expected to reduce costs over time.