Mini LED PCB Fabrication
Mini LED PCB Fabrication. Ultrathin LED PCBs, Minimum clearance and Microtrace LED PCB manufacturer, we have made 40um pads to pads gap LED PCBs with high quality and fast lead time.
Mini LED PCBs, or Mini LED printed circuit boards, are specialized electronic components designed to accommodate Mini LEDs. These smaller LEDs offer significant advantages, including higher pixel density, enhanced brightness, and improved energy efficiency compared to traditional LEDs. Mini LED PCBs play a crucial role in various applications such as high-resolution displays, backlighting for LCD screens, automotive lighting, wearable devices, and general lighting fixtures.
Their compact size and superior performance make them ideal for applications where space is limited or where high levels of brightness and resolution are required. Mini LED PCBs are meticulously designed to ensure precise alignment and electrical connections for each Mini LED, often in dense arrays or grids. They undergo rigorous manufacturing processes, including design layout, material selection, substrate preparation, Mini LED placement, soldering, testing, and quality control. Overall, Mini LED PCBs represent a cutting-edge solution for achieving superior display quality, energy efficiency, and versatility in a wide range of electronic devices and lighting systems.
What is a Mini LED PCB?
A Mini LED PCB (Printed Circuit Board) is a type of circuit board designed specifically to accommodate Mini LEDs. Mini LEDs are smaller versions of traditional LEDs (Light Emitting Diodes), typically with a size ranging from around 100 to 200 micrometers. These smaller LEDs offer several advantages, including higher pixel density, improved brightness, and better energy efficiency.
The Mini LED PCB provides a platform for mounting and connecting these smaller LEDs. It’s engineered to provide precise alignment and electrical connections for each Mini LED, often in a dense array or grid pattern. This type of PCB is commonly used in applications such as high-resolution displays, backlighting for LCD screens, and various types of lighting fixtures.
Due to their compact size and high performance, Mini LED PCBs are increasingly being used in products where traditional LEDs or other lighting technologies may not offer the same level of performance or flexibility.
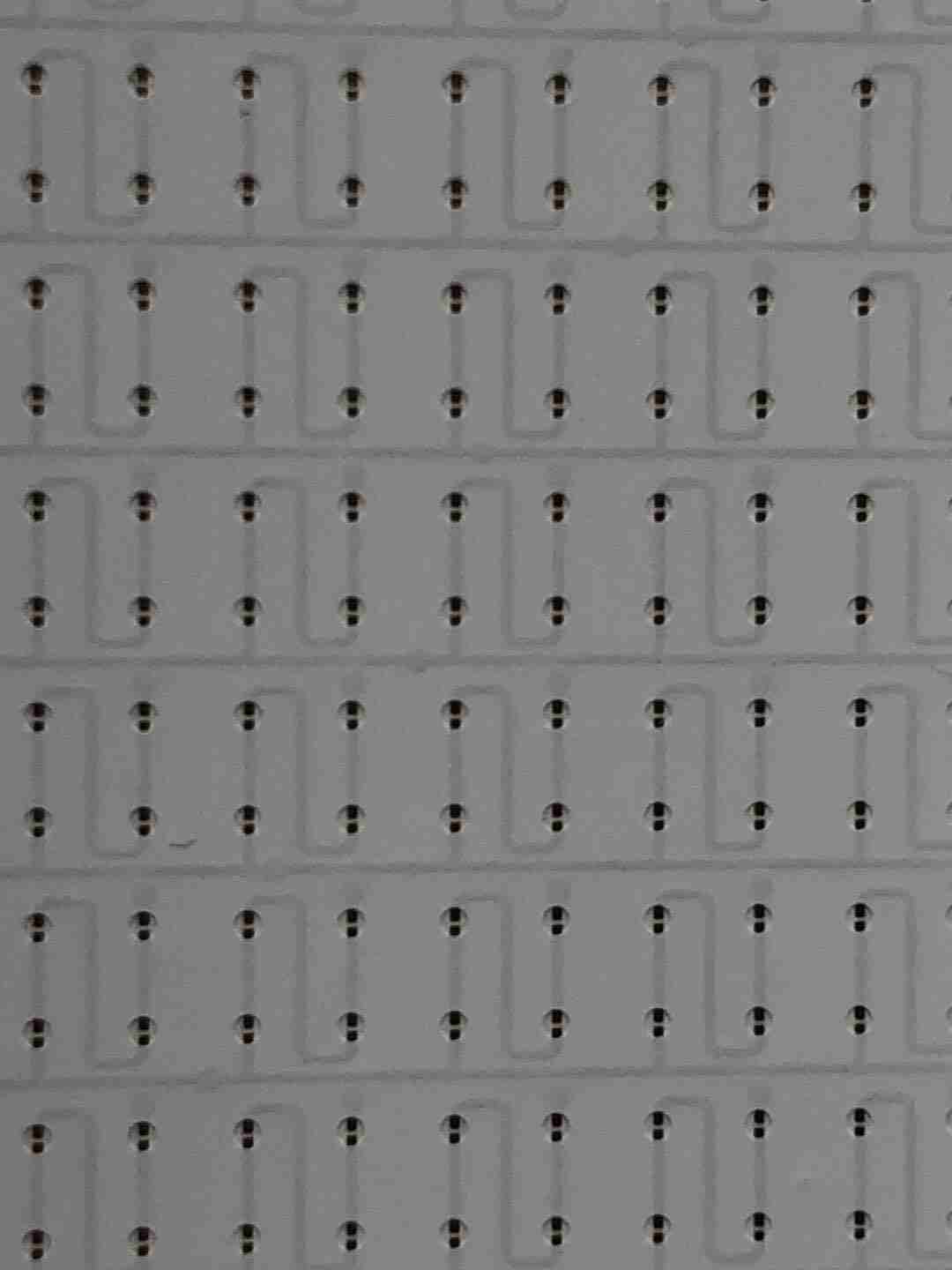
Mini LED PCB
What are the Mini LED PCB Design Guidelines?
Designing Mini LED PCBs requires careful consideration of several factors to ensure optimal performance and reliability. Here are some general guidelines:
- Mini LED Placement and Density: Determine the placement and density of Mini LEDs on the PCB to achieve the desired resolution and brightness. Consider factors such as viewing distance, pixel pitch, and required luminance levels.
- Thermal Management: Mini LEDs can generate heat, so effective thermal management is crucial to prevent overheating and ensure long-term reliability. Design the PCB with appropriate heat dissipation features such as thermal vias, copper traces, and heatsinks.
- Electrical Connections: Ensure proper electrical connections between the Mini LEDs and the PCB. Use techniques such as soldering, wire bonding, or flip-chip bonding, depending on the specific requirements of the application.
- PCB Material Selection: Choose PCB materials with good thermal conductivity and electrical properties to optimize performance and reliability. High-temperature materials may be necessary to withstand the heat generated by the Mini LEDs.
- Routing and Traces: Pay attention to routing and traces to minimize signal interference, voltage drop, and impedance mismatch. Use wide traces for power lines and minimize signal loop areas to reduce electromagnetic interference (EMI).
- Solder Mask and Silkscreen: Apply solder mask to protect exposed copper traces and pads from oxidation and environmental factors. Use silkscreen for labeling components and indicating polarity to aid in assembly and troubleshooting.
- Test Points and Probing:Include test points on the PCB for debugging and testing purposes. Ensure accessibility for probing during manufacturing and testing to facilitate quality control and troubleshooting.
- Component Placement: Optimize component placement to minimize signal delays and ensure signal integrity. Consider the proximity of Mini LEDs to other components such as drivers, controllers, and connectors.
- Environmental Considerations: Design the PCB to withstand environmental factors such as temperature variations, humidity, and mechanical stress. Use conformal coating or encapsulation to protect the PCB from moisture and contaminants.
- Manufacturability and Assembly: Design the PCB with manufacturability and assembly in mind. Minimize complex assembly processes and consider the capabilities of PCB manufacturers and assembly partners.
By following these guidelines, you can design Mini LED PCBs that meet the performance, reliability, and manufacturability requirements of your application.
What is the Mini LED PCB Fabrication Process?
The fabrication process for Mini LED PCBs involves several steps, from designing the layout to manufacturing the final board. Here’s an overview of the typical Mini LED PCB fabrication process:
- Design/Layout: The process begins with the design of the PCB layout using specialized PCB design software. Designers place Mini LEDs, other components, and routing traces according to the specific requirements of the application, following design guidelines for Mini LED PCBs.
- Gerber File Generation: Once the layout design is complete, Gerber files are generated. Gerber files contain the information needed for manufacturing the PCB, including layer information, component placement, routing traces, and drill holes.
- Material Selection: Select appropriate materials for the PCB based on factors such as thermal conductivity, electrical properties, and durability. High-quality materials with good heat dissipation properties are often chosen for Mini LED PCBs to ensure optimal performance and reliability.
- Panelization: Multiple PCBs are often fabricated together on a single panel to optimize manufacturing efficiency. Panelization involves arranging the individual PCB designs on a larger panel, allowing for simultaneous fabrication of multiple boards.
- Preparation of Substrate: The chosen substrate material, typically a rigid or flexible base material like FR-4 or polyimide, is prepared for the fabrication process. This may involve cutting the substrate to size and applying a layer of copper foil to one or both sides.
- Photoresist Application: A layer of photoresist is applied to the copper surface of the substrate. The photoresist acts as a mask for the subsequent etching process, protecting the areas of copper that will form the traces and pads on the final PCB.
- Exposure and Development: The photoresist layer is exposed to UV light through a photomask, which contains the pattern of the PCB traces and pads. The exposed photoresist is then developed, removing the unexposed areas and leaving behind the patterned photoresist mask.
- Etching: The exposed copper areas not covered by the photoresist mask are etched away using an etchant solution. This creates the traces and pads on the PCB, defining the electrical connections between components.
- Drilling: Holes are drilled into the PCB substrate at designated locations for through-hole components, mounting holes, and vias. Precision drilling equipment is used to ensure accuracy and consistency in hole placement.
- Plating: Copper plating is applied to the walls of the drilled holes to create electrical connections between the layers of the PCB and reinforce the vias.
- Solder Mask Application: A layer of solder mask is applied over the surface of the PCB, covering the copper traces and pads while exposing the areas for soldering components. The solder mask helps protect the PCB from oxidation and environmental damage.
- Silkscreen Printing: Component labels, polarity indicators, and other markings are printed onto the PCB surface using silkscreen printing. This aids in component placement, assembly, and troubleshooting.
- Surface Finish: A surface finish is applied to the exposed copper surfaces of the PCB to improve solderability and prevent oxidation. Common surface finishes include HASL (Hot Air Solder Leveling), ENIG (Electroless Nickel Immersion Gold), and OSP (Organic Solderability Preservatives).
- Testing and Inspection: The fabricated PCBs undergo testing and inspection to ensure quality and functionality. This may include electrical testing, visual inspection, and automated optical inspection (AOI) to detect any defects or errors in the fabrication process.
- Separation: After fabrication and testing, the individual PCBs are separated from the panel using cutting or routing equipment, resulting in the final Mini LED PCBs ready for assembly and integration into electronic devices.
Throughout the fabrication process, quality control measures are implemented to ensure that the Mini LED PCBs meet the specified design requirements and industry standards for performance, reliability, and durability. Collaboration between designers, manufacturers, and quality assurance teams is essential to ensure a successful fabrication process and the production of high-quality Mini LED PCBs.
How do you manufacture a Mini LED PCB?
Manufacturing a Mini LED PCB involves a series of steps that integrate Mini LEDs onto a printed circuit board (PCB). Here’s a comprehensive overview of the typical manufacturing process:
- Design and Layout: The process begins with designing the layout of the PCB using specialized PCB design software. Designers place Mini LEDs and other components on the PCB, considering factors such as spacing, alignment, and electrical connections.
- Material Selection: Choose appropriate materials for the PCB based on factors such as thermal conductivity, electrical properties, and durability. High-quality materials with good heat dissipation properties are often chosen for Mini LED PCBs to ensure optimal performance and reliability.
- Substrate Preparation: Prepare the substrate material, typically a rigid or flexible base material like FR-4 or polyimide, for the manufacturing process. This may involve cutting the substrate to size and cleaning the surface to remove any contaminants.
- Solder Mask Application: Apply a layer of solder mask to the surface of the substrate using a screen printing or spray coating process. The solder mask helps protect the PCB from oxidation and environmental damage while exposing the areas for soldering components.
- Silkscreen Printing: Print component labels, polarity indicators, and other markings onto the PCB surface using silkscreen printing. This aids in component placement, assembly, and troubleshooting.
- Placement of Mini LEDs: Use pick-and-place machines or manual assembly techniques to accurately place Mini LEDs onto the PCB according to the design layout. Precision is crucial to ensure proper alignment and spacing of the Mini LEDs.
- Soldering: Solder the Mini LEDs onto the PCB using reflow soldering or other appropriate soldering techniques. Reflow soldering involves heating the PCB and components to a specific temperature, causing the solder paste to melt and form a secure electrical connection between the Mini LEDs and the PCB.
- Quality Control: Conduct visual inspection and automated optical inspection (AOI) to verify the placement and soldering of Mini LEDs and detect any defects or errors. This ensures that the PCB meets the specified design requirements and industry standards for performance and reliability.
- Testing: Test the electrical functionality of the Mini LED PCB using electrical testing equipment to verify proper operation and performance. This may include continuity testing, voltage testing, and functionality testing to ensure that the Mini LEDs illuminate as intended.
- Finishing: Apply any necessary finishing processes, such as surface treatment or coating, to enhance the durability and performance of the Mini LED PCB. This may include applying a surface finish such as HASL (Hot Air Solder Leveling), ENIG (Electroless Nickel Immersion Gold), or OSP (Organic Solderability Preservatives).
- Packaging and Shipping: Once the Mini LED PCBs pass quality control and testing, they are packaged and prepared for shipping to customers or assembly into final products. Proper packaging helps protect the PCBs during transit and storage until they are ready for use.
Throughout the manufacturing process, rigorous quality control measures are implemented to ensure that the Mini LED PCBs meet the specified design requirements and industry standards for performance, reliability, and durability. Collaboration between designers, manufacturers, and quality assurance teams is essential to ensure a successful manufacturing process and the production of high-quality Mini LED PCBs.
How much should a Mini LED PCB cost?
The cost of a Mini LED PCB can vary significantly depending on various factors such as the size, complexity, quantity, materials used, manufacturing processes involved, and supplier/vendor pricing. Here are some key factors that can influence the cost:
- Size and Complexity: Larger and more complex Mini LED PCBs typically require more materials and manufacturing processes, which can increase the cost.
- Material Selection: The choice of materials for the PCB substrate, copper layers, solder mask, and surface finish can impact the cost. High-quality materials with special features (such as high thermal conductivity or impedance control) may increase the cost compared to standard materials.
- Manufacturing Processes: Different manufacturing processes, such as soldering techniques (e.g., reflow soldering), surface finishing methods, and testing procedures, can affect the cost. More advanced or specialized processes may incur higher costs.
- Quantity: Generally, ordering larger quantities of Mini LED PCBs can lead to lower unit costs due to economies of scale. However, smaller prototype or low-volume orders may have higher unit costs.
- Lead Time: Urgent or expedited orders may incur additional costs for faster manufacturing and shipping.
- Supplier/Vendor Pricing: Different PCB manufacturers or suppliers may offer varying pricing based on their capabilities, capacity, location, and overhead costs.
As a rough estimate, the cost of Mini LED PCBs can range from a few dollars to several tens or even hundreds of dollars per unit, depending on the factors mentioned above. For more accurate pricing, it’s advisable to request quotes from multiple PCB manufacturers based on your specific requirements and volume needs. Additionally, consider factors such as quality, reliability, and customer service when selecting a PCB manufacturer to ensure the best value for your investment.
What is Mini LED PCB base material?
The choice of base material for Mini LED PCBs depends on the specific requirements of the application, including thermal management, electrical performance, and mechanical stability. Some common base materials used for Mini LED PCBs include:
- FR-4 (Flame Retardant-4): FR-4 is a widely used standard material for PCBs due to its excellent electrical insulation properties, mechanical strength, and cost-effectiveness. It consists of a woven fiberglass substrate impregnated with epoxy resin.
- Metal Core PCB (MCPCB):MCPCBs feature a metal core, typically aluminum or copper, which provides superior thermal conductivity compared to traditional FR-4 substrates. MCPCBs are often preferred for applications requiring efficient heat dissipation, such as high-power LED lighting.
- Flexible PCB (FPC): Flexible PCBs are made of flexible polymer materials such as polyimide (PI) or polyester (PET). They are suitable for applications where space constraints or mechanical flexibility are important, such as curved displays or wearable electronics.
- Ceramic PCB: Ceramic-based PCBs offer excellent thermal conductivity, high mechanical strength, and stability at high temperatures. They are often used in high-power and high-frequency applications where thermal management is critical.
- High-Performance Substrates: Some advanced applications may require specialized high-performance substrates with enhanced properties such as low dielectric constant (Dk), low loss tangent (Df), or high thermal conductivity. Examples include materials like Rogers Corporation’s RO4000 series or Taconic’s TLY series.
The choice of base material depends on factors such as thermal management requirements, electrical performance, mechanical stability, cost constraints, and specific application needs. Designers often select the most suitable material based on a balance of these factors to ensure optimal performance and reliability of Mini LED PCBs.
Which company makes Mini LED PCBs?
There are many companies globally specializing in the production and supply of Mini LED PCBs (Printed Circuit Boards). These companies typically have advanced manufacturing technologies and extensive industry experience to meet the needs of various industries and applications. For example, companies like Innolux Corporation and AU Optronics Corporation in Taiwan, as well as Samsung Electronics Co. Ltd. in South Korea, are significant players in this field. These enterprises not only offer standard Mini LED PCBs but also customize products according to specific customer requirements.
Our company also possesses the capability to manufacture Mini LED PCBs. We offer services covering the entire process from design and manufacturing to testing, ensuring the delivery of high-performance and reliable products. Equipped with advanced manufacturing technologies and equipment, our production facilities can handle various complex designs and bulk order requirements.
Our company’s capabilities for Mini LED PCBs production include:
- Design and Development: We have a team of experienced engineers proficient in using the latest PCB design software for high-precision design work. We provide customized design services tailored to specific customer needs and application scenarios, ensuring the final product perfectly meets the performance and functional requirements of our clients.
- Material Selection: Depending on the specific requirements of Mini LED PCBs, we select suitable base materials such as FR-4, aluminum-based, copper-based, or ceramic-based substrates. We also provide solutions for high thermal conductivity and low thermal resistance as needed to optimize the product’s thermal management.
- High-Precision Manufacturing: We utilize high-precision manufacturing equipment, including automated pick-and-place machines, high-temperature reflow soldering, and precise inspection equipment. These advanced facilities ensure accurate placement and soldering of tiny Mini LEDs while ensuring every PCB meets stringent quality standards.
- Testing and Quality Control:Every Mini LED PCB produced undergoes comprehensive functional and performance testing, including electrical testing, thermal characterization, and optical testing. Through these rigorous testing procedures, we ensure each PCB exhibits optimal performance and long-term reliability.
- Customer Service and Technical Support:We provide comprehensive customer service and technical support to ensure customers receive effective assistance and consultation throughout the entire purchasing and usage process. Our technical team is readily available to address any inquiries and provide necessary technical guidance and support.
In summary, whether you require standard products or customized solutions, our company can deliver Mini LED PCBs that meet high standards. We are committed to meeting all your needs through continuous technological innovation and high-quality customer service.
What are the 7 qualities of good customer service?
Good customer service is characterized by several key qualities that contribute to positive customer experiences and satisfaction. Here are seven essential qualities of good customer service:
- Effective Communication:Good customer service representatives possess strong communication skills, both verbal and written. They listen actively to customers, ask relevant questions to understand their needs, and provide clear and concise responses. Effective communication fosters trust and ensures that customers feel heard and valued.
- Empathy and Understanding: Empathy is crucial in customer service as it allows representatives to understand and relate to customers’ emotions, concerns, and frustrations. Empathetic customer service representatives demonstrate genuine care and concern for customers’ well-being, which helps build rapport and strengthen relationships.
- Problem-Solving Skills: Good customer service involves being proactive in resolving customer issues and addressing their concerns effectively. Customer service representatives should be resourceful, creative, and quick-thinking when solving problems, striving to find satisfactory solutions that exceed customers’ expectations.
- Product Knowledge: A thorough understanding of the products or services offered is essential for providing excellent customer service. Customer service representatives should be knowledgeable about the features, benefits, and usage of the products/services to assist customers accurately and provide helpful recommendations.
- Patience and Courtesy: Dealing with customers, especially those who are upset or frustrated, requires patience and courtesy. Good customer service representatives remain calm and composed, even in challenging situations, and treat customers with respect and professionalism at all times.
- Efficiency and Timeliness: Time is valuable to customers, so good customer service involves providing prompt and efficient assistance. Customer service representatives should strive to resolve issues in a timely manner, minimize wait times, and follow up promptly to ensure customer satisfaction.
- Adaptability and Flexibility: Customer service situations can vary greatly, so it’s essential for representatives to be adaptable and flexible in their approach. They should be able to adjust their communication style, problem-solving strategies, and service delivery methods to meet the unique needs of each customer and situation.
By embodying these qualities, organizations can deliver exceptional customer service experiences that foster loyalty, positive word-of-mouth, and long-term success.
FAQs
What are Mini LED PCBs?
Mini LED PCBs are printed circuit boards designed specifically to accommodate Mini LEDs. These smaller LEDs offer advantages like higher pixel density, improved brightness, and better energy efficiency.
What are the advantages of Mini LED PCBs?
Mini LED PCBs offer several advantages, including enhanced brightness and contrast, higher resolution, improved energy efficiency, and greater design flexibility for applications like displays and lighting.
What applications are Mini LED PCBs used for?
Mini LED PCBs are used in various applications such as high-resolution displays (e.g., TVs, monitors, and signage), backlighting for LCD screens, automotive lighting, wearable devices, and general lighting fixtures.
What factors should be considered when designing Mini LED PCBs?
When designing Mini LED PCBs, factors such as Mini LED placement and density, thermal management, electrical connections, PCB material selection, routing and traces, environmental considerations, and manufacturability should be carefully considered.
How are Mini LED PCBs manufactured?
The manufacturing process for Mini LED PCBs involves steps such as design/layout, material selection, substrate preparation, solder mask application, Mini LED placement and soldering, testing, and quality control.
What materials are used for Mini LED PCBs?
Common materials used for Mini LED PCBs include FR-4 (Flame Retardant-4), metal core PCBs (MCPCBs), flexible PCBs (FPCs), ceramic PCBs, and high-performance substrates with properties like high thermal conductivity and low dielectric constant.
What are the cost factors for Mini LED PCBs?
The cost of Mini LED PCBs can vary based on factors such as size, complexity, quantity, materials used, manufacturing processes, lead time, and supplier/vendor pricing.
What are the key qualities of good Mini LED PCB manufacturers?
Good Mini LED PCB manufacturers should possess qualities such as advanced manufacturing capabilities, expertise in PCB design and fabrication, adherence to quality standards, responsive customer service, and flexibility to accommodate custom requirements.
How can I ensure the reliability of Mini LED PCBs?
To ensure the reliability of Mini LED PCBs, it’s important to work with reputable manufacturers, conduct thorough testing and quality control measures, select appropriate materials, and adhere to best practices in design and manufacturing.
Where can I find Mini LED PCB manufacturers?
Mini LED PCB manufacturers can be found through online directories, industry trade shows, referrals, and by conducting online searches using relevant keywords. It’s important to research and compare multiple manufacturers to find the best fit for your specific needs.