Millimeter Wave Radar PCB Manufacturer
Millimeter Wave Radar PCB Manufacturer,Millimeter Wave Radar PCBs are specialized circuit boards crucial for high-frequency radar systems, operating typically between 24 GHz to 77 GHz. These PCBs are designed with precision to ensure minimal signal loss and maintain signal integrity necessary for accurate object detection and distance measurement. They play a vital role in advanced driver-assistance systems (ADAS) found in modern vehicles, enabling features such as adaptive cruise control and collision avoidance. Utilizing advanced materials like PTFE-based laminates, Millimeter Wave Radar PCBs support reliable performance in demanding environments, contributing to enhanced safety and efficiency in automotive and industrial applications.
What is a Millimeter Wave Radar PCB?
A Millimeter Wave Radar PCB refers to a printed circuit board specifically designed for millimeter wave radar systems. These PCBs are crucial components in radar technology, particularly in automotive applications for advanced driver-assistance systems (ADAS) and autonomous vehicles.
Millimeter wave radar operates at frequencies typically ranging from 24 GHz to 77 GHz, enabling high-resolution sensing capabilities essential for detecting objects with precision and accuracy. The PCBs used in these radar systems are engineered to handle these high frequencies effectively, ensuring minimal signal loss and maintaining signal integrity.
Design considerations for Millimeter Wave Radar PCBs include impedance control, signal routing, and material selection to support high-frequency operations. They are often multi-layered boards with carefully designed transmission lines and ground planes to manage electromagnetic interference (EMI) and ensure reliable performance.
In automotive radar systems, these PCBs facilitate the transmission and reception of radar signals, allowing the radar sensor to detect objects, measure their distance, and ascertain their speed relative to the vehicle. They play a critical role in enhancing vehicle safety by enabling features such as adaptive cruise control, collision avoidance, and pedestrian detection.
Overall, Millimeter Wave Radar PCBs are specialized circuit boards tailored to meet the demanding requirements of millimeter wave radar systems, contributing significantly to the advancement of automotive technology and safety.
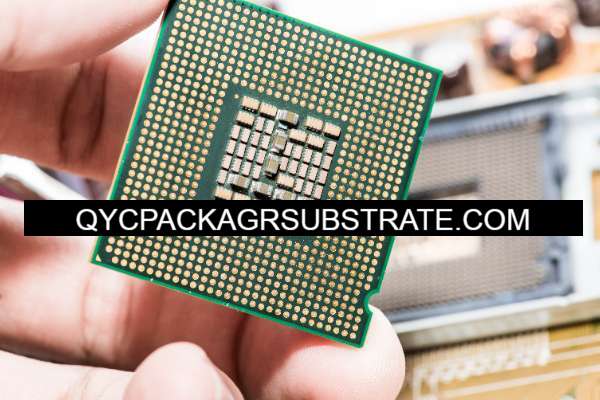
Millimeter Wave Radar PCB Manufacturer
What are the Millimeter Wave Radar PCB Design Guidelines?
Designing PCBs for millimeter wave radar systems requires adherence to specific guidelines to ensure optimal performance and reliability. Here are some key design guidelines for Millimeter Wave Radar PCBs:
- Impedance Control: Maintaining consistent impedance throughout the PCB is crucial for minimizing signal reflections and ensuring efficient signal transmission. This involves careful design of trace widths, spacing, and layer stack-up.
- Material Selection: Choosing appropriate PCB materials with low dielectric loss and stable electrical properties at high frequencies (typically 24 GHz to 77 GHz) is essential. Materials like high-frequency laminates (e.g., PTFE-based) are often preferred.
- Transmission Line Design: High-frequency signals require controlled impedance transmission lines (microstrip or stripline) to minimize signal loss and maintain signal integrity. Trace widths, dielectric thickness, and spacing to ground planes must be carefully calculated.
- Grounding: A solid and continuous ground plane is critical to provide a low-impedance return path for high-frequency signals and to minimize electromagnetic interference (EMI). Proper grounding techniques, via placements, and stitching are necessary.
- Signal Routing: Signal traces should be kept as short and direct as possible to minimize transmission line losses and signal degradation. Avoid sharp bends and use gradual curves where necessary to maintain impedance continuity.
- Component Placement: Place components strategically to minimize parasitic effects and ensure optimal signal integrity. Position high-frequency components closer to each other and minimize the distance to the antenna or radar module.
- Shielding and EMI Considerations:Implement shielding techniques such as grounded copper pours or shielding cans around sensitive circuitry to reduce EMI and ensure the integrity of millimeter wave signals.
- Thermal Management: High-frequency circuits can generate heat, so consider thermal management techniques such as thermal vias and heat sinks if necessary to maintain PCB reliability.
- Testing and Validation: Conduct thorough testing and validation of the PCB design using simulation tools (e.g., electromagnetic simulation software) and prototype testing to ensure that the design meets performance specifications.
- Compliance and Standards: Ensure the PCB design complies with relevant industry standards and regulatory requirements for radar systems, especially regarding electromagnetic emissions and susceptibility.
By following these design guidelines, engineers can develop Millimeter Wave Radar PCBs that deliver high-performance, reliable operation in demanding automotive radar applications and other millimeter wave radar systems.
What is the Millimeter Wave Radar PCB Fabrication Process?
The fabrication process for Millimeter Wave Radar PCBs involves several specialized steps to ensure the boards meet the stringent requirements for high-frequency operation. Here’s an overview of the typical fabrication process:
- Design Preparation: The process begins with the creation of a detailed PCB design based on the specific requirements of the millimeter wave radar system. This includes schematic capture, component placement, signal routing, and adherence to design guidelines for high-frequency applications.
- Material Selection: High-frequency PCBs require specialized materials with low dielectric constant and low loss tangent to minimize signal loss at millimeter wave frequencies (typically 24 GHz to 77 GHz). Common materials include PTFE-based laminates such as Rogers 4000 series or similar high-frequency substrates.
- Preparation of Substrate: The chosen substrate material is prepared by cutting it to the required dimensions for the PCB. Surface preparation involves cleaning and ensuring the substrate surface is free from contaminants that could affect bonding.
- Copper Cladding: A thin layer of copper foil is laminated onto both sides of the substrate. This copper foil forms the conductive layers of the PCB where traces, pads, and ground planes will be etched.
- Circuit Patterning (Etching): Using a photoresist process, a pattern of the PCB circuitry is transferred onto the copper foil. This involves applying a photoresist layer, exposing it to UV light through a photomask that defines the circuit pattern, and then developing and etching away the unexposed copper using chemical etchants.
- Drilling: Precision holes are drilled into the PCB to accommodate component leads, vias, and mounting holes. For millimeter wave radar PCBs, these holes must be drilled with high accuracy to maintain signal integrity and impedance control.
- Through-Hole Plating and Vias:Through-holes and vias are plated with copper to connect different layers of the PCB. This is crucial for creating signal paths and grounding connections that maintain impedance and reduce electromagnetic interference.
- Surface Finish: The exposed copper surfaces are coated with a surface finish to protect against oxidation and facilitate soldering during component assembly. Common surface finishes include immersion gold (ENIG), immersion silver, or OSP (Organic Solderability Preservatives).
- Solder Mask Application: A solder mask is applied over the PCB except where soldering is required (pads, vias, and holes). This helps prevent solder bridges and ensures the integrity of the PCB traces.
- Silkscreen Printing: Component designators, polarity marks, and other identifying information are printed onto the PCB surface using a silkscreen layer.
- Testing and Inspection: The fabricated PCBs undergo electrical testing to verify connectivity, impedance control, and ensure that there are no short circuits or open circuits. Visual inspection is also conducted to check for defects and ensure quality.
- Final Fabrication Steps: After testing and inspection, the PCBs are separated from the panel, and any final machining (e.g., edge routing) is performed. They are then ready for assembly with electronic components to form the complete millimeter wave radar system.
The fabrication process for Millimeter Wave Radar PCBs requires precision and attention to detail at every step to ensure the boards meet the high-frequency performance requirements essential for radar applications in automotive safety systems and other advanced technologies.
How do you manufacture a Millimeter Wave Radar PCB?
Manufacturing a Millimeter Wave Radar PCB involves a detailed process tailored for high-frequency operation. Here’s a structured outline of the typical manufacturing steps:
- Design and Layout Preparation: Begin with PCB design using specialized software. Design considerations include impedance control, signal integrity, and placement of components critical for millimeter wave radar systems.
- Material Selection: Choose high-frequency PCB materials such as PTFE-based laminates (e.g., Rogers 4000 series) known for low dielectric loss and stable performance at millimeter wave frequencies (24 GHz to 77 GHz).
- Substrate Preparation: Cut the substrate material (e.g., Rogers laminate) to size. Clean and prepare the surface to ensure proper adhesion and cleanliness for subsequent processes.
- Copper Cladding: Laminate thin copper foil onto both sides of the substrate material. This forms the conductive layers where circuit traces, pads, and ground planes will later be etched.
- Circuit Patterning (Etching): Apply a photoresist layer to the copper-clad substrate. Use UV light through a photomask to transfer the PCB circuit pattern onto the photoresist. Develop and etch away the exposed copper using chemical etchants, leaving behind the desired copper traces and features.
- Drilling: Precision-drill holes into the PCB for component leads, vias, and mounting holes. Drill with high accuracy to ensure precise alignment and maintain signal integrity at millimeter wave frequencies.
- Through-Hole Plating and Vias:Plate the drilled holes with copper to establish electrical connections between different layers of the PCB. This process, crucial for signal paths and grounding, ensures impedance control and reduces electromagnetic interference.
- Surface Finish Application: Coat exposed copper surfaces with a surface finish (e.g., immersion gold, immersion silver, OSP) to protect against oxidation and facilitate soldering during component assembly.
- Solder Mask Application: Apply solder mask over the PCB surface, leaving openings for solder pads, vias, and holes. This protective layer prevents solder bridges and ensures PCB trace integrity during assembly.
- Silkscreen Printing: Print component designators, polarity marks, and other identifying information on the PCB surface using a silkscreen layer. This aids in component placement and assembly.
- Testing and Inspection: Conduct electrical testing to verify connectivity, impedance levels, and functionality. Inspect visually for defects such as shorts, opens, or misalignments. Ensure compliance with design specifications and quality standards.
- Final Fabrication Steps: After testing and inspection, separate the individual PCBs from the panel. Perform any final machining processes (e.g., edge routing) as necessary to prepare for assembly.
Manufacturing Millimeter Wave Radar PCBs requires meticulous attention to detail throughout each step to meet the stringent requirements of high-frequency operation. Following these processes ensures the PCBs achieve reliable performance crucial for radar systems in automotive safety, telecommunications, and other advanced applications.
How much should a Millimeter Wave Radar PCB cost?
The cost of a Millimeter Wave Radar PCB can vary significantly depending on several factors:
- Complexity of Design: PCBs for millimeter wave radar systems often have complex designs due to high-frequency requirements, impedance control, and signal integrity considerations. More complex designs typically involve higher costs.
- Materials Used: High-frequency PCB materials like PTFE-based laminates (e.g., Rogers 4000 series) are more expensive compared to standard FR4 materials due to their superior electrical properties. The choice of material significantly influences the cost.
- Manufacturing Process: Processes such as precision drilling, controlled impedance etching, and high-quality surface finishes (e.g., immersion gold) add to the manufacturing cost. Advanced manufacturing techniques required for high-frequency PCBs can also impact pricing.
- Quantity: Economies of scale apply in PCB manufacturing. Larger quantities generally reduce the cost per unit due to efficiencies in production and setup costs amortization.
- Supplier and Location: PCB costs can vary based on the supplier and their location. Suppliers with expertise in high-frequency PCB manufacturing may charge differently based on their capabilities and overheads.
- Additional Services: Additional services such as testing, certification, and expedited manufacturing can add to the overall cost.
As a rough estimate, Millimeter Wave Radar PCBs can range from tens to hundreds of dollars per unit for production quantities. Prototypes and smaller volumes typically cost more per unit due to setup costs and lower economies of scale. For precise pricing, it’s advisable to consult with PCB manufacturers and suppliers who specialize in high-frequency and radar system PCBs. Providing detailed specifications and quantities will help in obtaining accurate quotes.
What is Millimeter Wave Radar PCB base material?
The base material used for Millimeter Wave Radar PCBs is typically a specialized high-frequency laminate. These materials are chosen for their ability to maintain stable electrical properties at frequencies typically ranging from 24 GHz to 77 GHz, which are common in millimeter wave radar applications.
Some of the commonly used base materials for Millimeter Wave Radar PCBs include:
- PTFE-Based Laminates (e.g., Rogers 4000 Series): These laminates are based on Polytetrafluoroethylene (PTFE) and are known for their low dielectric loss and stable dielectric constant across a wide range of frequencies. They are ideal for applications requiring high-frequency performance and are widely used in radar systems.
- Hybrid Laminates: Some PCB designs may utilize hybrid materials that combine PTFE with other substrates to achieve specific performance characteristics such as improved mechanical strength or reduced cost while maintaining adequate high-frequency properties.
- Ceramic-Based Laminates: Certain advanced radar systems may employ ceramic-based laminates. These materials offer excellent thermal conductivity and mechanical stability, which can be advantageous in rugged environments or applications requiring high power handling.
- Specialized High-Frequency Laminates:There are various proprietary high-frequency laminates available from different manufacturers, each designed to meet specific requirements of radar applications, including impedance control, signal integrity, and thermal management.
These base materials are selected based on their dielectric constant, dissipation factor, thermal conductivity, and mechanical properties, all of which are critical for ensuring the reliable operation of millimeter wave radar PCBs. The choice of base material significantly influences the performance, cost, and manufacturability of the PCBs used in advanced radar systems.
Which company makes Millimeter Wave Radar PCBs?
Millimeter Wave Radar PCBs are specialized printed circuit boards used in high-frequency radar systems, typically for applications like Advanced Driver Assistance Systems (ADAS) in automotive safety and other radar applications. Several companies in the market manufacture these high-frequency PCBs, including well-known electronic materials and PCB manufacturers such as Rogers Corporation, Taconic Advanced Dielectric Division, and Isola Group.
These companies focus on developing and producing high-frequency PCB materials, including PTFE-based laminates like the Rogers 4000 series. These materials offer excellent dielectric properties and stable high-frequency characteristics, making them ideal for the requirements of millimeter wave radar systems. Through precise manufacturing processes and stringent quality control, they ensure the PCBs maintain signal integrity and transmission efficiency during high-frequency operations, meeting the high-performance and reliability demands of radar systems.
For our company, if there is a need to manufacture Millimeter Wave Radar PCBs, we possess advanced PCB manufacturing facilities and a skilled technical team capable of meeting stringent requirements for high-frequency PCBs. Our strengths include:
- Professional Design and Engineering Team: We have experienced PCB design engineers and technical personnel who can design and optimize PCB layouts and circuits tailored to millimeter wave radar system requirements.
- Advanced Manufacturing Equipment: We invest in state-of-the-art PCB manufacturing equipment and technologies, including precision drilling machines, precise chemical etching processes, and capabilities for handling high-frequency materials, ensuring high quality and reliability throughout the PCB manufacturing process.
- Strict Quality Control: We adhere to rigorous quality management systems, ensuring stringent control and inspection from material selection and procurement to every stage of production, ensuring each Millimeter Wave Radar PCB meets design specifications and customer requirements.
- Customized Customer Service: We offer flexible responses to customer customization needs, including different sizes, layer configurations, material selections, surface treatments, and special requirements for PCB manufacturing, catering to various specific demands of millimeter wave radar applications.
In conclusion, our company has the technical capabilities and manufacturing expertise to produce Millimeter Wave Radar PCBs, committed to delivering high-quality, high-performance PCB solutions that support innovation and development in automotive safety, communications, and other high-frequency application fields.
What are the 7 qualities of good customer service?
Good customer service is characterized by several key qualities that contribute to a positive experience for customers. Here are seven qualities that define good customer service:
- Responsiveness: Good customer service involves being prompt and proactive in addressing customer inquiries, issues, or requests. Responding in a timely manner shows respect for the customer’s time and enhances satisfaction.
- Empathy: Empathy involves understanding and acknowledging the customer’s feelings, concerns, and perspectives. It requires listening attentively, showing compassion, and demonstrating a willingness to help resolve their issues.
- Clear Communication: Effective communication is essential in customer service. It means providing clear and accurate information, explaining processes or solutions in a way that is easily understood by the customer, and avoiding jargon or technical language that might confuse them.
- Knowledgeability: Good customer service representatives are knowledgeable about their products, services, and company policies. They should be able to answer questions accurately, provide relevant information, and offer helpful advice or recommendations.
- Problem-Solving Skills: Customers often reach out to customer service when they encounter problems or have questions. Good customer service involves being able to effectively analyze issues, identify solutions, and resolve problems efficiently to the customer’s satisfaction.
- Professionalism: Professionalism in customer service includes maintaining a positive and courteous attitude, even in challenging situations. It involves treating customers with respect, being patient and calm, and maintaining integrity and honesty in interactions.
- Personalization: Providing personalized service involves recognizing and valuing each customer as an individual. This can include remembering past interactions or preferences, addressing customers by name, and tailoring solutions or recommendations based on their specific needs or circumstances.
By embodying these qualities, organizations can foster strong customer relationships, build trust and loyalty, and differentiate themselves in competitive markets through exceptional customer service experiences.
FAQs
What are Millimeter Wave Radar PCBs used for?
Millimeter Wave Radar PCBs are used in radar systems operating at frequencies typically between 24 GHz to 77 GHz. They are essential components in automotive applications such as Advanced Driver Assistance Systems (ADAS), enabling features like adaptive cruise control, collision avoidance, and autonomous driving.
What are the key design considerations for Millimeter Wave Radar PCBs?
Key design considerations include impedance control to minimize signal loss, material selection for stable high-frequency performance (e.g., PTFE-based laminates), precise signal routing to maintain signal integrity, and effective thermal management due to potential heat generation at high frequencies.
Which materials are suitable for Millimeter Wave Radar PCBs?
Suitable materials include PTFE-based laminates like Rogers 4000 series, which offer low dielectric loss and stable electrical properties at high frequencies. Other options may include ceramic-based laminates for specific applications requiring superior thermal management.
What manufacturing processes are involved in producing Millimeter Wave Radar PCBs?
Manufacturing processes include substrate preparation, copper cladding, precise etching for circuit patterning, drilling for vias and component mounting holes, through-hole plating for interconnection, surface finish application (e.g., immersion gold), solder mask application, and quality testing to ensure reliability and performance.
How can I ensure the quality and reliability of Millimeter Wave Radar PCBs?
Ensuring quality involves using high-grade materials, adhering to strict manufacturing standards and processes, conducting thorough testing (e.g., electrical testing, impedance control verification), and complying with industry standards and customer specifications.
What are the challenges in designing and manufacturing Millimeter Wave Radar PCBs?
Challenges include maintaining precise impedance control across high-frequency circuits, managing signal integrity in complex layouts, addressing thermal management due to heat dissipation, and ensuring compatibility with stringent automotive safety and regulatory requirements.