Microtrace BGA substrates Manufacturer
Professional Microtrace BGA substrates Manufacturer, we mainly produce ultra-small bump pitch Microtrace BGA substrate, ultra-small trace and spacing packaging substrate and Smallest gap PCBs.
Microtrace BGA substrates are advanced components integral to modern semiconductor devices. Engineered with precision and sophistication, these substrates serve as the backbone for mounting and interconnecting semiconductor chips, facilitating efficient electrical connections within electronic systems. They feature intricate patterns of conductive traces, vias, and pads, meticulously etched onto substrate materials like silicon, ceramic, or organic laminate. Offering superior electrical performance, enhanced thermal management, and heightened reliability compared to conventional packaging methods, Microtrace BGA substrates enable miniaturization and optimization of electronic products across diverse industries. Their design adheres to stringent guidelines, ensuring optimal signal integrity, power distribution, and thermal dissipation. Manufactured by renowned companies with expertise in microelectronics, these substrates undergo rigorous testing and quality assurance measures to meet the demanding standards of modern technology. With their versatility and reliability, Microtrace BGA substrates continue to drive innovation and advancement in the semiconductor industry, powering the next generation of electronic devices.
What are Microtrace BGA substrates?
Microtrace BGA (Ball Grid Array) substrates are specialized substrates used in the manufacturing of integrated circuits, particularly for devices like microprocessors, memory chips, and other semiconductor components. BGA substrates provide the foundation for mounting and interconnecting the semiconductor chips, enabling efficient electrical connections between the chip and the rest of the electronic system.
These substrates are called “Microtrace” because they incorporate advanced microfabrication techniques to create intricate patterns of conductive traces, vias, and pads on a substrate material, typically made of materials like silicon, ceramic, or organic laminate. The term “microtrace” refers to the extremely fine and precise conductive traces etched onto the substrate, allowing for high-density interconnections between the semiconductor chip and the rest of the electronic system.
BGA substrates are crucial components in modern electronic devices, especially those with high-performance and high-density requirements. They offer advantages such as improved electrical performance, better thermal management, and increased reliability compared to traditional packaging techniques. These substrates play a vital role in the miniaturization and performance enhancement of electronic products across various industries, including consumer electronics, telecommunications, automotive, aerospace, and more.
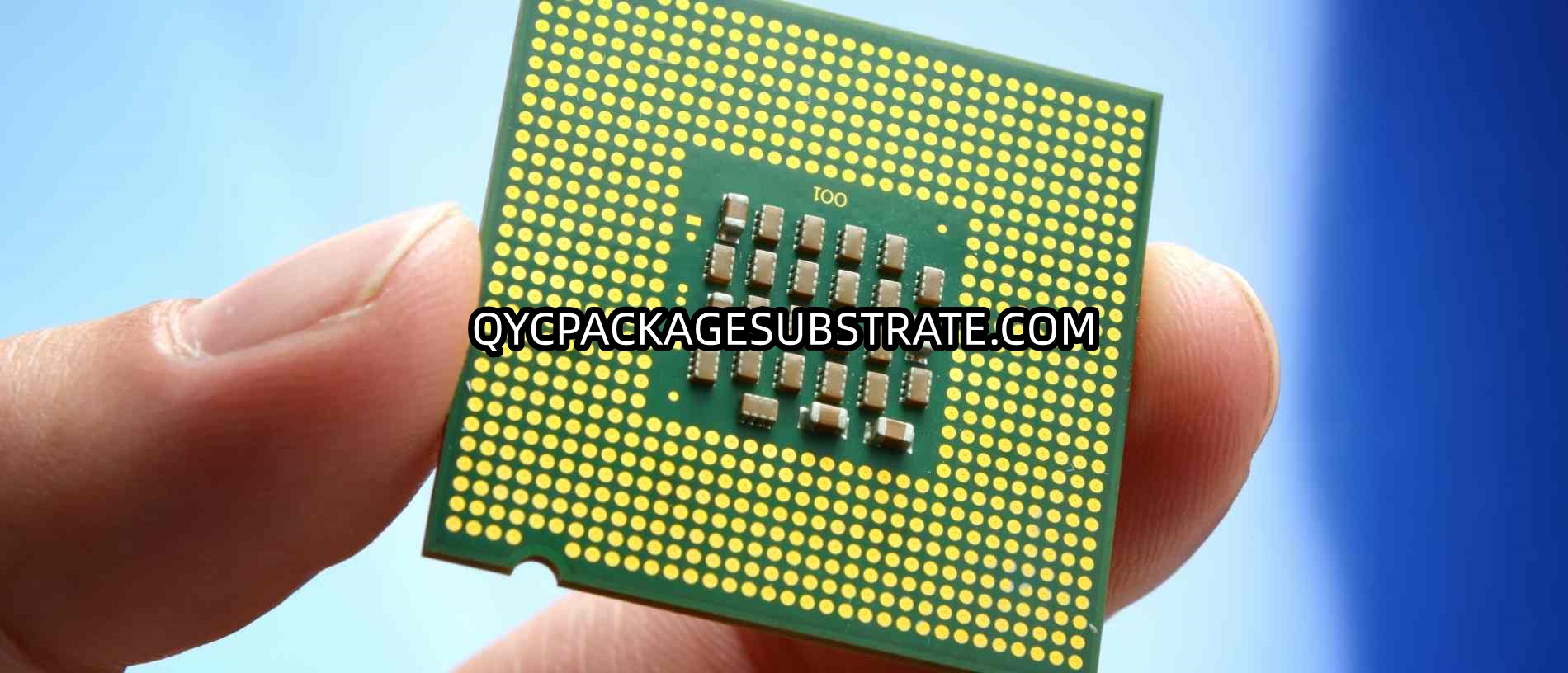
Microtrace BGA substrates Manufacturer
What are the Microtrace BGA substrate design guidelines?
Microtrace BGA substrate design guidelines typically encompass several key aspects to ensure optimal performance, reliability, and manufacturability of the integrated circuit package. While specific guidelines may vary depending on the manufacturer and application, here are some common considerations:
- Pad and Via Design: Designing appropriate pad and via sizes and spacings is crucial to ensure reliable electrical connections between the semiconductor chip and the substrate. Guidelines may include recommendations for pad and via dimensions, pitch, and aspect ratio to achieve optimal electrical performance and manufacturability.
- Trace Routing: Routing of traces on the substrate should be carefully planned to minimize signal interference, crosstalk, and impedance mismatches. Design guidelines may include recommendations for trace widths, spacing, and routing topologies to meet signal integrity requirements.
- Signal Integrity: Ensuring signal integrity is essential for maintaining the quality of electrical signals transmitted through the substrate. Guidelines may include recommendations for impedance control, signal routing techniques (such as differential signaling), and minimizing signal reflections and losses.
- Power Distribution: Proper power distribution is critical for supplying power to the semiconductor chip and other components on the substrate. Design guidelines may include recommendations for power plane design, decoupling capacitor placement, and minimizing voltage drops and noise.
- Thermal Management: Effective thermal management is essential to prevent overheating of the semiconductor chip and ensure long-term reliability. Guidelines may include recommendations for thermal vias, thermal pad placement, and optimizing the substrate material and thickness for heat dissipation.
- Manufacturability: Design guidelines should consider manufacturability factors such as substrate material properties, layer stackup, fabrication processes, and assembly techniques. Designers should work closely with substrate manufacturers to ensure that the design meets fabrication and assembly requirements.
- Reliability: Design guidelines should address reliability considerations such as mechanical stress, solder joint integrity, and environmental factors (e.g., temperature, humidity, vibration). Designs should be robust enough to withstand the intended operating conditions and maintain long-term reliability.
- Compliance: Ensure that the substrate design complies with relevant industry standards and specifications, such as IPC (Association Connecting Electronics Industries) standards, JEDEC (Joint Electron Device Engineering Council) standards, and customer-specific requirements.
These guidelines serve as a framework for designing Microtrace BGA substrates that meet the performance, reliability, and manufacturability requirements of integrated circuit packages. Designers should carefully consider these factors and collaborate with substrate manufacturers to develop optimized substrate designs for their specific applications.
What is the Microtrace BGA substrate fabrication process?
The fabrication process for Microtrace BGA (Ball Grid Array) substrates involves several key steps, including substrate material preparation, patterning, metallization, and assembly. While specific processes may vary depending on the substrate material and manufacturer, here’s a general overview of the fabrication process:
- Substrate Material Selection: The fabrication process begins with the selection of a suitable substrate material based on the application requirements. Common substrate materials include silicon, ceramic, and organic laminate (e.g., FR-4). The choice of substrate material depends on factors such as thermal conductivity, electrical properties, and cost.
- Substrate Preparation:The selected substrate material is prepared by cleaning and surface treatment to ensure proper adhesion of subsequent layers and metallization.
- Patterning: The substrate undergoes a patterning process to create the desired layout of conductive traces, vias, and pads. This patterning is typically achieved using photolithography, where a photoresist layer is deposited on the substrate, exposed to UV light through a photomask containing the desired pattern, and then developed to remove the unexposed photoresist, leaving behind the patterned areas.
- Metallization: After patterning, the substrate is metallized to deposit conductive materials (e.g., copper) onto the patterned areas. Metallization may involve processes such as physical vapor deposition (PVD) or electroplating to deposit thin layers of metal onto the substrate surface.
- Etching: Excess metallization material is removed from the substrate through etching processes, which selectively remove unwanted metal while leaving behind the desired conductive traces, vias, and pads.
- Surface Finish: The substrate surface may undergo surface finish treatments to improve solderability and corrosion resistance. Common surface finishes include electroless nickel immersion gold (ENIG), electroless nickel electroless palladium immersion gold (ENEPIG), and organic surface protectants (OSP).
- Assembly: Once the substrate fabrication is complete, it is ready for assembly with semiconductor chips and other electronic components. This assembly process involves attaching the chips to the substrate using solder or other bonding techniques, followed by encapsulation and packaging to protect the components from environmental factors.
- Testing and Quality Assurance: The fabricated Microtrace BGA substrates undergo rigorous testing to ensure that they meet the required electrical and mechanical specifications. Testing may include continuity testing, impedance measurements, thermal cycling tests, and visual inspection.
- Final Inspection and Packaging: After testing, the substrates are inspected for defects and then packaged for shipment to customers or further integration into electronic products.
Throughout the fabrication process, stringent quality control measures are employed to ensure the reliability and performance of the Microtrace BGA substrates for their intended applications. Collaboration between substrate manufacturers and designers is essential to optimize the fabrication process and meet the specific requirements of each application.
How do you manufacture Microtrace BGA substrates?
Manufacturing Microtrace BGA (Ball Grid Array) substrates involves a series of intricate processes that require specialized equipment and expertise. Here’s an overview of the typical steps involved in manufacturing Microtrace BGA substrates:
- Substrate Material Selection: The manufacturing process begins with the selection of a suitable substrate material based on the application requirements. Common substrate materials include silicon, ceramic, and organic laminate (e.g., FR-4).
- Substrate Preparation: The selected substrate material undergoes preparation steps such as cleaning and surface treatment to ensure proper adhesion of subsequent layers and metallization.
- Patterning: Patterning is a critical step in the manufacturing process where the desired layout of conductive traces, vias, and pads is created on the substrate. This is typically achieved using photolithography, where a photoresist layer is deposited on the substrate, exposed to UV light through a photomask containing the desired pattern, and then developed to remove the unexposed photoresist, leaving behind the patterned areas.
- Metallization: After patterning, the substrate is metallized to deposit thin layers of conductive materials (e.g., copper) onto the patterned areas. Metallization may involve processes such as physical vapor deposition (PVD), chemical vapor deposition (CVD), or electroplating.
- Etching: Excess metallization material is removed from the substrate through etching processes, which selectively remove unwanted metal while leaving behind the desired conductive traces, vias, and pads.
- Surface Finish: The substrate surface may undergo surface finish treatments to improve solderability and corrosion resistance. Common surface finishes include electroless nickel immersion gold (ENIG), electroless nickel electroless palladium immersion gold (ENEPIG), and organic surface protectants (OSP).
- Assembly: Once the substrate fabrication is complete, it is ready for assembly with semiconductor chips and other electronic components. This assembly process involves attaching the chips to the substrate using solder or other bonding techniques, followed by encapsulation and packaging to protect the components from environmental factors.
- Testing and Quality Assurance: The manufactured Microtrace BGA substrates undergo rigorous testing to ensure that they meet the required electrical and mechanical specifications. Testing may include continuity testing, impedance measurements, thermal cycling tests, and visual inspection.
- Final Inspection and Packaging: After testing, the substrates are inspected for defects and then packaged for shipment to customers or further integration into electronic products.
Throughout the manufacturing process, strict quality control measures are implemented to ensure the reliability and performance of the Microtrace BGA substrates for their intended applications. Collaboration between substrate manufacturers and designers is essential to optimize the manufacturing process and meet the specific requirements of each application.
How much should Microtrace BGA substrates cost?
The cost of Microtrace BGA substrates can vary widely depending on several factors, including the substrate material, size, complexity of the design, manufacturing technology, and order volume. Here are some factors that influence the cost:
- Substrate Material: Different substrate materials have varying costs. For example, ceramic substrates tend to be more expensive than organic laminate substrates like FR-4.
- Size and Complexity: Larger substrates with more complex designs requiring finer trace widths, smaller vias, and higher layer counts typically incur higher manufacturing costs.
- Manufacturing Technology: Advanced manufacturing technologies such as HDI (High-Density Interconnect) and laser drilling may increase the cost of fabrication due to the specialized equipment and processes involved.
- Order Volume: Larger order volumes typically result in lower per-unit costs due to economies of scale. Manufacturers may offer discounts for bulk orders.
- Surface Finish and Additional Features: Surface finishes such as ENIG or ENEPIG, as well as additional features like impedance control, blind vias, and buried vias, can increase the cost of Microtrace BGA substrates.
- Quality and Reliability Requirements: Meeting specific quality and reliability standards may involve additional testing and quality control measures, which can impact the overall cost.
- Supplier and Location: The choice of supplier and their location can affect pricing due to differences in labor costs, overheads, and market conditions.
Due to these factors, it’s challenging to provide a specific cost for Microtrace BGA substrates without knowing the details of the design and manufacturing requirements. Typically, customers obtain quotes from substrate manufacturers based on their specific design specifications and volume requirements. It’s essential to work closely with substrate manufacturers to optimize the design for cost-effectiveness while meeting the performance and reliability needs of the application.
What is Microtrace BGA substrate base material?
The base material for Microtrace BGA (Ball Grid Array) substrates can vary depending on the specific requirements of the application and the manufacturing process used by the substrate manufacturer. However, common base materials used for Microtrace BGA substrates include:
- Organic Laminate: Organic laminate materials, such as FR-4 (Flame Retardant 4), are widely used for BGA substrates due to their cost-effectiveness, ease of fabrication, and good electrical properties. These materials consist of layers of fiberglass cloth impregnated with epoxy resin.
- Ceramic: Ceramic materials, such as alumina (Al2O3) or aluminum nitride (AlN), are chosen for applications requiring superior thermal conductivity, high temperature resistance, and excellent electrical properties. Ceramic substrates are often used in high-power and high-frequency applications.
- Silicon: Silicon substrates offer exceptional electrical properties, mechanical strength, and compatibility with semiconductor fabrication processes. Silicon substrates are typically used in applications requiring high precision and integration with semiconductor chips.
Each of these base materials has its advantages and limitations, and the choice depends on factors such as thermal management requirements, electrical performance, cost considerations, and compatibility with the manufacturing process. Designers and manufacturers select the base material that best suits the specific needs of the Microtrace BGA substrate application.
Which companies make Microtrace BGA substrates?
Some companies specialize in manufacturing Microtrace BGA substrates, including well-known companies such as Toshiba, Hitachi, Intel, Samsung, Taiwan Semiconductor Manufacturing Company (TSMC), and IBM in the United States. These companies have extensive experience and advanced manufacturing technologies in the microelectronics industry, enabling them to produce high-performance and highly reliable Microtrace BGA substrates to meet various application requirements.
Just like these large companies, our company is also capable of producing Microtrace BGA substrates. While we may not have the same scale and resources as they do, we have a team of experienced and skilled professionals dedicated to providing customers with high-quality custom solutions.
Our manufacturing process covers every aspect from design to production, ensuring that we can produce Microtrace BGA substrates that meet our customers’ expectations and standards. We have advanced equipment and technology to achieve precise patterning, metallization, and other processing steps, ensuring the quality and performance of the substrates.
At the same time, we prioritize communication and collaboration with our customers to understand their needs and expectations, providing appropriate technical support and advice. We are committed to building long-term partnerships with our customers, providing ongoing technical support and services to ensure the success of their projects.
In summary, while our company may not be as large as some well-known companies, we have the experience and expertise to provide customers with custom, high-quality Microtrace BGA substrates. We work closely with them to achieve success in their projects.
What are the qualities of good customer service?
Good customer service is characterized by several key qualities that contribute to a positive experience for customers. Here are some qualities of good customer service:
- Responsive: Good customer service is responsive to customers’ needs and inquiries in a timely manner. This includes promptly answering phone calls, emails, and messages, and addressing customer concerns or issues promptly.
- Empathetic: Empathy is essential in good customer service. Customer service representatives should listen attentively to customers’ concerns, understand their perspective, and show empathy and understanding towards their situation.
- Knowledgeable: Customer service representatives should have a deep understanding of the company’s products or services, policies, and procedures. They should be able to provide accurate information and helpful guidance to customers.
- Professionalism: Good customer service is conducted with professionalism and courtesy at all times. This includes being polite, respectful, and maintaining a positive attitude, even in challenging situations.
- Effective Communication: Effective communication is crucial in good customer service. Customer service representatives should communicate clearly and effectively, using language that is easy for customers to understand. They should also be good listeners and ask clarifying questions when needed.
- Problem-Solving Skills: Good customer service involves the ability to effectively resolve customer issues and problems. Customer service representatives should be proactive in finding solutions, taking ownership of problems, and following through until the issue is resolved to the customer’s satisfaction.
- Flexibility: Good customer service requires flexibility to adapt to different customer needs and situations. This may involve being willing to accommodate special requests, offering alternative solutions, or making exceptions to company policies when necessary.
- Consistency: Consistency is key in good customer service. Customers should receive the same level of service and treatment regardless of who they interact with or when they contact the company.
- Follow-Up: Good customer service includes following up with customers to ensure that their issues have been resolved satisfactorily and to gather feedback on their experience. This demonstrates care and commitment to customer satisfaction.
- Continuous Improvement: Good customer service is always seeking ways to improve and enhance the customer experience. This may involve collecting customer feedback, analyzing trends and patterns, and implementing changes to address areas for improvement.
By embodying these qualities, companies can build strong relationships with their customers, foster loyalty, and differentiate themselves from competitors in the marketplace.
FAQs
What are Microtrace BGA substrates?
Microtrace BGA substrates are specialized substrates used in the manufacturing of integrated circuits, particularly for devices like microprocessors, memory chips, and other semiconductor components. They provide the foundation for mounting and interconnecting the semiconductor chips, enabling efficient electrical connections between the chip and the rest of the electronic system.
What are the key features of Microtrace BGA substrates?
Microtrace BGA substrates typically feature advanced microfabrication techniques to create intricate patterns of conductive traces, vias, and pads on a substrate material. These substrates offer advantages such as improved electrical performance, better thermal management, and increased reliability compared to traditional packaging techniques.
What materials are used in Microtrace BGA substrates?
Microtrace BGA substrates can be made from various materials, including silicon, ceramic, and organic laminate. The choice of substrate material depends on factors such as thermal conductivity, electrical properties, and cost.
What is the fabrication process for Microtrace BGA substrates?
The fabrication process for Microtrace BGA substrates involves several key steps, including substrate material preparation, patterning, metallization, and assembly. Each step is crucial for achieving the desired electrical performance, reliability, and manufacturability of the substrates.
What are some design guidelines for Microtrace BGA substrates?
Design guidelines for Microtrace BGA substrates typically include recommendations for pad and via design, trace routing, signal integrity, power distribution, thermal management, manufacturability, reliability, and compliance with industry standards.
How much do Microtrace BGA substrates cost?
The cost of Microtrace BGA substrates can vary depending on factors such as substrate material, size, complexity of the design, manufacturing technology, and order volume. Customers can obtain quotes from substrate manufacturers based on their specific design specifications and volume requirements.
Which companies manufacture Microtrace BGA substrates?
Several companies specialize in the manufacture of Microtrace BGA substrates, including well-known companies such as Toshiba, Hitachi, Intel, Samsung, TSMC, and IBM. Additionally, smaller companies may also offer Microtrace BGA substrates with custom solutions and services.