Microtrace Package Substrate Manufacturer
Microtrace Package Substrate Manufacturer,Microtrace Package Substrates are advanced printed circuit boards tailored for high-density packaging of microelectronic components. These substrates feature precise microtraces and fine-pitch interconnections, facilitating compact designs and efficient signal transmission. Microtrace Package Substrates are engineered with specialized materials and manufacturing techniques to ensure optimal electrical performance and reliability in demanding applications. They are essential in industries such as telecommunications, automotive electronics, and medical devices, where space efficiency and signal integrity are critical. Microtrace Package Substrates enable miniaturization while maintaining robustness and thermal management capabilities, making them ideal for modern electronic devices requiring high-performance and reliability in compact form factors.
What is a Microtrace Package Substrate?
A Microtrace Package Substrate refers to a type of advanced substrate used in semiconductor packaging. It integrates micro-sized conductive traces within the substrate material itself, enabling dense routing of electrical signals. This technology is crucial in modern electronic devices where miniaturization and high-density interconnects are critical.
Microtrace substrates are typically made using advanced materials like high-performance laminates or ceramics, depending on the application’s thermal, electrical, and mechanical requirements. These substrates support the precise placement and routing of components, ensuring efficient signal transmission and thermal management. They are utilized in various applications such as high-frequency communication devices, advanced computing systems, and aerospace electronics, where reliability and performance under demanding conditions are paramount. The manufacturing processes for these substrates involve precise etching and deposition techniques to create intricate microstructures that optimize signal integrity and minimize signal loss.
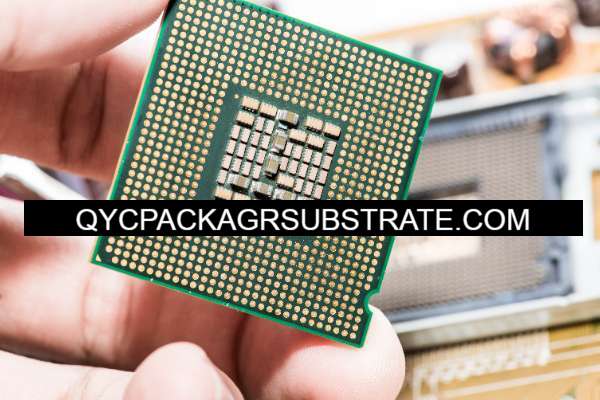
Microtrace Package Substrate Manufacturer
What are the Microtrace Package Substrate Design Guidelines?
Design guidelines for Microtrace Package Substrates focus on ensuring optimal performance and reliability in electronic applications. Here are some key considerations:
- Material Selection: Choose high-performance substrates with properties matching thermal, electrical, and mechanical requirements. Materials like high-performance laminates or ceramics are common for their excellent dielectric properties and thermal conductivity.
- Layer Stackup Design: Design an optimal layer stackup considering signal integrity, power distribution, and thermal management. Place power and ground planes strategically to minimize impedance mismatches and noise.
- Trace Routing and Width: Use micro-sized conductive traces for dense routing while maintaining signal integrity. Ensure appropriate trace widths and spacing to meet impedance requirements and reduce crosstalk.
- Via Design: Optimize via placement and design to minimize signal distortion and improve thermal management. Use microvias or blind vias for compact designs, ensuring they meet reliability standards for electrical and mechanical performance.
- Signal Integrity: Perform thorough impedance control and simulation to ensure signal integrity across different frequencies. Maintain consistent dielectric thickness and material properties throughout the substrate.
- Thermal Management: Incorporate thermal vias, thermal pads, or other cooling techniques to manage heat dissipation effectively, especially in high-power applications.
- Manufacturability: Design for manufacturability by considering the capabilities of fabrication processes such as laser drilling, photolithography, and precision etching. Ensure designs are scalable and compatible with mass production techniques.
- Testing and Validation: Implement rigorous testing protocols to validate design parameters such as impedance, thermal performance, and reliability under operational conditions.
By following these guidelines, designers can create Microtrace Package Substrates that meet the demanding requirements of modern electronic devices, ensuring high performance, reliability, and manufacturability.
What is the Microtrace Package Substrate Fabrication Process?
The fabrication process of Microtrace Package Substrates involves several key steps to create intricate micro-sized conductive traces within the substrate material. Here is a generalized outline of the fabrication process:
- Substrate Material Selection:Choose a substrate material suitable for the application’s thermal, electrical, and mechanical requirements. Common materials include high-performance laminates or ceramics with high thermal conductivity and low dielectric loss.
- Design Layout: Develop a detailed design layout specifying the placement and routing of micro-sized traces. Utilize CAD software for precise design and layout optimization, considering signal integrity, impedance control, and thermal management.
- Photolithography: Begin the fabrication process by coating the substrate material with a photoresist layer. Use photolithography techniques to transfer the design pattern onto the substrate. This involves exposing the photoresist to UV light through a photomask and then developing it to create the desired pattern of micro-sized traces.
- Etching: Etch away the exposed areas of the substrate material using chemical etchants. This process removes the substrate material where the photoresist has been removed, leaving behind the micro-sized conductive traces. Control the etching process carefully to ensure precise trace dimensions and edge quality.
- Surface Treatment: Apply surface treatment techniques such as metallization to the exposed conductive traces. This step enhances the conductivity of the traces and improves their resistance to oxidation and environmental degradation.
- Via Formation: Create micro vias or through-holes in the substrate material to facilitate interconnects between different layers. Use laser drilling or mechanical drilling techniques to form vias, followed by metallization and filling processes to ensure electrical continuity between layers.
- Layer Lamination: Stack and laminate multiple layers of substrate material to form the final substrate structure. Ensure proper alignment and registration of layers to maintain the integrity of micro-sized traces and vias.
- Quality Control and Testing: Conduct rigorous quality control checks throughout the fabrication process. Perform inspections for dimensional accuracy, trace continuity, impedance control, and adherence to design specifications. Test the fabricated substrates for reliability, thermal performance, and signal integrity under simulated operating conditions.
- Final Finishing:Complete the fabrication process by applying protective coatings or finishes to the substrate surface. These coatings provide additional protection against environmental factors and mechanical stress.
By following these steps, manufacturers can produce Microtrace Package Substrates that meet the demanding requirements of high-performance electronic devices, ensuring optimal performance, reliability, and manufacturability.
How do you manufacture a Microtrace Package Substrate?
Manufacturing a Microtrace Package Substrate involves a meticulous process designed to integrate micro-sized conductive traces within the substrate material. Here’s a structured outline of the manufacturing steps:
- Material Selection: Choose a substrate material that meets the application’s thermal, electrical, and mechanical requirements. Common choices include high-performance laminates or ceramics with excellent thermal conductivity and low dielectric loss.
- Design and Layout: Utilize CAD software to develop a precise design layout. Define the placement and routing of micro-sized traces, considering factors such as signal integrity, impedance control, and thermal management.
- Photolithography: Coat the substrate material with a photoresist layer. Use photolithography techniques to transfer the design pattern onto the substrate. This involves exposing the photoresist to UV light through a photomask and then developing it to create the desired pattern of micro-sized traces.
- Etching: Employ chemical etchants to selectively remove the exposed substrate material, leaving behind the micro-sized conductive traces defined by the photoresist pattern. Monitor the etching process carefully to ensure precise trace dimensions and edge quality.
- Metallization:Apply surface treatment techniques to the exposed conductive traces. Metallization enhances conductivity and protects against oxidation. Techniques may include electroplating or sputtering a thin layer of metal onto the traces.
- Via Formation: Create micro vias or through-holes in the substrate material to facilitate interconnections between different layers. Use laser drilling or mechanical drilling to form vias, followed by metallization and filling processes to ensure electrical continuity between layers.
- Layer Lamination: Stack and laminate multiple layers of prepared substrate material. Ensure precise alignment and registration of layers to maintain the integrity of micro-sized traces and vias.
- Quality Control and Testing:Implement stringent quality control measures throughout the manufacturing process. Inspect for dimensional accuracy, trace continuity, and adherence to design specifications. Conduct testing for reliability, thermal performance, and signal integrity under simulated operating conditions.
- Final Finishing: Apply protective coatings or finishes to the substrate surface for added durability and protection against environmental factors and mechanical stress.
By following these steps with precision and attention to detail, manufacturers can produce high-quality Microtrace Package Substrates suitable for advanced electronic applications demanding miniaturization, high-density interconnects, and reliable performance.
How much should a Microtrace Package Substrate cost?
The cost of a Microtrace Package Substrate can vary widely depending on several factors:
- Design Complexity: The complexity of the design, including the number of layers, density of micro-sized traces, and intricacy of via structures, can significantly impact the cost. More complex designs require more precise manufacturing processes and may involve higher material and labor costs.
- Material Choice: The type and quality of substrate materials selected for the Microtrace Package Substrate influence its cost. High-performance materials with superior thermal conductivity and low dielectric loss tend to be more expensive.
- Manufacturing Process: The fabrication techniques used, such as photolithography, etching, metallization, and via formation, contribute to the overall cost. Processes requiring high precision and specialized equipment can increase manufacturing expenses.
- Volume and Scale: Economies of scale play a role in determining the cost per unit. Larger production volumes typically result in lower per-unit costs due to efficiencies in material procurement, manufacturing setup, and overhead expenses.
- Quality and Testing Requirements: Stringent quality control measures and testing protocols can add to the overall cost of manufacturing Microtrace Package Substrates. Ensuring reliability, signal integrity, and compliance with industry standards may require additional investment.
As a rough estimate, the cost of Microtrace Package Substrates can range from several dollars to tens of dollars per square inch, depending on the above factors. For precise pricing, it’s advisable to consult with manufacturers or suppliers who can provide detailed quotations based on specific design requirements and volume considerations.
What is Microtrace Package Substrate base material?
The base materials used for Microtrace Package Substrates vary depending on the specific application requirements, but they generally include high-performance laminates or ceramics. Here are some common types of base materials used:
- High-Performance Laminates: These are composite materials typically consisting of layers of fiberglass cloth impregnated with epoxy resin (FR4) or other resin systems. High-performance laminates offer good mechanical strength, electrical insulation, and are suitable for moderate to high-frequency applications.
- Ceramics: Ceramics such as alumina (Al2O3) or aluminum nitride (AlN) are used when superior thermal conductivity is required. Ceramics provide excellent heat dissipation properties, making them ideal for high-power applications and environments where thermal management is critical.
- Polyimide Films: Polyimide films, such as Kapton, are used for flexible Microtrace Package Substrates. These materials offer flexibility, high-temperature resistance, and good electrical insulation properties, suitable for applications requiring conformal substrates.
- Rigid-Flex Materials: Rigid-flex substrates combine flexible polyimide films with rigid FR4 or similar materials. These substrates are used in applications where both flexibility and rigidity are required, such as in complex electronic assemblies.
The choice of base material depends on factors like electrical performance requirements (such as dielectric constant and loss tangent), thermal management needs, mechanical strength, and cost considerations. Designers select the most appropriate base material based on these criteria to ensure optimal performance and reliability of Microtrace Package Substrates in various electronic applications.
Which company makes Microtrace Package Substrates?
Microtrace Package Substrates are manufactured by several companies with extensive expertise in high-performance packaging substrates. Major manufacturers include Materion Corporation from the United States and Shinko Electric Industries Co., Ltd. from Japan, both known for their advanced technologies and experience in this field.
These substrates are typically made from high-performance laminates or ceramics, chosen for their excellent thermal conductivity and low dielectric loss, crucial for meeting stringent requirements in thermal management and signal integrity of complex electronic devices. Manufacturing Microtrace Package Substrates involves advanced processes and equipment to ensure the precision and reliability of micro-sized conductors and vias.
Our company is also dedicated to the production and development of Microtrace Package Substrates. As a rising star in the industry, we possess advanced manufacturing technologies and a professional team capable of customizing substrates for complex designs according to customer requirements. We utilize advanced CAD design software and precision manufacturing equipment to ensure that each substrate meets high standards of quality and performance.
Throughout the manufacturing process of Microtrace Package Substrates, we pay meticulous attention to detail, from material selection to process control, aiming to meet customer expectations and industry standards. Our products are widely used in communications, computing, medical, aerospace, and other fields, providing reliable solutions and technical support to our customers.
For specific inquiries or technical consultations regarding the production of Microtrace Package Substrates, we warmly welcome further discussion to explore how we can better meet your product needs and technical challenges.
What are the 7 qualities of good customer service?
Good customer service typically embodies several key qualities that contribute to positive customer experiences and satisfaction. Here are seven essential qualities:
- Responsiveness:Being prompt and proactive in addressing customer inquiries, concerns, and requests. Responding quickly shows customers that their time and needs are valued.
- Empathy:Understanding and empathizing with customers’ perspectives, emotions, and situations. Empathetic service acknowledges and validates customer feelings, fostering trust and rapport.
- Clear Communication: Communicating clearly and effectively to ensure mutual understanding. This includes using plain language, active listening, and providing thorough explanations or instructions.
- Knowledgeability:Possessing expertise and knowledge about products, services, policies, and procedures. Knowledgeable service agents can provide accurate information and solutions efficiently.
- Professionalism:Conducting interactions with professionalism, courtesy, and respect. Professional behavior builds confidence and enhances the customer service experience.
- Problem-Solving Skills: Effectively addressing and resolving customer issues or complaints. Strong problem-solving abilities enable service providers to find solutions that meet customer needs and expectations.
- Personalization: Tailoring interactions and solutions to individual customer preferences and circumstances. Personalized service demonstrates attentiveness and a commitment to meeting specific customer needs.
These qualities collectively contribute to creating a positive customer service experience, fostering customer loyalty, and enhancing the overall reputation of the organization.
FAQs
What are Microtrace Package Substrates?
Microtrace Package Substrates are advanced materials used in electronic packaging. They feature micro-sized conductive traces integrated within the substrate material, enabling high-density interconnects and optimized signal integrity.
What materials are used for Microtrace Package Substrates?
Common materials include high-performance laminates and ceramics. These materials offer excellent thermal conductivity, low dielectric loss, and mechanical stability, meeting the demanding requirements of modern electronic devices.
What are the applications of Microtrace Package Substrates?
They are used in various high-performance electronic applications, including telecommunications, computing systems, aerospace electronics, and medical devices. These substrates are critical where miniaturization, high-speed signal transmission, and thermal management are essential.
How are Microtrace Package Substrates manufactured?
Manufacturing involves precise processes such as photolithography, etching, metallization, and via formation. These techniques create intricate patterns of micro-sized traces and vias within the substrate material, ensuring reliability and performance.
What are the benefits of using Microtrace Package Substrates?
Benefits include enhanced signal integrity, improved thermal management, and support for high-density packaging. They enable designers to achieve compact and efficient electronic assemblies while maintaining reliability under demanding operating conditions.
Where can I get Microtrace Package Substrates?
Microtrace Package Substrates are produced by specialized manufacturers with expertise in high-performance electronic materials. Companies like Materion Corporation and Shinko Electric Industries Co., Ltd. are known for their advanced technologies in this field.
What considerations should I keep in mind when designing with Microtrace Package Substrates?
Design considerations include material selection, trace routing for signal integrity, via placement for interconnects, and thermal management strategies. Consulting with substrate manufacturers can help optimize designs for specific application requirements.