Microtrace Substrate Manufacturer
Microtrace Substrate Manufacturer,Microtrace substrates are advanced printed circuit boards (PCBs) designed for high-density electronic applications. With extremely fine traces and spacings, they enable compact, high-performance electronic devices. Utilizing materials like polyimide, FR-4, or PTFE, these substrates facilitate precise signal routing, reduced signal loss, and enhanced thermal management. Commonly used in telecommunications, aerospace, and medical devices, microtrace substrates support miniaturization and high-speed data transmission while ensuring reliability in demanding environments. Their manufacturing process involves intricate steps to achieve optimal performance, making them vital components in modern electronics.
What is a Microtrace Substrate?
In the field of electronic design and manufacturing, a “Microtrace Substrate” typically refers to a type of highly precise Printed Circuit Board (PCB) substrate characterized by extremely fine line widths and spacings. This substrate allows for the creation of very small conductive paths, which is crucial for applications involving high-density integrated circuits (ICs) such as high-speed computers, communication equipment, and advanced consumer electronics. Such substrates enable circuit boards to accommodate more circuit components within a limited space, thereby enhancing functionality and complexity.
Using a Microtrace Substrate can significantly improve the performance and signal integrity of PCBs, as finer traces can reduce interference and signal loss between circuits. Additionally, the design of these substrates helps achieve higher signal transmission rates and lower electromagnetic interference (EMI). During the design process, engineers must pay special attention to the layout and isolation of the traces to optimize electrical performance and ensure long-term reliability.
Overall, Microtrace Substrates are one of the key technologies in the manufacturing of high-performance electronic devices. They support the miniaturization and performance enhancement of modern electronic equipment by allowing more precise wiring, with applications ranging from mobile devices to high-end servers and communication infrastructure.
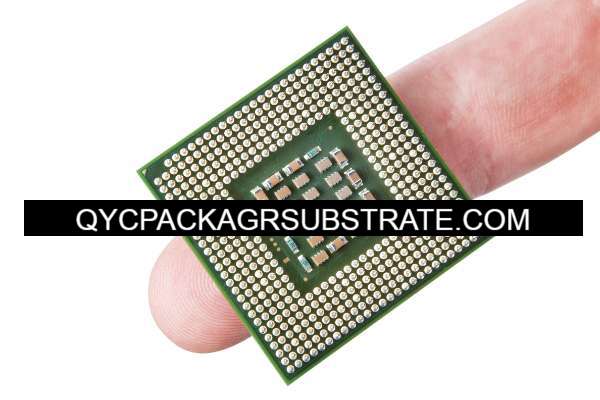
Microtrace Substrate Manufacturer
What are Microtrace Substrate Design Guidelines?
Designing a PCB using a microtrace substrate involves adhering to a set of specific guidelines to ensure optimal performance, reliability, and manufacturability. Here are some key design guidelines typically followed when working with microtrace substrates:
- Trace Width and Spacing: One of the most critical aspects of microtrace substrate design is selecting appropriate trace widths and spacings. The minimum trace width and spacing are determined by the capabilities of the fabrication house and the current carrying requirements. Typically, widths and spacings can go down to a few microns for advanced applications. Ensuring these parameters are correctly set is vital for avoiding electrical shorts and reducing the risk of signal integrity issues.
- Material Selection: The choice of substrate material can significantly affect the performance of the PCB. Materials with high thermal stability and good dielectric properties, such as high-performance FR-4, polyimide, or PTFE (Teflon), are commonly used. These materials help manage the challenges associated with high-density routing and thermal management.
- Impedance Control: Controlled impedance is crucial in high-speed circuit applications to prevent signal degradation. The impedance of a trace is influenced by its width, thickness, the dielectric material, and the distance to the reference plane. Accurate modeling and simulation are required to ensure that impedance targets are met.
- Thermal Management: High-density circuits generate more heat. Efficient thermal management strategies, such as using thermal vias, selecting materials with high thermal conductivity, and optimizing the layout for heat distribution, are necessary to prevent hot spots and ensure component reliability.
- Signal Integrity Considerations: At high frequencies, signal integrity becomes a concern due to issues like crosstalk and electromagnetic interference (EMI). Design techniques such as maintaining adequate spacing between traces, using differential signaling when possible, and employing shielding methods can mitigate these effects.
- Layer Stackup: The configuration of the layers in a PCB (stackup) can significantly impact the electrical performance. A well-designed stackup helps in balancing the capacitance and inductance of the board, which in turn supports better signal integrity and reduces EMI.
- Via Design:In high-density designs, the use of microvias, which are smaller in diameter than traditional vias, becomes essential. Microvias can reduce the space needed for connections and improve the electrical performance by reducing the path length for signals.
- Design for Manufacturability (DFM): It is crucial to consider the manufacturability of the PCB during the design phase. This includes accounting for the tolerances of PCB manufacturing processes, ensuring testability, and considering the ease of assembly.
By following these guidelines, designers can effectively manage the complexities associated with microtrace substrates, ultimately producing more reliable and functional high-density PCBs.
What is the Microtrace Substrate Fabrication Process?
The fabrication process for microtrace substrates involves several key steps to create the intricate circuit patterns required for high-density electronic applications. Here’s an overview of the typical fabrication process:
- Substrate Selection: The process begins with selecting a suitable substrate material, such as FR-4, polyimide, or PTFE (Teflon), based on the specific requirements of the application. The choice of substrate material depends on factors like thermal stability, dielectric properties, and dimensional stability.
- Surface Preparation: The substrate surface is cleaned and prepared to ensure proper adhesion of the subsequent layers. This may involve processes such as cleaning, surface roughening, and applying adhesion-promoting treatments.
- Copper Cladding: A thin layer of copper is laminated onto the substrate surface using a process called electrodeposition or electroplating. This copper layer serves as the conductive material for the circuit traces and pads.
- Photoresist Application: A layer of photoresist is applied over the copper-clad substrate. Photoresist is a light-sensitive material that will be used to define the circuit pattern.
- Exposure and Development: The photoresist is exposed to UV light through a photomask, which contains the desired circuit pattern. The exposed areas of the photoresist become soluble and are removed during the development process, leaving behind the patterned photoresist.
- Etching: The exposed copper areas not protected by the photoresist are etched away using chemical etchants. This process selectively removes the copper, leaving behind the desired circuit pattern on the substrate.
- Strip and Clean: The remaining photoresist is stripped away, leaving the patterned copper traces and pads on the substrate surface. The substrate is then cleaned to remove any residues from the fabrication process.
- Surface Finish: Surface finish options such as HASL (Hot Air Solder Leveling), ENIG (Electroless Nickel Immersion Gold), or OSP (Organic Solderability Preservatives) may be applied to protect the copper traces and improve solderability.
- Final Inspection: The fabricated substrate undergoes a final inspection to ensure that the circuit pattern meets the design specifications and quality standards. This may include visual inspection, electrical testing, and dimensional measurements.
- Additional Processing:Depending on the specific requirements of the application, additional processing steps such as drilling of via holes, applying solder mask, and silk screening of component identifiers may be performed.
By following these fabrication steps with precision and attention to detail, manufacturers can produce microtrace substrates with intricate circuit patterns that meet the demands of high-density electronic designs.
How do you manufacture a Microtrace Substrate?
Manufacturing a microtrace substrate involves a series of intricate processes to create a high-precision printed circuit board (PCB) with extremely fine traces and spacings. Here’s a step-by-step overview of the typical manufacturing process:
- Design Preparation: The process begins with the preparation of the PCB design files using specialized electronic design automation (EDA) software. Designers lay out the circuitry, including trace routing, component placement, and signal integrity considerations, according to the specific requirements of the application.
- Substrate Selection: A suitable substrate material is selected based on the desired electrical, mechanical, and thermal properties. Common substrate materials include FR-4 (fiberglass-reinforced epoxy), polyimide, and PTFE (Teflon). The substrate may come in the form of thin sheets or panels.
- Copper Foil Lamination: Thin layers of copper foil are laminated onto both sides of the substrate using heat and pressure. The thickness of the copper foil is chosen based on the current-carrying requirements and impedance control considerations of the PCB design.
- Photoresist Application: A layer of photoresist is applied to the surface of the copper-clad substrate using a process such as roller coating or spray coating. Photoresist is a light-sensitive material that will be used to define the circuit pattern.
- Exposure and Development: The photoresist-coated substrate is exposed to UV light through a photomask, which contains the desired circuit pattern. The UV light cures the exposed areas of the photoresist, while the unexposed areas remain soluble. The substrate is then developed to remove the uncured photoresist, leaving behind the patterned photoresist mask.
- Etching: The substrate is submerged in an etchant solution, which selectively removes the exposed copper areas not protected by the photoresist mask. This etching process creates the desired circuit traces and pads on the substrate surface.
- Photoresist Stripping: The remaining photoresist mask is stripped away from the substrate using chemical solvents or stripping agents, leaving behind the patterned copper traces and pads.
- Surface Finish: Surface finish processes such as hot air solder leveling (HASL), electroless nickel immersion gold (ENIG), or immersion tin may be applied to protect the exposed copper surfaces and improve solderability.
- Drilling and Via Formation: Small holes, known as vias, are drilled through the substrate to establish electrical connections between different layers of the PCB. Advanced manufacturing techniques such as laser drilling or mechanical drilling may be used to create microvias with extremely small diameters.
- Solder Mask Application:A layer of solder mask is applied over the entire surface of the PCB, leaving openings only where solder pads and vias are exposed. The solder mask protects the copper traces from oxidation and provides insulation between conductive elements.
- Silkscreen Printing: Component identifiers, such as part numbers, reference designators, and polarity markings, are applied to the PCB surface using silkscreen printing.
- Final Inspection: The completed PCB undergoes a series of quality control inspections to ensure that it meets the design specifications and quality standards. This may include visual inspection, electrical testing, and dimensional measurements.
By following these manufacturing steps with precision and attention to detail, manufacturers can produce microtrace substrates that meet the demanding requirements of high-density electronic applications.
How much should a Microtrace Substrate cost?
The cost of microtrace substrates can vary significantly depending on several factors, including the complexity of the design, the substrate material used, the number of layers, the dimensions of the board, the quantity ordered, and the specific manufacturing processes required. Here are some key factors that can influence the cost:
Design Complexity: The complexity of the circuit design, including the number of layers, fine trace widths, and tight spacing requirements, can significantly impact the cost. More complex designs with tighter tolerances may require specialized manufacturing processes and may incur higher costs.
Substrate Material: The choice of substrate material can also affect the cost. High-performance materials such as polyimide or PTFE (Teflon) tend to be more expensive than standard FR-4 (fiberglass-reinforced epoxy). Specialty materials with enhanced thermal or electrical properties may also come at a premium.
Manufacturing Processes: Certain manufacturing processes, such as laser drilling for microvias, sequential lamination for high layer count boards, and advanced surface finish options like ENIG (Electroless Nickel Immersion Gold), can add to the overall cost of the substrate.
Quantity Ordered: Economies of scale typically apply in PCB manufacturing, meaning that larger quantities often result in lower per-unit costs. Ordering larger volumes of microtrace substrates can help reduce the cost per board.
Lead Time: Shorter lead times may incur additional costs, as expedited manufacturing processes or shipping options may be necessary to meet tight deadlines.
Supplier and Location: The choice of PCB manufacturer and their geographical location can also influence the cost. Manufacturers with advanced capabilities and higher-quality standards may charge premium prices, while offshore manufacturers may offer lower costs but longer lead times and potential quality risks.
Additional Services: Additional services such as design assistance, electrical testing, and assembly services may incur extra charges but can contribute to overall cost savings and efficiency in the long run.
Given the complexity and variability of factors involved, it’s challenging to provide a specific cost without knowing the details of the project. Generally, microtrace substrates tend to be more expensive than standard PCBs due to their specialized requirements and higher precision. It’s advisable to consult with PCB manufacturers or suppliers to obtain accurate cost estimates based on the specific requirements of your project.
What is Microtrace Substrate base material?
The base material used for microtrace substrates can vary depending on the specific requirements of the application. However, some common base materials used for microtrace substrates include:
- Polyimide (PI): Polyimide is a high-performance polymer known for its excellent thermal stability, chemical resistance, and mechanical properties. It is often used in applications requiring flexibility or high-temperature operation, such as flexible circuits and aerospace electronics.
- FR-4 (Fiberglass-Reinforced Epoxy): FR-4 is a widely used substrate material in PCB manufacturing. It consists of a woven fiberglass cloth impregnated with epoxy resin. FR-4 offers good electrical insulation properties, mechanical strength, and dimensional stability, making it suitable for a wide range of electronic applications.
- PTFE (Polytetrafluoroethylene): PTFE, commonly known by the brand name Teflon, is a high-performance fluoropolymer with exceptional electrical insulation properties, chemical resistance, and low dielectric constant. It is often used in high-frequency and high-speed applications where signal integrity is critical.
- Rogers High Frequency Laminates: Rogers Corporation produces a range of high-frequency laminates specifically designed for RF/microwave applications. These laminates offer low dielectric loss, excellent signal stability at high frequencies, and tight dimensional control.
- Metal Core Substrates: In some cases, microtrace substrates may be constructed on metal core substrates, such as aluminum or copper, to provide enhanced thermal management capabilities for power electronics applications.
The choice of base material depends on factors such as thermal requirements, electrical performance, mechanical strength, and cost considerations. Designers typically select the base material that best suits the specific needs of their application while ensuring compatibility with the desired manufacturing processes and performance requirements.
Which company makes Microtrace Substrates?
There are many companies that offer microtrace substrates, including major manufacturers such as Isola and Rogers Corporation in the United States, Panasonic in Japan, and AT&S (Austria Technologie & Systemtechnik AG) in China. These companies have extensive experience and technological expertise in the microelectronics industry, enabling them to provide high-quality microtrace substrate products to meet the requirements of various high-density electronic applications.
As for our company, we are also capable of producing high-quality microtrace substrates. With advanced manufacturing equipment and a skilled technical team, we can achieve complex circuit designs and precision machining to meet customer demands for fine trace widths, tight spacings, and high signal integrity. Our production processes strictly adhere to international standards to ensure stable and reliable product quality.
We offer a variety of substrate material options, including polyimide, FR-4, PTFE, etc., to meet the diverse needs of different applications. Whether in communication, medical, aerospace, or industrial control fields, we can provide customized solutions to help customers achieve their design goals.
As a trusted partner, we are committed to providing customers with excellent product quality, superior customer service, and reliable delivery performance. We are willing to collaborate with customers to drive innovation and development in the field of microelectronics and contribute to their success.
What are the 7 qualities of good customer service?
Good customer service is characterized by several key qualities that contribute to a positive and satisfying experience for customers. Here are seven qualities of good customer service:
- Responsiveness: Good customer service is prompt and responsive to customers’ needs and inquiries. This includes timely assistance, quick resolution of issues, and efficient communication channels to address customer concerns.
- Empathy: Empathy is the ability to understand and relate to customers’ feelings, concerns, and perspectives. Good customer service representatives listen actively, show empathy towards customers’ situations, and strive to find solutions that meet their needs.
- Professionalism: Professionalism entails maintaining a courteous, respectful, and professional demeanor in all interactions with customers. This includes being knowledgeable about products or services, adhering to company policies, and maintaining confidentiality when necessary.
- Clarity: Good customer service involves clear communication that is easy to understand and free of jargon. Customer service representatives should articulate information effectively, provide clear instructions or explanations, and ensure that customers have a clear understanding of the assistance being provided.
- Flexibility: Flexibility is the ability to adapt to customers’ unique preferences, circumstances, and needs. Good customer service involves being flexible and accommodating, offering personalized solutions, and making adjustments as needed to meet customers’ expectations.
- Consistency: Consistency is key to building trust and loyalty with customers. Good customer service is consistent across all touchpoints and interactions, ensuring that customers receive the same level of service regardless of the channel or representative they engage with.
- Problem-solving: Good customer service involves effective problem-solving skills to address customers’ issues and resolve conflicts. This includes identifying root causes, exploring alternative solutions, and taking proactive steps to prevent similar issues from occurring in the future.
By embodying these qualities, businesses can deliver exceptional customer service that fosters positive relationships, promotes customer satisfaction, and contributes to long-term success.
FAQs
What is a microtrace substrate?
A microtrace substrate is a type of printed circuit board (PCB) with extremely fine traces and spacings, designed for high-density electronic applications where precision and signal integrity are critical.
What are the benefits of using microtrace substrates?
Microtrace substrates enable designers to create smaller, more densely packed electronic devices with enhanced performance and functionality. They allow for finer routing of electrical signals, reduced signal loss, and improved thermal management.
What materials are used in microtrace substrates?
Common materials used in microtrace substrates include polyimide, FR-4 (fiberglass-reinforced epoxy), PTFE (polytetrafluoroethylene), and specialty high-frequency laminates. The choice of material depends on factors such as thermal requirements, electrical performance, and cost considerations.
What are the typical applications of microtrace substrates?
Microtrace substrates are used in a wide range of high-density electronic applications, including telecommunications, aerospace, medical devices, automotive electronics, and consumer electronics. They are particularly well-suited for applications requiring miniaturization, high-speed data transmission, and reliability in harsh environments.
What design considerations are important when using microtrace substrates?
Designers working with microtrace substrates need to consider factors such as trace width and spacing, impedance control, thermal management, signal integrity, and manufacturability. Close attention to these factors ensures optimal performance and reliability of the PCB design.
How are microtrace substrates manufactured?
The manufacturing process for microtrace substrates involves several key steps, including substrate selection, copper cladding, photoresist application, exposure and development, etching, surface finish, drilling and via formation, solder mask application, and final inspection.
What factors can affect the cost of microtrace substrates?
The cost of microtrace substrates can vary depending on factors such as design complexity, substrate material, manufacturing processes, quantity ordered, lead time, supplier, and additional services required.
Where can I find suppliers of microtrace substrates?
Suppliers of microtrace substrates can be found through online directories, industry trade shows, and direct inquiries to PCB manufacturers specializing in high-density and precision electronics.