Minimum Clearance BGA PCB Manufacturer
Minimum Clearance BGA PCB Manufacturer,Minimum Clearance BGA PCBs feature intricately designed layouts with minimized spacing between the solder balls of Ball Grid Array (BGA) components and surrounding conductive elements. These high-density printed circuit boards are engineered for compact electronic devices, maximizing board space while maintaining reliable electrical connections. Through meticulous design and precision manufacturing, Minimum Clearance BGA PCBs enable advanced electronic systems to operate efficiently in space-constrained environments, offering improved signal integrity, thermal management, and overall performance.
What is a Minimum Clearance BGA PCB?
A Minimum Clearance BGA (Ball Grid Array) PCB (Printed Circuit Board) refers to a PCB design where the spacing between the solder balls of the BGA package and other conductive elements on the PCB is minimized to fit within tight design constraints. BGA packages are widely used in modern electronics for their ability to provide a high number of interconnections in a small footprint, which is crucial for advanced and compact electronic devices.
The term “minimum clearance” in this context is critical because it determines the smallest permissible distance between the BGA pads and adjacent traces, vias, or other components on the PCB. Ensuring adequate clearance is essential to prevent electrical shorts, ensure reliable soldering, and maintain signal integrity. Key factors influencing minimum clearance requirements include:
- Manufacturing Capabilities:The precision of the PCB fabrication process dictates how small the clearances can be. High-resolution manufacturing techniques allow for smaller clearances.
- Electrical Considerations:Sufficient clearance helps prevent crosstalk and interference between adjacent signals, especially in high-frequency applications.
- Thermal Management:Adequate spacing ensures proper thermal dissipation, reducing the risk of overheating.
- Mechanical Stability:Proper clearance ensures the mechanical stability of the solder joints, crucial for the durability and reliability of the assembly.
Designing a PCB with minimum clearance for BGAs involves precise calculations and adherence to manufacturing tolerances. Advanced design tools and simulations are often employed to optimize the layout, ensuring that the PCB meets both electrical and mechanical requirements while maximizing space efficiency. As technology progresses, the drive towards smaller and more powerful devices continually pushes the boundaries of what constitutes “minimum clearance” in BGA PCB design.
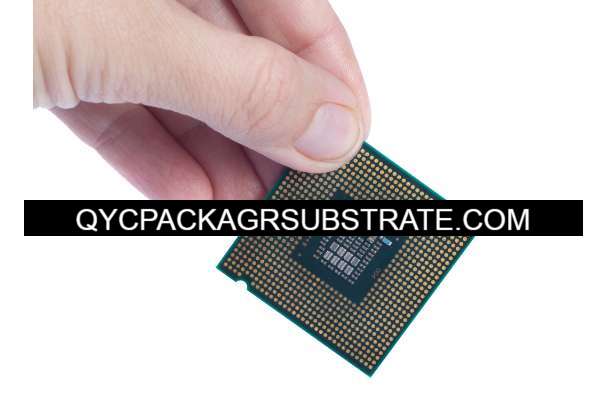
Minimum Clearance BGA PCB Manufacturer
What are the Minimum Clearance BGA PCB Design Guidelines?
Designing a PCB that incorporates BGA (Ball Grid Array) components with minimum clearance requires adherence to a set of detailed guidelines to ensure reliability, manufacturability, and performance. Here are some of the key guidelines and considerations for designing a Minimum Clearance BGA PCB:
- Pad Design and Size: The BGA pad size should be carefully selected based on the BGA ball size. Generally, the pad diameter is designed to be about 1:1 with the ball diameter but can be slightly larger or smaller depending on the solder mask and other design factors.
- Solder Mask Defined (SMD) vs. Non-Solder Mask Defined (NSMD) Pads: NSMD pads are typically preferred in BGA designs because they allow for better solder joint integrity. The solder mask opening is larger than the pad to expose the entire pad copper, which provides a larger surface area for the solder ball to connect, reducing stress on the joints.
- Trace Routing: Minimizing the distance between traces and BGA pads is crucial but must be balanced with avoiding crosstalk and maintaining signal integrity. Trace width and spacing should follow the manufacturer’s specifications and standards like IPC (Institute for Printed Circuits).
- Via Placement: Via-in-pad (VIP) technology is often used in BGA designs to save space and reduce inductance. However, these vias must be properly filled and capped to prevent solder wicking during assembly. Avoid placing vias between BGA pads to maintain structural integrity and reduce the risk of shorts.
- Thermal Management: Proper clearance must be maintained around the BGA for heat dissipation. Thermal vias under or near the BGA can help manage heat, but their placement and size must be carefully controlled.
- Escape Routing: For high-density BGA packages, developing an escape routing strategy is crucial. Utilize dog-bone, via-in-pad, or micro-via patterns to effectively fan out signals from under the BGA.
- Signal Integrity and Impedance Control: Maintain controlled impedance traces for high-speed signals and ensure that differential pairs are matched in length and impedance.
- Assembly and Rework Considerations: Design the board with considerations for how the BGA will be placed, soldered, and potentially reworked. This includes appropriate clearances for soldering tools and inspection.
- Testing and Inspection: Include test points and enable inspection access for x-ray or automated optical inspection (AOI) to verify the quality of the solder joints, especially since BGA joints are not visible externally.
- Clearance Between BGA Balls and Adjacent Components: Keep a minimum clearance between the edges of the BGA balls and any adjacent components or board features to avoid mechanical and thermal interference.
- PCB Material and Layer Stack-up: Choose materials and a layer stack-up that can handle the thermal and mechanical stresses associated with BGAs, particularly for boards with multiple BGAs or mixed-technology components.
Implementing these guidelines requires careful planning and often simulation, especially when dealing with high-density or fine-pitch BGA devices. Collaboration with PCB fabricators early in the design process is also critical to ensure that the design is manufacturable according to the capabilities and limitations of the selected fabrication technology.
What is the Minimum Clearance BGA PCB Fabrication Process?
The fabrication process for a Minimum Clearance BGA (Ball Grid Array) PCB involves several critical steps to ensure precise alignment, proper soldering, and reliable electrical connections. Here’s an overview of the typical fabrication process:
- Design Preparation:The process begins with PCB design using specialized software. Designers lay out the components, including the BGA package, and route traces according to the design requirements, including minimum clearance guidelines.
- Material Selection: Selecting the right PCB material is crucial for BGA applications. High-quality laminate materials with appropriate thermal properties are chosen to withstand the thermal stresses associated with BGA soldering and operation.
- Layer Stack-up Design: Based on the design requirements and material properties, a layer stack-up is designed. The stack-up includes the arrangement of copper layers, prepreg layers, and core layers, considering factors like signal integrity, impedance control, and thermal management.
- Inner Layer Processing: Copper foils are laminated onto both sides of the core material. Then, a photolithography process is used to transfer the circuit pattern onto the copper layers using a photoresist material.
- Drilling: Precision drills are used to create holes (vias) for interconnecting different layers of the PCB. For BGA designs, microvias or laser-drilled vias may be used to achieve high-density interconnects.
- Electroplating:After drilling, the vias are plated with copper to provide electrical conductivity between layers and ensure reliable connections.
- Outer Layer Processing: The outer layers of the PCB are processed similarly to the inner layers, including the application of photoresist, exposure to UV light through a photomask to define the circuit pattern, and etching to remove excess copper.
- Solder Mask Application: A solder mask is applied over the PCB surface, leaving openings for exposed pads and vias. The solder mask helps protect the copper traces and pads while providing insulation between conductive elements.
- Surface Finish: Surface finish options for BGA PCBs include HASL (Hot Air Solder Leveling), ENIG (Electroless Nickel Immersion Gold), or OSP (Organic Solderability Preservatives). The surface finish is critical for ensuring proper solderability and preventing oxidation of the copper pads.
- SMT Assembly: Surface Mount Technology (SMT) assembly involves placing and soldering the BGA components onto the PCB. Precision pick-and-place machines accurately position the components, and reflow soldering is typically used to solder the BGA balls to the PCB pads.
- Inspection and Testing: After assembly, the PCB undergoes thorough inspection and testing to verify the integrity of solder joints, electrical connections, and overall functionality. Automated optical inspection (AOI), X-ray inspection, and functional testing are commonly used methods.
- Final Finishing: Once testing is complete, the PCB may undergo final finishing processes, such as routing, depanelization, and cleaning, before packaging and shipping to the end user or assembly facility.
Throughout the fabrication process, attention to detail and adherence to design specifications are paramount to ensure the reliability and performance of the Minimum Clearance BGA PCB. Collaboration between designers, fabricators, and assemblers is crucial to address any issues and optimize the manufacturing process for quality and efficiency.
How do you Manufacture a Minimum Clearance BGA PCB?
Manufacturing a Minimum Clearance BGA (Ball Grid Array) PCB involves a series of precise steps to ensure the proper alignment, soldering, and electrical connectivity of the BGA components. Here’s a detailed overview of the manufacturing process:
- Design Review: Before manufacturing begins, the PCB design undergoes a thorough review to ensure that it complies with minimum clearance guidelines and other design specifications. Any potential issues or optimizations are identified and addressed at this stage.
- Material Preparation: High-quality laminate materials suitable for BGA applications are selected based on their thermal properties, dielectric constant, and other factors. The chosen materials are then cut into the required panel sizes for the manufacturing process.
- Layer Stack-up Preparation: The layers of the PCB are stacked together according to the design specifications. Each layer includes copper foils laminated onto the substrate material, with prepreg layers in between to facilitate bonding during lamination.
- Drilling:Precision drills are used to create holes (vias) for interconnecting different layers of the PCB. For BGA designs, microvias or laser-drilled vias may be used to achieve high-density interconnects. The drill diameters and positions are critical to ensure proper clearance around the BGA pads.
- Electroplating: After drilling, the vias are plated with copper to provide electrical conductivity between layers. This process involves electroplating copper onto the walls of the drilled holes, followed by a chemical process to remove excess copper from the surface.
- Inner Layer Imaging:A photolithography process is used to transfer the circuit pattern onto the inner copper layers. A photoresist material is applied to the copper surface, exposed to UV light through a photomask, and then developed to remove the unexposed resist, leaving behind the circuit pattern.
- Inner Layer Etching: The exposed copper is etched away using chemical solutions, leaving behind the circuit traces and pads. The remaining photoresist is stripped, leaving clean copper traces on each inner layer.
- Lamination: The inner layers, along with any buried vias, are laminated together with prepreg layers and outer copper foils to form the complete PCB stack-up. This multilayered assembly is subjected to heat and pressure in a lamination press to bond the layers together.
- Outer Layer Processing: The outer layers of the PCB are processed similarly to the inner layers, including imaging, etching, and solder mask application. The solder mask is applied over the surface, leaving openings for exposed pads and vias.
- Surface Finish: Surface finish options such as HASL (Hot Air Solder Leveling), ENIG (Electroless Nickel Immersion Gold), or OSP (Organic Solderability Preservatives) are applied to the exposed copper pads to ensure proper solderability and prevent oxidation.
- SMT Assembly: Surface Mount Technology (SMT) assembly involves placing and soldering the BGA components onto the PCB. Precision pick-and-place machines accurately position the components, and reflow soldering is used to solder the BGA balls to the PCB pads.
- Inspection and Testing:After assembly, the PCB undergoes thorough inspection and testing to verify the integrity of solder joints, electrical connections, and overall functionality. Automated optical inspection (AOI), X-ray inspection, and functional testing are commonly used methods.
- Final Finishing:Once testing is complete, the PCB may undergo final finishing processes, such as routing, depanelization, and cleaning, before packaging and shipping to the end user or assembly facility.
Throughout the manufacturing process, strict quality control measures are implemented to ensure that the Minimum Clearance BGA PCB meets the required specifications for reliability, performance, and manufacturability. Collaboration between designers, fabricators, and assemblers is crucial to address any issues and optimize the manufacturing process.
How much should a Minimum Clearance BGA PCB cost?
The cost of a Minimum Clearance BGA PCB varies depending on several factors, including the complexity of the design, the number of layers, the quality of materials used, surface treatment, order quantity, and manufacturer’s capabilities. Here are some key factors affecting the cost:
Design complexity: PCBs with complex layouts, fine-pitch BGAs, and high-density wiring may require more manufacturing steps and specialized equipment, leading to increased costs.
Number of layers: The number of layers in the PCB stack affects manufacturing costs. Multilayer PCBs generally cost more to manufacture than single or double-layer boards because they require more materials and processing techniques.
Material selection: High-quality laminates with specific thermal and electrical properties are often more expensive than standard materials. Specialized materials for high-speed or high-temperature applications may incur additional costs.
Surface treatment: The choice of surface treatment, such as HASL, ENIG, or OSP, can affect the overall cost of the PCB. Some surface treatments, such as gold plating, are more expensive but offer better performance and reliability.
Manufacturing quantity: Larger production batches typically result in lower unit costs due to economies of scale. However, smaller quantities may incur setup fees or minimum order quantities (MOQs), which can affect overall costs.
Delivery time: Urgent orders or expedited manufacturing services may incur additional fees. Longer delivery times allow for more efficient production scheduling and may reduce costs.
Additional services: Optional services such as panelization, electrical testing, protective coatings, and assembly may increase the total cost of the PCB.
To obtain an accurate cost estimate for a Minimum Clearance BGA PCB, we recommend consulting with us. We can provide detailed quotes based on your specific design requirements, quantity, and desired delivery time.
What is Minimum Clearance BGA PCB Base Material?
The base material for a Minimum Clearance BGA (Ball Grid Array) PCB refers to the substrate or core material used to construct the PCB before copper traces and other components are added. The choice of base material is crucial as it determines the PCB’s electrical, mechanical, and thermal properties. Several types of base materials are commonly used in PCB manufacturing, including:
- FR-4: FR-4 (Flame Retardant 4) is the most widely used substrate material for PCBs due to its cost-effectiveness, good electrical insulation properties, and compatibility with standard manufacturing processes. It consists of woven fiberglass impregnated with epoxy resin.
- High-Tg FR-4: High-Tg (glass transition temperature) FR-4 is a variant of FR-4 with a higher glass transition temperature, making it more suitable for applications where elevated temperatures are a concern, such as lead-free soldering processes.
- Polyimide (PI): Polyimide is a high-temperature resistant material known for its excellent thermal stability and mechanical properties. It is commonly used in flexible PCBs (FPCBs) and rigid-flex PCBs, as well as in applications requiring resistance to harsh environments.
- Rogers or Other High-Frequency Materials:For high-frequency applications such as RF (radio frequency) and microwave circuits, specialized materials like Rogers or other high-frequency laminates may be used. These materials offer low dielectric loss, tight control over electrical properties, and stable performance at high frequencies.
- Metal-Core PCBs (MCPCBs): Metal-core PCBs use a metal substrate, typically aluminum or copper, as the base material instead of a traditional FR-4 substrate. These PCBs offer excellent thermal conductivity, making them suitable for applications requiring efficient heat dissipation, such as LED lighting and power electronics.
- Ceramic Substrates:Ceramic substrates are used in high-power and high-frequency applications where superior thermal conductivity and stability are required. Aluminum oxide (Al2O3) and aluminum nitride (AlN) are common ceramic materials used in PCB manufacturing.
When designing a Minimum Clearance BGA PCB, the choice of base material should consider factors such as thermal management, signal integrity, mechanical stability, and cost. It’s essential to select a material that meets the specific requirements of the application while also considering manufacturing constraints and budget considerations. Collaboration with PCB manufacturers and material suppliers can help ensure the selection of the most suitable base material for the intended use case.
Which company makes Minimum Clearance BGA PCB?
Manufacturing Minimum Clearance BGA PCBs is typically undertaken by specialized PCB manufacturing companies. These companies usually possess advanced manufacturing equipment, experienced technical teams, and strict quality control systems to meet the highly precise and complex requirements of PCB manufacturing. Some well-known PCB manufacturing companies include Foxconn Technology Group, Hanaoka Technology, and LCSC.
As for our company, we also have the capability to produce Minimum Clearance BGA PCBs. We have advanced production equipment and a skilled technical team, focusing on providing high-quality PCB manufacturing services. Here are some advantages and capabilities of our company in producing Minimum Clearance BGA PCBs:
- Advanced Manufacturing Equipment: We have invested in state-of-the-art PCB manufacturing equipment, including high-precision CNC drilling machines, automated soldering equipment, and high-resolution printing devices. These equipment enable precise manufacturing processes to ensure the quality of Minimum Clearance BGA PCBs.
- Experienced Technical Team: Our company has a team of experienced and skilled engineers who can provide professional design support and manufacturing advice. They are familiar with the latest PCB manufacturing technologies and processes and can effectively address various complex manufacturing challenges.
- Strict Quality Control:We implement stringent quality management systems, conducting strict controls and inspections at every stage of the manufacturing process from raw material procurement to production. Our quality control team ensures that every Minimum Clearance BGA PCB meets customer requirements and industry standards.
- Flexible Production Capacity: We have flexible production capacity and can adjust production schedules to meet the varying demands of customers in terms of quantity and delivery time. Whether it’s small-scale customization or large-scale production, we can provide efficient and reliable services.
- Customized Services: We offer personalized customization services, tailoring Minimum Clearance BGA PCB designs and manufacturing solutions to meet the specific requirements of customers. We are committed to collaborating with customers to achieve project success.
In summary, our company has comprehensive capabilities and advantages in producing Minimum Clearance BGA PCBs. Whether in technical strength, manufacturing equipment, or quality management, we can meet customer requirements and provide high-quality PCB manufacturing services.
What are the 7 Qualities of Good Customer Service?
Good customer service is characterized by several key qualities that help foster positive relationships with customers and enhance their overall experience. Here are seven qualities of good customer service:
- Responsiveness: Good customer service involves being prompt and responsive to customer inquiries, requests, and concerns. Responding in a timely manner demonstrates that the company values the customer’s time and is committed to addressing their needs promptly.
- Empathy: Empathy is the ability to understand and share the feelings of others. Good customer service representatives empathize with customers’ frustrations, concerns, and challenges. They listen actively, show compassion, and strive to find solutions that meet the customer’s needs.
- Professionalism:Professionalism entails conducting oneself with integrity, competence, and respect in all interactions with customers. Good customer service representatives are knowledgeable about the company’s products or services, adhere to established policies and procedures, and maintain a courteous and professional demeanor at all times.
- Clear Communication: Clear communication is essential for effective customer service. Good customer service representatives communicate clearly and concisely, using language that is easy for customers to understand. They provide accurate information, set realistic expectations, and keep customers informed throughout the interaction.
- Problem-Solving Skills: Good customer service involves being proactive and resourceful in resolving customer issues and complaints. Customer service representatives should possess strong problem-solving skills, enabling them to identify root causes, explore alternative solutions, and take decisive action to resolve issues to the customer’s satisfaction.
- Flexibility: Flexibility is the ability to adapt to changing circumstances and customer needs. Good customer service representatives are flexible and adaptable, willing to accommodate reasonable requests and make exceptions when appropriate. They recognize that every customer is unique and may require personalized solutions.
- Follow-Up and Accountability: Good customer service doesn’t end with resolving an immediate issue; it also involves following up to ensure customer satisfaction and accountability. Customer service representatives should follow up with customers after resolving an issue to confirm that their needs have been met and to address any remaining concerns. They should also take ownership of customer issues, taking responsibility for ensuring a positive outcome.
By embodying these qualities, businesses can deliver exceptional customer service experiences that build trust, loyalty, and satisfaction among their customer base.
FAQs
What is a Minimum Clearance BGA PCB?
A Minimum Clearance BGA PCB refers to a printed circuit board (PCB) design where the spacing between the solder balls of the Ball Grid Array (BGA) package and other conductive elements on the PCB is minimized to fit within tight design constraints.
Why are Minimum Clearance BGA PCBs used?
Minimum Clearance BGA PCBs are used in electronic devices where space is limited and high-density interconnections are required. They allow for more efficient use of board space and can accommodate advanced electronic components with fine-pitch solder balls.
What are the benefits of Minimum Clearance BGA PCBs?
Benefits of Minimum Clearance BGA PCBs include increased board density, improved signal integrity, enhanced thermal management, and reduced overall PCB footprint. They also enable the integration of advanced electronic components in compact electronic devices.
What are the challenges in designing Minimum Clearance BGA PCBs?
Designing Minimum Clearance BGA PCBs poses challenges such as ensuring adequate spacing between traces and BGA pads to prevent electrical shorts, managing thermal issues due to the high-density layout, and optimizing signal integrity in high-speed designs.
What factors influence the minimum clearance requirements for BGA PCBs?
Factors influencing minimum clearance requirements include the BGA package specifications, PCB fabrication capabilities, signal integrity considerations, thermal management requirements, and design constraints imposed by the end application.
How are Minimum Clearance BGA PCBs manufactured?
The manufacturing process for Minimum Clearance BGA PCBs involves several steps, including material selection, layer stack-up design, trace routing, via placement, surface finish application, BGA assembly, inspection, and testing.
What are some best practices for designing and manufacturing Minimum Clearance BGA PCBs?
Best practices include following design guidelines provided by BGA manufacturers, utilizing advanced design tools and simulations, collaborating closely with PCB fabricators, and conducting thorough testing and inspection throughout the manufacturing process.
How can I ensure the reliability of Minimum Clearance BGA PCBs?
Ensuring reliability involves selecting high-quality materials, adhering to design and manufacturing best practices, conducting rigorous testing and inspection, and working with experienced PCB manufacturers who specialize in high-density and fine-pitch BGA PCBs.